Introduction: Making Your Mini Laser Engraver Safer and Better
Perhaps you've bought one? They usually cost $80-$150, are advertised as something like "Laser Engraver Printer Cutter Carver DIY Engraving Machine," and have names like NEJE and SuperCarver. They're quite cute, with a laser module that looks like a little laser pointer wrapped in a heat sink. However, that cute little laser is most commonly 300mW, 500mW, or 1000mW. That's plenty of power to quickly burn designs into wood -- also more than enough to cause serious injury almost immediately if used in unsafe ways.
In the US, I think many people have gotten used to the danger of low-power lasers being overstated. Looking directly into the beam from a Class IIIa laser device, such as laser pointer or laser scanner, could be hazardous to the eyes, but they are otherwise quite safe. The catch is that those devices only deliver between 1mW and 5mW. The laser in your cheap engraver might look like a laser pointer, but it delivers enough power to require very different handling to be safe.
Avoid the temptation to try things first and read instructions after a serious problem has surfaced: I didn't even plug-in my laser's power supply until after I had built an enclosure for the unit.
I'm not an expert in the law, nor in laser safety. I'm just a maker who sees the potential, both good and bad, of these little engravers. You bear all responsibility for safe configuration and operation of your laser. I'm writing this Instructable to try to make folks more aware of the potential for serious bad... and to describe what I did with the intent of reducing the risk and improving functionality. In sum, when you saw "DIY" in the advertising of these engravers, you probably wondered what was left for you to "Do It Yourself" -- the units seem fully assembled. The answer is mount the laser and add safety features.
Actually, this Instructable not only overviews the safety issues and suggests fixes, but also applies improvements that make the machine more consistent and easier to use. There are other ways it could be done, but I took advantage of 3D-printing to make custom parts upgrading the laser engraver -- and I've made my designs for those parts freely available so you can too. Never forget that you can use your tools to make better tools.
Step 1: What's the Worst That Could Happen?
Before going into the details of how we'll make the device safer, it's useful to get a quick understanding of how much damage misuse of one of these laser engravers could cause.
- Eye injury: even 1/4 second accidental direct exposure to the beam of one of these lasers is not considered "eye safe" unless you are literally at least hundreds of feet away from the laser. It is quite possible to cause severe temporary or permanent vision defects by direct exposure, and even short-term exposure to a scattered (diffuse reflection) of the beam is hazardous. Of course, this also implies that trying to cut anything shiny is a bad idea, because shiny things will scatter a lot of laser light.
- Burning: eyes aren't the only body part you can damage. A 1000mW laser will burn your skin just as easily as it burns wood or leather, and it burns them just about instantaneously.
- Smoke: the material removed by a laser is burned and, to a great extent, released into the air. There are plenty of things you might think about engraving that you really don't want to be inhaling -- like any material containing chlorine (e.g., Vinyl or PVC). Also don't engrave Polycarbonate, Lexan, nor resin/coated materials like Fiberglass (e.g., circuit boards). Even ABS, which isn't all that bad when 3D-printing, produces nasty fumes when laser cut. Venting and/or filtering helps, but making good material choices is the best way to minimize problems. There are lots of lists of good and bad materials online: ATX HackerSpace, FabLab Devon, Pololu Robotics & Electronics, JR Laser Solutions, etc.
You can get more gory details about what damage lasers can do from many web sites, including the wikipedia article on laser safety, the laser safety facts web site, and OSHA's guidelines. These little semiconductor lasers definitely can hurt you, but.... DON'T PANIC! Think of it this way: using these lasers is truly dangerous if they are handled incorrectly, but so is improperly using many power tools or driving a car. Use reasonable care, and everything should be fine.
By the way, the sticker design above is the label I made to warn of the danger. I know it looks scary, and your laser probably didn't come with any such sticker, but it really should have. Put an appropriate warning sticker on your unit! At least print-out and fill-in the blank sticker above. The key elements for an appropriate warning are:
- Show appropriate danger or warning markings, such as the triangular laser radiation symbol
- Specify the laser class, maximum power, and wavelength -- give details
- Indicate the primary dangers, which for these lasers is exposure of eyes to direct or indirect laser light or direct exposure of skin to the laser beam
- State basic safety procedures, such as wearing protective eyewear or only operating the laser when the light is fully enclosed
It should go without saying that kids, and adults unaware of basic laser safety issues, should never be using this type of laser without supervision.
