Introduction: Fidget Spinner - 3D Printed
Seems like spinners are trending right now so I thought I would design one.
Here is my take on a fidget spinner. Designed in OpenSCAD. I made two models.
My print settings:
PLA, 190 degrees Celcius
Heated bed at 50 degrees Celcius
0.4 mm nozzle
0.3 mm layers
40% fill (for weight = more momentum)
No rafts
No supports
Bed coated with 2 layers of Glue Stick (Target brand that changes from purple to clear)
Step 1: Tools and Materials
Materials:
1 or 3 608zz bearing (bore diameter 8 mm, outside diameter 22 mm, width 7 mm)
PLA fillament
WD-40
Jar or oil resistant container
Tools:
Computer with OpenSCAD (if you want to change design), printer host and slicer software
3D Printer
Step 2: Clean the Bearings
The bearings, especially brand new ones are packed with a really thick grease. Now this grease works great when the bearing has a heavy load on it, like a person standing on a skateboard. All the inertia from all that mass will easily overcome the viscosity of the grease. However, it does not work very well when we are dealing with something light like a spinner.
So the grease has to go. I tried Dawn dish soap and hot water, but soap and water requires a lot of mechanical work using a toothbrush and also a lot of hot water. The best solution is to dissolve the grease with WD-40. Put all your bearings in a jar. Add WD-40 until at least half the bearings are submerged. Cover the jar and set aside. Swirl it around twice a day for two days.
After two days, remove the bearings from the jar (save the jar and WD-40). Soak the bearings in hot soapy water for 10-15 minutes. Move the bearing around in the soapy water to remove as much of the WD-40 as possible. Rinse with hot water and let air dry for at least 1 hour. Give them a spin. If all the grease is removed, the bearings should spin freely for at least 5 seconds.
Step 3: Print the File
Choose which one you want to make depending on how many bearing you want to use.
If you are using three bearings then the infill can be 15%-20% (MySpinner_x_3_608.stl). If only using the 1 bearing design the infill should be 40% to give the spinner more mass (MySpinner.stl).
Attached are the files. I have included the SCAD files in case you want to change the design. Just to warn you, i am not a programmer, so my code is sloppy.
Printed on my printer, the bearing press in by hand and stay firmly in place. in the scad design i have the bearing holes at exactly 22 mm diameter. if on your print the bearings are too tight or too loose scale the model up or down a couple of percent.
Step 4: Add Bearing(s), Spin, Enjoy
After the print, do your post-print cleanup work (if any).
push the 608 bearing(s) in.
Give it a spin.
Spin time with one bearing is about 35 seconds. Spin time with the much heavier 3 bearing model is about 1 minute.
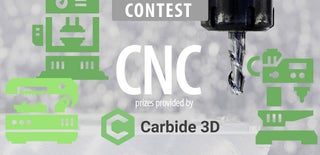
Participated in the
CNC Contest 2016
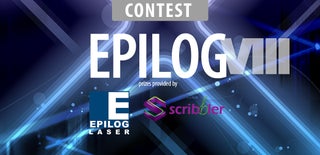
Participated in the
Epilog Contest 8
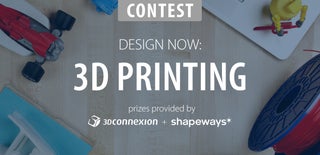
Participated in the
Design Now: 3D Design Contest 2016