Introduction: Hammered and Pieced Brass Bracelet
I created this Instructable because I love to make, wear and sell jewelry! This is a great introductory bracelet; it covers a lot of really helpful skills and tips, but is easy enough that those without a lot of experience can still create a fantastic conversation piece. I know when I wear one of them, many admire the visual impact it has! I teach art at a high school, and both students and fellow staff enjoy examining it. This particular design can be worn either way, shiny side or hammered side out.
For this Instructable, we will be looking at how to create this stylish bracelet using a sheet of metal and wire. All components in this bracelet are handmade- this is fantastic because you won't have to stock individual findings like jump rings. I am all about individualizing your own pieces, and make sure to include different ideas or variations so that you can modify your design as you like. There are also multiple ways to do the same skill, so I try to include each different method to help you develop your experience when working with metal.
Supplies:
- 1 2x6" Brass Sheet 20 gauge
- 1 Spool of 18 gauge Brass Wire
Tools:
- Metal Shears or Jeweler's Saw and Blade
- Chasing Hammer
- Texturing Hammers
- Steel Block
- 2 Round Nose Pliers
- Bench Pin
- Metal File or Needle Files
- 320-400 Grit Sandpaper
- Polishing Discs
- Drill/Flex Shaft or Dremel
- 1/16" Drill Bit or #53
- Awl
- 1.5mm Metal Hole Punch
- Liver of Sulfur (or something to oxidize the surface for blackened finish if you want a blackened finish)
- Sealant
- Ruler
- Sharpie or Metal Scribe
- Rubber Cement (if you want to glue a paper pattern to your metal)
- Jump Ring Jig (you can make one of your own with a piece of plexiglass and a chunk of wood and a couple screws to hold it in place)
Safety Materials (PPE):
- Safety Goggles
- Respirator or Dust Mask
- Rubber Gloves (if you're using liver of sulfur)
- Ventilated Area or Hood (if you're using liver of sulfur)
*Note: Any time you sand, file or hammer, it's always a good idea to wear your PPE (Proper Protective Equipment).
Step 1: Decide Your Design
Once you have all of your materials, you first need to ask yourself if you would prefer curves or squares. You will then map out your design. This can be done either on a separate piece of paper or directly scribed onto your metal sheet using the metal scribe. If you choose to scribe directly on your sheet of metal, Sharpies are always handy for making preliminary marks without damaging the metal's surface. I've included a sample template that you're welcome to use. Personally, I enjoy really organic, fluid pieces, so I opted to make inconsistent curves for each of the pieces. The template is exactly 1x6", so if you print it, do not scale the photo. To attach this pattern to the metal, I use rubber cement because it peels off after I've cut my metal.
You can modify the length of your design as needed, especially if you have skinny wrists like I do. A standard bracelet is usually 8 inches long, so I make mine around 6 3/4" to 7" in overall length. You may be asking yourself, 'But isn't my metal only 6 inches long?' Before you freak out, don't forget to account the gaps between each of the pieces and the size of the toggles. You can usually count your toggle's length to be an inch to 1 1/2", depending on the style you go with. The one I used for this Instructable is about 1" in length. If you need to eliminate some of the metal, like I did in the brass sample, I got away with only using 4" of metal with the additional length of chain made from jump rings to get the adjusted length I wanted.
Step 2: Cut Your Metal
With your metal shears or jewelry saw (or band saw if you're fortunate enough), next cut your pieces. The ones pictured here are called 'French shears', which are handy if you have small hands. I've also included images of sawing with a jeweler's saw and a bench pin. If you need more help with sawing, there's a lot of great information out there! Here's one particular website that I find incredibly useful, found at Interweave.
Be sure to wear safety googles while working with metal.
If you need to brush up on how to saw, take a look at this helpful page and video located on Rio Grande's page. Interweave also has a fantastic page about sawing metal with a jeweler's saw.
If you have simple, straight cuts, these metal shears are quick and easy. If you have more delicate curves, I recommend using a jeweler's saw. Both have their drawbacks: shears tend to leave marks on your metal surface that will have to be sanded out later and can curve the metal, which means having to flatten it later (flattening is in the next step); sawing takes a little more time. Making a choice between the two depends on how efficient you'd like to be and how comfortable you are working with metal. I tend to go with shears the majority of the time because my designs lend themselves to straight, easy cuts.
Step 3: Hammer and Texturize!
