Introduction: How to Design and Build Astronomical Clocks
In this instructable I'll discuss my techniques for designing and building astronomical clocks. There is no one right way to do this sort of thing but in the process of learning I have found a lot of wrong ways. Rather than walk you through exactly how to build one of my designs I want to show you how you can design and build your own from scratch. So strap in if you are interested, and be prepared - these things are like potato chips. One is never enough!
Step 1: Tools and Materials
These will vary depending on your preference and design, but in general you will need:
Raw Materials (for a wooden clock)
-Plywood (for gears. Plywood is ideal because it does not have a weak grain direction. Hardwood gears are possible but require extra steps)
-Wood for the frame
-metal rods and tubes (I've used aluminum, copper, and brass. Brass is probably best)
-Wood glue
-epoxy
-Synchronous motor
-lamp wire
-solder
-Mineral Spirits
-Tung Oil
Tools
-A way to cut gears (I've used a laser cutter and a scroll saw. I actually prefer the scroll saw. You could also use a CNC)
-Planer (to prepare wood for the frame)
-Band saw (to cut the frame)
-Drill Press (this is essential)
-Soldering iron
-Tap and die (optional)
-Belt Sander (for the frame and to shape planets)
-Sander
Step 2: A Note About Synchronous Motors
I use a 1 RPM synchronous motor to drive my clocks. Synchronous motors run on A/C power (meaning, they plug into the wall) and use the alternating current to drive the shaft motor. That makes the motor extremely accurate. The downside of this of course is that you are going to have to use A/C current for this project, which can be extremely dangerous. Be careful. That said, using these motors is about as complicated as wiring a lamp socket. If you are comfortable doing that with a little bit of soldering added in, then you are set.
A few tips when considering the motor for your clock:
-Buy new. You can buy these on Ebay for pretty cheap but you have no guarantee on the quality and you have no idea if they were designed to run continuously. Cheap synchronous timing motors are not designed for continuous use and can overheat. The motors I use are about $50 with shipping.
-Use 1 RPM motors: for astronomical clocks slower is better. This is because a lot of the orbital periods you want will be pretty slow (for instance, Saturn takes ~33 years to go around the sun). However, I've run into a lot trouble trying to find reliable, slower synchronous motors. 1 RPM is easy to find and buy new.
-Synchronous motors run hot: When you plug one in you will notice pretty quickly that it will heat up. This is normal, but it should never get so hot that you cannot hold the motor in your hand. I also use a heat sink in all of my clocks that helps prevent the wood around the motor from getting too hot.
-They are almost silent: Almost, but not quite. Some of my motors groan a little every once in a while. When the motor starts to fail it can make some really strange noises.
-They don't last forever: Since I've started buying new 1 RPM synchronous motors I haven't had many issues. I've had one running for about two years with no problems. All the same you should be prepared to replace your motor in the future: clocks can last forever but motors definitely can't.
-They are pretty strong: I haven't had any issues with running a whole lot of gears on one motor. That said, the amount of load probably shortens the life of the motor. I've burned out recycled, slower motors on my planetarium.
Step 3: References
I have found the following books extremely helpful:
A Practical Guide to Wooden Wheeled Clock Design by Clayton Boyer
This book is focused on building weight-driven wooden clocks and is a gem. Mr. Boyer's designs are stunning and he also sells plans on his website.
Gears and Gear Cutting by Ivan Law
Goes over the basics of gear theory and calculations
This book is available in full for free on Google Books. James Ferguson was an incredible horologist and all of his designs are described here. My Planetarium and Tellurion use gear ratios from this book - I just added gears for the clock and calendar.
Step 4: Gear Ratios and Design
To design a clock you need to understand the basics of designing with gears. Don't worry if this seems like an overload of information - it really is pretty basic once you get going.
Basics
Gears are used to transmit power between one shaft and another. If Gear A is moving clockwise and it turns Gear B, Gear B will turn counter-clockwise (the same movement is passed on but in the opposite direction). If you need gear B to turn in the same direction as A, a 3rd gear, or idler (pinion) , is needed. The diameter of the gear (and the number of teeth) are directly related to the speed of the gears.
Tooth form
The take home point is that there are two types of gears: cycloidal and involute. Both types of teeth allow the teeth to engage without locking. Improperly formed teeth will result in noise and a loss of efficiency in the gear train.
Involute is the standard today (and is most likely what your gear generator will be making).
