Introduction: DIY Super Bright LED Skate Lights
You might remember my first set of lights that I put on my dad's skates. Well those weren't bright enough and they were a lot of work because I didn't know how to make PCBs. In this i'ble I'll cover how to make your own custom PCBs in under an hour! Keep in mind, if you've never made a PCB before it isn't hard at all! This would be a good beginner project to get started with making PCBs. All it takes is a trip to an office supply store and to a radioshack! See, I never got around to making PCBs because I didn't want to have to go to the store and buy etchant and stuff, you know what I mean. Eventually I just made myself do it and it was the best electronic skill I learned for a while! So quite being lazy and go get some PCB material!
Below is the link to my first RGB skate-shoe lights, which doesn't require making a PCB.
https://www.instructables.com/id/RGB-LED-Skate-Ligh...
I hope you enjoy this i'ble and please cast it a vote!
Step 1: Ingredients:
Electronics:
- Arduino
- ATtiny2313 or similar IC
- 20 DIP IC socket
- Breadboard
- Jumper Wires
- 4x AAA battery holder
- 4x 2N222A NPN transistors
- 4x 1kΩ resistors
- 4x 100-150Ω resistors
- 5x red LEDs
- 5x green LEDs
- 5x blue LEDs
- 5x yellow (or white) LEDs
- Heat Shrink
- Non-conductive material, such as cork board.
Materials for Etching:
- Copper Clad
- Etchent
- Iron
- Laser Printer
- Photo Paper (the same shiny paper you would get your pictures on from a pharmacy)
- Paper towels
- Surgical Gloves
- Rag
- Plastic Tray
- Steel wool soap cleaning pad
Tools:
- Dremel or Drill (Dremels work better because they are much lighter and have way higher RPMs)
- 1/32 bit for Dremel or drill
- Soldering Gun
- Double-sided Tape
- Electrical Tape
Step 2: Files
First you will need to download these images and this Arduino sketch, unless you would like to make your own sketch.
Even though I already know that this circuit works, it's always a good idea to breadboard it first. That way you can learn to prototype your circuits! The next step includes the circuit, so you can prototype like 1 row and see how it works or something like that!
Step 3: Schematic
Terms: I/O = Input/Output
Here is the schematic. Now I wanted to run 5 LEDs off of 1 pin, but I couldn't just hook them all up to the same pin on the ATtiny2313! If you look in the datasheet is says, "40mA per I/O pin". Lets do a little math! 5 Leds @ 24mA a piece is 5 x 24mA = 120mA. This means when all 5 LEDs are on, they are using 120mA, which is 80mA over the absolute maximum working load of the I/O pin. So to fix this I use a 2n2222A NPN transistor as a switch. When a small current is applied to the base of the NPN transistor it connects the all the LEDs to ground, thus completing the circuit. The transistor barely uses any current, so this considerably lightens the load on each I/O pin.
Step 4: Making Your Own Easy PCB! Part 1: Printing
This will be a slighty condensed version of making PCBs. I will make an I'ble very soon with a full video and instructions soon. You will be able to find it here https://www.instructables.com/member/Enjoying+Electronics/.
Some other good i'bles on this topic are
https://www.instructables.com/id/Mostly-easy-PCB-ma...
https://www.instructables.com/id/Sponge-Ferric-Chlo...
https://www.instructables.com/id/Turn-your-EAGLE-sc...
Print off the the circuit that I attached to this i'ble. Do not resize it or anything. Don't reverse it. Load photo paper into your printer's bypass tray (if you have one). Usually in the bypass tray they have two little tabs for you to adjust the paper constraints. Since photo paper is small, you will need to push the constrains most of the way in. You will now need to find out which side of the paper your laser printer prints on. Usually you will face the side you want printed on downwards, so print it off circuit onto the shiny side of photo paper and trim the edges on the lines I provided.
On a blank sheet of paper, print off the silkscreen, and trim it on the guide lines. This will show you which electronic components go where. It's quite important!
Step 5: Making Your Own Easy PCB! Part 2: Preparing the Copper Clad
Using the schematic as a template, cut to size a piece of copper clad. Then using a very fine grit or
steel wool with a dab of soap clean off the copper to roughen it up just a bit and to get rid of any grease or dirt.
Step 6: Making Your Own Easy PCB! Part 3: Ironing
Place the cleaned copper on a flat surface, such as a desk, then put schematic face down on top of the copper. Remember, the shiny side should have the circuit on it, and that gets pressed against the copper. Lay a piece of paper towel over the paper and the copper. This will keep your iron clean.
Set the iron to it's highest setting, and set it on top of the paper
towel that is covering the photo paper. Press down on the iron for about 1.5 minutes, without moving the iron. Do not slide the paper around or you will not get a clean ink transfer. After 1.5 minutes, pick up the iron gently and rotate the iron a little bit then press down evenly for another 1.5 minutes. Make sure that you get the corners ironed well. Now that you are done ironing, the paper will be sticking to the copper. Be careful; the copper is hot.
Don't worry, you won't set the paper towel on fire, it's actually kind of difficult to do that!
Step 7: Making Your Own Easy PCB! Part 4: Cleaning
Carefully transport the copper clad with the paper stuck on top of it into a pot of warm water. This will soften the
paper and make removing it easier. Don't stick the hot copper plating into cold water because it will begin to warp. Gently begin peeling off the paper. Start from the corners and peel slowly. You should be able to peel off the top layer leaving a very thin layer hugging the copper. I found that rubbing my thumb in circular patterns works best. If a couple bits of the ink come off that's OK, we can fix it with a sharpie.
