Introduction: DIY Small LARP Shield in Under an Hour!
Getting started with LARP kit can be an expensive and absolutely daunting process. Your character ideas change, kit is super expensive and, if you have no previous crafting experience, the idea of making your own gear can be absolutely daunting. This tutorial aims to provide the absolute beginner with a basic 'biscuit' shield that can be assembled in under an hour, and on a budget. It provides a blank canvas that can be filled with almost any character design, and also gives you a starting point to springboard into other shield shapes by using the same basic technique.
This shield design passes the basic safety requirements for all the LARPs I have access to, however it's important that you check with your own group's guidelines to make sure this fits with their safety requirements, and what size category it falls into. Modifications to ensure safety can be made to this design with minimal fuss. This particular shield is also ridiculously light, making it a practical option for younger players, highly active fighters, and players without the ability to maneuver heavier shields.
Most of all, it gives you a fantastic starting point for diving into the world of making your own gear, whether you're a complete newbie, or a seasoned fighter, and a chance to truly personalise something to your own kit. Happy making!
Note: This is an image-heavy tutorial. Please take the time to look at all the pics carefully as they'll help you along your way. As ever, please feel free to leave a comment with any questions or suggestions you might have!
Step 1: You Will Need...
- 45cm x 55cm sheet of 9mm plywood. You can use thicker, up to marine ply, but since the group I'm a part of doesn't allow any kind of shield-bashing, 9mm does just fine for a light-weight, sturdy shield. Do not use MDF. This size makes it the largest 'small' shield you can make within our group's rules.
- 13x13mm K-flex pipe insulation. (http://www.kflex.com.au/kflex-australia/) This is the brand we use, however any similar pipe insulator will work. The important parts are the thickness of the foam walls, and the diameter of the center hole. We used 2 single-metre lengths for this project.
- Garden hose. You'll use 2m for this project. Make sure you buy it new as old hose is too brittle to use.
- EVA foam matting.
- Calico fabric. We bought a piece that was 1m long, by the width of the roll, which was about 1.2m. We specifically bought calico for this project because it'll give me a great base to paint on once it's sealed, and it's a pretty neutral color. You can realistically use almost any cotton fabric for this project, so long as it'll stand up to the rigours of fighting, and so long as it doesn't stretch. This is incredibly important. If you want something with colour, I suggest looking into broadcloth, drill cotton and cotton duck. I love the idea of someone out there running around with a Disney-princess-themed shield. If your fabric is too thin, you can follow the same instructions, but just double your fabric over when you go to wrap the shield.
- Gaffer tape.
- Cotton webbing, the same stuff that they use on canvas bags and some totes. You should be able to find this at any haberdashery or fabric store. The width is entirely up to personal comfort, but a 2m length should see you through the project.
- A craft/Stanley knife
- A staple gun and staples. Your staples need to be thinner than your plywood. You to NOT want them protruding through the other side. 8mm staples work well, we found.
- Scissors
- Contact cement. Not pictured because that stuff is super stinky.
Everything we needed, we were able to purchase by going to both a fabric store, and the hardware.
Step 2: Step 1 - Edging Your Base
For the purpose of this tutorial, our base is a piece of 7mm thick plywood, 45 x 55 cm long.
If you want to be fancy and make a shield with a different shape, avoid anything that has an angle less than 70', otherwise maintaining a safe, padded point becomes very difficult. Kite and round shields work well for this technique, as do some other more adventurous designs that we've tried. I'll add pics at the end of the tutorial.
We cut this out quickly with a band saw, but a jigsaw, scroll saw or even a hand saw will work, so long as your edges are clean. If you've got a few gnarly bits, hit it with some 250grit sandpaper to take any splinters off.
Once your edges are safe to handle, you'll want to cut your hose to the length of your four sides. You want your hose to overlap at the corners, so just use the exact measurements of your shield.
When you've cut them to length, take your craft knife and carefully cut along the length of the hose. The straighter the cut, the easier it will be to use, but don't fret too much if you go off-kilter slightly. The idea is to create a cut so that both sizes of the hose can be parted.
