Introduction: Wood Fired Hot Tub
Wood-fired Hot Tub
Perfect for 6-10 friends. It can be carried in the back of a small pickup truck. It takes about 3 hours to get up to temperature and cost about $650.
Materials
-55 gallon closed steel barrel ($30)
-Barrel stove conversion kit ($50)
-14 2" x 4" x 8" firebricks ($30)
-2 2 foot sections of 6 inch black stove pipe ($13 each)
-50 feet of 1/2 inch flexible copper pipe ($80)
-10 feet of 1/2 inch rigid copper pipe ($15)
-10 1/2 inch straight pipe fittings ($5)
-10 1/2 inch elbow pipe fittings ($5)
-plumbing solder and flux ($5)
-Rubbermaid 300 gallon stock tank ($300)
-1/2 horsepower centrifugal water pump ($40)
-10 foot garden hose ($15)
-1 foot 3/4" CPVC pipe ($5)
-assorted fittings to connect tub to pump and stove with garden hoses ($50)
-ground fault switch to turn on pump ($15)
Equipment
-jigsaw with metal blade for cutting holes in barrel
-hacksaw for cutting pipe
-pliers
-slip-jaw wrench
-drill with sharp drill bits
-propane torch for soldering pipes
-shop vacuum with blower attachment (optional)
-screwdrivers
-socket set
Step 1: Build Barrel Stove
Get a 55 gallon steel barrel with a closed top. I got mine from a guy in Bradford, VT who calls himself the "Barrel Man," but if you don't live in the area, you can usually find them on craigslist. Make sure you get a barrel that hasn't been holding anything toxic, since you'll have to spend a fair amount of time crawling around the inside during the assembly process. This barrel formerly held palm oil, and there was a small puddle of it on the inside (it had the consistency of crisco) and every once in a while I accidentally stuck an elbow in it.
I bought a Vogelzang Barrel Stove Kit, Model# BK100E from Amazon.com. Assemble the stove following the directions in the kit. The kit comes with the door, the chimney collar and the legs. The stovepipe is not included in the kit. I bought mine at Home Depot.
When cutting the holes for the chimney and collar, make sure you use a blade designed for cutting sheet metal, and when drilling holes, make sure you have a sharp drill bit, otherwise it will take forever to drill your holes.
After assembling the kit, I added firebricks to prolong the life of the bottom of the barrel. I used 2" x 4" x 8" bricks there were 3 rows of 4 and a final row of 2 for a total of 14.
Step 2: Coil Copper Tubing for Heat Exchanger
The copper tubing comes from the store as a flat coil. First straighten it out by hand. Then crimp one end of the tubing with a pair of pliers. Fill with fine dry sand. The tube should be held almost vertically when filling with sand or the tube may be filled unevenly. Once the tube is full of sand, crimp the other end. The longest length of tubing I could hold vertically and still reach the top to fill was about 10 feet, so I cut the tubing into 10-foot lengths and filled each one separately.
The tubing can now be bent into a coil. I found a piece of 4 inch pipe to wrap the tubing around. There were a few sections where the sand had not completely filled the tube and it kinked. I cut these sections out.
After bending the tubing into a coil, you have to get rid of the sand. Cut the crimped ends off with a hacksaw. Then shake and tap the coil to remove the sand. Getting the sand out of the coils took a lot of time. After most of the sand was out, I used compressed air to remove any last remnants.
5 short coils were soldered together to make the large coil. In order for the coils to fit together nicely, make sure they're all coiled in the same direction.
Step 3: Put the Heat Exchanger on the Stove
The heat exchanger was inserted into the chimney (2 sections of 6 inch stove pipe). I drilled a hole in the bottom for the tubing to come out. Two pieces of angle iron were used to reinforce the tubing and the chimney, along with a lot of bolts (probably more than necessary).
The heat exchanger was plumbed to the bottom of the barrel to keep the hoses low to the ground (don't want anyone tripping over them) and also to keep them away from the heat of the stove. The copper tubing was terminated with a female hose fitting. In the photos you can see a short section of 3/4 inch iron pipe, but that was not necessary.