Designing with Gears:
Here are a few definitions to get us started:
Pitch Circle (or Pitch Circle Diameter, PCD): The imaginary diameter of the gear teeth and bearings in peripheral contact (where the two gears will actually mesh). Imagine that you have replaced your gears with two circles that turn each other with friction - the diameter of these circles is the pitch circle diameter.
Pitch Diameter (PD): the PCD in inches (a lot of definitions depend on whether you are using metric or imperial units. Swayed by common practice, I go with imperial. Once you pick a system be sure to be consistent).
Pressure Angle: The angle on an involute gear between the acute angle formed between the line of action and the common tangent to the two pitch circles. You don't need to worry about the formal definition much - you just need to be consistent. A pressure angle of 20 is common.
Diametrical Pitch (DP): The number of teeth divided by the pitch diameter. Two correctly meshing gears will have the same DP (and pressure angle, see above). For instance, if you need two gears, one with 20 teeth and one with 10 teeth, and you choose a DP of 20 than the 20 tooth gear will have a PD of 1", and the 10 tooth gear will have a PD of 0.5".
Center Distance:The center distance is equal to the sum of the pitch diameters of the two gears divided by two. In the above example the center distance is equal to (1"+0.5")/2 = 0.75"
Gear Ratio: The ratio of gear teeth required to reduce or increase the speed of the shaft. For instance, for every revolution of the 20 tooth gear, the 10 tooth gear will turn twice, and so the speed is increased by a factor of two.
Step 5: Decide on Your Clock Elements
What do you want your clock to do? The design elements are up to you and just about anything is a possibility:
-The planets moving around the sun
-The moon moving around the earth
-The stars visible in the sky
-The phase of the moon
-The moons of Jupiter
-The time on Mars
-Calendar
-Day of the week
-And of course the time of day (might as well)
I use a 1 RPM synchronous motor to run my clocks. So be aware that if, for instance, you want to show Saturn moving around the sun you are going to have to get from 1 revolution per minute to 1 revolution per ~33 years. That is going to require more gearing than if you just wanted to show the moon moving around the earth, or 1 revolution per ~29.53 days.
Once you've decided what you want your clock to accomplish you can move on to the design phase.
Step 6: Gearing Your Clock
OK, now we have some basic ideas about what we want to do and how we want to do it. For this step I will go through gearing a clock using some of Ferguson's gear ratios (his clock designs are explained in detail in his biography and I used them for my first two clocks). In my next step I'll walk you through how to design your own gear ratios for orbital periods.
Remember to keep the direction of your gears in mind. A gear that turns clockwise will turn the next gear counterclockwise. Your hour and minute hand need to be clockwise and planets should turn around the sun counterclockwise.
Step 1 - Minute Hand: All of my clocks tell the time here on earth, so my first step is to get from 1 RPM to 1 RPH. That is a speed reduction of 60 (1 revolution per minute * 60 minutes per hour = 1 Revolution per hour). Any combination of gears that gets us to a speed reduction of 60 will work. For this clock we will use two gear sets: 8-48 (a speed reduction of 6) and 8-80 (a speed reduction of 10). Combining those you get 6*10 = 60. In general 8 teeth should be the minimum for your gears. Fewer teeth and the gears just don't run well. 10 is even better, but as you can see from this calculation, the more teeth your pinion (or driving gear) has, the more teeth you will have to cut in the driven gear.
Step 2 - Hour Hand: Now we just need to get from 1 RPH to 1 Rev / 12 hours. That is a pretty easy speed reduction of 12. In order to keep the hour hand going counter clockwise, we need to use 2 gear sets. I usually use 9-36 (reduction of 4) and 9-27 (reduction of 3).
Step 3 - Calendar: This is optional to include, but very useful to have and if you are showing the earth moving around the sun you need to have a 1 revolution / 365 day orbital anyway. To get from 1 rev / 12 hours is a speed reduction of 700 (1 rev / 12 hours * 24 hours / day * 365 days / year). That is pretty steep but you can get there in all sorts of ways. For instance, you can do 7 * 10 * 10 or 8-56, 8-80, and 8-80.
Step 4 - Orrery: We'll use Ferguson's gear ratios for his orrery (described starting on page 263 of his autobiography). These will be driven from our calendar gear set so, for example Saturn's pinion gear with 7 teeth will have a speed of 1 rev/year.
