Introduction: Casting With Delft Clay (White Bronze Anvil Pendant)
Delft clay casting is just one of many methods to cast metal objects. Delft clay casting has some drawbacks but is arguably the most accessible casting medium for those who are just starting out.
Step 1: Create Your Form
One of major drawbacks to using Delft clay, or other casting sands, is that you can't cast an object with undercuts in a typical two part mold. luckily for me, I wanted to cast an anvil which doesn't have any undercuts from the side. The blue anvil about was hand carved out of medium density carving wax. The material of the model being cast is important because it's going to have to withstand a considerable amount of pressure. let's say that your favorite carving or sculpting medium is something soft like very soft wax or marshmallow, then before you proceed to the next step you would need to cast a hard resin version of it first. Once you have a tough object that you think is worth casting, then you may proceed to the next step.
Step 2: Gather Your Supplies
Before getting ready to cast, you should have a casting frame. You can buy casting kits that come with tiny aluminum frames. My project wouldn't fit, so I decided to build my own. For this project, I didn't have my welder handy so I had to build one out of wood. However you decide to make it, it needs to be two flat forms that can somehow lock together. In my case, the locking mechanism was just some bent steel that kept the two pieces from shifting. Before creating the mold please save yourself some trouble later and put down a tarp or some plastic. Delft clay is just a pain to clean up, especially if you step in it. Delft clay is also reusable so being able to save as much of it as possible would be ideal because delft clay is expensive.
Step 3: First Half of the Mold
Take one frame and pack it with the delft clay. I don't just mean fill the frame, I mean take something like a mallet and pound it until you basically have a solid brick within the frame that can hold its shape. The frame should be overflowing with with compacted clay, take a straight edge and cut the clay level with the frame. Once you have leveled clay, take your model and press it into the clay in such a way that you could later pull it out without disturbing the clay. The biggest part of the model should be toward where the pour point of the frame to allow for a cleaner pour.
Step 4: Second Half of the Mold
Once you have the model in the first frame, you need to cover it in powder. The powder endures that the two halves won't stick together. The finer the powder the better, though in a pinch you can use all sorts of powder. In this instance, I didn't have any talcum powder, though I did have a charcoal block that I scraped over the first frame. With the powder applied, lock in the second frame over the first, and pack more clay into it before leveling it.
Step 5: Remove the Form and Carve Channel
Carefully pry the two halves apart and carefully remove the model. With a sharp craft knife, carve a channel for the metal to travel from the opening of the frame to the cavity. Do this so that both halves match up and create an unobstructed funnel into the cavity.
Step 6: Create Vent Holes and Connect Them to the Form
In order to prevent air pockets from forming in the final product you will need to carve vents. Take a sharpened dowel or a straw and poke several holes into one of the mold halves. Angle the holes so that the ultimately point upwards. This will keep the metal from all pouring out of the vents. with the holes places, carve tiny chanels from the model cavity to the vents so that the air can escape.
Step 7: Put the Mold Together
This step is pretty self explanatory. Put the two halves together to that everything matches up and locks together.
Step 8: Melt and Pour the Metal
Once again, pretty self explanatory. Put on all of your safety gear, set up your metal melting apparatus of choice and melt the metal. Be sure to add borax or some other flux to the metal to keep it clean and flowing consistently. Once everything is liquid then pour the metal into the channel and pray to your diety of choice that it worked. If you use far more metal than you need to, like I did, then some might come out of the vents. While a bit of spillage is a bit dangerous and a pain to remove, it doesn't mean that the rest of the cast didn't fill completely.
Step 9: Remove the Solid Product
Once everything has cooled down, pry the two halves apart and remove the product. The product at this stage will be pretty ugly with flashing and vent spouts poking out from every direction. The next stage is removing all of that and clean up the form. You will notice that some of the clay in the two mold halves has turned black. Remove the blackened clay before reusing the clay because it will dilute the clay overall and make it less cohesive.
Step 10: Cleaning Up the Product
Cut off all of the flashing, grind everything flush, and polish up the product. I realized that I didn't design a finding in the wax model, so I ground one out of the sprue metal that was attached instead of just cutting it right off.
Step 11: Final Touches
I wanted to make the white bronze look more like weathered steel so I oxydized it. I also gave it a couple coats of renaissance wax so that the oxides won't rub off onto clothing and skin when it's worn. Thanks for reading!
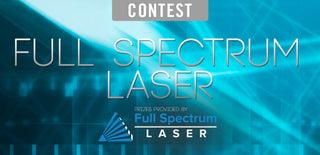
Participated in the
Full Spectrum Laser Contest 2016
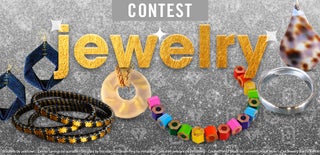
Participated in the
Jewelry Contest
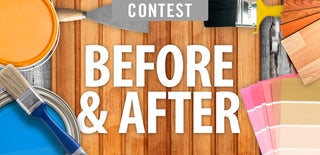
Participated in the
Before and After Contest 2016