Introduction: Custom Quidditch Bracers
Rough game, Quidditch, but nobody's died in years. And for good reason!
Over the years wizards all over the globe have utilized some form of projective gear to minimize damage caused by a wayward bludger (or a well aimed Beater's bat). One of the most practical and enduring pieces is the humble bracer.
Today I'll be demonstrating how to make a pair of your very own genuine leather Quidditch Bracers - without magic of course. You don't learn anything if you just wave your wand and...poof!
Things You'll Need:
- 6-7 ounce vegetable tanned leather for outer shell
- 3-4 ounce vegetable tanned leather for straps (and trim - optional)
- 1.5-2 ounce pigskin liner leather, or other liner material
- 1/8 inch (3mm) Brown Utah Distressed Lace (or your preferred lace)
- Padded filling (strips of old t-shirts or socks)
- Bison brown Eco-flo dye
- Yellow Eco-flo dye or waterstain
- Eco-flo Matte Finish or your preferred finish
- Tanner's Bond, or other leather/fabric glue
- Sponge or paper towels
- Small Paintbrush
- Plastic container of water
- Tracing film and pencil
- Thin cardboard
- Needle and waxed thread or Stitching Awl
- 2 pronged lacing needle
- 3/4 inch #12 bridle buckles (or other buckle if choice - 6 needed for 2 bracers)
- Strap cutter
- Head knife and/or X-acto knife
- Stitching Groover
- 3/4 inch oblong punch
- 9/64 inch (3.5mm) drive punch
- 5/32 inch (4.0mm) drive punch
- 4 & 6 prong 3/32 inch (2.3mm) Diamond chisel punch
- Multi-size wooden edge slicker
- #3 Edge beveller
- Poly Board
- Poly Mallet
Note: I will show the contruction of one bracer during the following steps, but the same processes can be used and mirrored for the duplicate bracer.
Annoying Disclaimer:
During the creation of this bracer I will be instructing you to use sharp, pointy tools. Needless to say, please be careful. I'd like to avoid a trip to St Mungo's if at all possible.
The finished product is not official protective sports gear. Any injury recieved while attempting to use it as such cannot be attributed to me or affiliated parties. Ain't mutual indemnification grand?
Step 1: Make Your Pattern
After looking at some high quality reference (read: Google image search) and looking at some cosplay versions, I started laying out my pattern. What most reproductions fail to recreate is the elbow guard that extends from the back, but we're going to make it so!
You'll need one cardboard pattern, which will be used for the Armor (the top side of the bracer) and for the Lining. The template can be flipped to be used for either left or right bracers - unless one of your forearms is significantly larger/smaller than the other.
For the Armor Template:
- Grab your measuring tape and take some measurements of your wrist at it's widest point, about 3 inches below your elbow, and from the outside of the wrist to the elbow. Because the bracer won't completely wrap around the forearm, take off about 2.5 inches from your wrist and mid-forearm measurements.
- On a piece of paper or thin cardboard, use the altered measurements to draw a basic rectangle (parallelogram?) from the wrist to the elbow.
- Draw a line 3 inches down from the elbow, and then divide that rectangle evenly in half. One of these squares will be the elbow guard. To help avoid confusion, lightly shade in the outermost squares
- On the unshaded sections use a coin or other cylindrical form (Firewhisky bottles will work) to draw in rounded corners at all the angles. I used my poly mallet head for the smaller curves, and the bottom of a wine bottle for larger curves.
- Cut your pattern free from the paper and cackle like Babbity Rabbity.
- As you'll see in the pictures, I had to significantly cut down one side of the top of the bracer - this is because when I laid the pattern over my arm, the corner was sticking into the fold of my elbow and limiting the freedom of movement. I cut it down to where it felt comfortable.
You have your pattern all ready, now it's leather time!
Note: To ensure you don't wind up making two bracers for the same arm, mark one side of each of the patterns Left and Right. To figure out which side is which, do the following:
- Wrap the pattern around your right forearm as if it was the finished bracer
- Mark the side facing up Right, and mark the underside Left.
Step 2: Grab Your Dragonhide!
Using the paper pattern, we're going to trace out the shapes onto the flesh side of the leather. When laying out the pattern, place it with Left side facing up. This may seem wrong, but imagine you have Mad-Eye Moody's magic eye - if you turn the leather and paper over together and x-ray through the leather, the Right side of the pattern and the skin side of the leather will be facing up.
- Grab your 6-7 ounce veg tanned leather and trace the Armor template onto the flesh (rough) side - this will be the top piece.
- Grab your pigskin or cloth lining - I chose to use embossed cloth lining sold by Tandy Leather. Keep the Left side facing up, then trace onto the embossed side of the liner - this will be the base of the bracer.
- Grab your favorite cutting tool - be it head knife, x-acto knife, or Godric Gryffindor's sword - and cut out the leather and lining pieces.
