Introduction: Leather Viking Spangenhelm
You're on a longship sailing towards your first raid! This is likely the most important day of your life - you could become a famed warrior, and the skalds will sing of your triumphs! Only one problem...you've forgotten your helmet, and no self respecting warrior goes into battle without something to keep his grey matter intact. Not to worry, with a good handful of tools you can make one!
Okay, so I'm not going on a raid, but I'm planning on using it as part of my Viking Archer Halloween costume. The helmet we're going to make is based on a classic Norman design, with a total of 9 pieces of leather used to construct the helmet. I will also be doing some decorative stamping and tooling on the panels, bands, and nasal guard of the helm.
You can make this build as complex or as simple as you like depending on your wants, and this extends to the leather tooling portion as well. Feel free to scale back (or scale up) this design as much as you want! It took me the better part of a month to complete from start to finish in my spare hours, but hopefully this instructible will help streamline the process for you.
IMPORTANT: This helmet was designed as a costume piece, and therefore should not be used for SCA or historical re-enactment unless you reinforce the design in such a way that it complies with the safety rules and guidelines of the organization. I imagine that it would stand up to some LARPing, but I don't make any guarantees as to its protective capabilities - any injuries sustained due to improper use cannot be legally attributed to me in any way.
Things you'll need for:
Basic Construction
- Cardboard (for pattern making)
- Scotch Tape
- Leather - vegetable tanned leather (6 to 7 oz)
- Xacto knife, head knife, or leather shears
- Strap cutter (if possible)
- #3 Edge beveller
- Edge slicker/burnisher
- Rotary Punch or Drive Punch
- #9 1 inch Copper burr rivets and rivet setter: 53 in total (you could also use rapid rivets, domed rivets or chicago screws)
- Side cutters or wire cutters
- Domed rivet setter (optional)
- Hammer (a regular household claw hammer will do)
- A circular form that roughly fits around your head (I used a metal salad bowl - see Step 2)
Tooling and Carving
- Sponge and plastic or glass container of water
- Celtic basketweave stamp (or any other pattern/border stamp you have at your disposal)
- Celtic knot stamp set
- Stitching groover
- Poly mallet
- Modeling Spoon/Ball Modeling tool
Dyeing and Finishing
- Dyes of your choice (I used Bison Brown EcoFlow, Wheat EcoFlow Oil Dye, and Saddle Tan Hi-Lite Color Stain)
- EcoFlow Clear Matte leather finish
- Latex/rubber gloves (so that when you're dyeing your hands remain their natural color)
Wool daubers and paper towel
Step 1: Making Your Pattern
Right off the bat we'll need patterns for the nasal guard and one of the panels that will end up forming the bowl of the helmet. You can design your own, or employ the help of the almighty Google to find a suitable pattern - most patterns that you'll find are for metal helmets, but those patterns will work just as well with leather. For this build, I used the Norman Spangenhlem pattern by Halberds on armourarchive.org as reference for the creation of my own.
After drawing the patterns on paper, cut them out and fold them in half to check that your pattern is symmetrical. Trim off any of the extra bits that are sticking out, and voila! Two new patterns ready for making a cardboard template! Mark one side as 'Front', and the reverse side as 'Back' on each pattern - this will help later when constructing the cardboard and leather versions.
Trace the nasal guard pattern and panel onto a good sturdy piece of cardboard. For the panels, you can trace it 3 more times so that when cut out you have a total of four panels. Now cut all the pieces out and mark them front and back like their paper counterparts, we'll be using these in the next step.
As for the bands that will hold the helmet together, we can get started making these as well. There are three: one for the headband, one that runs front to back, and one from side to side. I had to go through a bit of a trial and error process with these, and it's worth noting that the measurements I'll be using fit my particular melon - you'll have to adjust them to fit you. To make the head band, you'll have to do a measurement of your cranium where you want the helmet to sit. In my case, I measured 24.5 inches long from the brow ridge of my forehead to back of the skull. I added a half inch to fit the rest of the parts on the inside. So the measurements of the bands came out to:
- Headband - 25 inches long by 1.75 inches wide
- F2B (front to back) - 17.5 inches long by 2 inches wide
- S2S (side to side) - 17 inches long by 2 inches wide
Label the bands so you don't mix up which is which, and like the others indicate the front and back sides. To help us out in the next step, I also to marked the length and width center lines on the nasal guard, F2B, and S2S pieces. I also drew lines 1/4 inch from the edge to indicate roughly where the rivets would go to make sure that they'll be level.
