Introduction: DIY Plastic to Oil
"Till date nothing has proven to be a truly effective or environmentally responsible solution to the burgeoning global landfill problem. In fact, many existing solutions have been just the opposite: costly, energy inefficient or equally as harmful to the environment as the plastic itself. "
It is only now, that with the evolving pyrolysis technology, there is a solution that is remarkably simple, economically viable and "green" as well.
Pyrolysis is a thermochemical decomposition of organic material at elevated temperature without the participation of oxygen. In this process long polymer molecules are broken down into shorter chains of hydrocarbons with the help of heat and pressure. You can learn more about this process here: How to make oil from plastic
Some benefits of pyrolysis are that the process does not generate harmful pollutants and that the by-products can be used as fuel for running the plant. In the case of plastic, some of the valuable fuels and solvents that can be extracted through waste plastic pyrolysis are fuels like gasoline, kerosene, diesel, and high-value ones like benzene, toluene and xylene. And a kilo of waste (typically PP) can yield upto a litre of fuel whereas the incineration of the same quantity of plastic would produce 3 kilos of CO2!
This technology is growing in popularity and in demand. Commercial machines for home are still expensive. But with the following method, you can convert waste plastic to fuel all by yourself!
If you like this project, do vote for it!
Step 1: Procedure
WARNING:
You will be working with highly inflammable substances. So do take the following precautions:
- Avoid inhaling the potentially harmful fumes
- Keep the fumes, produced in the reaction, away from fire and from electrical points
- Work in well ventilated spaces
- Keep some water and a fire extinguisher on stand-by in case of an accident
Construction of prototype pyrolysis reactor
- Build a robust leak-proof reactor chamber
- Build a condensation tube of copper, steel, or aluminium
- Build a system for monitoring the temperature of the feed
- Build a system to efficiently condense and collect the mixture of products
Step 2: Build the Reactor
Before getting down to work, first decide the scale of your setup.
Ideally, 1 kg of plastic can produce 1 kg of fuel. For getting a good yield, you can use polypropylene i.e. any plastic product with the mark PP or '5'.
The reactor that I built has a capacity of about 100g.
So while selecting the container for your reactor, keep in mind the following considerations:
- It must be a robust metal container
- Its shape will affect the reaction speed, intensity and chemistry
- It must be easily openable and cleanable, yet...it MUST be perfectly leak-proof!
I used a stainless steel vessel and clamped it with a bolted aluminum strip. Next I drilled a hole in the centre of the lid for the outlet of the fuel vapour.
Step 3: Condensing Energy
Back in the reactor, the plastic is converted to vapourized fuel above 400C.
You need to convert this vapour to liquid by passing it through a condenser. Once again, it needs to be robust, heat resistant and leak-proof. I used copper pipes (used as condensate piping in A/Cs and refrigerators) but you can you aluminium or steel.
The length of the condenser may not be sufficient for the circulating water to bring the 400C vapour to room temperature. So you'll need to further bubble it into water and then seperate the floating oil from the denser water. Let me know if you come up with a smarter way for doing this!
Step 4: Start Producing Black Gold
Once you are done with the construction work, start the fascinating process of converting trash to black gold!
Here's how:
1. Collect some waste plastic items and shred them to pieces for faster and better reaction
2. Seal the shredded plastic tightly in the reactor chamber
3. Setup the equipment on your stove and turn on the inlet water flow
4. Turn on the stove, stand back, and watch the spectacle!
Initially you'll see fumes flowing out of the condenser, then drops will trickle, and finally you'll have a stream of usable oil flowing out! At the end of the reaction, when you open the chamber that was initially full, you'll be surprised to find it empty, only charred.
The trash disappears and all you are left with is usable oil of high calorific value. Light the obtained fuel and witness it burn flawlessly and for long! If you want to obtain refined usable products from this mixture, you can do so by careful fractional distillation. Although few people can extract the different product of pyrolysis, we successfully did! After successive distillations, we extracted four distinct products, which on the basis of boiling point, odour and calorific values, were concluded to be benzene, toluene and even a mixture similar to diesel!
Waste is a misplaced resource...your trashcan is a treasure chest.
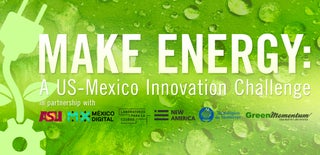
Participated in the
MAKE ENERGY: A US-Mexico Innovation Challenge
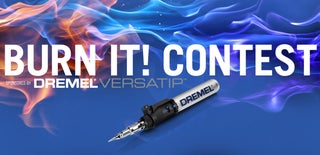
Participated in the
Burn It! Contest
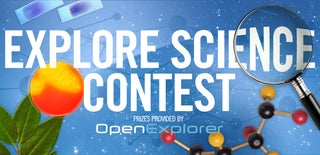
Participated in the
Explore Science Contest