Introduction: Experimenting With Small Parts on Your 3D Printer
This Instructable could be a "Game Changer" for people like myself who sometimes need many copies of small, highly detailed parts. In my case, to help with those models. 3D printers are great for many things, but some things, not so great. In the past, the only other way I could make small parts was by hand, with a high-pressure injection molder (which I don't have) or cast them in resin.
By hand is tedious, my eyesight isn't what it used to be and it takes what little time I have away from other things.
Resin is brittle, costs $150 per gallon, has a shelf life measured in weeks and makes a horrendous mess every time I use it.
Injection molders are inexpensive, clean, easy to use and take up little space. But, they require metal dies. Metal dies are made with machinery called "mills". Mills are horrendously expensive and take up lots of space. They also produce tons of oily dirt, and require years of training before they can be mastered.
FORGET TEDIOUS, FORGET RESIN, FORGET INJECTION MOLDERS, FORGET MILLS
YOU HAVE A 3D PRINTER... YOU CAN MAKE INJECTION MOLDED PARTS IN ABOUT AN HOUR... NEATLY AND FOR FREE:
With your printer, the filament that's sitting on your shelf and the demonstration mold I provide, you can make an injection molded "proof of concept" part without adding, modifying or removing a single thing on your printer. And it will only take about an hour from start to finish.
This is one cool paradigm shift for people who love making things with their 3D printer, but also want small, highly detailed parts or jewelry, far beyond the printer's limited resolution capabilities.
Don't have a 3D printer? Don't worry, you will. As of this month, Staples is selling them, and within 2 years, I predict you'll be able to pick one up at WalMart. 3D printing is having the same growth cycle as the microwave oven had (remember when those came out?). All "WOW factor at first, but in everyone's home within a couple of years.
Enjoy the descriptions and images I have so far. And while you're waiting for me to post more information, please vote...
Vote for anyone... But preferably me :)
This is a new idea and new ideas need data. Negative feedback is actually more valuable than Positive. And don't worry, I'm very comfortable with criticism. You won't hurt my feelings and you may have a better idea we all can use.
Thanks,
bfk

Attachments
Step 1: What You'll Need:
Here's what you'll need:
1. A 3D printer. Now, if you don't have a printer, but have an extruder and heater from an old printer or from a printer you're making, you may be able to construct a "free standing" version of an injection molding machine that may actually work better than the method I'm describing here.
2. A mold. Printing the supplied mold will allow you to produce a true injection molded part, but it will still have all the external characteristics of a 3D printed part. As I've said, you can make a mold from just about any standard mold-making material, but I don't yet know what materials work best for this process. I've been experimenting with polymer clay, a hard, inexpensive, heat resistant and easy to use material that can be picked up at WalMart. Silicone RTV rubber is a material I've had success with and recently, I've tried a product called "Sugru" which works better than polymer clay, but not as well as RTV. I've added instructions on how to make a mold out of Sugru in the next step, along with the instructions for using the downloadable printed mold. If you just want to get on with it and print the mold I'm supplying, You can download it at the bottom of this page.
If you have mold making experience, you may want to use RTV, or do as I did, use an old mold to prove to yourself this process works.
The pressures involved aren't large, so metal dies aren't necessary. However, if you do experiment with metal dies, I'd be very interested in hearing how it works out. I have no way of making metal dies myself.
If you use my printed mold, you'll also need higher and lower melting temperature filaments. I used ABS for the mold and PLA for the part. If you use a more heat resistant mold material, theoretically, you may be able to print in ABS, PLA, Nylon or any other material that fits through your machine (chocolate bars, anyone?). One person even suggested hot glue. None of these other materials have been tried. I've only used ABS for the mold and PLA for the injection medium. So far, other than the lack of color, I'm quite happy with it.
3. A watch. You'll need to time your injections. Too short and the mold won't fill completely. Too long and you'll have to trim too much flash from around the parting line. The time it takes to fill a small mold is measured in seconds. Once you work out the best time for each shape, your parts should be good every time.
4. Time: The "proof of concept" demonstration in this Instructable will take about an hour of your time. Most of this time will be taken up by printing the mold. For best results, the mold needs to be warm, so plan to be there when the print finishes and you can make the injection then.