-Saturn: 7-206 (yes, the pinion has less than 8 teeth, but it works OK)
-Jupiter: 7-83
-Mars: 25-47
Earth: 40-40 (this is a 1:1 gear ratio because the driving gear has a speed of 1 rev/year, which is how fast we want the earth to go around the sun)
Venus: 52-32
Mercury: 83-20
Ferguson walks through the calculations involved in coming up with his gear ratio in his biography. However, you can also develop your own gear ratios to approximate almost any number. I'll cover that in the next step and then we will move on to creating a model for our clocks.
Step 7: The Stern-Brocot Method of Calculating Gear Ratios
From the previous step it is clearly pretty easy to figure out how to achieve a speed reduction for just about any integer. It is much more difficult to find the right gears to approximate non-integer numbers - for example 1 rev/29.53059 days, or the average period of the moon's orbit (also called the synodic month). To find those gear ratios you can use experts like Ferguson, you can use a computer program, or you can do it by hand using the Stern-Brocot method. This method is covered beautifully in On the Teeth of Wheels, an article by Brian Hayes (you can read it here with a free JSTOR account). Essentially the method is to approximate the gear ratio by trial and error, and it can be done very easily in an Excel spreadsheet.
For example, let's calculate a gear ratio for the synodic month. For my Planisphere clock I knew the lunar phase gear train would be driven off of the hour hand with a speed of 1 rev/12 hours or 2 rev / day. My output speed would be 1 rev/29.53059 days. To calculate the gear ratio we want you divide the input speed by the output speed, or 2 rev / day divided by 1 rev / 29.53059 days. That comes out to a speed reduction of 59.06117771.
So the speed reduction we want is between 59 and 60. So on our excel spreadsheet we start with the following:
59 1 29.5
60 1 30
The first line uses a gear ratio of 59:1. The third number is the output speed of that gear ratio, or how long the synodic month would be if we used a ratio of 59:1. The third number is calculated by dividing out the gear ratio (59/1) and then dividing that by the input speed (2 rev / day). We do the same thing for the second line and come out with a synodic month of 30 days.
OK - looking at those two lines, it is clear that 59: 1 is closer to our desired gear ratio. So we will add a line in between the first two lines and add the first two columns together, calculating out the third column as we did before:
59 1 29.5
59+60 = 119 1+1 =2 29.75
60 1 30
Now we basically just repeat that step over and over. Looking at those three lines, we know our desired synodic month period is between the first and second lines. So we would add a line between those and add the first two columns together, calculating out the third column again.
59 1 29.5
59+119=178 1+2=3 29.6667
119 2 29.75
60 1 30
You continue doing this until you get reasonably close to the output speed that you want and until you get a gear ratio that is easy to work with. For my synodic month I ended up choosing the 19313 : 327 gear ratio which resulted in 1 day of error per 10354 years (not bad!). Using the least common denominator method (remember your fractions?) I came up with 7/1 * 31/3 * 89/109 = 19313/327. This worked out to a gear train of 56/8, 93/9, and 89/109.
Isn't math fun? Remember, you do not need to do this to build your own clocks. There are tons of resources out there where people have already figured this stuff out. But if you master this tool you can figure just about anything out for yourself.
Step 8: Making a Model - Start With Gears
I model my clocks in sketchup using the involute gear add-on. I follow these basic steps:
1. Determine what diametrical pitch (DP) you want to use for each gear set (for the teeth to mesh each set of gear must have the same DP). The DP will basically determine the size of the gear and is entirely up to you. Just make sure the teeth are not too small or they will be fragile and impossible to cut. The larger the DP, the larger the gear and the easier the teeth are to cut. I try to stick between 9 and 18.
2. Set a universal pressure angle. I use 20. Just make sure it is the same for each set of gears.
3. Calculate the pitch diameter for each gear (PD = number of teeth / DP)
4. Calculate the pitch radius for each gear (necessary for sketchup: PR = PD / 2)
5. Determine what shaft radius you want to use (I use 1/16" for all of my gears, or 1/8" diameter shafts).
6. Use the involute gear tool to generate each set of gears. Set the keyway width and depth to 0.
7. Calculate the center distance between each gear set. CD = (n1 + n2) / (2*DP) where n1 = number of teeth in the first gear and n2 = number of teeth in the second gear.
8. Model the gears in sketchup, setting the center distances. Don't worry too much about how to arrange the gears, just get them in the model.
9. If you want, create gear cut-out designs. These are decorative but also functional as they reduce the weight of your gears.