Wash the board.
Next inspect your board. You need to make sure that you get all the paper off. If you look very carefully between thin traces and pads that are in close proximity of each other you might notice tiny bits of paper residue between them. That has to go, or else the copper under it won't etch very well, leaving the two traces connected. This could result in a short circuit, ruining your parts, so make sure to get up all that paper! Fix any broken traces with a sharpie. Get the finest-tipped sharpie you have. Draw in the missing lines and let the ink dry. Repeat until the traces are completely black.
Step 8: Making Your Own Easy PCB! Part 5: Etching!
Time to etch! First go outside to a well-ventilated area and put on your surgical gloves. Pour enough etchent to fill a small plastic container and cover the PCB. You don't need a lot of etchent, just enough to cover the board. Place the board circuit-side down in the liquid. Now all you have to do is simply leave the board in for about 30-40 minutes and no longer, but you should probably check the board every 5 to 10 minutes and agitate the liquid. You should begin to see the copper begin to dissolve but the copper under the ink stays in place! After ALL the copper between traces and pads have been dissolved, using your gloves, remove the new PCB. Wash off the PCB and inspect. You shouldn't have any copper traces still connected. If there is you should have left it in the etching solution longer. But if you have a few spots were the copper didn't etch all the way, take a razor blade or Dremel and remove the unwanted copper. Be careful not to cut any traces.
Step 9: Making Your Own Easy PCB! Part 6: Cleaning, Again!
Your almost done! Using the steel wool soap pads to rub off the ink, exposing the
copper traces beneath. Now all that's left is to take the Dremel and cut out all the holes! You will need to use a 1/32 bit.
Step 10: Circuit P.1
First print off the second image on regular sheet of paper, which is the silkscreen. I tried ironing on mine, but the ink doesn't stick to the plastic under the copper very well. So just print it off and use it as a guide. You could even try taping it to the board or using clear sticker paper. If you were to print it off on clear sticker paper then you would need to flip the image (flop, invert).
Notice that we will be sticking in the components from the blank side (top) of the board. The top side of the board is the blank side and the bottom is the side with the copper traces. Make a two marks on either side of the top of the board so that you know which side is up. Keep the silk screen oriented as well. Refer to it so you know which way components are installed. When soldering you may get confused because everything will be reversed.
- Place the 20 DIP IC socket into the PCB and bend all the leads over to hold it in place. Solder pins 3-6, 10, & 20 to the PCB.
[Pictures 1A, 1B, 1C]
- Solder in the 4 2N222A transistors into the board and solder them.
[Pictures 2A, 2B] - Solder in the 4 1kΩ resistors. This resistor is the one that controls the transistors. Be careful not to mix them up with the resistors for the LEDs because the circuit won't work. They need to be the 1kΩ.
[Picture #3]
- Solder in the 4 150Ω resistors into the board. These will be current limiters for the LEDs so you don't burn them out!
- Time to start with the LEDs. Push them in until they stop at the little square that's on the lead. This will give you enough room to bend them as you see fit. Make sure you get the orientation correct. I had some cheap LEDs that had the flat side on the wrong side. Remember that the flat side marks the negative side. Repeat this for the other LEDs. Make sure that each row contains LEDs of the same color. Refer to picture to know where which colors go. Leave enough leads on the top of the board to bend them. If you solder them right up to the board then you won't be able to bend them. [Picture #4]
Step 11: Programming the ATtiny2313
I made a very detailed and updated i'ble on how to do this. Visit
https://www.instructables.com/id/How-to-Program-ATt...
for instructions on how to program your ATtiny2313.
Push the ATtiny2313 into the circuit. Make sure the orientation is correct. The little notch of the chip should be facing to the right of the PCB.
Step 12: Finishing Up
I created two big pads for you to solder + and - connections. Load the battery pack with AAAs, and solder the two wire coming from the battery pack to the correct pads on the board. If the board is properly oriented, the RED wire will be soldered to the right side.
Using some cork or other non-conductive material tape it to the metal bar on the bottom of the skates. Then tape PCB to the cork. You may want to cover the whole backside of the PCB in tape to prevent any shorts, but the cork does a great job of that. Tape the battery pack in place. Note, you may not find such a handy place as I did. You may need to solder on long wires to the battery pack so you can run them up your shoe and stuff the pack into your sock. Get creative! Tape the battery pack to the side or top of shoe, or even under the circuit board.
Last and final step, be the coolest dude on the skate floor!
I hope you enjoyed this i'ble if you have any questions or comments feel free to PM me or ask in the comment box below. Please vote for the Maker-Lympics, Full-Spectrum Laser, and 123D circuits contest. Thanks!
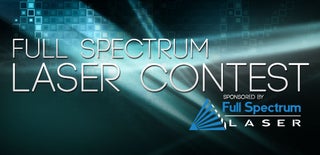
Participated in the
Full Spectrum Laser Contest
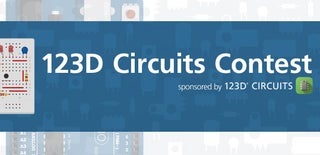
Participated in the
123D Circuits Contest
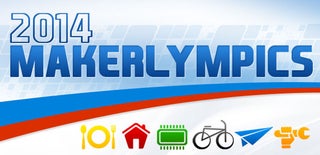
Participated in the
Makerlympics Contest