Take your hose and, using the slit you just cut, fit it over the edge of your shield base as pictured. If your hose has been curled tightly, it might take a bit of coercion to get it to sit flat. Gratuitous use of gaffer tape can be employed at this point if it makes your life easier.
Fit your hose lengths over all sides of the shield blank, ensuring the corners overlap as pictured. You may want to tape your corners down for added safety, however we've personally never encountered an issue with ours being left simply fitted over.
Step 3: Step 2 - Foam Edging
If you haven't already used your gaffer tape, now is the time to break out that silver roll of goodness. You'll need it.
Your first step is to cut along the length of your K-flex, the same way we did to the hose. A pair of scissors is much better for this than a craft knife, but for the love of god, don't use the fabric scissors. I will hunt you down.
Once you have those bad boys sliced up, fit them over the hose. You're going to want to tape as you go, as this stuff is even less willing to stay where it's put. Pay careful attention to the corners, putting tape either side to secure it. You will end up with a small pucker at the edges. If you're a pedant like me, you can opt for cutting a small wedge (2cm or so) in the edge of the foam, but be frugal with your slicing. The corner padding is arguably the most important on a shield, so you really need to make sure you're not leaving anything exposed.
Ideally, you'll match your corners up with the K-flex. If you have the luxury of doing this, overlap them like you did to the hose, but make sure you add a piece of tape lengthways so that it won't pull apart. If your K-flex needs to join on a straight or a curve, simply gaffer tape them down at the ends, and then add a bridging piece of tape to secure the two ends together. Just make sure there's no gaps between them. You can bunch some of the K-flex up if you need to, as it's quite malleable and it's better to have a little too much, rather than not enough.
Step 4: Step 3 - Sizing Your Fabric
As I mentioned earlier, we brought a metre of calico off the roll, and with this particular project, we have plenty to spare. Your biggest concern is ultimately making sure that you have at LEAST a handspan of fabric to fold over on all sizes of your shield. Depending on the size of your shield, this may be best done on the floor, but we were able to fit our project on the table.
Lay your fabric out. If you need to fold it over, now is the time. Lay your shield on top of your fabric.
Grab the edge of your fabric and fold it over the shield, ensuring that you cover the edging entirely. You want it covered by a few centimetres at minimum. I generally go by rule of a thumbspan from the far edge of the foam, but that may change depending on the thickness of your edge. Mark where your shield sits on the fabric WITH the fold over.
Go around and do this for all sides. If you're working with complex curves, err on the side of caution and go with more fabric than you immediately need. You'll be trimming it back later after we've secured it, and with the way fabric pulls, it's imperative that you have enough.
You must not leave any part of your foam exposed! This is super important for a few reasons.
- The longevity of your shield depends on it. Fabric can be dragged along the ground. Foam can not.
- It's a big-ass safety issue. Exposed foam will tear. Torn foam exposes hard surfaces. That's bad.
- The fabric over your foam is what gives it the springy, rather than spongy quality, and ultimately holds it in place.
Cut that fabric up to size, and get out your staple gun for the next step.
Step 5: Step 4 - Ca-chunk!
This is where things get fun.
Placing your shield on the fabric so all sides can be covered, pick a starting point and begin stapling your fabric down. I always try to start with one of the largest surfaces, because it ensures that the fabric is stable while I'm doing the rest of the shield.
When you're stapling, you simply want to fold the fabric over, nose the staple gun up against the foam, and plant your staple. I space my staples 4-5cm apart, and generally work from the corners, into the centre of the fabric, but go by feel for what works for you. Don't worry about making sure your fabric is tight for this first side. You want that staple as close to the foam as possible because it will secure your fabric better and, in the event that one of your staples pushes through the board for whatever reason, it will be on a part of the shield that is highly unlikely to have contact. Still, it's worth lifting your shield up to check that you're not having them protrude.
