Introduction: Wooden Elephant Tusk
This semester I took a class called "The Culture of Elephants" as an Environmental Studies elective class for an arts credit. For the final I was given the option of either writing a research paper, writing a reflection on a piece of elephant culture, or making a creative project and writing an artist's statement about it. I was quick to choose the artistic project as I am a novice woodworker and am always excited to improve my skills. After learning about the horrors of the ivory trade I wanted to make a tusk and explore the history of the material I used(reclaimed Douglas Fir) versus real ivory.
Step 1: Materials and Tools
Materials:
For this project I used three 4.5"x1''x5.5' boards of Douglas Fir. These boards came from the old bleachers in the gym of the college I attend. When the bleachers were ripped out someone had the foresight to save the beautiful wood for future projects. As you may be able to see, this lumber is from old growth forests with a very tight grain and absolutely no knots to be found. There were a couple of bolt holes and seat numbers but these were easily avoided or planed off.
The other materials I used were simply wood glue, newspaper, and Danish oil (optional)
Tools:
- Electric planer
- Band saw
- Clamps, clamps, and more clamps!
- Hand plane
- Pull saw
- Chisel
- Belt sanders (3"x21" and 1"x21" with 80 grit belts)
- Random Orbital Sander (variety of increasingly fine grit pads)
Note: I currently work as a shopkeeper at my college so I am lucky enough to have access to a large variety of tools but sadly none of the tools used for this build actually belong to me.
Step 2: Designing
If you wanted to, you could spend time modeling a beautiful tusk on a computer program that would give you perfect dimensions and an easier time building it. Instead, I decided to draw it out on a piece of paper then make a full size stencil on newspaper.
Step 3: Prepping the Wood
I planed the wood to remove any finishes, leaving just a fresh wooden surface which would allow for a good bond when gluing the boards together.
Step 4: Tracing the Stencil
Due to the curve of the tusk, it was impossible to align the whole stencil on one board so I decided to break it up into three segments trying to waste as little wood as possible. I found the best alignment possible then bent my stencil over the edges leaving a crease where the board ended. Later I drew the line in with a pencil to make it clearer. I was then able to cut along this line and use these smaller stencils to make the other two parts. (Steps to come)
Step 5: Creating the Three Dimensional Shape
I cut the middle part out on the bandsaw and made two more pieces just like it. Then I laminated the three pieces together with wood glue and clamps. I ended up adding another two pieces to make it even thicker (5" wide, this can be done now or later). This gave me the base for the rest of the tusk and some of the thickness required for the final shape.
Step 6: Creating the Smaller Pieces
With the other two parts of my stencil, I started cutting pieces of wood on the band saw to shape, then laminated five layers together for the end and glued two pieces of scrap together for the tip.
Before gluing the three main components together I used a hand plane and sander to flatten out the sides that would be glued together until they were flush with one another.
Step 7: Gluing It All Together
For the glue up I added two rectangular pieces of scrap to provide additional thickness and a more secure clamping surface. I put the main piece in a vise which allowed me to position the clamps more conveniently.
Step 8: Beginning to Shape
After about 24 hours the glue had dried so I was able to cut all the odds and ends off, creating the general shape of the tusk and checking to make sure it still matched the shape of my initial stencil.
Step 9: Shaping With Hand Tools
At this point it was time to remove the sharp corners off the tusk, giving it its smooth rounded shape. I considered trying to freehand it on the bandsaw but I didn't feel comfortable doing that so instead I cut notches to increasing depths and used a chisel to remove the large pieces in-between.
Step 10: Sanding
The key to getting a shape I was happy with was the use of two of my favorite power tools: a Bosch 3x21 inch belt sander and Makita's 1,1/8x21 inch belt sander. The Makita tore wood away, especially on the inside curves removing significant amounts of material while the Bosch gave it all a consistent smoothness removing any divots.
Note: Be sure to use a mask or ventilator for this step as you are going to be creating LOTS of dust. I was lucky enough to have a downdraft table available for me in addition to my mask.
Step 11: Finishing
To finish the project, I used a random orbital sander with progressively finer and finer grits until I was content with its smoothness. After a quick dusting, I applied a couple of coats of Danish oil following the directions on the can.
Step 12: Questions
If you have any questions about the process please let me know below in the comments! If you happen to end up making a tusk please post pictures below in the comments as well!
Also if you liked the Instructable please consider voting for me in the reclaimed wood contest!
Step 13: The Artist's Statement/ Paper
If you are interested in reading the paper I wrote to go along with the tusk, here it is
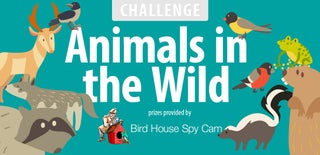
Runner Up in the
Animals in the Wild Challenge
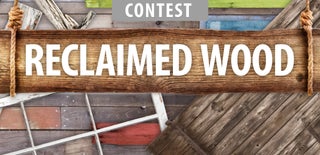
Participated in the
Reclaimed Wood Contest 2016