Introduction: Soapstone Counter Breakfast Bar
My house had a tiny dining space and a tiny kitchen. After hiring a contractor to transform my exterior window into a back door, I installed a 9-foot soapstone counter breakfast bar with floating shelves to double my counter and storage space. It's now one of my favorite spots in the house!
For this project, you need some woodworking basics (tools and supplies) and soapstone slabs or other counter materials.
Supplies
Materials
- Soapstone slabs. I bought the Kitchen to Go kit from M Teixera Soapstone: https://www.soapstones.com/. Unfortunately they now show the kit as out of stock, but you can buy slabs from other stone suppliers if you look around.
- Wood for counter supports and shelving. I used hard maple.
- Shelving supports. I bought metal heavy-duty J-Lip shelf brackets.
- Good screws: I'd recommend spending a little extra money on good screws from a supplier like McFeely's. They're better quality than what you can find in a hardware store and don't break or strip easily.
- Soapstone finishing materials: epoxy and sandpaper
- Wood finishing materials: wood glue, sandpaper, tung oil, mineral spirits
Tools
- Standard woodworking tools: tablesaw, joiner, planer, circular saw, sander, drill, studfinder.
- Safety: respiratory, hearing, and eye protection
- Countertop seam setter (I bought these: link)
- Optional tools - lacking manpower, I used pulleys and a hydraulic lift to help move my soapstone slabs. I happened to have the lift on hand and bought the pulleys, rope, and lift straps from Amazon and Cal Ranch. Each slab weighs around 200 lbs, so it isn't too bad to move if you have enough help.
Step 1: A Note About Soapstone
Soapstone is great for a DIY counter. You can cut and sand it using standard woodworking tools, install with epoxy, it's not crazy heavy to move, and it looks amazing. It is also non-porous and heat resistant, so you don't have to seal it like granite and you can stick hot pans on it.
However - soapstone is soft and can be dinged and scratched easily. It darkens with oil, so if left un-oiled it can collect darker spots over time. If you want it to be uniformly dark you have to oil it routinely. It's also pretty expensive. And as with working with any stone, you should be very careful with respiratory protection while cutting and finishing the slabs.
I'm leaving my soapstone natural, so I don't have to do any regular oiling or maintenance. It's lower maintenance than the wood slabs I have elsewhere in my kitchen. That said, this project would also work well with wood or even concrete slabs, although the installation method would have to be adjusted for other materials.
Step 2: Building the Counter Support Box
I used 2-inch thick hard maple to create the box frame. Each piece of the box frame was joined, planed, and cut on the tablesaw to size. The dimensions are about ~9 ft long by ~22-inches wide to support the 25-inch wide counters. Due to the length, I didn't try to use any fancy joints as it would be difficult to clamp properly. So I just used butt joints, used screws to secure the joints while gluing, and reinforced with wooden dowels.
To doubly reinforce the joint, I built two L-brackets out of 3/4-inch maple for the front of the frame. These hide the ugly butt joints from the front and are screwed into place on both sides to provide additional reinforcement. For the back of the frame I cut a flat brace to reinforce the joint. The braces are installed after the counter support is screwed into the wall.
Also, this is a great way to find out that your walls are not square! I had to fit the box frame via trial and error and used a circular saw to shave off the ends to fit my wonky walls.
Step 3: Building the Corbels
The corbels were designed to slot into the box frame. These provide support from the back to the front of the box frame to keep the frame from dipping and provide additional vertical support along the wall. The right-angle pieces are attached via rabbet joints and cut out of 2-inch thick hard maple. I cut the curved pieces with a bandsaw and glued to the center of each corbel. I used the open-slot design both for looks and to allow me an extra space to screw the corbels into the wall for additional support.
Step 4: Finishing the Wood
To finish the wood:
- Sand to 220 grit. I wet the wood between sanding to raise the grit and improve the finish. My usual progression is 80 grit, 100, wet, 100, 150, wet, 150, 220, wet, 220.
- Apply a 50/50 mixture of mineral spirits and tung oil. Allow a day to dry between coats and rub the wood with 0000 steel wool before applying additional coats. I usually apply between 7 and 11 coats depending on the wood, the use, and my patience level.
Step 5: Prep the Wall and Install the Counter Supports
Before installing anything I painted the walls dark blue to give my kitchen some much-needed contrast and color.
I don't have any good pictures of the support installation process, because I did it alone and spent most of the time swearing and hitting my head on the box support while crawling around. Get some help!
-Before installing I located each stud. The box support is screwed directly into the studs: Six along the back wall and one along each side. I used the longest, strongest screws I could find to make sure everything is secure.