After you've cut your pieces, you will want to use your steel block and chasing hammer to flatten them. Like mentioned in the previous step, cutting with metal shears tends to curl the metal- you want to eliminate that curl. When you're hammering, make sure you are starting with the curve down (like an upside-down "u"); this will allow for an air space between your block and your metal, making it a lot easier to remove any large curl.
Continue to flip your metal and hammer it from both sides to make sure that you are getting your metal as flat as possible.
If you want to add texture, you will want to do it after you've flattened! One fun texture you can do is achieved using the ball pein side of the chasing hammer. This creates that distinct 'hammered' look you see everywhere! Texture plates or various other texture hammers can create different patterns as well. You can make each piece a different texture, or you can keep them all the same. You can also make the texture consistent, or transition texture from one end of the bracelet to the other.
For this tutorial, I am going to use the ball pein side of the chasing hammer.
Step 4: Drill/ Punch the Holes
Once your pieces are flattened, you will want to mark where your jump rings will be linking together your pieces. This can be done with the scribe or a Sharpie. I use Sharpies, because if I mess up, I can always wipe it off and start fresh; using a scribe to scratch the metal is more permanent, but does not run the risk of wiping off prematurely. Again, there are benefits and drawbacks to both ways, but the choice is yours. To place where they will join together, I measure about 3/8" from the top and bottom and about 1/8" in from the sides.
After you've marked where the holes will be made, there are two approaches you can take to make a hole in metal.
The first is using a drill- I tend to use Dremel, but if you've got a drill press, use that. You will want to use a 1/16" drill bit (or #53). If you have an awl handy, hammering a small dent in your metal first will help keep your drill from 'skipping' over your metal and scratching the surface. Then, use your drill to gradually bore out the hole. Keep the drill as vertical as you can (a drill press would help with this). Do this for all your areas where your jump rings will go. File and/or sand any burrs (metal shards) that may occur from your drilling.
The other way, which I show you in this tutorial, is using a metal hole punch. These are mostly for thinner gauges of metal, and you would want to replace the tip if you use it on anything thicker than 20. Conceptually, these work just like a paper hole punch, but on a smaller scale. They do generally leave behind burrs that will need to be filed later.
Step 5: File and Sand Your Metal
Once you have your metal cut and flattened, you will want to file and smooth any sharp edges you may have, because nobody likes getting poked! You can opt to use sandpaper, but I tend to use a hefty metal file for the long, straight edges. You can also use rounded files for curves, and smaller files for finer grooves and details.
When you file, you want to put the file in one hand and your metal in the other (or in a clamp). To be efficient with your filing, you want to apply it to the metal to the tip of your file and push it away from you, firmly holding the metal in your hand. The file does the moving, not the metal. Note that when you're holding the metal in your hand, you will occasionally slip and skin your knuckle, finger, etc. so take precautions and pay attention while you're filing!
I've included images of before and after filing and sanding. You may notice some filing marks are left behind- these you can sand out if they are deep. That will save you time when you polish later.
Just to make sure none of my jewelry can cause any scratches, I tend to take a bit of 400 grit sandpaper over my edges to make them even smoother.
Step 6: Make Your Jump Rings Pt. 2
After you've constructed your coil, you will then cut down the length of it.
If you have a jeweler's saw, there are rigs using a 2x4 and some plexiglass similar to the one above. Using that, the coil would sit in the 'v' of the wood with your saw blade running through the coil. The cut in the plexiglass will serve as a guide to cut straight down; this makes your jump rings flat on the ends, eliminating any taper wire cutters may traditionally do. The jig can be bought on Etsy, or you can make your own using a chunk of 2x4, a couple of screws, and some plexiglass.
If you're in a pinch, flush wire cutters or metal shears can do the trick. The brass jump rings were cut with French shears, but if you have flush cut pliers, those can also work. You do, however, run the risk of cutting a taper in the ends of your jump rings which can lead to problems with closures.
If you want to try and sawing the coil on your bench pin, you can, but I find that sometimes the saw doesn't sit in the same groove, and you'll get some weird cuts. In the copper cut rings, you will see an example of that where the saw cut 'jumped' a bit and didn't get as clean of a cut; that's why I recommend using the jig.
Step 7: Make Your Jump Rings Pt. 1
Once your metal pieces have been prepped, the next step is to create your jump rings. You can buy pre-made jump rings (4.5 mm brass jump rings), but if you want to be able to create your own in any size, the best way is to take your round nose pliers (or a wooden dowel rod or if you have a Gizmo) and make a coil. I used my round nose pliers to create the coil. If you are not confident in making your coil a consistent size, you can draw a line on your pliers to make sure that they are being made the same size every time you wrap the wire around, as shown above. For about 30 jump rings using 18 gauge wire, you will need a coil about 1.25 inches long.
