Introduction: Elemental Iron Man T-Shirt
One of these days, I will finally finish my MK3 Iron Man suit. But until then.....this will just have to do! For halloween this year, I wanted to make a nerdy "iron man" t-shirt using the periodic element for Iron. To add to this super simple and easy project, I decided to combine some crafting, 3D printing, laser cutting, soldering, and more to make a unique t-shirt costume.
Through this Instructable, I outline all of the materials I used, as well as the techniques (and mistakes) I implemented to create this last minute project! Check out the embedded video for an overview of the build, and thanks for reading!
Supplies
I used the following supplies to build this "suit"
- Two cotton t-shirts
- Iron-on velcro
- White felt
- 3 Black EVA Foam Sheets
- 12v LED light strip and controller
- 11.1v LiPo battery
- Xt60 connector
- Barrel connector
- Switch
- Red and Gold PLA Filament
- Sewing supplies
- Soldering supplies
- Hot glue sticks
I also used the following tools and machines:
- Scissors and X-Acto knife
- Soldering iron, wire cutters, heat gun
- LulzBot TAZ Pro 3D printer with a SE head
- Universal CO2 Laser Cutter / Engraver
- Sewing Machine
- Low temp & High temp hot glue gun
- T-Shirt Press
Step 1: Designing the "Reactor" Patch
To create the patch....or "reactor", I used Adobe Illustrator to create layers that would be assembled to give the desired effect. First, I created a simple design based on the periodic element for Iron with basic text and an outer box. From there, I copied and pasted this design to create the following layers:
- Bottom Layer - Square base that all pieces would be glued to
- Middle Layer - Outer ring to stop LED light from escaping off the sides
- Upper Layers - A negative of the element design to cover the LEDs so light only shines through the element
- Top Layer - The element text / box
A key tool for this was the pathfinder tool. This tool allows you to cut / merge shapes to create combined designs, or to slice out pieces. I used this to create the negative layer by cutting the text of the element out of a square. After creating theses layers, it was time to send them over to my laser cutter to create them!
Step 2: Building the "Reactor" Patch
After finishing up the vector design of the reactor in Illustrator, it was time to manufacture the layers using my laser cutter. I combined craft foam sheets with felt and t-shirt fabric to cut pieces for the patch in the following layers:
- Black Craft Foam - Square base that all pieces would be glued to
- Black Foam - Outer ring to stop LED light from escaping off the sides
- Black Foam - A negative of the element design to cover the LEDs so light only shines through the element
- T-Shirt Fabric - A negative of the element design to cover the LEDs so light only shines through the element
- White Felt - The element text / box
With the air-assist nozzle on my laser, I didn't see much scorching. There was a bit on the bottom of the white felt, but the top of each layer was clean. After cutting the pieces, I assembled using spray adhesive between each later. The LED light strip was adhered on layer 2 inside of the outer ring. I used the adhesive on the back of the LED in addition to spray adhesive to attach the strip. For corners, I folded the light strop ensuring I didn't overlap any of the metal contacts where you can cut the segments. If these cross (conductor on conductor), you could short your lights and damage your hardware....so be careful! This was really difficult, and I ended up damaging some of my lights. Alternatively, I could have (and probably should have) used corner connectors to make cleaner bends. After attaching the light strip, I used a low-temp hot glue gun to secure all of the corners.
Next, I put down another coating of spray adhesive, followed by the next layer of foam. This masked the LEDs so light would only shine in the areas of the element design. I put spray adhesive on this layer (#3) to then cover it using the t-shirt fabric cut with the same design (#4). This was a bit tricky as everything flexed and stretched a bit between the layering and gluing. Lastly, I put tabs of glue in the openings to put down the top layer of white felt. I avoided gluing right over LEDs to keep them bright, and I also worked to keep glue strings from just making a mess of the whole project.
Step 3: Designing the Power Supply Box
Next, I moved into Onshape to design the box that would hold all of the electronic components. I am a huge fan of Onshape as I find it to be an incredibly capable program while also offering tons of flexibility for device usage. Check out tutorials for how to use Onshape on my youtube channel here.
The box not only needs to fit everything, but also clip onto my belt and have controls for the light strip. I started by creating a box, then a groove for a sliding lid. I find that 0.015" is a good tolerance offset for PLA filament when making parts that need to slide in and out. I then opened the front of the box and created a slot for the remote to fit into so the buttons would be accessible from the outside. I also created an opening so the IR of the remote could be pointed right at the IR of the LED controller.
The box also has a hole for the LED light strip connector to fit through, and a hole for the toggle switch. Lastly, I added a clip that would allow the box to easily fit over my belt. To assist in the functionality of the design, I added fillet round overs on overhangs to reinforce the design.
Step 4: Creating the Power Supply Box
I am a huge fan of LulzBot 3D printers, and have been for some time. One of my favorite printers to use is the LulzBot TAZ pro with a single extruder head because of its quality, and high-end sensors to keep prints printing consistently. For the main part of the box, I printed using Polymaker PLA in red at a layer height of 0.3 with a fill density of 15%. I also used auto generated supports at a fill density at 5%. For the top, I used metallic gold silk PLA and printed at a layer height of 0.25 with no support and a fill density of 20%.
One of my favorite things about 3D printing is that it is such a cost effective prototyping method. One of the many mistakes I made during this project was getting my measurements wrong on the the controller, so I ended up making some tweaks between printing a new version of the box with an improved belt clip.
After printing the box, I was able to create the circuit! To do this, I soldered a xt60 connect to a battery connector and switch so the LiPo would power the LED controller. As xt60 uses a heavy gauge of wire, you need to apply a lot of heat before the solder will flow to make a solid connection. Its also important to insulate your wires to ensure all the connections are covered and safe.
Step 5: Preparing the Shirt
The shirt was a pretty straightforward part of the build. First, I placed the reactor in place on the shirt and traced it with a pencil to get the alignment squared up. I then cut out a window into the shirt that the wire for the reactor to pass through. To prevent this window from tearing during wear or in the wash, I used my sewing machine to sew a hem all the way around. Sewing is not my strength, but this was pretty easy to do.
I then used iron-on velcro to attach the reactor to the shirt. Using the pencil line I created, I placed velcro in the four corners and one in the center. I then used my t-shirt press to iron the velcro to the shirt at 300F for 90 seconds. Make sure you put down a protective sheet, like teflon, so you don't melt anything!
Lastly, I used a high-temp hot glue gun to put the other side of the velcro to the back of the patch.
Step 6: Assemble!
To finish assembly I need to put on the shirt, attach the reactor to an extension cable and then fish it through the shirt before attaching it with the velcro. Then just plug it into the controller box and power up! Running LiPos completely empty can damage the cells, so I also use a voltage reader that will chirp when the cells drop too low.
This build was a lot of fun to put together and made me feel like my lazy t-shirt costume was a bit more exciting and a bit more iron-man-like for 2022. I hope you enjoyed this project and thanks for reading! Please check out my channel or social for more projects and guides, I look forward to sharing the next build!
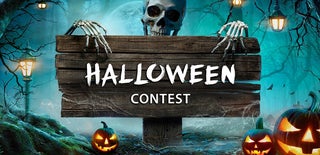
Participated in the
Halloween Contest