Introduction: Bicycle BoosterPack: a 3D Printed Portable Electric Assist
I really wanted an E-bike but I didn't have $4,000 for a brand new one, or even $1,500 for a hub motor conversion kit. So instead I created a third option: Alow-cost high-value E-bike kit: The ‘Bicycle BoosterPack’.
The BoosterPack leverages custom 3D printed parts so it can quickly mount to almost any bicycle to give it an electric boost at the push of a button!
It's a great option for anyone in need of an occasional boost to get up a hill, blast through an intersection, or to take the edge off & prevent sweating.
Primary Features:
· Versatile: Multiple configurations let to mount on most adult road bikes.
· Affordable: Compared to the similar $1,000+ 'Add-E' & 'Go-E' commercial products, <$300 is a steal.
· Simple Operation: Hold the button to boost, let go to resume normal riding.
· No Parasitic Drag: The drive fully disengages from the tire when powered off.
· Can be Removed in Seconds: Take it inside to recharge and prevent theft.
· Light Weight: Weighing in at 4 lbs with the battery (6s, 5Ahr, Li-Po).
· Powerful: Up to 25 mph top speed with pedal assist. 660 Watt output.
· Range: A 111 Watt Hour battery pack gets 5 mi of pure boost & ~10+ mi of assisted range.
Limitations:
· Cannot drive a wet tire. (Though it is electronically water resistant and rain is not a threat.)
· Cannot function on bikes with rear wheel suspension. (Front or seat suspension is fine.)
· Cannot drive knobby tires. (See image in next step for details)
.
This instructables will provide some background on how the BoosterPack works and show you how to assemble your own using the 3D printable files & hardware kit I've made available for sale!
*Link to the 3D printable BoosterPack STL files on Pinshape.
**Link to the Hardware & 3D printed Parts Kits on EngineerDog.com
(If I sell out and you are still interested then send me a message!)
Step 1: HOW TO MAKE SURE IT FITS YOUR BIKE
The BoosterPack is highly adjustable and is intended to fit on most adult size road bikes. It has different configurations to give you multiple mounting options in case one way doesn't fit. Reconfiguration can be done with the two hex keys included in the kit!
In all configurations the BoosterPack needs to be able to clamp to your bike. The adjustable clamp design can mount to round seat posts and frame tubes between 21mm & 39mm in diameter. (This criteria encompasses the vast majority of bicycles.)
You can check to see if it will fit your bike by printing out the attached pdf files (no scaling) and holding them up next to your bike. (See step 9 for detailed mount instructions)
Note 1: The BoosterPack does not work on bikes with rear wheel suspension. Having a front, seat, or no suspension is fine.
Note 2: The drive uses friction to drive the rear tire and so needs an adequately smooth tire surface to grip. See attached tire chart for details.
Step 2: BILL OF MATERIALS
(See attached excel document for a line by line version of the BOM and some performance calculations. Updated 11-18-16)
Hardware:
There are 70 total (27 unique) 'non-printed' 'non-electronic' parts on the BoosterPack, some of which require special tools to make. It would be cost prohibitive for an individual to buy all of them piecemeal, so I have made the hardware available as a kit here. This kit includes everything seen in the attached image with the red numbers. UPDATE-See this google sheets document for specific links to the hardware used in this kit.
.
3D Printed Parts:
The stl files and print instructions for the 3D printed parts can be downloaded at this link. If you don't have a printer you can send the files to a local maker found through 3dhubs.com, or you can purchase a prefabricated kit from me here. The parts in my photos were made from ABS on an original Printrbot, but PLA+ will work too. Printed parts do require a bit of post-printing-processing (such as tapping) to make them usable. (This was already done for you in the kits!)
.
Drive Electronics:
Update 1: Also sold here: http://www.michobby.com/product/maytech-5065-220kv...
Update 2: Also Here: https://hobbyking.com/en_us/hobbykingr-tm-x-car-be...