You may have a misfire where one of your staples isn't sitting right. Depending on the situation, either pull it out and put a new one in, or make judicious use of percussive maintenance (see: hit it with a hammer).
When you've completed that first side, you're then going to go to the opposite side of your shield, and start there. At this point, you're going to want to gently tug on the fabric so that it's lying flat against the table/surface you're working on, rather than wrinkled or gathered underneath. Working out the tension of your fabric can be a little tricksy, so I've included a photo of how I pick it.
What you're looking for is, when pulled across the foam, the fabric making a taut bridge between the foam and the wood. Not so taught that you can't push your finger into it, but definitely not floppy. It should have gentle give to it, as we're going to use the other side of the shield to add proper tension If you over-tighten it now, you're going to have a very uncomfortable shield later. Don't let go, simply push your staple gun into the fabric, butt it against the foam, and fire.
If you've ever stretched a canvas before, this is a very, very gentle version of that. What you'll notice is that, in the areas between your staples, you will have fabric pulling. You may want to add more staples accordingly.
Step 6: Step 5 - Tucking Your Corners
So we're now up to the point where corners get involved. For the most part, you're going to follow the same instructions - pick a side, gently fold it over, go to the opposite and add a little tension - but you're eventually going to have to face these pointy bastards.
Your first step is to make sure the foam insulation is tucked in. Pull your fabric over it like you would with the straight sides, but you may need to give the foam a poke inside gently to get it to sit right. Ultimately, it doesn't need to (and very likely won't) sit flat, but it's also not a big deal.
What I like to do is to bring the staples right up on both sides to the very corner, and then fold my fabric over, almost like I'm wrapping a Christmas present. So, pull it across three-quarters of the way, fold it under, and then tuck it down. Lock it in place with one or two good staples. Rinse and repeat for all your corners.
If you're working with a more complex design, I follow my curves until I hit the corners, and save them for last. Get all your near-straight edges done first, and then focus on folding your fabric neatly, and stapling it into the corner.
So at this point, you should have a pretty well stapled shield back, with lots of fabric to spare, especially around your corners. You have two options:
- Get the scissors (yes, the fabric ones are okay this time) and trim the excess down so that there's roughly a 2cm lip of fabric around the edge. At this point, you can either leave it as it is, and your fabric shouldn't really fray, or you can go an extra step for finishing and use any extra webbing you bought to staple over the raw edges. It'll purely be a cosmetic difference, but that might be your jam.
- If you're a bit of a masochist, you can fold that fabric under itself a few times, and then staple it down to get a really clean finished look, but the corners will be a nightmare.
Congrats! The back of your shield is almost finished.
Step 7: Step 6 - Finishing the Front
Flip that bad boy over. Right now we have something that resembles an awkward pillow, but we're not done with the stapler yet. This is where things get really neat, because we're going to use the flex in the fabric on the front of our shield to really tuck it all in and make sure our padding is soft, but springy.
Start with a corner and work your way across one side of the shield, like we did on the back. What you might find is that you actually need to use more staples on the front than you do on the back, just to get nice and unpuckered fabric edges. Go with what looks good. Your main goal at this point is to simply get a flush surface for painting on, and to hold that foam in place. When you're done with that first side, give your foam edging a squeeze and see how the feeling has changed from really soft and spongy, to quite bouncy under the fabric. That's what we're aiming for here.
Go to the opposing side, do the same thing, starting at the corners and working your way across. You'll notice at this point that the fabric across the middle of the shield should be laying flush against the shield base.
Finish the last two sides of your shield.
Yus! That's the front of this completed and ready to paint!
Step 8: Step 7 - Getting a Grip
So, you have a tight, good-looking shield. That's awesome. But how are you going to wear it?
So at this point, you have a few options:
- You can follow the process we're using to use webbing to create two shield straps
- You can use your own technique to leather-strap your shield, though I don't recommend this for newbies. You'll really need to know your body dynamics and what's most comfortable for you, otherwise you may end up positioning the shield in a way that can cause pain with long-term use.
