Introduction: Mini Circular Bench Saw From Scrap [UPDATED]
Try to salvage little electric motors from scrap, because you can usually find a way to reuse them. I don't remember where this motor comes from, I've got it many years ago when I used to dismount everything I bumped into, anyway when I found it the other day I immediately pictured a small bench saw to cut metal. Not wood, because motor has a belt and a ratio so that the gear turns at a speed of about 600-1000 RPM which is good for metal, bricks, stones but wood needs very fast speed. To cut these materials you can use a disc grinder, so I bought a pair of discs to apply to my motor.
[UPDATE] I also can apply a disk of sand-paper if needed. To check speed of the disk see last step.
Step 1: Motor and Pulley
I already put together motor, pivot, belt and gear with a wood block when I was a boy, so I left that mounted. The pivot is a very sturdy steel beam and at that time I drilled an hole in the wood and I wedged the pivot into it. The gear has not bearings but uses a metal bushing to rotate around the pivot. The mechanism you see around the little gear on the motor pivot is meant to release the rotation when motor stops, anyway I don't need this feature.
The motor has 30W power, and with this gear the final disc has a very strong cutting force.
Step 2: Finding a Fastening
To attach and change easily the discs on the gear I needed a simple and effective way. After some research I retrieved a piece of hydraulic pipe and a cylindrical nut. Since the pipe's external diameter is almost equal to the disc hole measure, and the pipe fits very good on the gear's steel pivot, that solution works perfectly. I only had to glue with two-components adhesive the pipe on the pivot, adding a plastic ring where discs will be pushed by the cylindrical nut. This nut is very easy to tight by hand, and changing the disc will be fast.
Step 3: The Base and the Top Surface
Also to build the body of the saw I used what I already had, so you can see some wood boards and a little metal L beam, which I thought it was good to keep the disk adjacent to the plane edge.
Step 4: Gluing Together
With vinyl glue I attached the three wood parts together, I clamped them with a pair of vises, and I left everything to dry meanwhile I carried on with the making.
Step 5: The Disc Runner
Using a pair of existent holes in the metal L profile, on the thinner side, I screwed to the wood side edge. With three washers for each screw you can keep the space for the disk. Just add or remove washers if you change disk thickness. The disc obviously has to rotate freely.
Step 6: The Electrical Section
Since the motor had a big capacitor and an ON-OFF switch, I left everything in its box. To lock this box on the left side of the saw, with the switch on the front, I drilled a three holes in the wood and added a pair of holes in the plastic container.
After closing everything the switch is easily accessible and the electric box remains under the wood top board, so it's not very ugly to see.
Step 7: Last Details
I ended up to change the cable and the wall plug, since the original one was too much rigid. Then I added four silicon feet on the bottom four corners. You can see the other disc I bought, that one is to cur bricks and stones, who knows if I will ever use it ;-)
I know that I will have some problem when the discs will wear out, and the diameter will reduce, but anyway I don't imagine I will use it very much for long operations.
Step 8: Ready!
Woah! The new mini circular bench saw to cut steel bots, copper circuit boards, metal plates, or to refine screwdrivers heads or to make many other operations, is ready to use! Admire it in all its ugliness! ;-)
Step 9: [UPDATE] Sand-paper and Disk Speed
I found very useful applying a sand paper disk. And with the occasion I also checked the speed of the disk. Looking the angle covered by the white paper in the slow photography we can easily determine the exact speed. Indeed, since the photo exposure is 1/20 sec, and the disk makes in that time less than half turn (let's say 3/8) we can calculate that 1/20 * 8/3 = 0.13 secs to make an entire turn, and 1 / 0.13 = 7.5 revolutions per second, which is the same as 7.5 * 60 = 450 rpm (revolutions per minute). A good speed to not burn wood or melt plastic.
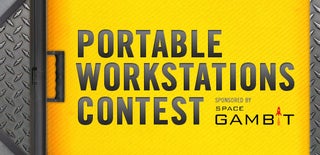
Third Prize in the
Portable Workstations Contest