Step 9: Design the Frame
Now it's time to get creative, arrange your gear sets, and design your frame. This is the most exciting and frustrating part of designing clocks for me - the possibilities are truly endless. Sometimes in the process of designing the frame I'll realize I need to re-size a set of gears in order to make things work. Keep up with the trial and error. A couple of things to keep in mind:
-The primary purpose of the frame is to support the gears and the clock elements. That mean the frame needs to be big enough and strong enough to support your design. I use 3/4" thick hardwood for the back of my frames and 1/2" - 3/4" thick hardwood for the front.
-Don't forget to include the motor in your design.
-Make sure you have enough clearance between your arbors (another word for gear shafts) and the edge of your frame. I've accidentally split my frames by getting too close to the edge before.
-Be careful that you leave enough space between your gears to allow them to turn without hitting each other.
-Leave enough space in your design to allow for supports to secure the front and back of the frame.
The pictures show my design process for my Planisphere clock (which includes a star map and the lunar phase). As you can see this went through a lot of variations during the design process.
Step 10: Printing Patterns From Sketchup
To print off patterns from Sketchup:
1. Go to File -> Document Setup. Uncheck the "Fit View to Page" box and set the print scale to 1" = 1".
2. Go to Camera -> Check "Parallel Projection"
3. Go to Camera -> Standard Views -> Top
Your model is ready to print, just arrange your component in the workspace so it prints on as few pages as possible.
Step 11: Time to Build - Cutting Gears
When I started doing this I had minimal tools so I ordered lasercut gears from Outfab.com. Now I cut my gears on a scroll saw and prepare my frame using standard woodworking tools. What you decide to do will depend on what you want your clock to look like and what you have available. The next few steps will focus on putting clocks together using woodworking techniques.
To cut gears on a scroll saw:
1. Apply the pattern to the plywood with a spray adhesive.
2. Cut out the rough shape with a band-saw.
3. Drill the center hole. It is absolutely essential that this is drilled as accurately as possible and as close to 90 degrees as possible. I try to square up my drill press before every big project. I also use these drill bits and a center finding pin for accuracy.
4. Cut out the teeth using the scroll saw. Cut close to the line but don't worry about cutting it exactly on the line.
5. Sand the teeth. I use a belt sander to take off the excess plywood on the edge of the teeth. To sand the teeth I fold a piece of adhesive sandpaper over an old scroll saw blade. This is a cheap and easy way to sand in small spaces. Sand it down to the line.
6. Cut out and sand the interior design, if any.
That's it! Your gears are ready for depthing.
Step 12: Fine-tuning Your Gears
You already calculated your center distance and designed your frame, so now is the moment you realize that the calculated center distance is not the true center distance. In fact the tiniest adjustments can make a tremendous difference in how well your gears run.
In order to make this process easier I put together a gear depthing tool which allows me to make fine adjustments to the distance between two gears. If you don't want to go through the trouble you can test your gears without depthing by running them on a piece of scrap wood. As you turn the gears pay attention to any points where the teeth stop or chatter. Mark those teeth and sand them further. My gears end up a lot more rounded than they are designed in sketchup. I made my first two clocks without a depthing tool and they run just fine, it just took some extra effort to make them run smoothly.
Step 13: Make the Frame
Once your gears are done and running smoothly you can start taking care of the frame. There are just a few things to keep in mind.
-Make sure you are using wood that has been planed flat. Failure to do so will cause your frame to wobble on a flat surface and will make you cry.
-Remember your frame is essential to the stability and strength of your clock. If your frame is weak your clock will be also.
-I always drill the holes on the back of the frame, then use the back of the frame as a template to drill the front holes. It is essential everything lines up. I had an issue with this on one of my clocks and it caused it to click very loudly exactly two minutes. It was terrible.
-I always install a heat sink behind the synchronous motor. You can do this using a router to cut out the area for the heat sink.
-If you use a printer to print out the pattern for your frame, triple check that the printer did not shrink the pattern. I made an entire frame that was 97% of the size it was supposed to be and it almost didn't work.
Step 14: Mount the Arbors and Frame Supports
Time to start cutting metal. I buy telescoping tubes and metal rods from McMaster Carr. On my first clock, the planetarium, I had no idea how to do this and used fat semi-telescoping aluminum tubes. They work but are clunky and required a lot of sanding to get them to fit. Plus they are heavy and a lighter clock is a happier clock.
My arbors and frame supports are almost all 1/8" rods. These are handy because you can use a 5-40 die to create threads on the end and can use 5-40 nuts to secure the rods. 5-40 is not the easiest thing to find but it is extremely useful to be able to thread your arbors.
I've used aluminum, copper, and brass. I would not recommend aluminum - it is easy to work with but so soft it deforms easily. Brass it the best choice but I also no issues with copper, it was just hard to thread.