The electronic drive components used were designed for hobby remote control aircraft & 'truggys'. These parts have become popular for use on electric skateboards in recent years so they can be tricky to acquire. HobbyKing.com is generally the hobby community's go-to supplier but even their stock is not to be relied upon. (Any links I post here will surely be bad in a few months). So if you want something specific then you will have to have a contact in China.
Don't worry, I will hook you up with mine. Maytech is a reputable manufacturer of these parts and will make them per your request. Contact Yina at yina@maytech.cn and tell her Michael from EngineerDog.com sent you. Ask for these parts:
*Standard Motor: 50mm outrunner, Part No. MTO5065-220KV
*Standard Electronic Speed Controller (ESC): Part No. MTC150A P-SD
*LED Programming card made for the above ESC.
.
Battery & Accessories:
*Banana Connector For ESC to Motor (only connecting 3 wires)
*Bullet Connector for ESC to BATTERY (only connecting two wires)
.
Throttle Electronics:
.
Alternate & Optional Parts:
This project has lots of room for customization and accessorizing, here are a few options:
*Battery Charging Safety Bag to put your battery in during charging.
*Battery Watt Meter for measuring performance.
*You can add a hall effect sensor to any Maytech motor by adding '-HA' to the end of the motor part number. (I recommend NOT doing this because my system functioned worse on this project with the sensor plugged in! If you want to attempt anyway then you will also need a 'JST-ZH' connector with 1.5mm pin spacing from somebody on ebay.)
*Large Motor: 60mm outrunner, Part No. MTO6355 - 200KV This was the big motor I experimented with but was unfortunately unable to get to function as a BoosterPack. (see the Big Motor Step later)
*Since the motors are custom made you can request to get different KV ratings! Refer to my excel document for calculations on the effects of different variables.
*Bike Headlight & Brake light to stay visible and safe!
*The VESC motor controller: An ESC actually designed to allow RC hardware to be used on EV's.
Step 3: TOOLS REQUIRED
You will need the following tools:
*Hex Keys (Included in hardware kit!)
*Phillips screwdriver.
*1/4" -20 Tap (for threading the plastic holes.)
*Drill with drill bits, sizes: 1/8", 5/16", 3/8" (Used to clean up printed holes.)
*Soldering iron with standard soldering consumables.
*Wire strippers.
Step 4: ASSEMBLY: PREP THE PARTS
*Please be aware: that there were some minor changes that occurred after I took these photos to simplify or improve the. I.E. In the hardware kits, the nylon set screws were replaced with stainless steel ones, and the carriage bolts were replaced with hex bolts which can be installed using the 3d printed tool.
*Be sure to follow the photos in the order they are shown and read the overlaid notes for the specific assembly details.
The first step is to prepare the 3d printed parts. No matter what kind of printer you have this step is necessary. You have to form the threads in the appropriate holes and use drill bits to make holes perfectly round and smooth.
Step 5: ASSEMBLY: FRONT SUB-ASSEMBLY
Note that the purple parts shown earlier for the other configuration have the same number of holes in different places and are assembled the exact same way.
Notice that there are two different lengths of set screws in the hardware kit. Here the short ones are used to lock against the nut head to ensure that over tightening doesn't cause the nut to strip its hole.
Step 6: ASSEMBLY: REAR SUB-ASSEMBLY
NEVER crank down on set screws too hard or you will strip the threads out of the printed parts! (But to be perfectly ambiguous, you'd be surprised how durable the threaded holes have been on mine). Snug tightening is recommend. When assembling the shoulder bolt DO crank down tightly to make sure its seated all the way. (The assembly is designed so that the motor arm should still swing freely when when tightened firmly.
The purpose of the spring in this assembly is to keep the motor pulled away from the tire when not in use. (The sudden acceleration of the motor will throw it into the tire.). Rotate the 'spring tension nut' in the direction you want it to pull the motor, then you tighten the two set screws down onto the head of the shoulder bolt. You can vary the tension in the spring by pulling it back as far as you want before locking it down, though in practice you shouldn't need more than 90 deg.
Step 7: ASSEMBLY: MOUNT TO FRAME & WIRE IT UP
For now I'll just treat the servo tester as a black box because the detailed wiring of the throttle is discussed in a later step.