READY? Let's begin:
Attachments
Step 2: Make the Mold:
This step is in 2 parts.
Part 1 will walk you through the making of a mold out of Sugru, a popular "hacking" material popular on Instructables. I've tried it, and it does work. Not as well as proper RTV molds, but better than printed ones... The mold won't last but a couple of times, but for proof of concept, it's pretty good.
Part 2 details the downloadable mold.
Choose whichever one you want. Let's begin:
Part 1. Sugru
Sugru cures overnight, so rushing, as I did, will most likely produce poorer results. I've added the instructions to the photos, so if you're planning on using Sugru, just follow the pictures in order.

For this method, you'll be making a mold of a ball about 1/2" in diameter.
A ball is a good shape to use, since there aren't any overhangs no-matter how it's set up and the parting line is a simple matter to place. You can download it at the bottom of this page
Once the print is complete and the mold is still hot, remove the upper half (the one with the hole through it) and place it on top of the lower half. You don't have to release the lower half from the build plate. I kept mine attached to the plate as a way to keep everything warm and steady.
The printed mold is large (volume-wise), so it's probably important to fill it with PLA as soon as possible after the print has completed. The printed mold would distort if you attempted to heat it with a heat gun, but after printing, the mold will be evenly warm throughout it's structure and won't be at a temperature that would cause problems.
Note: The photo of the printed and assembled mold sitting on my printer was taken AFTER the piece had been cast.
Whichever you use, you'll be printing the mold on your printer the same way you print anything else. They'll print in 2 halves as shown in the first image that appears immediately after the Sugru files.
If you're bold, and want to play with the mold of the 1/2" long gun tube (which may, or may not work on your printer), that mold is also available as a download at the end of this section. If the gun tube doesn't work, don't throw things down and give up. Try making the ball. The gun tube cavity wasn't even fully formed in the mold I printed, but you may have a better printer than me.
Step 3: Make the Casting:
Once the mold is together and sitting on your build platform, disengage your printer's motors and maneuver the extruder head, the one with PLA installed, over the opening on top of the die. Lower the head into the opening and insure it's centered and the seal is snug.
Turn your extruder's "load" function on and wait until PLA begins to squeeze out between the nozzle and the die. Depending on the size of your part, it should take less than a minute. I left the ball on for 1 minute and got the results in the picture (waaaay too long). The cannon parts took 15 seconds for the gun tube and 30 seconds for the truck. Even then, the amount of flashing around the parts was excessive.
The extruder on your printer produces nothing near the pressure of an injection molder. For all intents and purposes, there is very little pressure working to fill the die on your prnter. The filament moves into the available space, pushing the plastic that came before it further into the cavity. As long as the filament stays hot, it all fuses together into a solid mass, the size and shape of the cavity.
As soon as the mold cavity is filled, and PLA begins to push it's way out of the mold and past the extruder nozzle, turn the extruder off and wait for things to cool down. I have a tendency to want to rush things, but pulling the mold apart before the plastic cools will present you with hot plastic that acts like molasses. You'll burn yourself and only have a distorted glob of plastic for your troubles. Be patient. I pulled my molds off of the build plate and drop them into cold water to help speed things up.
If you're using the printed version, crack the die open with a screwdriver and take pride in your first injection molded part. Carefully drilling through the top hole may be enough to allow you to remove the part without having to destroy the die. The Sugru version will peel apart. If I had used mold release (talcum powder, dry lubricant, even soapy water should work) the part wouldn't be permanently attached to my washer. :)
That's it. You're done with the Instructable. Everything that follows is about what I've been learning as I continue to experiment with this new technique.
This Instructable will be the only place I'll be adding new discoveries about injection molding on a 3D printer. (As of this moment) A Google search on injection molding with your 3D printer will only send you back here, or to a couple of other pages... That will send you back here. (You will find a lot of sites about making molds with 3D printers though... Like bryanbrutherford's excellent Instructable. This may be something we should all look at and use to help us out).
So... You may continue reading, or not. If you decide not, at least scroll down to the end and leave a comment on your thoughts. Please. It will help me and you'll be adding your valuable perspective to this new technique.
Enjoy,
bfk
Step 4: Now That You Know There Are Other Ways to Make 3D Parts With Your Printer...
