Introduction: Rorschach Liquid Enamel Earrings
In this tutorial, I will be demonstrating using the liquid enameling techniques used in traditional enameling styles like grisaille. This technique can be easily substituted with custom shapes and colors beyond just simple circles and black/white enamel. What you will need is all listed here and I also included links to various locations where you can find these products. Most of these skills are fairly straightforward and can be done with a novice or beginner. I teach a high school jewelry class, and my most of my students love enameling the most out of the lessons I teach.
Supplies:
- 20 gauge sheet copper
- Sterling or Argentium Silver 20 gauge wire
- Thompsons Foundation White Enamel
- Thompsons Black Liquid Enamel Powder or Tube
- Klyr-Fire
- French Shears
- Optional: Metal Disc Cutter
- Single Mill File
- Sifter
- Brush
- Small Lid or waterproof surface
- Sunshine Polish Cloth
- 1.25mm Hole Punch
- Round Nose Pliers
- Flat Nose Pliers
- Steel Mesh Screen
- Clamp and Metal Table OR Tripod--If you go with the tripod, it comes with a screen
- If you don't have a metal table, a 12" tile is a good protective surface or an old cookie sheet (never use it for cooking once used for jewelry processes)
- Safety Glasses
- Torch--propane torches can be used with MAPP gas
- MAPP Gas
- Steel Block
- Leather Mallet
I don't endorse one particular resource, but I personally check a few different resources to price check. I only included links to help you start on your search! For example, I typically use Fire Mountain Gems, Rio Grande, Rings-Things, Thompson Enamel, and various Etsy sellers carry many of these products.
Step 1: Cut Your Pieces
For this first step, you will want to cut your pieces. There are several different ways to cut metal. One, you can use the circle cutters (found online at amazon) that require using a brass hammer and you can find them at various places, like Harbor Freight. Anytime you use steel tools with force, you want to use a brass hammer to prevent your dies from mushrooming. There are precut circles you can buy at a much higher cost at about $1.10 a circle, or you can buy the sheet metal and do the cutting yourself. The circle cutters demonstration can be seen in this video. You can also use french shears and manually cut them out as well. Ultimately, it's the matter if you plan on only doing it once versus a lot and how much you want to wrap up in tools vs time. The shears are good for large slight curves and straight cuts. If you plan on manually cutting and want them to be consistent, you can use paper and rubber cement to attach the paper templates to the surface of the metal. Apply the rubber cement to both surfaces and let dry before attaching the paper to the metal. It allows for better placement and it won't move around on you as you try to cut.
Step 2: Hammer the Metal Flat
After you have your forms cut, use a steel block and leather mallet to hammer the metal flat. When resting it on a steel block, you always want to hammer the side that when resting, it makes a 'bubble' off the block, so edges down, rather than edges facing upward. When satisfactory that you hammered most of it flat, flip it over and repeat until you get a really flat piece. This will make the filing easier and enameling smoother.
Step 3: Punch Your Holes for Your Earring Wires
Once you have your metal cut and flattened, punch your holes. If you have a 1/32" drill bit, you can drill your holes, but these little hole punches are fantastic! I like to use the 1.25mm size, primarily because it fits a 20 gauge wire comfortably. They work just like a paper punch, but takes a little more effort.
Step 4: File Your Edges
Smooth your edges using either sand paper (preferably 220 or 400 grit) or a single mill file. I tend to use the file for most of the smoothing and dulling of the edges on many of my other projects. Most people who wear jewelry like to fiddle with it, so you want to make sure your edges are nice and smooth. Here in the photo, you can see I also added a slight bevel to the edge to remove any burrs from cutting or filing the edge.
Step 5: Clean and Prep Your Metal
Scrub with a sunshine polishing cloth to remove any tarnish that may be on the metal. It should be bright and shiny bare copper. Wash with soap and water to remove any residual oils and compound. Any that is left behind can cause the enameling process to go wrong. You could substitute the polishing cloth with a green scotch pad, which it won't be as shiny as a finish, but it will remove the tarnish you may have.
Step 6: Apply Klyr-Fire
Using a brush, apply Klyr-Fire to the one side of the copper discs that you plan to apply to and let dry. Use the Klyr-Fire only when you have metal-glass contact. If you ever have to layer glass on glass, it is not needed. This is the binder that allows the glass to fuse to the metal.
Step 7: Sift on the Enamel Powder
Place your discs onto a sheet of paper or magazine. Using the sifter, apply a thin, even coat onto the copper discs. It should be thick enough that you can't see any copper through, but not too thick that it is thicker than the thickness of the metal. Any extra you don't use can be saved as long as it's not contaminated with dirt or debris. If you place it on a shiny sheet of paper like a magazine, you will find the enamel slides off much easier than non-slippery surfaces.
Step 8: Place the Copper on a Metal Screen
Either place the tripod on a fire-safe surface (like the cookie sheet or 12" tile) or clamp the screen onto a metal table and suspend it. Ideally, torch enameling is heated from below. In my examples, I have an old metal cart that I clipped it to. When I move my pieces from the board to the screen, I typically use flat nose pliers or a pair of old tweezers as well. Make sure the holes from the hole punch are cleaned out before firing. Any left in the hole will close and is incredibly difficult to reopen once the glass is melted. I usually use a piece of scrap wire to poke through and open them up.