*If you don't use a sensored motor then the three ESC wires can be plugged in to the motor in any order. If you want the switch the motor spin direction then switch any two wires. If you do have a hall effect sensor then you will have to trial and error until the motor functions, just keep your finger on the OFF switch for those tests when the connection is incorrect.
**The polarity of the ESC battery wire is important! Red is +, black is -. The bullet connectors that come on the battery prevent an accidental reverse connection, but the ESC comes with bare wires. So be aware of polarity when soldering the ends on. (See the BOM for the end connectors I recommend.)
**The motor wires are zip tied to the swing arm so that if you tug on the wires it doesn't rip them out of the motor. This is called "strain relief".
Step 8: ASSEMBLY: BUTTON IT UP
See images and the notes attached to them. The two sub-assemblies attach to the frame and are held in via 8 silver screws provided in the kit. These screws are specially designed for plastic and have a slightly triangular cross section to prevent self loosening. They will also form their own threads the first time you screw them in.
There is a lot of velcro provided in the kits and each has its own specific use. The reason the battery needs the adhesive back velcro strips on it is twofold. To prevent it from sliding off the back of the frame and to act as a barrier between the battery and the heads of the screws.
Step 9: MOUNTING ON BIKE & ADJUSTING
This step is super important: If you do not adjust the pack correctly then it will not work! All images in this step are important.
My bike happens to be in the sweet spot where all 3 configurations will fit it in both motor sizes. Not all bikes can expect to be able to do this, but all configurations function equally well and in the same way anyway.
You use the set screws to limit the travel of the motor so that it is held away from the tire by the spring when not in use by about 1/8" at most, and it should engage the tire by about 1/16" when in use (not much!). Do not allow the center of the motor to go beyond the imaginary line drawn between the motor arm pivot and the center of the tire!
The drive can be finicky to adjust the first time you do it until you get it figured out. One you find its happy place use the hose clamp provided in the kit to clamp onto the frame/seat post to act as a hard stop so you can quickly find the happy place again.
The BoosterPack is not intended to be used when the bike is not moving! The starting torque on the motor would be too much so you must ride at least 5 mph before engaging the motor!
*When clamping to the seat post or frame its desirable to crank on these handles a bit. They have to be clean, tight, and even between the two sides or else the BoosterPack will rotate when you engage the drive. You should be able to tighten them with your bare hands without trouble, but if you feel the need to use a tool then use the printed wrench which should help just enough but not allow you to over tighten.
Step 10: THROTTLE WIRING
Technically you could just use the servo tester as purchased and control your motor speed with the little knob. But that would be a terrible throttle design because it wont spring back to zero speed if you lose control, and because the act of turning the knob will induce a low acceleration on the motor so it wont swing hard enough to fly out and engage the tire.
This step requires a little soldering and wire cutting to do but the intent is to created a single ON/OFF momentary button throttle. This took a bit of playing around to figure out but I realized that you could do this very easily by replacing the 10kohm potentiometer with a resistor and then using a button to short the output side of the connection. The servo controller was made for an analog input but now it only senses a null input or a signal to go full speed!
The servo tester connects to a 3 wire cable that comes out of the ESC. The cable has a white(Signal), red(+), black(-) wires. This cable must be plugged into the the servo tester in the correct orientation or it will not work.
The servo tester has a button on it that can change its settings but this is mostly a hindrance for this project. 'Manual' is the only setting that makes sense for use as a throttle while the others could cause the drive to start at undesirable times. Set the servo tester to MAN then desolder the button so you can't accidentally press it.
TROUBLESHOOTING:
*The throttle is probably the trickiest part of this project so if it doesn't work immediately here are some things to try:
*Make sure your electronics and motor all function with an unmodified speed controller, this removes the 'custom wiring' variable from the equation just to make sure everything else works
*Use a multimeter to double check that the throttle switch is electrically functioning.
*The 3 wire pin that goes from the ESC to the speed controller is polarized, so if it is plugged in backwards then it won't work.
