Introduction: Mac Pro Junior - DIY Hand Built Case
I have a Mini-ITX x99 motherboard with a Xeon e5-2696v3 (18 core) that I wanted to Hackintosh into a G4 Cube case, along with an AMD R9 Nano 4gb. I have had the motherboard/cpu for three years, just getting around to this now as life always gets in the way. Not enough cubic space (350ci or 5.7liters) for water cooling without the radiator being external, so after the new Mac Pro (super cheese grater) was announced, I decided the components would fit into a tower case better, hence the concept of the Mac Pro Junior (610ci or 10liters). The Jr. is 63% the size of the original G5/Intel Mac Pro tower (the new mac pro is relatively the same size as the original). It will stand about 12.5" (317mm) tall and 5.25" (132mm) wide. The 2nd image is my G4 Cube concept with external radiator, the 3rd image is the full size original Mac Pro tower with my Junior concept in the center and the G4 cube on the right for comparison of sizes.
To build this case prototype I used these tools and components.
Tools:
- Hacksaw
- Jig Saw
- Drill Press
- Hand Drill (corded or battery)
- Belt Sander
- Hand files
- Nibbing Tool (radio shack)
- Locking Pliers (vice-grip)
- Bench Vise
- Center Punch
- Various drill bits and tap sets
- Slip Roller (I made my own)
- Rotary Tool with cutting/sanding discs
- Aviation Snips
- Elbow grease
Supplies
- 30x48 (762x1220mm) sheet aluminum 0.063" (1.6mm)
- 12x12 (305x305mm) sheet perforated 0.125" (3.2mm) holes
- 12x12 (305x305mm) sheet perforated 0.1875" (4.8mm) holes
- 0.75x0.125"x8' (19x3.2x2440mm) flat stock aluminum
- 0.063x0.75"x4' (1.6x19x1220mm) angle aluminum
- 2mm phillips machine screws (couple dozen)
- 4-40 torx head machine screws (30+)
- 6-32 torx head machine screws (8+)
- 6-32 phillips countersunk machine screws and nuts (dozen)
Step 1: The Concept
I have all the computer components running on the bench in a water cooled configuration with a 120x120mm radiator, but to give a little more cooling capacity and more quiet operation, I will double the radiator to 120x240mm and make it push/pull. This tutorial is primarily to show how I built the case, not how to configure a Hackintosh.
I built a cardboard prototype to test component size before I started on the aluminum case. I wanted to Braze or TIG weld everything together, but I don't have the tools or capacity to do either, so this prototype will be built completely with screws.
Step 2: Rolling, Rolling, Rolling...
I purchased a couple sheets of perforated aluminum to try to get close to the hole diameter of the original Mac Pro Tower. The smaller size has 40% holes and the larger 51% holes (more air flow). On the 5x12 inch (127x305mm) face/back, that gives me about 22-27 square inches (142-174 cm2) of free air flow. I will use the smaller holes on the front to closely match the original Mac Pro, and the larger holes on the back because of the blockages from the I/O plate, the PSU, and the video card slots.
To bend the perforated panels, I used a 1-1/4 inch (317mm) dowel and placed the panels in my bench vise. Make sure everything is square, and bend it over to 90 degrees. Very nice roll. This was my first attempt at rolling metal. Upon success, I decided to proceed with the frame.
Step 3: The Frame
The frame is build from flat stock and angle aluminum. The angle aluminum is half as thick as the flat stock. The mesh will be attached to the flat stock with 2mm screws. This means a 1/16" (1.6mm) hole in the edge of 1/8" (3.2mm) metal and followed by a 2mm tap to put threads in it. Very tiny screws salvaged from small hard drives (see my solar cookers). The frame corners are attached with 6-32 Torx head screws. Other misc 6-32 screws to hold mounting brackets and motherboard mounts.
Step 4: The Outer Shell
Time for the outer shell! Estimated size 24-5/8" x 11-3/4" (62.5 x 29.8cm). Again, mostly hand tools and the occasional power tool, this time being a jig saw. After my sloppy corners, a little hand filing smoothed them out.
I made my own roller bender with a 1.5" (380mm) dowel and a 1 inch (25.4mm) box tubing piece of scrap metal. Both are bolted on to the start line of the bend, then apply downward pressure onto the dowel and pull up on the handle to roll against the table top. I did a few test bends on leftover metal and then gave it a go on the final.
It looks groovy, so I slip fit it onto the frame. Compare it to the cardboard aided draft (CAD). Last image shows G4 cube, CAD, my Junior, and the full size Mac Pro (2006-2012).
Step 5: The Front Panel
The front panel ports are: two USB3.0, audio in/out, and illuminated power button. I could not attach it to the perforated aluminum face well, so I decided to use the aluminum angle and mount it to the frame on the left side. The holes are sloppy, and I will eventually redo this part. Once mounted to the frame, I cut the mesh panel to fit around it. I mounted the fans on the radiator and just placed the radiator inside for the photo, the radiator is not mounted yet.
Step 6: The Rear Panel
The first picture is the final, and the following photos are the steps to get there... I completed the internal mounts for the motherboard, so I could find where the I/O panel cutout needed to be. I also mounted the power supply to find where that cutout needed to be. The PCI-slot cage took some work. Several ideas, and changes, and once I built it, things changed. I ended up building it wider than I imagined (fat fingers need to be able to unplug DisplayPort latches), and it almost didn't fit on the rear panel. I wasn't sure how I was going to attach it to the rear panel, until I drew this design and decided to bend the rear panel. This gave the rear mesh some rigidity from all the access holes, and allowed my PCI cage to be mounted to the side frame. It also increased the strength along the I/O panel.
Step 7: Exterior Panels
Final shell assembly. I cut top/bottom panels and attached with 4-40 Torx screws. The screws are under the handles, so not too visible near the seams where mesh meets solid panels. The outer shell is connected with 12 4-40 Torx screws on each side. The component access panel is attached with 4 screws. Not as easy as the original Mac Pro latch, but size is a limit.
Step 8: Finishing
Finishing. I think I will sand all the deep scratches out and then sandblast it. Then either anodize it or cover with clear matte paint. This was a great little project that was conceptualized and completed in about three weeks time. Next I want to try a Mac Pro Micro with a Mini-STX motherboard, which would be 1/4 of this case size.
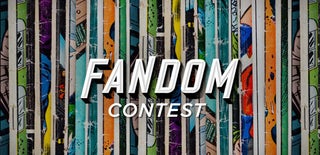
Participated in the
Fandom Contest