Introduction: Etching Large Metal Items
Alright first ible, here we go. Used this for my second: https://www.instructables.com/id/Gorget-neck-armour-neck-armor/
Ok so small update, although I got voted up to 4th position the judges didn't find my ible good/relative enough to pass the first round:(, but I still want to thank everyone who voted for my ible!!
I wanted to etch an image onto my neckarmour(gorget) but i found no instructable on how to etch larger metal pieces, just a load on etching smaller pieces(mostly knives). Considering the size of this etching and the size of the metal, it would take too long to do by hand(the q-tip method) and too large to do with the submerged method, so i flipped the submerged method over and came up with this:
Step 1: Tools and Materials
A simple list of materials, if you dont have these items just improvise.
your metal piece
a piece of waste metal
an adaptor / 9v battery (i used a 12.5v adaptor)
few pieces of copper wire
bag of tealights / paraffin candles (i used about 10, it depends on the size of your design)
nailpolish (doesnt matter what colour, wouldn't go for metal colour :P)
nailpolish remover / acetone
exacto knife / hobby knife
lighter
vinegar
salt
lots of tissues
*optional items*
q-tips
A4 sticker paper
pen / pencil
fan
bowl
Step 2: Preparation and Nailpolish
Ok so you got your large metal piece ready to etch, lets begin.
First find or create a nice design you want to put on your piece. print and cut it out with about 0.5cm to spare on the edges.
Second you will need to clean the metal with some degreaser.
Third apply a thick coat of nailpolish the size of your design and add about 2 inches / 5cm to all sides.
now lets just wait till it dries and watch some lego starwars:P
Step 3: Design
Now put on your design either by drawing it onto the nailpolish, or glue on your printed design (I used sticker A4 paper). Trace your design with a hobby / exacto knife, thus carving into the nailpolish. Go slow and steady with this, dont push too hard. if you screw up you can fix it with some nailpolish, but if you scratch the metal its probably permanent.
this step takes really long so put on a series or something and take your time to prevent screwups!!
Step 4: Clearing Your Design
Ok so now you're done with tracing your design(or partially if your impatient like me) so lets start the next step.
first start out by removing all of your design paper / sticker (unless you drew yours) and widen and deepen you traced design.
Next cut out all the parts that need to be etched down. make sure that ALL the nailpolish is removed from the surface that is to be etched down or you might end up with bumps in the middle of your design.
Step 5: Cutting the Candles
Finally! you're done with cleaning up your design after hours of carving nailpolish....
Now cut your tealights / candles in half and place them around your design untill it's completely surrounded. Cut some more in 4 pieces to put on top / in between the halves to fill up the holes.
Step 6: Candle Dam
When you have enough candles cut, you can start building a candle dam. This is why this instructable is different from the rest;).
Start out by slightly melting the flat side of the candle halve and stick them around your design, make sure that the candles are on top of the nailpolish edge around your design so there is no metal(except the carved design) exposed within you candle dam.
Have 1 or 2 candles lit nearby so you can pour on some molten wax to seal the edges and secure the halves.
Next place the quarter candles in the gaps between the halves and secure with more molten wax. keep this going till you have a dam all around your design. make sure there are no gaps and no metal exposed that is not part of the design, use some more wax if needed.
Be sure to keep your design clear of any molten wax.
This method can be used (as shown in this ible) on curved surfaces as well.
Simple and short step, walk over to the sink and fill with water to check for leaks. if there are any leaks dry it off and seal with more molten wax.
Step 7: Etching
Ok so now we are ready to etch. DO THIS IN A WELL VENTILATED AREA!!! during this process harmfull gasses are produced like chlorine gas. Its common sense to do a test piece first to check how long you need to keep the current connected.
Using a battery is not recommended for large pieces because it will probably take a few batteries.Connect a piece of wire to the positive (+) side of your battery / adaptor and to the metal. the best place to connect your wire to the metal is on the underside in the middle of your design.
Now take your scrap piece of metal and connect a wire for your negative (-) to this piece.
Mix your vinegar and salt (in a bowl) and place your project on a stable and level surface. fill your candle dam with the vinegar and salt mixture. Take a q-tip and rub in the solution into all the fine lines to make sure there are no airpockets.
Place the scrap piece of metal (with the negative connected) in the solution in such a way that the two metal pieces dont touch. When everything is secure and safe plug in the adaptor / connect the battery and leave so you dont inhale any gas.
now its waiting time, it takes a while (mine took about a half hour) for the metal to get etched.
I don't know if it helps but i think it does, if you take a q-tip and every 10 minutes or so just wipe the design clean to get the oxide and bubbles off.
Step 8: Cleaning and Reveal
After the excruciating wait (you should have done a test to check how long it needed) the time has come to clean and reveal you masterpiece. start of by dumping your vinegar / salt solution and breaking off the candle dam.
Wash off any vinegar and candle wax left in the sink.
Now its finally time to reveal your hard work! take some nail polish remover / acetone, put some on a tissue and start removing the nailpolish.
Stop and admire your work once in a while.
Once fully cleaned grab yourself a beer and ride into battle looking sharp;)
Cheers!
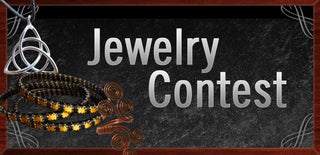
Participated in the
Jewelry Contest