*Make sure you used a 10K resistor, I don't know what would happen with any other size.
*Make sure the speed controller is in manual mode, which is shown by the first LED lighting up.
If it STILL keeps screwing up I would suspect a bad soldered connection somewhere.
*Watch the throttle calibration procedure on Youtube here: https://youtu.be/e0H5AryLz0g?t=524
Step 11: BATTERY USE & CARE
As anyone familiar with EVs already knows batteries are the biggest limitation. For this project I needed a physically small package that could sustain a ~30 amp output. The only chemistry capable of doing this at a reasonable price is Lithium Polymer (Li-Po). The energy dense Li-Po batteries are quite safe when handled appropriately and I have never had any problems, however, they are not 'kid proof.'
Improper care of these batteries will ruin them and become a hazard to you. You must follow these instructions!
*The battery I recommend is a 6S (22.2 V), 5 Amp Hour, Lithium Polymer (LI-PO).
*Nominal Cell Voltage: 3.7V
*Safe Storage Voltage: 3.8-3.9V (Between 22.8 - 23.4 Pack Voltage)
*Max: 4.20V (25.2 Pack Voltage)
*Min: 3.00V (18 Pack Voltage)
*Recommended Programmed Cutoff Voltage: 3.2V per cell (19.2 pack voltage)
*Never store LiPo batteries fully charged, not even for a week.
*Maximum charge current is always 1C (that would be 5 amps for a 5 amp hour pack).
*Never charge the battery unattended. A fire proof charging bag can be a good bit of insurance if you are concerned.
*That is all you need to know to get started, for the curious, there's lots more info on battery care here.
.
~I also experimented with the super safe LiFePo4 battery chemistry but I was unable to put together a pack that could sustain the high currents needed for this build.
Step 12: MOTOR SCIENCE
The exact specs of the recommended motor and other hardware used are listed in the Excel document in the BOM step. There is also a tab that lets you change input variables such as motor KV to see what the effect on performance is. This step is to help you understand why I chose the motor I did.
Gearing:
In this application the exterior surface of the motor uses friction to directly drive the rear wheel. It may be counter intuitive but the diameter of your bike wheel does not matter! The wheel acts like an idler gear in that the output rotational displacement is the same as the input. The real variables we control for 'gearing' are the exterior diameter of the motor and the KV of the motor. Increasing the diameter of the motor increases the theoritical top speed of your bike.
Motor KV:
The KV rating is how fast the motor will spin per applied volt (in RPM/V). For the same motor, a lower KV has more windings with thinner wire, while a high KV has less windings with thicker wire. As long as they have the same mass of copper, they will have exactly the same max RPM, power output, torque, & efficiency BUT at different currents/voltages. By definition, the lower the KV the less RPM you get at a given voltage, but the more torque you get in return. Power = Torque x RPM. Unfortunately, manufacturers aren't designing these motor for this purpose and so do not provide enough data to calculate how much torque the motor can produce. All I could do is calculate the torque required by the application as a frame of reference, and experiment with a couple different KVs to see what worked best. From my experience, I recommend a motor between 200 and 270 KV for this application.
Current Capacity:
The motor is by far the weakest link in the drive train. My calculated max current of the 50mm motor is 36 amps. I did an experiment to verify the calc and I got it up to 30 amps before major slipping of the motor relative to the tire occurred, limiting the current. That’s actually a good thing. The ESC is not current controlled so if the motor were to be held in a vice the current would go up to the 100A that my battery can supply and quickly fry the motor. (The ESC would be fine because it handles up to 150A.).
30A is still a lot though, note the 3d printed radial fan I put on the motor. This protects your fingers and helps keep it cool! Note: Neither the motor or the speed control should be hotter than 160-175 degrees F after a five minute run!
Motor Timing:
Electric motor timing is a lot like timing the cam shafts on an internal combustion engine. Basically you are adjusting the angular position at which the energized coils change force application direction. A motor with lower timing will produce more power at low rpm, and a motor with higher high timing will produce more power at high rpm. The best timing setting does not necessarily achieve the max horsepower the motor is capable of, but rather produces the max horsepower within the rpm range you’e most frequently using. I had the best luck with high timing settings.