-I located the corbels on the four outside studs. I might build an additional two corbels for the center, but don't think it's needed for structural support. I did add a horizontal support roughly in the center of the box frame where the two large slabs meet.
-I slotted the corbels into place. Each is screwed into the front of the box frame and into the wall.
-I installed the braces on each corner, screwing them into both pieces of the box frame to reinforce the joints.
-I plugged the screw holes with 5/8-inch wood plugs after installation was complete.
Step 6: Over-engineer Your Soapstone Moving Process
This step is not necessary if you have enough people who can help lug your soapstone around. I wasn't comfortable asking my awesome helpers (hi mom and dad!) to deadlift the slabs, so I installed a pulley / hydraulic lift / ramp system to minimize the amount of lifting required.
- I installed two pulleys on my ceiling. One was a 7:1 pulley (link). After testing it I added a snatch block pulley to make it even easier to lift. I bought a lifting strap from a Cal Ranch and secured it to the soapstone with some spare straps.
- I created a wooden frame to support the soapstone slabs on the hydraulic lift. In the pictures you'll see a horizontal bar along the bottom that I actually had to remove so that I could tilt the soapstone onto the countertop.
- I built a long ramp with spare wood and 2x4s out of my back door. Fun fact, melanine is very slippery! Not great for ramps while lugging a heavy cart!
To move a slab:
- I used the pulleys and a lift strap to move the slab onto the lift
- Secured the slab to the lift frame
- Pulled the lift up the ramp and to the counter supports
- Lifted the slab as high as the lift would allow
- Removed straps and gently lowered the slab onto the counter supports. Note: you really want to avoid hitting the slab on an angle while lowering as it could crack the slab.
- Push the slab into place
I had two helpers for this process, mostly for getting the lift up the ramp and for lowering the slabs onto the counter.
Step 7: Cutting Soapstone
My slabs are 4-feet long and my counter space is just under 9-feet, so I needed to cut an additional piece of slab to fit. To cut the stone I used a circular saw with a stone cutting blade. It is easy to cut as long as you are not cutting into anything beneath the slab - any supports should be on either side of your cut and not directly beneath. It is hard to cut perfectly square - if I were to do this again I would build a jig first to keep the saw perfectly flat.
Safety note: I use a half-face respirator with P100 cartridges whenever I generate dust in the shop. It is especially important to use respiratory protection and have good ventilation when cutting stone due to silicosis and potential impurities in the stone that can be hazardous. After cutting I used a shopvac to remove the stone dust from my shop.
Step 8: Setting and Gluing the Slabs
Get out your seam setter!
To install the slabs I dry-fit everything with the seam setter before gluing the slabs. The seam setter is just two suction cups set on either slab that can be adjusted to move the stone up/down and pull them together. Once the dry fit looks good, use painters tape to mask either side of the seal, mix epoxy (I used 5-minute set clear epoxy), apply to the seam, and use the seam setter to pull the stone together and keep the seam flat.
They worked beautifully for my two large slabs, however my short slab (on the right side of the image) was too small / close to the wall to use the seam setter. As a result I applied epoxy and used a shim between the short slab and the wall to push the slabs together. The seam on that side does not look nearly as good as the central seam - I could have got around this by putting the short slab in the center, or cutting one of my long slabs shorter and using a larger slab on that end. I didn't want to waste any stone, so I just have a wider seam on that side.
Step 9: Finishing the Countertop
Once the slabs were glued and in place, I hung plastic sheeting around the counter to contain dust for sanding. I sanded the entire surface and front edge, rounding the top edge as I went, with 80, 100, 150, and 220 grit sandpaper. Sanding is really crucial to transform it from a rough surface to a polished look.
After sanding I used the hydraulic lift to lift the countertop and apply adhesive between the stone and the wooden supports. Finally I caulked all around the edge between the stone and the wall and all along the front between the stone and the wooden supports.
Step 10: Install Shelves and Enjoy!
For shelves I used 1-inch hard maple glued to ~11.5 inches wide. The shelves were prepped using the same wood finishing methods as the counter supports. I used the metal J-brackets for the main supports (screwed into studs) and reinforced with L-brackets on the top.
That's it! The extra counter and storage space is a huge improvement and now this counter is one of the most used areas of my house. Eventually I'll build my own cabinets and replace the rest of my countertops with soapstone - I'll let you know how it goes :)
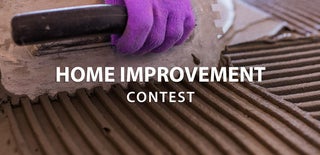
Runner Up in the
Home Improvement Contest