Step 9: Torch Your Pieces
Next, you will torch your pieces from the underside and make small circles.
Safety first. Always use goggles to protect your vision when handling fire! Tie back any loose clothing and hair so you don't catch it on fire. Well ventilated spaces are preferred.
There's three stages to look for when torch enameling.
- 'Burnt Sugar'- Most enamels change color when heated, but still have the powdered look in this first heating stage.
- 'Orange Peel'- When it's starting to get half melted, it creates a texture similar to an orange peel.
- Glossy/Glassy- The final stage when glass is fully melted.
To see these stages, I position myself where I can see the reflection glare on the glass to monitor this progress.
Let it cool SLOWLY. Don't quench in water. Any rapid cooling of the glass will cause it to break. Anytime you mix powdered glass, you want it to have the same COE. COE stands for co-efficiency of expansion, which is the rate of how glass expands and contracts when heated and cooled. Delphi Glass is a great resource for explaining this concept, but they focus on fused glass, which is a whole other type of glass art form.
Most enamel powders are already compatible, but if you get any fracturing/flaking off, there's several things that could cause that to happen.
1. Incompatible/mixed COEs
2. Rapid Cooling like quenching
3. Contaminants like dirt or
Step 10: 2nd Coat of Enamel (Liquid Enamel)
Once your piece is cooled, you will either mix your powdered enamel with Klyr-fire to make a paste or you can buy it premixed. I like to use old film canisters, but any small sealable container will do. Here in my photograph, I used a premixed one (found on Etsy). Brush on the paste with a bristle brush. The grungier the brush, the better your results will be. If you don't like your first attempt, you can always wipe it off and try until you are happy with your results. You can see I tried a variation and wiped off some. Because I am an art teacher, I have many abused brushes around, and I intentionally use the banged-up kind. If you thin the solution down further, you can create some gorgeous ink-stain or watercolor-like textures, rather than brush-stroke, similar to a dry-brush technique. The more Klyr-Fire you mix in, the thinner the solution will be. You can ALWAYS rewet/mix with Klyr-Fire to make into a paste. You can also buy unmixed paste in a really fine powder form and mix it yourself, which gives you more of a range of color to use in your designs, rather than being limited to the handful that are in paste form.
Step 11: Firing the Liquid Enamel
Once your liquid enamel is dry and after you've brushed on your abstract design with the liquid enamel, then you will torch it in the same manner as before, only this time, there's a really small window where the liquid enamel fully melts and fuses to the beautiful textures. If you heat it too long, you will lose a lot of that line separation because the glass gets too hot and the black enamel starts sinking into the white. Again, I stress that carefully watching for the reflection will help you hit that small window. As soon as you see the brushed enamel turn glossy, pull the heat away. Let it cool slowly.
Step 12: Fiddle-Head Earring Wires
Once you have your pieces torched, next comes the fun part of making the earring wires. You can spring for the premade ones, but I personally like to make them myself, primarily because I can make them silver for far less than buying premade ones. IF you want to buy sterling or argentium silver earring wires , firemountaingems.com. They have a plethora at reasonable prices. If you're like me and would rather make them, I have instructions included in the next couple of steps. The style I am going with for this instructable is called the fiddle-head style. If you want the standard fish-hook style, see my other instructable, Enameling Metal Jewelry.
When making earring wires, to conserve the wire as much as possible, I work directly off the spool, rather than cutting a length and hoping it's the right length. You will need your round nose pliers. Take the end of the wire and make a loop about 1/4-3/8" in diameter.
Step 13: Earring Wire Bend
Once you have your loops, measure about 1" from the very end of the loop and take your flat-nose pliers and make a 45 degree bend in the wire. I also like to gently curve the first inch by hand, so the first inch isn't completely straight. If you prefer straight, you can leave them straight. I find they hang in the ears a little better and balance a little more with that slight curve.
Step 14: Cut the Earring Wire
Measure an additional 1.25" for the back of the earring and cut it off. If you want to be a little more conservative, you can go with 1", but I like to err on the side of caution and go a little more generous, so they are less likely to fall out. Using your big file, file these down so they're not sharp. I usually check by gently poking it into my finger or rub across the back of my hand to test for sharpness. If you skip this step, you are likely to cut your ear with putting them in. So, in short, always file your earring wires. When finished with the first earring wire, make a second for the other earring. To make them symmetrical, I usually measure and hold them side by side as I am creating them. It takes a little practice to get them perfect.
Step 15: Assemble!
Assemble your earrings by using the round nose pliers and opening the loop, feed it through the hole on the earring, and then close it fully, so the disc doesn't come off the earring wire. Enjoy the compliments you'll get with these beautiful earrings! Hopefully you enjoyed the process as much as I and my students do!
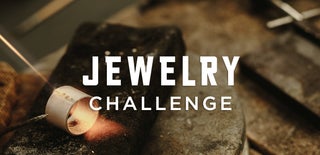
Runner Up in the
Jewelry Challenge