RPM Sensing: You can order these motors with a built in hall effect sensor to detect the RPMs and provide the motors position as feedback to the controller. In theory this would make the system more effective at doing its job. In practice when I connected the RPM sensor the motor was louder, more likely to screech, and ran hotter. This baffled me but it was consistent across all motors I tested, so my anecdotal recommendation is to do without the RPM sensor. This leaves your system to operate in 'open loop' and liable to losing synchronization between the motor and controller. If this happens it will give off a loud screech and you need to stop immediately! Let it stop spinning and you can start again.
Starting Torque: As mentioned above, This type of motor and the accompanying electronics were originally designed for use in remote control hobby airplanes and the like, so their use here is considered a hack. We have to operate without motor torque curves and such to help design our system. In any case one thing we know for sure about this type of motor is that it is happiest when operating at high speeds. So the BoosterPack is best used for speed rather than steep hill climbing. On big hills is use it to get a running start, but the electronics just cant handle the super high torque of trying to boost when the bike is stopped/slowed. On steep hills when your bike starts to slow down too much it will put extra stress on the motor and you have to stop boosting or it will get too hot.
Lots more info on this type of motor & drive system here:
https://www.instructables.com/id/The-New-and-Improv...
Step 13: CONTROLLER (ESC)
The ESC is the electronic command center of the BoosterPack. It has the main ON/OFF switch and has programmable settings. When turned on it consumes about 7watts constantly, so when you are storing the BoosterPack make sure to turn it off!
Programming Card: These are the optimum settings for the 50mm motor:
1. Cut off voltage: 4 (3.2v/cell) (This prevents you from over discharging your battery)
2. Running Mode: 1 (Forward without reverse)
3. Motor Timing: 4 (High) (See previous step for explanation of timing)
4. Initial Acceleration: 4 (Very High)
5. Throttle Percent Reverse: 1 (20%)
6. Throttle Limit: 1 (0%)
7. Percentage Braking: 9 (100%)
8. Percentage Drag Brake: 8 (30%, set at max to stop the motor from moving when not in use)
9. Motor Rotation: 1 (Normal)
10. Neutral Range: 1 (2%, this makes the throttle button more sensitive)
*For the 60mm motor you may want to turn down the initial acceleration and the motor timing to account for the increased current draw from the motor.
.
Braking: The braking option is set so that when you release the throttle the motor will apply a brake to prevent it from continuing to spin. I use it here because the motor it swings the farthest when it is reving up from a stopped position. If the motor was still spinning from the last time you used it then it may not swing hard enough to right the spring and engage the tire. The brake saves you from having to wait until it naturally stops spinning.
Different ESC manufacturers may use different braking methods, but the model I recommend uses an active brake for an instant hold in either direction by injecting voltage opposite to the motor's spin. Regenerative braking is not possible with the system I used and isn't available in any RC hardware that Im aware of other than the VESC controller. (FYI that looks like an excellent controller for this application if you have a few extra bucks.)
.
Throttle Calibration: The ESC needs to be tuned in to the servo tester and your throttle so that it knows what to do when you press the button. The procedure to do this is putlined in the attached manual but I will reiterate it here. Connect everything like you are ready to run. On the ESC ON/OFF Switch there is a button labeled 'SET', hold this button down while turning on the ESC then let it go. Then HOLD the throttle button until the esc beeps once (This programs in 'go' input). Then press the throttle button once briefly and let go and wait for two beeps (This programs the 'brake' input). Then do nothing and wait for 3 beeps (this programs the 'neutral' input). Then turn off the ESC and it will remember.
!!!!!UPDATE 5-14-16!!!!!!: Maytech just released a new ESC product. For about $40 more than the standard ESC listed below, this new ESC is also designed for use on skateboards but it has a higher voltage tolerance. This allows you to use up to a 12S battery which will give you greater speed and a cooler motor!