In the past, as I've developed my ideas, I've made additional Instructables with titles like "New and Improved". But I think keeping everything in one place may be the better way here. I'll re-invent the Instructable instead of forcing those who are interested to figure out where the latest version is... Less work for me too.
___________________________________________________________________________________________________
I make model ships and forts for museums as a hobby and have been contracted (probably not the correct term, as I donate them) to build a pre-Revolutionary fort, an historic battle scene and a Revolutionary War ship later on this year. Because museum models need to fit a given space, their scale is... Well, let's say, "non-standard". Store-bought scale parts aren't usually an option.
I've added this Instructable to the Epilog V Contest (and another Instructable, using the same principle, in the 3D Printing Contest ) with the hopes people think this is a truly unique and innovative idea worthy of a prize. An Epilog laser would round out my shop, propel my models into another incredible universe and allow me to bring sooooo many more ideas to reality. It would also be important to many more people, which I'll touch on later.
The following steps will be focused more on my own interests, the types of items I want to injection print, and ways I can integrate them into laser cut and etched projects, should I be lucky enough to win the grand prize.
I'll also be using this space to plead for feedback. This is the fun phase of inventing things. And the time when ideas can bounce and blend, giving birth to entirely new discoveries.
This concept is so fresh, that if you think about it, toy with it, experiment with it, it's guaranteed you'll come up with something new. You can add your discovery to this Instructable, make your own Instructable, or make your fortune. Any way you decide to express it, you'll help shape the future of 3D printing.
Inventors always think their ideas are important... And it's not any different with me. I know this is not an idea that can be used by everyone just yet, but when 3D printers become commonplace, it'll be like realizing your pair of scissors can be used to poke holes through paper as well as cutting it. A perfectly valid use of something intended to do something else.
And until 3D printers are able to print objects as good as and as fast as those made by injection molders, the race will continue. And who knows if this "realization" isn't the flick that ignites the idea, that produces the component, that reaches that goal...
And you could be the person who does it.
I'll beg one last time:
If you're an expert or new to 3D printing, if you've ever thought about buying or building one, or if you'll be around in 2 years when you'll have to pick one up at your local big box store, because all of your friends have one. Or your kids need one to finish a class project... Please join in... Leave a comment. Please.
Attachments
Step 5: Now, a Point About the Importance of Mistakes and Some Blatant Advertising
When 3m was experimenting with glass-based fillers to strengthen and lighten plastics, their engineers invented an extremely fine powder composed of hollow glass spheres. While in development, they discovered the process that produced the spheres would, once in a while, make spheres that weren’t hollow, adding weight to the fill. In figuring out how to get rid of these solid "mistakes", they learned how to make them… Solid glass spheres reflect light back to it's source. And is why today, stop signs glow so brightly when your headlights shine on them.
I stumbled on this technique May 1, 2013. I don't have the resources of 3M, nor do I have unlimited time to perfect the process. So far, I've had as many failures as I've had successes. As an engineer, I know accidental things, like 3M's glass spheres have a physical, discoverable and repeatable cause. I also know a 3D printer will work as an injection molder... Because I've been able to do it... Repeatedly. Now, I only have to figure out how to make it work correctly every single time, how big, how small, what materials, what temperatures, what speeds, ad nauseum.
Eventually, this technique will become another awesome tool that can be added to the 3D printer's growing bag of tricks. Please understand that the journey will be bumpy with plenty of "U" turns and mis-steps. I'll try as well as I can to avoid mistakes, but so far, I've never truly learned anything without making them.
And now for that advertising;
Instructables states in their rules; "... be sure to tell us what you'll do with the Zing if you win!" I want the Zing and I want to follow the rules... So here goes:
I'm retired. And volunteering has become an important part of my life. Everything I do is done with my own money and resources... Here's a partial list of the things I do and what I can see the Zing doing for me:
I'm a Red Cross certified Extra Class VE Amateur Radio operator, involved in Disaster Communications and the testing of new "Hams". I'm sure a Zing would be well used in making signs, awards and objects that our local radio club could use and sell to pay for our equipment. It will definitely be used to make customized disaster equipment and high end signage for our mobile disaster trailer.