- You can opt for a 'centre grip' shield and use a prefab handle. I've included a pic of one we made earlier (with a calico pocket for a very thick sword as well) that uses a sponge handle as the grip. I've also seen sanding tools, trowel handles and drawer handles used for this, but the biggest thing you're going to need to be aware of is that you only have a limited depth of wood to affix it to. You can NOT have any screw, nail or other fixing protruding through the board. It's a huge safety issue. Resin adhesives like Araldite work well if you have a large enough surface to adhere to, and in our version, we used a combination of shallow screws and Araldite for a very strong bond.
So, if you're going with the webbing option, read on.
You're going to want to lay your shield down on a flat surface and position your arm across it at whatever angle is most comfortable for you. Make a fist.
Trace the shape of your arm directly onto the wood.
In this instance, this will be a vertical rectangle shield, but you can realistically strap it in any direction and, so long as you have enough room, it'll work.
Step 9: Step 8 - Padding
For the sake of this tutorial, we've used some leftover EVA foam we had lying around from other projects. It's just the standard floor mat stuff you can get at any hardware.
What you're going to do is grab that matting, and lay it over the shape of your arm. You want it to cover more than the area traced.
Cut it to size and glue that stuff down. Foam tends to absorb contact cement really well, so you may need to apply more than one coat. Don't forget to apply it to the shield as well. Always work in a well-ventilated area.
If you're using scrappy bits of foam like us, your biggest sticking point (no pun intended) is to ensure that there are no gaps between the pieces.
Once it's stuck down, you can choose to go over it with something like a rolling pin if you want a really secure adhesion, but just sticking it down as you would normally is fine.
Step 10: Step 9 - Strapping
So we've got our padding down.
Lay your arm across the shield as you did to mark it before. This time, grab your webbing and drape it over your hand, measure and cut. The goal here is to have enough webbing to staple to the shield both above and below your hands, all whilst the webbing is loose enough to comfortably slide your hand in and out, and also for you to grip.
Do the same with the strap over your forearm. You should be able to easily slide it in and out, but not so free that your shield will flop around when you use it.
When stapling, I like to tuck the ends of my webbing underneath, just to give it a tidy look. I staple both sides of the strapping. As you'll see, on the arm strap, I like to reinforce the staples by adding a second row on the forearm straps. That's where most of the weight will be supported - your hand strap is mostly there for maneuvering.
Once you're done, give it a test fit. It'll be easier to make the straps tighter by adding a few more staples.
If you're not super confident the staples will hold, adding some extra glue under the straps will help.
Step 11: Step 10 - You're Done!
You animal! Providing nothing has gone horribly wrong, you've completely finished your shield by now.
The one we made weighed in at just under 1.5kgs, so it's SUPER light for a LARP shield as sturdy as it is. if you've used thicker ply, different foam, more fabric, etc. this will have changed, but it's worth experimenting with materials to make equipment that's perfect for you.
Now you get to enjoy the thrill of painting it, scuffing it up, staining it with the blood of your enemies, etc.
If you're intending on painting, I highly suggest giving it a good coat of primer beforehand, just so you have more time to work with the paint, and the fabric is sealed, however if you just intend on using it as is, no sealer or primer is necessary.
You can also glue foam to the fabric if you want to create raised designs and crazy awesome effects, but that's a tutorial for another day.
I've included pics of two finished shields using the same process. Complex curves and points will add difficulty to the edging and fabric process, but once you've got the hang of it, it's possible to achieve some really wicked looks using the same basic technique.
As always, inspect your gear before and after each game for any signs of damage, wear or needed repair, and always make sure that your equipment is approved by your marshal before bringing it out on the field.
I would absolutely LOVE to see some of the shields you all come up with!
Happy hunting!
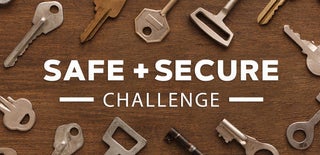
Participated in the
Safe and Secure Challenge