While we're at it, we should also sort out our padding that will go between the leather and liner. I'll be using old clean socks that would otherwise be tossed out - but you can use any padding material you happen to have on hand. We'll need at the least we'll need 5-6 strips that can be rolled up to form a cushy pad.
- Grab a pair of Uncle Vernon's long socks
- Cut down the length of the sock and open it up like a butterfly
- Seperate the foot from the shin part of the sock, and cut each of the pieces in half
And lastly, we're going to cut the arm straps from 3-4 ounce leather. I'll be using 3/4 inch buckles, so the straps will need to be 3/4 of an inch wide at the most. I've shaved off a millimeter just to make sure the strap slides through the buckle easily. It is easiest if you find or create a straight edge on your leather first.
For the Buckles:
- Using the strap cutter (set at just under 3/4 of an inch) cut out a series of strips about 6 inches long
- Using a piece of scrap, I made a test piece to check where to place the oblong hole for the buckle tongue - for my needs I placed it about 3/4 of an inch from the end of the strip - using the 3/4 inch oblong punch, hammer out the buckle tongue hole
- Fit the buckle in and make sure you have enough room for secure stitching
- I used the test piece as a template to mark the straps for hole punching, then punch those out as well
For the Straps:
- Using the same measurement setting on the strap cutter, cut out a series of strips about 9.5 inches long
- Trim off any unusuable bits (thin spots, scars, or cuts that could harm the integrity of the strap
- With a 5/32 inch (4.0mm) drive punch, cut out the pilot hole - about 3 and 3/4 inches from the end, as well as two other holes on either side about a 3/4 inch or less away
If you are using a different buckle than the one described in list, slide the tongue of the buckle through different sizes of drive punches to find the optimal size.
Step 3: Aguamenti! - Wet Molding the Leather
Looking at the reference images, there are raised sections (I'm going to call them risers) running down most of the length of the bracer, and even one that runs horizontal on the wrist section. To make those we'll be doing some wet molding.
First things first, though, let's plan out which areas to mold. We'll need 4 risers that run most of the length of the bracer, and 1 that runs horizontally across the wrist - I've included a picture that shows the layout I used for the risers, as well as the loaction of the strap holes.
Trace out the lines onto the rough side of the leather using a pencil or pen, and then prepare for wet molding:
- Wet your sponge, and evenly dampen the leather on both flesh and grain sides
- Cradle the leather in your hand - splay your fingers so that there is one on either side of the area you are raising
- Use the large end of the wooden edge slicker to stretch the leather - on the ends and around the sides, use the narrow end to help define the raised areas
- Turn the leather over periodically and check to see which spots need more work
- As the leather dries and shrinks slightly, you may have to rework some areas to maintain the definition
- You can also use the edge slicker on the grain side of the leather to flatten the non-raised areas - this also burnishes the leather and gives it a bit of a shine
- Let the leather dry thoroughly, and then proceed to the next step
Now that we have the wet molding complete, I'm quickly going to punch the holes in the bracer where the straps are going to attach.
- With a 3/4 oblong punch, cut out the holes for the straps - notice that I'm punching from the rough side, so I've put some note paper over the poly board to protect the grain side of the leather
- Using a #3 edge beveler, round off the top edges of the strap holes
NOTE: If you plan on adding trim, use a stitching groover to gouge a channel about 1 cm in from the edge of the bracer - this will be our guide to help us place lacing holes. Or you can do this as way to give your piece a tooled look without much effort.
Step 4: I'm Ready to Dye
The horrible thematic pun aside, we're now at the stage where we can start dyeing our work - I'll be using the Eco-flo Bison Brown to dye the straps and armor leather, and Eco-flo Matte Finish to seal and protect the leather.
- Follow the directions on the bottle for use (ie: shake well)
- Apply using damp sponge or paper towel - for the outer shell, I'm only dyeing the grain side because the liner will cover the flesh side
- Use a small paintbrush to get coverage on the inside of the strap holes
- After the pieces have dried, rub with paper towel to remove excess pigment
- Apply your finish to all pieces and allow to dry
NOTE: If you plan on adding the trim as detailed in the following section, follow the steps above to dye the trim pieces after they're completed, but use the Yellow Waterstain instead of the Bison Brown
Step 5: Constructing the Base
Now that we have all the pieces more or less complete, let's start work on the assembly of the main body. We'll need our cut up leather, lining, and socks, as well as our glue.
- Roll up the strips if socks into little sausages and lay them into the raised areas. Trim off any excess and fill any large gaps.
- Apply the Tanner's Bond around the edge of the bracer, as well as the strap holes.
- Overlay the lining material and glue the edges down. Wait for the glue to dry thouroughly.
- Using an x-acto knife, trim off any excess on the edges, and cut out the strap holes in the lining.