*Super ESC: Part No. MTES120A-SBEC
Attachments
Step 14: 3D PRINTING & DEVELOPMENT PICS
The use of 3D printed parts is key to this project because it eliminates the need for expensive custom machining. In fact, if you own a 3d printer then parts are quite cheap to make. (I made the BoosterPack with less than a single $25 spool of plastic.) It may come as a surprise, but the printed plastic parts are plenty strong enough for this application when made properly. I used ABS material with a minimum of 3 perimeters, rectilinear infill, and between 30-50% infill for all the parts. Also, 3D printing also allows you to make it any color you want!
Important Note: The 3D printed parts must be printed in the orientation that they appear when you load the files! 3D printed parts have a directional strength, like wood, and are stronger is certain orientations. Notice the images in this step to see what happens if you print parts in the wrong orientation. Additionally, different infill patterns have a significant effect on strength and I only recommend using the rectilinear infill pattern.
**Printing from PLA would also work, though ABS is recommended.
Step 15: MEASURING PERFORMANCE
Bicycles are the most energy efficient human powered vehicles and electric propulsion is the most efficient form of powered locomotion, so when you combine the two something awesome happens... Electric bikes are the most practical and environmentally friendly short range mode of transportation available!
To help quantify statements like that I did an experiment to measure the performance of the bike with and without the BoosterPack. I used a battery watt meter and my phone GPS with the "Runtastic" app to measure energy consumed, distance, & time while I rode my I rode my bike on the same course twice in succession. The first time like normal and the second time while boosting. Not only was the booster ride faster but I was less fatigued afterwards.
*You can find the stl files for the phone holder I designed attached to this step. It is one of the most useful things I've ever printed. It can mount to your bike, or hang from your car rearview mirror, or mount to a tripod. Just add (1) hose clamp, (1) hex bolt 4" long, (2) 1/4" hex nuts, (1) spring, and (1) nylock 1/4" hex nut.
Step 16: BIG MOTOR OPTION
The standard design uses a 50mm motor, but if you print a couple extra parts as shown in the pics you can mount a 60mm motor to get 20-40% more power! Since this motor has a larger outer diameter it needs to have an even lower KV to 'gear it down' to be the right speed for this use.
NOTE: When I experimented with the big motor my system refused to maintain proper motor timing under load, so no matter how I adjusted it it was unusable. It worked fine in the open air but every time the motor engaged the tire, even when I rode at high speed, it started screeching and I couldn't pin down why! Admittedly these electronics were not made to be used this way, but I think it would work just fine if you were to use the new opensource VESC controller.
Step 17: OTHER EXPERIMENTS
Experiment 1. Improving Wet Traction:
Oh the terrible irony, I made this great toy and recently moved to one of the most bike-able cities in the United States, but the Pacific Northwest is a very wet place to live! The BoosterPack design relies on friction and is unable to function on a wet bike tire. So I tested various grits of sandpaper, coatings, meshes, and rubberized heat-shrink but my conclusion is that ANY material able to grip a wet tire will quickly wear the tire (or be quickly worn) when the tire is dry.
The little black flecks on the bike frame was my tire! But there is a good side to this too. The inherent slipping that occurs between the smooth metal motor exterior and the tire surface is actually perfect for providing enough traction under dry circumstances to not wear the tire at all. The slipping also functions as a clutch and keeps the motor from locking up. So for this reason I only recommend driving directly off the exterior of the motor.
Another interesting part of the sandpaper experiment was the glue selection process. I needed an adhesive that stuck in use but was easily completely removed when I needed to change the paper…that’s a tall order! The result of glue failure during use was also unacceptable. It caused the sandpaper to touch and wear the motor wires and almost cause some MAJOR problems! For the curious, “Zap Goo PT-12” with 24 hours of cure time ended up being the perfect glue for the job.
FYI a 2″ drum sandpaper sleeve was a perfect fit with glue on the 50mm motor, and that's what I used in the photos.
.
Experiment 2. Boosted Scooter:
Just for fun I wondered if the design could be reconfigured to function on other types of vehicles. In this case I mounted it to my favorite ride, an adult size kickscooter!)
