Introduction: Wooden Sheath for Cook's Knife
I have a knife block full of medium grade stainless steel knives for general use, but I also have a high quality forged cook's knife I keep separate. The duct taped cardboard it came in was okay for a while, but I wanted to make a proper sheath for it. I decided to make a wooden sheath, sort of a one knife block. It's a pretty simple build and I've very happy with the end product.
Step 1: Cutting the Wood
I started with a 1/2" x 4" poplar board. You can use whatever hardwood you want, but in the big box stores around here you get poplar or red oak. Place the knife on the board and mark down 1/4" on either side plus a little buffer. Cut two pieces of wood to the marked dimensions. I wanted a bit of a thinner sheath so I planned one block down to 1/2" thick.
Step 2: Rout the Groove
I used a bench top router and a straight plunge cutting bit to rout a U shaped channel through the thicker block making it deep enough for the knife, but not so deep as the knife it extremely loose. Start shallow and continue until you have a proper depth. Use wood glue along the edges and clamp the blocks together to set.
Step 3: Cleanup Work
I wanted a slight curve to the shealth edges so I ran it through a 1/4" round over bit on all but the side the knife will enter from. That was followed with 60-100-150 grit sanding, a coat of water-based stain, and spray on gloss enamel. I didn't worry about staining the interior because it won't be seen and I don't really want my blade in contact with the stain anyway.
Step 4: That's It
It's a pretty simple, straight forward wood working project. It probably cost about $2 worth of wood. It's easy enough to bang out in an hour or two over the weekend, but a quality product that will hopefully be around for a while. You may even consider padding the interior of the sheath with some felt.
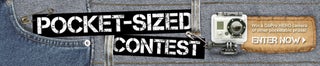
Participated in the
Pocket-Sized Contest
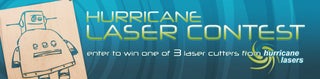
Participated in the
Hurricane Lasers Contest