Keep in mind, you will need at least 26 jump rings based on the sample pattern I have included. If you opt to do a row of three rings, be sure to make more to accommodate for the extra that will be needed.
If you're unsure about overall size, make a few extra jump rings; if you need to extend the bracelet and make it bigger, you can always add jump rings and connect them in a chain.
Step 8: Make Your Clasp
To make your closure, there are many different styles of making the clasp. You can opt to buy one, but I believe that it's much more meaningful to make ALL the components to your bracelet. There are two parts to the clasp: the hook and a loop. There's all sorts of different variations, but the style I will be showing you is a simple hook clasp. Again, there is more than one way to construct the hook and the loop, but I will demonstrate two in particular: the dual bar style and the simple S hook.
I've included visual steps for each method. You will need a pair of round nose pliers and bail pliers (or you can opt to use a dowel rod, but I prefer the bail pliers.
For the dual bar style, cut 2 1/4" of 18 gauge wire. Bend the wire in half. File the ends of the wires to make the end of the wires the same length. Then you will want to bend the end that has the pinched half of the wire to make a little open loop. After that, the final step will be make a loop of the opposite ends of the wire and close the loop. You can go in the same direction, or in the opposite direction; that will be your choice.
If you prefer the S hook style, that is slightly different. Measure and cut 1 3/4" of wire. Be sure both ends of the wire are filed, then make a loop at the end of one wire. Line up the bail pliers with the top of this small loop to make the 's' of the hook (or the big loop) and then use the round nose pliers to make another loop to join up with your bracelet. I like to bend the final loop at 90 degrees around to make it easier to use.
Finally, for the loop portion of the clasp, you will do similar steps to the S hook with wire cut at 1 3/8" with filed ends, but instead, you take your bail pliers, make a big closed loop, and use the round nose pliers to make the second closed loop used to join your clasp to the rest of the bracelet.
Step 9: Polish, Polish, Polish!
There are many different ways to polish, but one thing is certain for all methods: it will take time. Polishing is a gradual process. In the set I recommend from Rio Grande (see materials page for a link), you can find these silicone discs- I LOVE THEM! It's a 4 step process to achieve that illustrious, high-shine finish. First, use the white discs, the course grit, with your Dremel or flex shaft to sand out any deep gouges or scratches you may have. I usually do just the back and only in places that really need it.
ALWAYS SAND IN THE SAME DIRECTION for each application and step. For example, if you sand horizontally across the piece, be consistent throughout the step. When you change grits, you may want to go in the perpendicular direction, just to make sure you get a thorough sanding, but usually I stay consistent in the same direction.
After the deepest scratches are sanded out, switch to the black discs. These still leave a grain/texture, but will be significantly smoother. Again, be consistent in the direction, but you may want to go over all the surfaces to make the sanding texture consistent.
Next are the blue discs. These start to get a nice shine and can be a final step to polishing, especially if you have the hammered texture, but still leave several marks. I like to get a really reflective shine, and so I finish up with the final step, which are the pink discs. There's a diagram inside the lid of the container that labels it all, so if you forget, it's all there.
Step 10: Step 11: Jewelry Parts, ASSEMBLE!
Finally, you will want to carefully link all of your pieces together. Use the jump rings that were cut earlier to join each of the pieces. When you're closing jump rings, it's important to 'complete the circle', then work harden (stiffen) them by bypassing the ends several times. This is important to keep them from reopening when they snag on something. Once you have the jump rings all closed, attach the two clasp pieces. You're almost finished!
The final step to it all is to seal your entire piece. You can use a high grade wax, like Renaissance Wax, a high quality car wax, or even clear coat to prevent your piece from oxidizing or getting a patina. Some prefer a rougher, brown-toned patina from wear, but if you want to keep that high shine, be sure to protect it! I included a few images that show a sample that has a liver of sulfur patina using the same pattern.
Now, you have a finished bracelet: ta-da! I hope you enjoyed my first Instructable and learned some basics about working with metal. Thank you for following along! If you enjoyed my instructable, please vote for me in the jewelry contest!
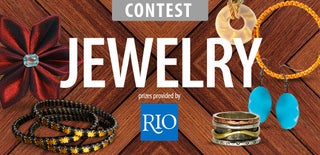
First Prize in the
Jewelry Contest 2017