Introduction: Upcycling/upgrading Old Fluorescent Lighting
Replacing older fluorescent lighting can yield gains in available power density and increase efficiency, or in other words lower your power consumption for a given irradiance. The newer high frequency systems make ideal propagation lamps for horticulture due to the higher power density than older types.
DISCLAIMER: I WILL NOT BE HELD RESPONSIBLE FOR ANY DEATH OR INJURY OR DAMAGE TO PROPERTY AS A RESULT OF FOLLOWING THESE INSTRUCTIONS. WHEN DEALING WITH MAINS ELECTRICITY, IF IN DOUBT, ALWAYS CONSULT A QUALIFIED ELECTRICIAN.
For a twin fitting you will need:
1x old fluorescent light fitting at least big enough to take the tubes you wish to run.
1x High frequency electronic ballast - I ordered mine direct from China.
4x T5 end caps
2x T5 tubes - I am using 4' T5 / 865 daylight spectrum tubes
lengths of wire between 0.5mm^2 and 1.0mm^2 to suit the crimp terminals with insulation resistance able to withstand 350VAC rms.
Tools including various screwdrivers, files, hacksaw, bench vice and a few more...
Step 1: Strip the Striplight!
Remove the plastic tube fittings from each end.
Remove the wiring by pressing a screwdriver in the catches on each side which allows access inside the tube cap.
Remove the original passive components, the ballast, the capacitor and the starter and holder. Might be a idea to short the capacitor's terminals if the fitting has been powered up recently.
Remove ay old wiring from the terminal block.
Step 2: Cut the Fitting to Size
Measure where the new T5 tube cap sits relative to where the steel case/gulley is when pushed fully home. Use this to calculate the distance you need to make the cut. I was using 4' T5 tubes which are 1149mm (!) base-to-base.
Cut the steel case using a wooden former to maintain the structure of the gulley.
Same applies to the top of the case. Use a thin wooden shim to avoid damaging while cutting.
I had to make do with a hacksaw to make the cuts - you might have better ideas.
Step 3: Construct New Plastic End Stops With T5 Tube Caps
I cut the original tube cap off the end stop and drilled pilot holes for small self-tapping screws and holes for wiring for the tube caps.
Step 4: Bolt in and Wire Up Ballast
The bolts retrieved from removing the passive ballast were a little too big for the new electronic ballast - a quick file with flat file fixed that problem.
Wire up the connector block (not yet attached to mains in!!!) according to the wiring diagram (printed on the ballast in my case).
The colour coding shown is simply because I salvaged inner cores from 1mm^2 twin and earth. I don't think any standard applies as it is internal appliance wiring - besides, you have already voided any warranty and you've already agreed that you know what you're doing. I guess be kind to whoever looks next.
Take extra care with the earthing arrangements. I removed the connector block and stripped paint from it before reattaching and testing continuity between earth on the connector block and:
- the steel case
- the earth terminals on the ballast
If you don't know what that means then please STOP!
Step 5: Wire Up the T5 Tube Caps
Screw in the end caps and wire up the caps according to the wiring diagram.
There is a common connection required at one end.
Step 6: Wire Up a Mains Plug and Cable
Step 7: It's Alive!
Hooray!
You should have a new super efficient fluorescent light.
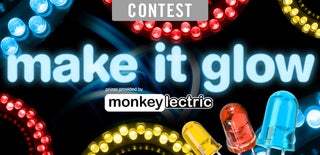
Participated in the
Make It Glow! Contest