Introduction: Casting a Ring
If you are like me, and have very large fingers, most rings won’t even come close to fitting you. The only options that you are left with are to either spend lots of money on getting a ring in your size or to make one yourself. While away from my forge for the semester, I had the opportunity to try my hand at casting with my university’s equipment. I wanted to make something that looked a little sinister, so I decided that I wanted to make a big skull ring for the fun of it.
Step 1: Getting Started
First, I started with a wax tube that is designed to form rings. You can get these tubes in a variety of shapes, sizes and wax compositions depending on the project that you want to make. I used a saw to cut a section that I felt was appropriate for the ring and got to work.
Step 2: Make It Wearable
Before you remove too much material for the decorations, you need to make it wearable. The inside of the wax tube is rather small but the walls are thick, so that you can size the ring. There are several ways to make the hole bigger, but for this project, I used a torch to heat up a ring mandrel and slid the tube down the mandrel until it reached the size that I wanted. Since the mandrel is hot, it will melt out the extra wax. Be sure to do this to both ends of the ring so that the hole is even from both ends. Personally, I like this method because it is fast and leaves the inside of the ring smooth.
After that you shape the ring to be whatever you want. For this ring, I wanted a big sturdy ring shank. To remove the majority of the material, I used a belt sander because the wax that I am using is fairly sturdy. Please note that different kinds of wax will require different methods. The green wax that is pictured is very hard and is better for carving rather than sculpting.
Step 3: Decorate
After that, I added a wax skull from a mold that I made a while ago for just such a purpose. The wax for the skull is closer to paraffin than it is to the green wax, so I had to be careful not to overheat it while joining it to the band. After that I cleaned up the model and got ready to cast it.
Step 4: Sprue It Up
For this project, I was allowed to use a centrifugal casting machine. The first step in casting this way is to sprue up your wax item. The rubber base in the pictures has a little cone on the bottom that will act as a funnel for the metal to travel through during casting and the sprue act as channels for the metal to travel throughout the mold. Typically you should cast with the largest part of the ring towards the sprue base because it will cool slower than the smaller areas and lead to a better cast. For this ring, however, the largest part is also the most detailed part so I had to add extra sprues. As you can see in the picture, there are sprues that lead from the base to right under the skull and to the sides this is so enough metal can reach the skull without having to put a sprue on the skull and possibly ruin the detail.
Step 5: Investment
The next step is setting up the mold for casting. First spray your wax item with debubblizer and let it dry. This will prevent bubbles from forming when you pour investment and help save the detail. After that, coat the piece in you casting investment with a brush. You want to make sure that you get the investment into all of the nooks and crannies. Once this first layer has dried, add a second layer and let it dry. With it all dry, you add your steel flask and pour the investment. Once the investment has been poured, you can either use a vibration table or vacuum pump to remove the air bubbles from the wet investment. After that, you cook the mold based on the instructions for that type of investment. The investment that I used had to be baked for 15 hours at a range of different temperatures.
Step 6: Melt and Spin
Once the mold has been baked and all of the water has been removed, you can load it into the centrifugal casting machine. Initially, I was going to cast this ring in sterling silver, but I realized that I was a little short. Instead, I cast this ring with a sort of bastardized Shibuichi, which is a Japanese alloy comprised of silver, copper and a little gold. Once the metal is loaded into the crucible, put it in the machine and just melt it. Add a little borax to keep it clean and run the machine. Once it’s done spinning, submerge the mold in water to cool the piece and see how it worked.
Step 7: Remove Sprues
The cast piece should be solid without gaps or inclusions. As far as I could tell the casting was a success. The next step is to remove the metal that filled the gaps that the sprues left and to clean away as much of the investment as possible.
Step 8: Grind and Polish
After that all that is left is to grind away any bumps, sand it smooth and polish it. If the design that you wanted requires that the piece be polished then you are done.
Step 9: Patina
I didn’t want a bright shiny skull so I decided to use patina on it. Shibuichi is supposed to yield a very dark rich color if the right patina is applied. The only problem is that that patina requires about a week to make and ordering a bunch of chemicals so that will be left for another instructable. Instead, I applied a patina that is supposed to yield a smooth black color and gave it one last buff.
Thanks for reading.
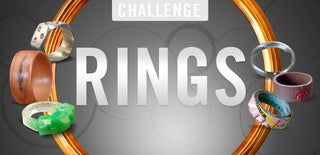
First Prize in the
Rings Challenge
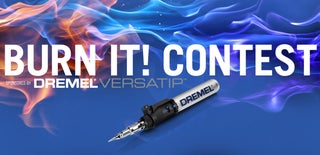
Participated in the
Burn It! Contest