Step 2: Cardboard Is Cheaper Than Leather
In this step we'll create a cardboard version of the helmet using the patterns created previously. This step can be as much work as creating the final leather helmet, but don't get discouraged! The more time spent in this step will result in a helmet that fits better and is excellently aligned to the other pieces - realizing you have a crooked nasal guard is a real bummer after you've cut out your leather and punched all the rivet holes. It will save you money (leather is not a cheap material) and your walls from projectiles thrown in frustration.
Apologies for the massive number of pictures, but I feel that they will help you construct your own much easier. I've assembled them in chronological order, and written the instructions so that you can easily match the instructions to the image. When building the cardboard helmet, we're going to build it with the Back sides facing out - I'll explain why a little later.
Take one of the cardboard panels made in the last step and lay it over your knee like an unruly child (with the Back side facing up), then starting from the edges and working your way to the center, 'knead' the cardboard into a rough domed shape using your kneecap as a form. The cardboard will start out stiff, but as you bend it at various angles the fibres loosen up and it becomes more malleable. Do the same with the brow part of the nasal guard, and then bend the cardboard of the guard in half to form the distinctive angle. Dome the rest of the panels like the first and set them aside. For the bands, just roll the cardboard down the length so that it has inherent curvature.
Grab your circular form (a metal salad bowl) and wrap the headband around it with the Back side facing out, and tape the two ends of the headband together securely - the seam will be the back of the helmet. Next, grab the nasal guard and (with the Back side also facing out) line it up to the center line on the headband and then tape it down onto the headband. Next, tape the F2B band and the S2S band together (both with Back side facing out) so that the guidelines you drew are even. It's worth noting that I drew a quick graphic on the F2B band that lines up to the front of the helmet, and labelled the S2S piece with L and R to make sure that once disassembled in will be easy to reassemble. Tape the ends of the bands into their proper places using the guidelines - if you look at it from a top down view and each of the holes where the panels will go are more or less even, then you're good!
Now you can start planning where your rivet holes will be - use the guidelines and a ruler/measuring tape to help you figure out where things need to go and then draw a circle for your reference.
The reason that we're building it with the Back side out is because of the next step - punching the rivet holes. If we were to build it with the front side out and punch our rivet holes, when we thread the rivet through it won't sit straight and flush with the material - it always ends up on an angle, which isn't great when you're trying to set rivets. I'm not %100 why this happens, but I think it has to do with either the angle of the hole that the punch makes on a curved surface, or the way the material pulls on the rivet. I'll have to do some more research on it, but suffice to say that for best results we need to build it backwards - this will also have to be done for the leather version as well when it comes to punching the rivet holes.
Now grab your rotary punch or drive punch tool and get to punching holes! I focused on punching the rivet holes on the bands and nasal guard first, and then moved on to the panels. Punch three holes at each corner an equal distance from the edge from each panel, then place the panels inside the helmet and thread rivets through to hold them in place. Use a pencil or pen to mark through the holes in the bands to find the locations for the rest of the rivet holes, and then punch those out.
Now for the moment of truth - cut through the tape to separate the pieces, and thread your rivets through the holes so that the posts stick outside of the helmet. If everything went well, the bottoms of your rivets will sit flush with the cardboard! Stick the helmet on your head and take a selfie! But chances are there are a couple holes that aren't completely working that you'll need to adjust. You can probably tell from the pictures, but I made two or three versions of the cardboard helm until I was satisfied.
If you're happy with the result, great! And as an added bonus, you could just clean up and paint the cardboard, set the rivets and call it a job well done! You read that right! Two helmets for the price of one! But chances are if you've been bitten by the leather bug, you'll not be satisfied with just cardboard - you'll have to make it out of leather! If this applies to you, keep going!
NOTE: As a last minute addition, I made a rectangle piece of cardboard to cover the seam at the back of the headband - this will make the ninth piece of leather.
Step 3: Leather Time! Cutting Your Leather and Temp Assembly
This is when the big smile spreads over your face as you finally get to pull out the leather! When working with the leather, remember that there are two sides - the flesh side (the rough side), and the grain side (the smooth, skin side where any tooling you choose to do will go).
Using your paper patterns with the Back side facing up (you could use the cardboard templates as well if you made radical changes to the design during the previous step) trace the shape onto the flesh side of the leather. Like the paper and cardboard counterparts, label the flesh side of each piece as Back and the name of the particular piece. For the sake of clarity I'll refer to the panels as P1, P2, P3, and P4 - look at image #5 to see where each one is placed on the helmet.
Grab your cutting utensil of choice, and get cutting! I used a round knife to cut out all the pieces including the bands. I had intended to use a strap cutter to get perfectly straight cuts on the bands, but I seemed to be doing well with the round knife so I just kept on cutting.