If you've opted not to use trim, skip the next section and move onto Adding the Straps.
Step 6: Optional - Adding Trim
I decided to add some trim pieces to match the bracer as seen in the movies - again I used the 3-4 ounce veg tanned leather. Instead of using one long strip to go around the whole edge of the bracer, I opted to create segmented pieces that overlap each other at the corners - I think in my next attempt I will try out using a long strip of lighter leather or fabric, and I would encourage you to give that a try as well!
IMPORTANT NOTE: you will notice from the pictures that I've switched to working on the left bracer- this will not affect any of the following steps
- Measure the sides that the trim pieces will cover
- Cut a strip of leather at least 3 centimeters wide, and about the length of wrist area
- Bevel the long edges of the strip, and slightly skive the ends with the x-acto knife
- Gouge a channel down the middle of the strip with the stitching groover - this will make it easier when we fold the leather
- Dampen the leather slightly with a wet sponge to make it more pliable, and fold the strip over the edge of the bracer, molding it into shape
- Grab your 9/64 inch (3.5mm) drive punch, and punch holes along the un-bevelled edge of the trim , again using note paper on the poly board to protect the leather
- Line up your trim to the bracer, and mark where you need to punch rivet holes. As you punch, note that the holes should not completely cross the gouged channel in the bracer.
- Cut another strip of leather the length of the 2nd longest edge + 3 inches - the extra 1.5 inches on either side will be used to create tabs that will slide underneath the cap ends of other trim pieces
- Follow steps 3-7, but make sure not to punch any holes in the tab sections. Trim the tabs so that they form wedges, and skive as thin as you can. Use the wrist piece to line up to on the bracer and test the fit as you go.
- Follow the above steps until you have all your trim pieces completed, then go back to the dyeing section and complete the steps using Yellow Waterstain.
Once the trim pieces are dyed and dried, we can get started with the lacing!
- Cut off a string of lace about as long as your two arms stretched out sideways
- Using an x-acto knife, skive off a good amount of thickness from one of the ends
- Insert the skived lace tip into a 2 pronged lacing needle - the teeth should go through the thickness of the leather and pop out the other side when the needle is securely closed
- Grab the trim piece for the wrist, place it in line with the lacing holes on the bracer, and start lacing from about the middle of the wrist - make sure the smooth side of the lace is facing out from the top of the bracer, and leave some length of lace sticking out of the first hole
- About 2 holes from the end, get the next piece of trim and get it in place, sliding the tab under the wrist piece. Then continue lacing.
- Continue adding trim pieces and lacing until you get to the last hole
- Lace through the back of the trim and the bracer lacing holes, then push the needle underneath the front of the trim piece
- Grab the opposite tail of lace and thread it through the unoccupied hole
- Secure the lace with a double knot - pull it tightly and it will tuck itself under the trim edge
- Snip off the excess lace
Step 7: Adding the Straps
To attach the Buckles:
- Slide the buckle into place on the strap
- Insert the back end of the strap through the bracer, and hold in place as in the picture
- Using a 6 prong 3/32 inch (2.3mm) diamond hole punch, create the stitching holes - I've positioned it so that the middle of the punch lines up with the seam
- Using brown waxed thread, thread the needle and sew a running stitch from the buckle to the bracer - leave some thread sticking out of the first hole so that you can hold it down with your thumb to keep the stitch tight
- In order to ensure a secure stitch, continue the running stitch back up to the buckle
- Backstitch 2-3 holes to firmly secure the thread, then snip off the excess
To attach the Straps:
- Slide the strap through the buckle and put the buckle tongue through the central hole
- Insert the back of the strap through the bracer, and tighten until it's comfortably snug
- Mark and trim off where there is any excess, but be sure to leave room for your stitches!
- Swap out the 6 prong punch for a 4 prong punch of the same size, and follow steps 3-6 of the buckles directions
Step 8: You're Done!
Grab a pint of Butterbeer and set off a few Filibuster's Fireworks! You're done! I hope you had fun during the process of the make, and that you got something new out of it (besides the bracers)!
Keep the DA strong by voting for this Instructible in the Wizarding, Tandy Leather, and Maker Oplymics contests!
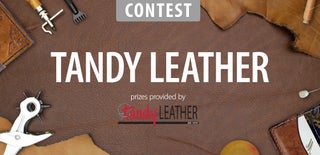
Third Prize in the
Tandy Leather Contest 2016
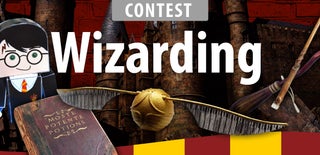
Participated in the
Wizarding Contest
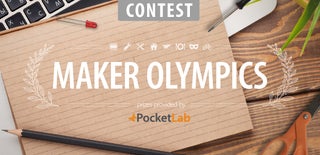
Participated in the
Maker Olympics Contest 2016