The result? Yes it can clamp up, but it won’t drive. The little polyurethane wheels are too slippery to be gripped by the motor. And I'm sure the sandpaper would eat this wheel into oblivion.
Step 18: FINAL THOUGHTS
*E-bike laws vary throughout the US, but this hybrid technology is usually legal as long as you abide regular bike laws. Where I'm from there are no regulations if the system is limited to 750 W and the speed is under 20 mph unassisted, classifying the bike as a ‘low speed electric bicycle’ rather than a motor vehicle. In any case, the bike is still a regular bike when it’s not boosting!
.
**Friction drives have been around for a long time of course, and I was not the first to think of building one using RC components and a swinging motor mount. The ultimate credit for the concept goes to a couple engineers from Australia named Kepler and Adrian, who created the ‘Eboost’ and the ‘Commuter Booster’. This project was also inspired by the work of instructables member BlanTheGenius.
.
***UPDATE: THANK YOU SO MUCH for voting for this project in the Instructables "Bicycle Contest", the "Robotics Contest", and the "Make it Move Contest". I LOVE my new Witbox 2 3D printer!
Step 19: PROJECT UPDATES:
This project is not a one-and-done type of thing. I realized that dispersing updates throughout the instructable made them difficult to find. Here is what's new as of 6-25-16:
1. Free optional accessory: A handlebar button throttle. In the BOM I recommended buying a handlebar button assembly from Amazon but they have since tripled their price This model will enable you to get the same functionality for the price of the switch & a screw ~$5.
2. New Part: 'Locking Tube End Cap' Intended as an optional accessory for the mid-drive mounting configuration. It is a block with a big hole that mounts to the backside of the aluminum tube and is intended to give you a place to strap a bike lock cable through. File available on Pinshape
3. Maytech just released 2 new ESC products. For about $40 more than the standard ESC listed in the BOM, this new ESC has a higher voltage tolerance. This allows you to use up to a 12S battery which will give you greater speed and a cooler motor! Super ESC: Part No. MTES120A-SBEC The second new ESC is their own version of the VESC, ask Yina (contact info in step 2)! (6-4-16)
4. New Video Series on assembly, install, and adjustments out now! (6-4-16)
5. New Throttle design: Spring loaded potentiometer flick throttle as pictured above:
6. New Recommended Safety Accessory: Li-Po Temperature Sensor Probe for your charger http://amzn.to/2dHYujT
7. New Parts: ‘universal’ motor mount, a new ESC Specific mounting plate, and a printable frame tube. All now available with the rest of the purchasable pinshape stl files.
8.New Mini BoosterPack Kits out now! The Mini kit sacrifices configurability in return for simplicity by limiting the mounting choice to just the mid-frame of a bike (the best place to put it anyway).In doing so it eliminates the need for a few expensive pieces of hardware and quite a few 3d printed parts so I can offer the entire thing for a better price and lower the barrier to entry on this specialty toy. Check it out here, Video Demo below:
9. Supplier Update: http://www.michobby.com/product/maytech-5065-220kv...
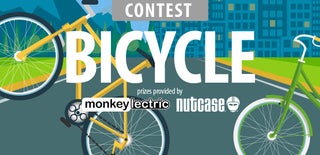
First Prize in the
Bicycle Contest 2016
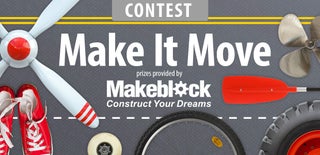
First Prize in the
Make it Move Contest 2016
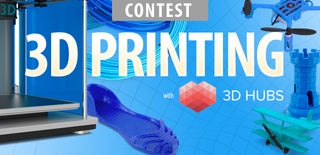
Grand Prize in the
3D Printing Contest 2016
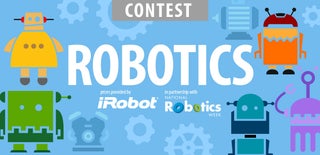
Participated in the
Robotics Contest 2016