Once all the pieces are cut out, you can round off the edges of the leather using an edge beveller - I personally only bevelled the grain side of the nasal guard, but you can bevel however you would like.
This is where the bonus of spending all the time on the cardboard helmet comes through, as you can use the cardboard template to match the rivet holes. Place your leather with the flesh side up, and then overlay the cardboard pattern with the Back facing up. I also placed a small scrap of cardboard beneath the leather as well to avoid the anvil of the rotary punch marring the grain side. As you punch out the holes, thread a few rivets through at the corners and edges to ensure that the holes in the leather line up exactly with the cardboard and that the alignment won't shift over time.
When all the holes are punched do a quick temp assembly to check that everything is working - assemble the helmet with the grain side facing out by threading the rivets through each piece. Pop the helmet on your head to check the fit and find the nearest mirror to ogle at the awesomeness.
Step 4: Tooling, Celtic Stamping, Brow Repousse
Nothing screams Viking like a good stream of Celtic knots! In this step I'm going to do some basketweave stamping on two of the panels, as well as some border stamping on the bands and nasal guard using a Celtic knot stamp set. If you are new to tooling and stamping, be sure to watch the Tandy Leather videos on their YouTube channel and practice on some scrap leather before moving to the final piece.
First I'll do the basketweave stamping on panels P2 and P4 using the angled basketweave method so that it will form a diagonal cross-section with the plain panels for contrast. Below is a basic description for the basketweave - I would definitely recommend watching the basketweave demo done by George Hurst for a visual aid.
Grab your container of water and sponge, and then moisten the leather thoroughly. Once the leather has returned close to its natural color (but is still cool and damp to the touch) scribe a line on the grain side using a scratch awl or modeling tool. Then line up the basketweave stamp so that the top left and bottom right corners of the stamp touch the scribed line and tap firmly several times, leaning the stamp to one side and the other to make sure that a clear impression is made on the leather. Move down the line and make another impression that lines up to the end of the first - you should be able to feel the raised areas of the stamp fit inside the impression. Continue stamping following the impressions until you've covered the area that will be visible once assembled. You may have to periodically wet the leather as it dries over time - dry leather doesn't accept the stamp as well, and can actually create cracks in the skin.
Next, grab your border stamp of choice, the nasal guard, headband, and the seam cover. Treat the leather with water like previously, and stamp in a straight line between the rivet holes (or wherever you want the border to run) making sure to connect the impressions. I had intended to do the same with the other two bands, but for the sake of ease I chose instead to use a stitching groover. Adjust the guide on the tool so that it will gouge out a channel between the rivet holes on the F2B and S2S bands for a quick and easy way to add decorative tooling without much effort.
Another thing you can do to add polish to your work is to burnish the edges. To do this, simply get the edge of the leather wet, and then rub the edges vigorously with the edge slicker, or a piece of paper towel. This compresses the fibres, and also buffs the edge so that it darkens a bit and gives off a little shine - I've included a picture comparing two pieces of leather, one which has a burnished edge and the other that does not. Ideally you'd do this step before tooling, but I did it after and it didn't seem to cause any problems.
As the final step, we're going to fold the nose guard and add a little repousse to the brow area. Repousse is the technique of pushing the leather from behind to create a raised design - in this case, I'm just going to be doing simple eyebrows.
First, I'm going to use the stitching groover again to gouge a line right down the middle the nose area - this will be the guide for our fold, and will create a more distinct angle. Get the leather wet again, this time on both the grain and flesh side - the wetter the leather the more pliable it will be, but don't soak it. Using a sharp 90 degree corner (in this case, my wooden toolbox) place the nasal guard so that the gouge line is exactly on the edge, and then press the edges down along the length. Smooth out any bubbles or wrinkles, and try and create as crisp a fold as possible. As the leather dries, it will maintain the shape you've made.
To do the repousse, re-wet the leather if you need to, and then place the brow piece in your hand like in the picture - this will act as sort of a cushion, or a pitch pot if you've done metal chasing before. Then using a ball modeling tool, push the leather down and draw the outline of an eyebrow. You should feel the leather stretching a little, and it's always a good idea to turn it over every once in a while to see how it looks. Once you're happy with what you're seeing, fill in the middle and push it as far forward as you like. Repeat this for the other side.
Now you're done! But all this work will not go truly appreciated until it's given a little color...