I also volunteer at and consult with local museums. Primarily making displays, building models and anything else that enhances the museums' public face. One of those museums is the United States Marine Corps Recruit Depot on Parris Island, where I also work with recruits and new Marines. I bet access to a Zing Laser Cutter would be very well received where the men and women of our country's elite fighting force are made. And no, the government does not supply us with endless supplies and gobs of money. The reality is, the non-politicial arms of government (ours, or anyone's), like the rest of us, have to make do with what they have. Except for some office tools, paper and a few old and well-used desks, volunteers and most employees make do with their own equipment. Today, I had to order and pay for parts for a display that went belly up... And hope there's enough money in petty cash to reimburse me at some point.
I also mentor elementary and middle school students. Our future depends on young people. And when they graduate, they'll be going into jobs that don't exist today, using tools that haven't even been invented yet. Because education is one of those politicized things, schools do have some money to spend, but politicians get to tell them where to spend it and what to teach. If you haven't already noticed, politicians are stuck somewhere back in the 1950s and don't have a clue what kids need going into the future... (don't get me started...)
That last statement is why it will be the most important thing I'll be doing with the Zing if I win it. I'm already using my 3D printer to introduce children to layered deposition manufacturing, knowing full well, today's best equipment is the "Model A" version of that technology in the developing digital era. By the time they graduate, 3D printers will have become those microwave ovens of today. In a blink of an eye, everyone will be using one. If kids can comprehend the basics, they'll be able to comprehend the improvements and changes.
I also have a classic 1970 race car and am a member of a local car club. In the summer, it's not unusual to have 2 or 3 car shows going on in a week. Clubs need money to operate and a large portion of the money they get goes to laser cut and engraved awards... They also make money by selling things, like personalized laser engraved key chains and shift knobs and car badges and... I could go on and on...
Oh, I almost forgot! I'l definitely need to make small, highly detailed items to cast using my new injection molding method. That Zing would be the perfect tool for that... You betcha.
So that's my story. and there's no wrong response on your part. I feel I'm at a disadvantage because I'm not an Instructable employee with a gazillion followers, nor do I come up with ideas that are tremendously popular or understood. But please take the time to read what I've come up with here, and if you like it, press the red "Vote" button at the upper right of this page.
If you do that, a lot of people will thank you for it.
And... If you decide to give me either a comment, or a vote, but not both... I'll take the comment.
And whether you comment, vote, or not: Please check out my website:
Children in Freefall
It's about kids, and something you probably didn't realize is a terribly common occurrence. it affects not only those of us who matter most, but their families, neighbors and community too.
Thanks for listening,
bfk
Step 6: Variations and Experiments... Where I'll Post the New Stuff and Delete the Old Stuff.
Now that we're done with that awkward little piece of business and I've had a few days to experiment, I'm beginning to understand the mechanics that control the success of this technique. One thing I wanted to find out is if an inclosed cavity is needed at all. I didn't have an open mold small enough to test this, so I made an impression of the crown on one of my watches.
I discovered, at least with silicone dies, the plastic (PLA in this case) won't adhere to silicon, nor will it form itself to the shape of an open mold. It's more attracted to the extruder nozzle than the die. I solved the issue by placing a fender washer over the cavity, converting it into a closed mold. This is a good time to suggest that you might experiment heating molds with a heat gun. I heated mine away from the printer because I have float glass on my bed and the heat gun may split it. If your bed is aluminum, there shouldn't be any problem heating the mold in place on the printer (if you have a heated plate, a heat gun is also a good way to speed up the printer's heating cycle).
My results were satisfactory. More so than with the old cannon molds. Since my watch impression was located dead center in the mold and there weren't any parting lines to contend with, the shot went in with no problem. There also didn't seem to be any of that black soot or bubbles that were present earlier.
Because it's transparent (try THAT on a home 3D printer), the details are difficult to make out, but seen in real life, the part is a nearly perfect replica of my watch's crown.
My RTV has arrived and in a couple of days, I'll have the time to re-make my molds. I think I'll make as detailed and as small of a master as I can. I'll also stick with the cannon theme, since I know I'll be needing them later on this year.
5/19/13 NEW PRINT (same old cannon) and a NEW INSTRUCTABLE!
