Introduction: 3D Printed Rey's Blaster From Failed Print
After the exhilarating Star wars Force awakens, I am sure all crafty minds are at work.There are some cool instructable on the site featuring the costume and hairstyle of Rey.
This powerful new character not only embody the moral of Star Wars, but also carrying the torch of the original trilogy. More symbolically represented as Han Solo handed her a blaster before meeting Maz. This Blaster is certainly more streamlined and modern as thee design style goes. It undeniably shares similar form language with the kit-bashed Mauser that Han carries.
As a 3d modeler, and a forever 8 year old inside, I have had the opportunity to model and print my version of it! I wanted to make it for my girfriend as a secret project! I hit some speed bumps along the way, but there is no stopping me!
This instructables also aim at showcasing that 3d prints are not end game. Polishing and further fabrication are crucial! 3d prints are not computer replacing machinist and sculptors, it still needs some love and craftmanship as an extra push on perfection! you can see the evil layer shift and spagetti...
I created the 3d model myself you can download it for free in limited time!! Let start!!
Step 1: Material and Tools
Material:
- SuperGlue
- modeling clay or modeling putty
- plastic film (old file holder)
- Spray Sufarcer
- Black and silver Spraypaint
- Acrylic paint (red, black, yellow)
- newspaper
tools
- Sanding paper
- Sanding file (i used the manicure kind, works like a charm)
- coping saw
- briushes
- scrapped fabric
Step 2: 3D Modeling
A week before my final exams, i bumped into a tested video on youtube. They released a video with their friend punished Props. They covered a design they did and released a free blueprint.
I was motivated and went ahead modeled my blaster after that. I also found a few pics other took at a prop exhibit of some sort. i did in around 2 hours, which is a bit off my game. hehe. For those of you who really love 3d printing, you should always model what you wanna print! my rationale being you dont own it, unless you modeled it. Same applies to everything, designing pep files versus downloading/printing/cutting it without understanding pep files. The mental process is more fun then pure manual work! The work and hence sense of fulfillment is mental versus manual.
This is a discipline call hard surface modeling, where you deal with geometric forms like nuts and bolt rather than sculpting an character. There are tons of approaches, In CAD drawing, you only deal with shapes and the computer will do all the work regarding vertices. CAD is probably the faster and intuitive method, like addition and subtraction of primitive forms. But Cad drawing usually do weird things with bad topology and unnecessary polygons. As a Modeler, i hate both of those, they mean large file size and slow in render. So i dive in a different path, i push and pull every edgeloop and vertex.This way i have complete on control over my model and it is good for printing, rendering or even as game asset.
Here is the time lapse of my modeling workflow. one small note is that for joints and peg, you may want a tolerance, which mean the female and male of a peg/joint should have some extra room, if they are the same size, they most likely wont fit, regardless of the manner of fabrication.
attacched also the Vector design of a vinyl cut in did as an accessory to the prop piece.
Step 3: Life Gives You Lemon
Again, i dont own a 3D printer, cus i am just a broke student. I have been using the Printer at my school. how ever, the staff has no love for the machine, they have poor maintenance. The UPBOX is in a sad condition, pumping out fail print all the time. on top of that i have to register on the tight schedule they have, compete with people who download models from thingiverse simply cus it is "COOL".
The targeted assembled size is around 10 inches. It is a balance between my allowed print time and real life scaling.
I printed my model and after hours of printing, i have to go back to school and retrieve the print the day after, only heartbreakingly knowing that the print had failed. the problem is their poor maintenance cause the base plate/bed to shift during printing, and hence, there are major layer shifts, i even lost a complete part.
They told me to book the next available session for a reprint which was 2 weeks from that time. I manage to find their rubbish bin and salvage the poor piece of PLA. I swore to do it justice!
Step 4: You Make Lemonade
The layer shift is a big problem. They are like earthquake ripping a vault. These shift destroy some pegs and slots. So i cut the pieces at the vaults, with a coping saw. so that we can relocated the pieces and fix the pegs.
The toughest part would be the two grips. Cutting out dozen of pieces and keeping them until you glue them back on. Chance its you got distracted by your dog and lose a part, or the part was ruined straight from the printer. You need some old folders or plastic sheet that is easy to cut and glue compensating the lost part.
An Other tip is to use airdrying clay or modeling putty to fill gaps and cracks.
This is a good practice for being patience, and to develop deeper understanding with your model at a different depth. Since the model is not printed as you intended, its like seeing the principal with your kid cus it messed up. i am not a parent, but i guess the love and hate of building is somewhat similar.
Step 5: Sanding, Priming and Painting
Rough sanding was required, Since i had no choice but to print in .2mm vertical resolution deal to the limit print time in my library printer. Sanding is necessary not only to eliminate the print lines, but also to roughen the surface a bit for the paint to grip tightly.
I applied 4-5 coat of primer, with light sanding in between, to patch up some surface imperfections from the layer shift.
After which, i spray painted it black as a base coat, i tried the gloss type which was 2 year old, but it bit me later on, it starts peeling off. I had to redo it with the matte black again later. This mess happened in a blink and was overwhelming i forgot to take pics of it.
Then it is the metallic spray paint. My advice is to go a bit over on the shiny aspect, this can be achieved safely with more layer of thin paints. Cause you will cover this layer of shininess with weathering and lacquer. the shininess will be tune down.
Before the lacquer, you would like to give your prop a weathered look, by brushing on black and dark colors on the prop, and wipe them away as much as you could. this process mimic how dust and dirty will be collected on the creases and cracks over time in usage. Picking the right color can your your unique story! here are some translation from color and possible story element.
- black = dust, machine grease, burnt mark
- red = rust, dried blood
- green = mold, minerals
- yellow = mud, sand
- purple = burnt mark
When you are happy and comfortable with the weathering, you can choose to hit it with 2 layers of lacquer, this may not be what you want. But for long term, this does help protect the paint job against water, humidity and minor scratches.
Tips:
introductory note for spraypaint: For glossy spray paint, the more layers your build up, the shinier it gets. The glossiness of Lacquer comes from smoothness, While the metalic spray paint not only have the smoothness, but also the tiny sparkling particles. The effect of the sparkling particles will be tuned down by Lacquer on top.
Step 6: Final Words (on This Project)
As a fan of Adam Savage, No blaster model is completed without a felt-laying case. So here i made it for my baby girl!! i made the case with a cardborad structure with a fancy paper on the outside, i saw my mother did sth similar as book case. I went straight to cutting and gluing.
From fail print to a classy gun case, none better example of phoenix rising from the ashes than this. This case is not really part of this tutorial, it is more a shout out for my Girlfriend and give this prop a deserving settlement! i could teach you at this point even if i wanted to, the instructable editor keep giving me server error when i try to upload new pics! Sorry guys.
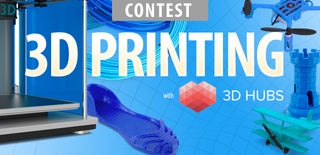
Participated in the
3D Printing Contest 2016
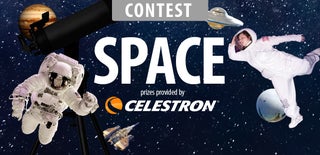
Participated in the
Space Contest 2016