Finally, we added handles by connecting short sections of galvinized pipe (electrical conduit, I think) to the barrel with wire rope and bolts.
Step 4: Connect the Heater to the Tub
The tub is a 300 gallon Rubbermaid stock tank. It has a 1 1/4 inch threaded opening at the bottom. Using a series of adapters, I was able to connect this to 3/4" CPVC pipe. Next, there's a union fitting. This allows the pump to be easily connected and disconnected. Then I added a ball valve. The ball valve was basically unnecessary. Then I added another adapter to bring the 3/4" CPVC up to the 1" threaded diameter of the pump intake.
The pump output is also 1". It's connected with regular PVC (CPVC probably would have been a better choice, but it's a short enough section that heat flexibility isn't a problem) to an elbow. The elbow is important because if you try to connect the garden hose to a vertical fitting, it will kink. The elbow has a male hose fitting on the end.
To control the pump I use an inline portable ground-fault circuit interruptor. The "test" and "reset" buttons can be used to turn the pump on and off. Side benefits of added safety from electrocution.
Step 5: Transport to Location
Pile everything in the truck. Strap the tub down to keep it from blowing away.
Step 6: Fire It Up and Enjoy
When we fired it up, we decided to attach the exhaust of a shop vac to the barrel to get the fire going a bit faster. It worked great. In fact, it caused the end of the barrel to glow. With the stove closed up, we were able to adjust the temperature of the tub by turning the shop vac on to increase the temperature in the tub and turn it off when the tub was warm enough.
Step 7: Analyze Performance
I used a digital logging thermometer to measure the temperature of the tub over the course of the evening. There are a few missing data points, I think this might have happened when the logger got splashed.
Time 0 was at 4:30 pm when we lit the fire in the barrel and started filling the tub. The outside temperature was about 65F and the water from the hose was 45-50F (I didn't get the thermometer until 2 hours in.) After 3 hours the tub had reached a comfortable 105F. The heating was greatly accelerated by using the shop vac blower. When the blower was turned on you could feel the water in the hose get warmer. The stove heated it at about 20 degrees F per hour.
The next 5 hours (hour 3 to hour 8) was spent lounging in the tub. The temperature was controlled by turning the shop vac blower on and off. During this time the temperature fluctuated between about 100F and 108F.
At hour 7.5 the tub had 10 people. When 8 of them left we needed to fill it up with more water. I think the temperature drop from time 7.50 to 7.55 was a result of the "cold hose" being pointed at the thermometer. Later on the temperature jumps to 130F, which is probably from the "hot hose" coming out of the stove. I was in the tub at the time and it was quite comfortable despite local variations in temperature.
The stove was turned off after 9 hours and the tub cooled down at a rate of about 7 degrees per hour for the next 5 hours.
Doing a bit of math, we can see that the heater was generating about 13.4 kW, the tub was losing about 3.4 kW and the remaining 10 kW is what was getting used to heat the water. To put it another way, we lost 1/4 of our energy from cooling, which suggests that the tub might benefit from an insulated cover.
I'd estimate we used about 1/12 of a cord of wood, which works out to about $17 (for wood at $200/cord).
Step 8: Mistakes to Avoid
Always keep water circulating through the copper coil. Otherwise the solder joints will melt and start to leak. Started the fire about 10 minutes before turning on the water, and the coil started leaking so much that it put out the fire. To fix the problem, I had to disassemble the chimney, take the copper coil out, clean off the solder joints (all 5 of them were leaking), resolder and reassemble the stove. I'd estimate the procedure took about 4 hours. It occurred to me that brazing might have been a better choice for joining the tubing sections instead of soldering.

Runner Up in the
Jury Rig It! Contest
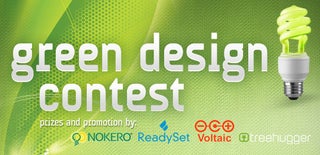
Third Prize in the
Instructables Green Design Contest