Introduction: How to Make Custom Electronics Panels (Beginners Guide)
Have you ever wanted super cool and easy to make control panels for your fancy projects and cool gagets?
Well look no further than this instructable. With the use of a CNC and Fusion 360 this has never been easier!
Here is a quick and easy tutorial on how to use Fusion 360 and a CNC to make custom electronics control panels for your projects and gadgets. You could also use a laser cutter to do a similar idea by layering thinner wood (if you do not have a CNC on hand).
Throughout this instructable I will demonstrate this process by showing how I made a control panel for my cabinet egg incubator project.
Supplies
Tools:
- CNC
- Vernier Callipers (Or ruler - clear works best)
Software:
- Fusion 360
Materials:
- Plywood
Note. Premium plywood is often rather expensive (especially for the thicker stuff), so a cheaper alternative that also works well is using a 19mm thick panel of pine and using a thicknesser to get the desired thickness (12mm in my case).
Step 1: Designing the Panel
The first portion of this project is up to personal preference. The layout of parts and where they sit on a control panel is entirely up to you. I would highly recommend sketching it out first to see how it looks and even cut it out in a cardboard box first to see how it all feels in real life (as a drawing can only get you so far!).
Once you are happy with your layout fire up fusion 360 as it is time to get some dimensions ready!
Step 2: Fusion 360
Normally manufacturers should provide dimensions for panel cutouts when mounting switches, buttons, LCD's, LED's and the such. However, in the chance you have salvaged a part or can't find any dimensions online, get our your vernier callipers (or ruler, a clear ruler works best) and measure the dimensions of the part. Remember, you want to slightly oversize your holes so that it fits in snugly, but not too much such that it wobbles around. I often do a test cut in a scrap piece of wood when I use a new part for the first part then save the dimensions for the future!
Remember, a CNC cannot cut perfect internal 90 degree corners (due to cutting bits being cylindrical), so make sure you add "Micky Mouse Ears" (Also called dog bones) to your corners. These are essentially rounded corners that still allow rectangular objects to fit.
Once you have all the dimensions noted down, start a new sketch in Fusion 360 and layout all your parts. The reason a CNC is so valuable in this case is because it can cut in multiple depths (unlike a laser cutter). I like my control panels to feel solid and to withstand small collisions and so often use 12mm thick wood, however most switches and LED's as well as threaded components such as rotary encoders or potentiometers often are designed for 1mm to 3mm panels.
Because of this we want to cutout the correct sized hole the entire depth, and then cut out clearance in the remaining 9mm (if you use a different thickness of wood you will need to adjust this depth to suit). For most parts you can simply use the Offset function in the sketch library however, for parts (such as potentiometers) where the main shaft is off-centred you may need to take some more measurements and design a new shape surrounding your panel hole.
If you wish to add text or icons create an SVG or DXF in your program of choice (mine is Adobe Illustrator) then simply import it in the top right corner of Fusion 360 and place it on the sketch where you want. Do note you will need to use a V-Carve bit for the best results here and this can get slightly more complex with tool changes.
Step 3: G-Code
Your CNC will likely use different firmware than mine, however regardless it needs G-Code to know where to cut. Fusion-360 can do this for us if we go to "Manufacture" instead of "Design" in the top left drop-down menu.
We will need to create a setup and then click your model and set the origin. Then we can choose 2D contours for the cuts that go through the entire depth of the material and Pocket for the clearance cuts. Additionally, you can use Bore if you have a cylindrical hole, or just load in a drill bit into your CNC and have it drill it out for you.
If you have never used this aspect of Fusion-360 before it will prompt you to create a Tool or get you to choose from the hundreds of precompiled ones (This has been made very easy and is self-explanatory).
Finally, you can right-click on your setup to see Manufacturing Time and Simulate. ALWAYS make sure you simulate your entire cut to make sure you have no unexpected errors that could snap bits or ruin your project! When you are happy you can Post Process into the format your CNC can understand.
Step 4: Tool Settings
I don't want to go too in depth with tool settings as every CNC bit is different, and every CNC is different. However, it is very important to get your feeds and speeds correct, I would highly recommend always testing them before working on your actual project.
Step 5: CNC Time!
Now we are onto the last step!
Plug in your CNC, clamp down your work-piece, get it all centred and ready, then load up your fresh G-Code! Then with any luck you will have a beautiful project panel for your gadget or project.
Step 6: Finishing Touches
Now that your panel is all cut out and ready, it is time to add any final touches. You could paint it, stain it, or add any other cool details or images with a laser engraver!
For example, I like to paint the edges of my clearance cuts a dark brown/black because I think it looks nicer.
If you have any text engraved and want it to be to be darker (or lighter) than the rest of the wood you have a few choices;
- Use a laser engraver, the burn will appear darker (this works best for lighter woods)
- Stain/paint a thin layer of colour before engraving, the engraved letters will then cut into the "true" colour of the wood underneath making a contrast
- Apply tape on your surface before engraving, this way you can paint the engraved letters without making a mess, then once the paint is almost dry you can peel back off the tape
- Finally you can do a deep cut (or cut out the letters entirely) and use a separate piece of wood (that is lighter/darker) and insert it into the void
I hope this instructables helped you in someway and all the best making stuff!
Step 7: Inspiration
Just a few photos of some that I have made, in some cases I've used a laser cutter to make a box with finger joins, then used the CNC to cut out slots and clearance pockets.
Hopefully it can inspire you to try this out as well (:
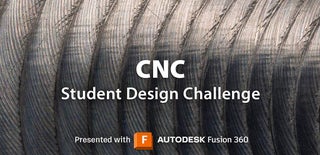
Runner Up in the
CNC Student Design Challenge