I polish all of the arbors using polishing grit and a leather strap. It helps the gears run a little more smoothly.
Step 15: Mount the Gears and Test
Start assembling the gears in your clock. Once you have the spacing from front to back figured out you need to attach the gears so that they run together on the same arbor. I usually use 3/64" metal rods to attach the gears together and use epoxy to secure the 3/64" rods.
Once everything is roughed out you can assemble your clock and test. First test without the motor, just by turning the gears by hand. Everything should run smoothly. If you notice anything wobbly or unbalanced now is the time to fix it.
Step 16: Wire and Attach the Motor
To wire the motor simply solder the wires to lamp cord and cover with heat-shrink tubing. At this point I usually test the motor by itself, letting it run on a sheet of aluminum for a day or two. It is important to make sure it does not overheat - remember, these are supposed to get hot but not so hot that you can no longer hold them in your hand.
Depending on the motor you bought it may have a small metal gear already attached. I just use a dremel with a metal cut-off saw to (gently) remove that gear so that I can attach my own. Then I use epoxy to attach my gear. Then (very, very carefully) I use the metal cut-off saw dremel attachment to score a horizontal slot in both my gear and the motor's metal rod. I then insert a thin horizontal bar into that slot and secure with additional epoxy. Because of the amount of stress on this gear and the motor's heat epoxy is not strong enough to hold the connection.
To mount the motor I use a strip of metal and either bolts or a threaded 1/8" rod. You want the motor to be snug but not so tight that it hurts the motor's ability to run freely.
Step 17: Test Your Clock
This is a good time to put your clock together and let it run. Keep an eye on the motor, monitoring its heat and listening for any weird sounds. Make sure it is keeping accurate time. This is the time to address any issues with balance, noisy gears, and wobbly arbors. Once you are satisfied you can move on to the finishing touches.
Step 18: Little Bits: Hands, Planets, Moons, and Stars
This is a really fun bit, when everything is working and you can just get creative on making it look good. There is no wrong way to do this, but here are my general methods.
-For clock hands on the Planetarium and Tellurion I used 1/4" thick wood, cut on a band saw. I inlaid copper on the Tellurion hands and it really makes the clock brighter and easier to read. For the Planisphere I cut sheet brass with a jeweler's saw and used a patina from Sculpt Nouveau for the color. After applying the patina use a clear coat to seal it.
-I shape planets on the belt sander. I've never been able to try this on a lathe, but it is very easy (if tedious) to use a belt sander and you can go as big or small as you like.
-For my lunar phase clock I used sheet brass and blue patina. To achieve the weathered look I applied the patina on the entire piece of brass and washed it off. Then I used tape to mask the moon shape and applied the patina around the tape and sealed it with a clear coat.
-For my planisphere / star chart I used the same method as I did on the moon to achieve the weathered look. Before using the clear coat to set the patina I used a sharp piece of metal to score the horizon and the ecliptic. Then I downloaded a template star chart for my latitude, taped it to the front of the patina'd brass, and drilled slightly into the brass to create the stars. I drilled slightly deeper for the larger stars, making them appear brighter. Then I sealed with a clear coat.
-For my planetarium I used a laser cutter to create my calendar, but I didn't have that option for my planisphere. So I used a dremel to in-lay brass at the month dividers wood-burned the month names.
Note: in general, I just use a friction-fit to mount my hand (meaning, the fit is tight enough that the hands turn with the arbor but can still be adjusted just by turning the hand and holding the gear steady). I've also used rubber O-rings to make more snug friction-fits (I used these on my lunar phase and planisphere dials).
Step 19: Assemble and Enjoy (and Repair)
When your clock is on your wall you will feel a burst of pride and enjoy teaching all of your visitors on the finer points of astronomical horology. But be warned: these are living works of art and every once in a while they require tending. A motor might need replacing, or a gear may slip, or an epoxy seal might fail. Keep good notes on your work, be patient, and learn from your mistakes.
Thank you for reading :) Happy building and if you want to give this a try let me know if you have questions.
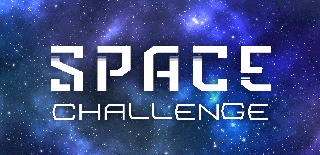
First Prize in the
Space Challenge
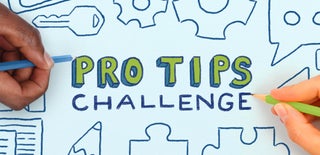
First Prize in the
Pro Tips Challenge