Step 5: Prepare to Dye
Grab your favourite dyes, put on your gloves, and let's get cracking! I wasn't sure which colors I wanted, so I tested them out on a piece of scrap leather. In the picture (from left to right) are Canyon Tan, Wheat oil dye, Saddle Tan Hi-Lite color stain, and Bison Brown. I decided to use the Wheat oil dye for the basketweave panels, Bison Brown for the plain panels, and Saddle Tan for the bands and nasal guard. Feel free to use the same, or create your own color combinations.
I started with the Bison Brown on panels P1 and P3. Make sure to follow the directions on the dye - EcoFlow products usually need to be shaken before use. Fold up a sheet of paper towel into a pad, get some dye on it, and apply to the grain side of the leather in a circular motion. Once the piece is covered use a clean piece of paper towel to remove the excess dye and pigment that is still on the surface, again rubbing in a circular motion, then set aside.
For panels P2 and P4, I used a wool dauber to apply the Wheat oil dye. Load up the dauber with dye, and then apply in straight lines, making sure to get the dye in all the crevices of your basketweave stamping. As before, get a clean sheet of paper towel and remove the excess dye. Follow the same procedure with the nasal guard and bands using the Saddle Tan, and then leave all the pieces to dry for a good while.
After the pieces have dried thoroughly, you can apply your favourite finish. I'm partial to the EcoFlow Clear Matte finish because it doesn't leave a plasticy sheen when it's dried, but you could always use Super Sheen in a pinch.
Apply in much the same way as the EcoFlow dye - give it a good shake, then pour onto a paper towel and rub it all over, including the back side, and leave to dry overnight. Get a good sleep, because tomorrow is the final assembly (insert appropriately themed music here).
Step 6: Final Assembly
Get your rivets, hammer, and wire cutters. It's assembly time! I'll do a quick demo on some scrap leather to show how to properly set the rivets. Wear safety glasses and dust mask when you're doing the filing - copper shavings in your eyes and copper dust in your lungs is not pleasant, I would imagine.
- Thread the rivet through the pieces of leather and set on a sturdy surface - you should always have something metal to set the rivets on, like an anvil (a jeweller's anvil could work). I actually have access to a metal circular saw table, so that's what I used.
- Place the washer on top of the post.
- Place the rivet setter over the washer so that the hollow shaft is directly over the end of the post.
- Hammer the washer down so that it sits flush with the leather. Be sure to keep the rivet straight as you hammer, otherwise you'll bend the post out of shape (see picture).
- Using the wire cutters, snip the excess post off, but make sure you leave enough sticking out so that you can peen over.
- Place the domed part of the rivet setter over the remaining section of post, and hammer down so that it mushrooms slightly over the washer. This is how the rivet will remain set in place.
- (Optional) If you have a domed rivet setter, you can flip the leather over and slightly dome the outside of the rivet like you see in the pictures.
And that's all there is to it! After you do the first couple, it's all repetition after that.
Before I started hammering away I did another quick temp assembly, partly to see that everything was still fine and no last minute adjustments were needed, and partly because I wanted a sneak peek at the (mostly) final product.
When you look at the pictures you can tell that I've set the rivets with the posts on the inside of the helmet - you could have the posts stick out on the grain side, but I personally like the cleaner look of the bottom of the rivet on the outside of the helmet. If you choose to do the same, I definitely would start setting rivets at the top of the helmet and working your way down. As the helmet closes up, it will become more difficult to fit the hammer and rivet setter inside.
Once you reach the point where you begin to attach the headband, I would also recommend that you start setting the back of the helmet first. I didn't, I assembled from front to back, and I ran into the problem of having the nasal guard in the way as I tried to set the last few rivets. Otherwise follow the pictures, as I snapped them chronologically.
Finally, grab a file or some sandpaper and smooth off any rough edges on the peened rivets - these will be sitting right next to your scalp and forehead (unless you choose to add a liner), so a little precaution goes a long way.
And now you are finally done!
Step 7: Go Raiding!
Don your newly created helmet, raise your sword into the air and sound the battle cry! It doesn't matter if you're battling Danes, dragons, or dandelions, you'll be ready!
I hope you enjoyed the creation process and the final product. Be sure to share your creations, I'd love to see them! If you really really enjoyed it, please consider voting for this instructable project in the leather contest! Happy making and even happier raiding!
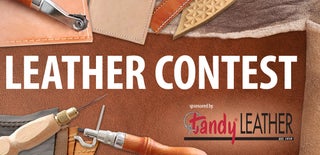
Participated in the
Leather Contest
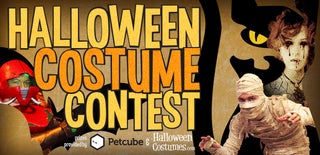
Participated in the
Halloween Costume Contest 2015