OK, I know I said this would be the only place for new information. I didn't lie. I thought that it might be better for people who just want to get on with it and make a mini 3d part, but don't care about the long-winded how or whys. The new instructable is a step-by-step "How To", in traditional Instructable format describing how to make a mold and set it up on a printer.
5/19/13 Sugru Update
I attempted to make a more detailed part with Sugru and ended up a bit disappointed. The material breaks off and flakes, and the part never extruded far into the cavity. i've added pictures here to show the results. I'm going to declare Sugru a proof of concept material, but not too good for extended use.
5/20/13 An entirely new idea:
I received another comment about using hot melt glue, and how it would be much less expensive (than buying a 3D printer).
I had to discard the suggestion for myself, because my museum quality (if that's what you want to call it) models wouldn't survive if they were made from a wax-like material.
I'll break a hot glue gun apart and see what would be needed to bring the heater size down to filament diameter and the heat stabilized to produce the proper density for PLA. A mechanical modification for the trigger is the easy part, I assume. Give me some time and I should have some answers.
A hand, operated and controlled device that allows direct injection of plastic into a mold, certainly sounds like an improvement to me. Having the extruder speed hand controlled, as opposed to mechanically extruded as recent designs of hand held 3D printers require, the task may actually be quite simple. We'll see.
If anyone would like to run with this idea, it would be nice if you came back here and referenced this Instructable so we can pool the knowledge and improve the hobby.
Task 1. Try casting with hot melt
I've replaced the photos in this step to reflect this deviation. The results are encouraging. The entire mold of the barrel was filled without heating the mold, only the hot glue gun. the part is a bit floppy and not good for models, but the results give me hope that i'll be able to modify the gun to accept PLA filament. The worse that can happen is i'll lose a trusty old hot melt gun. i've annotated the photos with all the pertinent "stuff" and ordered a mixture of urethane and polycarbonate sticks to experiment with.
Credit needs to go to qwixel who's comment about using a hot melt glue gun started me in this direction.
So far, there's no PLA based hot melt available, so the continuation of this idea needs to be put on hold and made into its own Instructable. As soon as I have results, I'll post a link to it here.
5/21/13 Update
I've been trying to make a successful casting of the gun barrel shown here with little luck. the plastic never seemed to be able to make it all the way to the end of the barrel. At it's narrowest, it's only .061" in diameter, and the plastic may be having trouble squeezing down that far. I tried adding vent holes to relieve air pressure and I've tried heating the plastic up to 260c degrees with no luck.
What I learned today...
FORGET THE HEAT GUN
Without heating the mold or plate, I held the cannon barrel mold by hand, pressing it tightly against the nozzle and hit "load". The dumb thing filled!.
The important step must be keeping the nozzle well sealed against the silicone. The plastic may take the path of least resistance. If it's prevented from flowing back through the filling sprue around the outside of the nozzle, then it will go further into the mold. And continue until it fills the mold completely.
You have to be very accurate with timing, I found out. Because the silicone is flexible, the plastic will begin to expand it like a balloon if it's left on too long. I've had a few gun tubes that look, umm, un-photographable. The end of the barrel is expanded and looks like... Well, you get the picture :)
All of the photos of the "decent" casts and descriptions are the first ones in this step. As of now, my success rate is very high and the task of casting is becoming incredibly simple:
1. Heat the extruder.
2. Holding the die against it.
3. Press "load".
4. count seconds.
Much cleaner and user friendly. This process keeps on getting better and better.
Next... How large can I make things.
5/24/13
Today was a day fo me to spend working on my race car. I came home in the afternoon to say "hi" to my wife and saw a package from the good people at HotMelt.com sitting on the front porch. Inside was a package of their polyamide hotmelt product and a couple samples of a plastic hot melt. I was very interested in the polyamide product as that is one of the materials being used successfully in 3D printing. I stayed home an hour or so, experimenting with this material, injecting molds with my hotmelt gun and running to the magnifier. I am quite happy with the results. There are a couple of negatives, which I'll touch on first:
Negative 1. Polyamide is moisture sensitive. I don't know if it's moisture cured, but over time, the parts become less rigid, telling me something is happening chemically. What concerns me is, the shelf life of the material. It arrived in a foil bag with the warning that it should be re-sealed after being used.
