Introduction: How to Make a Live Edge Desk
Live edge desks are all the rage these days, especially now with so many people working from home this last year. So I figured I would try my hand at making one since the space it would occupy is not very large.
So in this Instructable I show you how I scratch built one, woodworking is not my forte but I think this desk came out awesome.
If you like my project consider voting for me in the wood working contest.
Step 1: Materials and Tools
Here is a list of the major materials and tools I used. I may have forgotten some of the smaller items and tools.
Materials
- Slab of live edge wood
- 3" x 1" x 1/8" Rectangle Steel tubing
- 1" Angle Steel Tubing
- 1" x 1" Steel Flatbar
- Misc Screws
- 8-32 Screws and Inserts
- Clear Epoxy
- Tack cloth
Tools
- Circular Saw
- Welder
- Straight edge
- Drill and bits
- Clamps
- Spokeshave
- Various Hand Tools
- Sander
- Sandpaper
Step 2: Welding the Legs/Stand
For the legs I thought about making them from wood but ended up going with metal because it would be a nice contrast with the maple hardwood.
I mocked up the angles I wanted for the legs on some cardboard, this made it much easier to cut and align them.
Made from 3" x 1" steel rectangle tubing, the legs are solid and look nice too. Fabricating them was easy, I just aligned them to the cardboard and used some magnets to hold them in place when tack welding them together.
On the top of the legs a piece of 1/4" plate was welded and then holes drilled so it could be used to attached them to the desk top.
The bottom of the legs have holes tapped for some adjustable threaded feet.
The mill scale on the steel was left as the finish, it is rust resistant and was rubbed with some oil for additional protection.
Note: Something really important is to drill the holes extra large or channel the holes, so if the wood contracts or expands with the changes in humidity there is some give and helps prevent the wooden desktop from cracking. There are better ways to address the expansion of the wood but this was the easiest way for me, I'm sure better table builders than me have other solutions.
Step 3: Preparing the Live Edge Slab
The wood I chose was a beautiful piece of Ambrosia Maple for the desktop. This type of wood has a cool looking pattern that is caused by fungus that infects the tree from wood boring beetles.
To prepare the live edge slab, the wood was trimmed to size using a circular saw and a guide, I don't have any pics for this but it's pretty straight forward. I'd recommend taping the cut line to prevent tear out and use a fine tooth blade.
Next the live edge was cleaned up by using a chisel to remove the bark and soft wood under the bark, being careful not to dig into the actual inner part of the wood. A spokeshave made this really easy too.
The top of the desktop was sanded to a smooth finish, starting with 220 grit and then up to 280 grit, since the wood was already very smooth from the planner.
Brass screw inserts were installed where the stand of the desk would be installed. This allows for easy disassembly of the desk for storage or transport. If screws were to be put directly in the wood, they could strip over repeated loosening and tightening.
Step 4: Assembly
The assembly of the desk was straight forward, the top was bolted to the stand via the threaded brass inserts. The rear steel brace had holes drilled in it and was screwed to the desktop but only loosely and the holes were oversized to account for the expansion and contraction of the desktop.
Step 5: Sealing and Finishing
To seal the desktop, I thought about using varnish but I ended up using clear epoxy because it's very clear and won't give the wood a yellow tint. Also epoxy is incredibly durable and I can wet sand it to get a super smooth satin finish. The waterbased varnishes are not durable at all and even tho they state they are durable, they are not, trust me stay away from them for this purpose.
The epoxy I am using is for making surfboards but there are other types out there, amazon has a selection of them.
When working with epoxy follow the manufactures directions for mixing, usually they give directions by volume and by weight. I prefer using weight as it's easy and you don't need special pumps or measuring cups. When actually mixing the epoxy, don't mix it too fast or too hard or you will introduce air into it which will make the finish cloudy looking. Try to keep the stir stick in the epoxy when mixing and scrape the sides when mixing as well.
Sealcoat
I wiped down the wood with a tack cloth and then applied a seal coat first, to prevent too much epoxy from soaking in. I used a plastic spreader to apply the epoxy but a brush would work too. I like using a spreader because I was only trying to apply a very thin coat.
After it hardened (overnight) , I wet sanded it with 220 grit sandpaper, this removes any bumps and ridges. I let it dry and made sure to clean off all the dust with a tack cloth, before applying the next coat of epoxy.
Second Sealcoat
For the second coat of epoxy, I applied it a bit thicker and used a chip brush to apply it. Chip brushes are cheap and since the brush will be ruined after applying the epoxy there is no reason to use an expensive brush. To apply the epoxy to get the an even coat, start by pouring out all the epoxy onto the desktop and then using the brush, "plow" the epoxy around, this spreads it out and prevents it from hardening too quickly if left in the pot too long. Next coat the edges and then using a light touch go over the epoxy with long overlapping brush strokes. Do it crosswise and lengthwise, the epoxy will level out by itself to a certain degree as well. My video shows how to do this as it's easier to see than explain.
Optional: You may notice that there are small trapped air bubbles in the second coat. Use a blow torch on a low setting and gently lick the flame over the top of the epoxy. This will smooth out the epoxy and pop any trapped air bubbles.
Final Wetsanding
So at this point we can call the desk finished but I did end up wet sanding the top one more time with fine grit sand paper, starting with 320 and working all the way up to 1000 grit and then polishing with automotive clearcoat polish. This made a super smooth finish!
I didn't show it but I also sealed the bottom of the board to keep the moisture loss even when the desktop dries or absorbs moisture from the air, this helps keep the warping to a minimum.
Hope you enjoyed this build and consider voting for me in the wood working contest!
Check out my video of the build too:
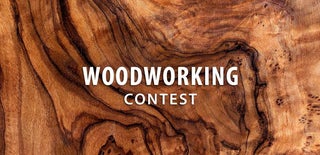
Participated in the
Woodworking Contest