Introduction: Wood Stove Heat Reclaimer
I recently moved into a home that had been using wood heat. The chimney had been installed correctly and everything looked ready for a wood stove. I discovered in the barn, the stove which had been used but was suffering from a crack in the heat box itself.After some welding and cleaning up it was ready to re-install. The stove is equipped with a blower which was factory installed. My father had a wood stove which was equipped with a heat re-claimer which was a factory made unit, so I did understand how it was built and how much heat they actually scavenge from the rising smoke. I also understood how pricey these units are. Being a do-it yourselfer, I decided that I could build one just as, or, more effective. I do love metalwork and welding so I had access to a wire welder and sheet metal. I tried to use as much re-claimed material as possible,just because that's the way I like to build.
There is a little work involved, but, I think the time invested was well worth it. Mine has been installed for nearly a month now and I love it. There are a few different ways you could go about building one of these. This is how I did it.Throughout the project, the one thing to keep in mind is safety. Wear the right gear and do it right. all of the pieces need to fit as tight as possible because of the the mere fact that it does involve high temperatures and it cannot leak.
Step 1:
Step 1:
Determine the diameter of the stovepipe you will be connecting to. This will give you the dimension for the upper an lower connectors that you will be making.One must be slightly larger, one slightly smaller.The two large cylinders in the photo are the ones I created.
Step 2:
Now, you need a center body, we will call it the barrel. This is something you can make from sheet metal or repurpose something. This one I found a 3 Gal. pressure tank for a water system. Either way this just needs to be a cylinder with both ends open. Its diameter is up to you and that will decide how many heat collecting tubes will fit inside.Mine was 11' dia with 6 tubes.
Step 3:
Next, for the heat collectors. I used 1 1/2" exhaust tubing from the local auto parts store. So far this is the first expense I incurred. Was about $15.00. I cut it into 11" lengths, you can use whatever you have available to cut them.Might even be able to have them cut right at the store. I will add the next parts here because they are part of this assembly. You need 3 sheet metal discs. My method for cutting was a jigsaw.There are much easier ways,I know.Anyway, 2 of them are slightly larger than the center cylinder because they are the ends.One of them needs to be about 1" dia smaller than the barrel. This will be the cleaning plate which slides back and forth on the tubes to knock off any built up creosote.
Step 4:
Now, heres an important step that needs to be accurate.
Using a scribe or whatever, lay out the pattern for the tubes. the number of tubes you use determines the pattern.You may want to cut a template for this but, all three discs have to be lined up with this pattern. I mean that they have to match. I used a 1 1/2" hole saw and cut the holes out of all three discs. The two end peices can and should fit tight. The cleanout plate needs to slide freely on the tubes. Remember, it cant leak, so, the ends should fit tight. We will make sure of this later.
Step 5:
one more item we need is one 1/4" steel rod about 1ft. long. this is the cleanout rod which will be attached to the center plate so it needs to either be threaded on one end or welded in place on the center of the center disc which will need a 1/4" hole drilled in it's exact center.
Step 6:
Ok, so with all the parts ready it's time to assemble it. I guess I missed a step here so the barrel needs to be cut for the inlet and outlet pipes. ok, now were ready. You will need to put the welding skills to work here.By no means should you attach any part of the pipe connections together by other than welding. And they need to be good welds, cleaned and checked. They dont have to be continuous unless you feel like doing it that way. but the order of assembly is.one end with the tubes attached, the center cleanout plate and the opposite end. your inlet and outlet pipe should already be in place. Next. after welding it I used furnace cement to seal all seams regardless if they were welded already or not. I used a fan which was a small house fan that happened to be the same diameter. I attatched it to what became the rear of the unit.
Step 7:
Heres the step for the fan control. I purchased online a bimetal fan control switch. I think its range is 85 to 180 degree. but it needs to be a N O . You want it to close when the heat gets to temp. This cost about $6.00 shipped.
So, it can be installed where it will be easier to service. I placed mine in the outlet pipe just above the connection. I cut a hole in that spot so the element was exposed to the heat and used self tapping sheet metal screws to make it easier to service.The method for wiring this is pretty straight forward. You can cut and splice it into either line or load, the switch closes the circuit.
Ok,,that's about it. If youre not sure, ask. Thank you
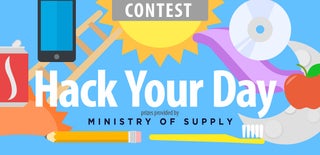
Runner Up in the
Hack Your Day Contest
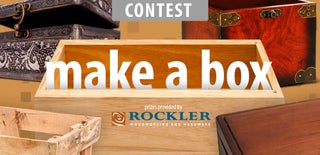
Participated in the
Make a Box Contest