Negative 2. Negative 1 wouldn't be such an issue if it didn't cost $20 per pound. Still less than resin, but I went through a stick in no time (Having fun with it though)
Now for the positives:
Positive 1. This material flows smoothly into the most detailed of openings in my molds. I'm still having difficulty in determining when I should let off on the pressure, but the results, even surrounded by flashing are incredible.
Positive 2. While still remaining flexible, the parts seem to stiffen up after a short time. This may be due to the material continuing to cure after the heat dissipates, or it may be my imagination. The parts also seem to hold up to rough handling, something I know my models will have to live with.
Positive 3. They are paintable with acrylic paints. If polyamides come in 1/2" diameter rods, in a range of colors, I'll be right there in line to pick some up. Even if my parts have to be painted, I couldn't be more pleased.
Positive 4. Cyanoacrylate adhesive sticks like glue (pun). i was totally surprised when I used cyanoacrylate to glue the wheels and gun tube to a field cannon. No complaints from the polyamide, and the part stuck together like it was one piece.
The first 2 pictures today are 1) the difficult for me to cast gun tube. Notice the muzzle flare at the end of the barrel. Also notice all the warts along the barrel. Those are bubbles, and I intended them to be there... That's my story and I'm sticking to it:)
The second picture is the field cannon. I cut all the flashing I could with a pair of normal sized Fiskar scissors and painted it real quick, all in about 5 minutes. Still, it looks pretty good.
I'll end the discussion on hot glue gun injection casting, but it is very promising and I'll start another Instructable on glue guns and polyamide. I'll link to it here when It's published. stay tuned.
7/14/13 some time ago, I received a pound of Nylon filament. My intent is to use it to make engineered plastic parts for my 1970 race car. I'll most likely have enough material left over to experiment with injection printing small nylon parts as well. Nylon seems to be a natural match for 3D printers. Perhaps it will also do well with injection printing. I'll be working on the car for the next couple of months, getting it ready for next year's events. But stay tuned... I'm not going anywhere.
Step 7: Final Thoughts:
OK, Not Final Thoughts... Rambling:
I normally like to use childrens' plastic building blocks to make my molds. Molds made with blocks can be custom sized and because they disassemble quickly and have no bottom, cured silicone can easily be removed, flipped over and re-inserted.
For this process, I've recommended using a small ceramic container. Ceramic for heat and the closed bottom for neatness (open bottoms and liquid materials require special and not so easily mastered steps to prevent it all running out, onto the table top, shoes and floor).
My data and methods could be someone's commercialization link, which would be OK with me (I'm retired and happy... Read my bio)
Things I don't have answers for, that still need to be resolved and that I'd gladly accept help with:
Time:
The most difficult issue for me, at the moment is, knowing when the cavity is filled.
Perhaps, an electronic means to give a visual clue that the process is complete or shut off the extruder.
We know the speed and volume of the filament and we can calculate the volume of the cavity. I suppose the correct time can be calculated, but who's actually going to take the time to do that? At the moment, I'm using the "try 10 seconds, then 15 seconds, then 20 seconds and so on' method. That's what I did for the cannon and ended up using 15 seconds, even though it should probably have been closer to 12 seconds. The largest of the two carriages for the gun is 30 seconds, and I got that watching the video I made of me making it.
Once the time for a specific part is known, production of additional parts is a simple matter of keeping an eye on the clock.
Maybe this is a non-issue and someone, smarter than me already has a sure-fire solution.
I've noticed when there's a washer on top of the mold, it will lift up slightly when the cavity is filled. Perhaps that mechanical movement can be linked to stop flow.
Molds for non mold-makers:
I'd like to find an easier way for people with no molding experience to try this technique. Sugru works somewhat, but it's not in everyone's home.
I tried a box of kid's modeling clay... Terrible with heat, but I haven't yet tried it without heat... The nozzle sprue would need to be insulated somehow.
I'll keep trying and keep everyone informed of my results... Stay tuned.
OK... One Last Time:
Please, please, please leave a comment... Good or bad... Please add your thoughts and ideas... I won't get mad, I promise.
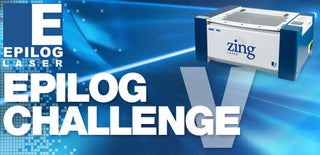
Participated in the
Epilog Challenge V