Step 2: Supplies
The main materials we used in making our modifications are:
- The engraver. In our case, it is a 1000mW @ 405nm HTPOW-branded SuperCarver (see photo).
- Some magnetic strips. Actually, these are little sheets of soft magnetic material that you can cut to size with scissors. We used these both for securing the side panels of the enclosure to the (iron?) frame of the engraver and fixing the part-holding jig to the new 3D-printed build platform.
- A 12"x12" piece of acrylic sheet which is (mostly) opaque with respect to the laser light. Unfortunately, it's a bit of a guessing game as to which sheets will let just the right amount of light through unless you buy material made explicitly for use as laser shielding. We used a translucent green sheet that is 1/8" thick... which is too opaque -- you barely see an occasional flash from the laser, but I think it would be obvious if the material being engraved caught on fire. In any case, if you must guess, guess on the dark side because too light isn't safe. Alternatively, you could 3D-print opaque PLA side panels, but that's not really a task 3D printers handle all that efficiently.
- If you guessed too dark for the sheet, you can resolve that by either enclosing a USB camera or putting in a smaller window of a material with known spectral properties. We put in a small circular window made of Roscolux theatrical lighting gel filter. The gel filters are too fragile to use for the whole enclosure, but a sampler book with many colors (and the wavelength transmission spectrum for each) is very cheap.
- Activated carbon filter material. These sheets are also easily cut to size with a pair of scissors. That said, they are definitely a weak point in our mods because they do NOT trap anywhere near all the nasty things lasers put into the air. We're looking at other options.... The issue is that the tiny fan cannot blow through material that offers too much resistance; these carbon filters give good airflow, but don't filter as well as we'd like.
- Stuff to engrave. There is plenty of cheap stuff designed to be engraved; don't try to engrave random objects, because they can generate toxic fumes, catch fire, etc.
- Optionally, a cheap webcam. Even though it is reasonably safe to look at the laser through appropriate filter material, it's even safer to stare at the live view from a cheap USB webcam. You know you're gonna want to stare at it... so spending $3 on a webcam basically reduces risk of eye damage to zero. The one I used in step 10 here is basically the same style that I used for adding a webcam to my MakerGear M2 several years ago, and the mounting is somewhat specific to that style, but it would be easy to make a similar type of mount for nearly any cheap webcam -- especially the tiny ones intended for use with laptops. It's a plus if the webcam has white (not NIR) LEDs built-in for lighting the scene.
You'll also need a filament-extruding 3D printer, some opaque PLA filament, and these part design STLs we posted on Thingiverse. It's not a lot that you need to print, and only one of the pieces might be too big to fit on the bed of the smallest filament-extruding 3D printers, but it's very hard to make these mods without 3D-printing a few parts.
What tools will you need? Well, there are lots of options, but here's what we found easiest:
- Scissors. Used to cut the magnets, lighting gel, and activated carbon filter material.
- Some way to cut the acrylic sheets. A scroll saw worked really well for us; be careful about some saws chipping the edges.
- Tools for taking the printer bed apart to mount the new build platform -- a 2.5mm hex wrench and a small adjustable wrench work pretty well. Nothing fancy needed.
Step 3: The Build Platform
The most important safety issue is getting your engraver enclosed... but that's not the thing you should do first.
Even after your laser is enclosed, you'll still need to use it open sometimes in order to adjust focus, etc. That should all be done at low-power, but even low power isn't no power... So, wear laser safety glasses and keep shiny things out of the laser's way. Shiny things? Yup; like the shiny aluminum build plate it came with.
Now that build plate looks kind of nice, and even has little notches to help rubber bands work as workpiece clamps, but it's definitely a hazard. Unfortunately, the way it is put on makes it very hard to take off. So, is there any way to darken the build platform? Sure. How about black paint or even Aluminum Black (a strong acid that can give aluminum a hard black surface almost instantly); any such coating could be applied to the build platform without having to remove it from the housing. The catch is I don't know what laser exposure will do to those coatings, so I can't recommend them.
The best option is to remove the build platform and replace it with something that can easily accept interchangeable jigs, made of a laser-safe material (i.e., PLA), to hold any of the objects we'll want to engrave. That's pretty easy to do if you have a 3D printer. The secondary benefit is that the improved build platform design doesn't get in the way if you need to disassemble the engraver base.
To swap-out the aluminum build plate, start by removing the four screws on the left and right sides of the printer that hold the black metal floor plate in place. Unfortunately, you can't lift the floor plate out because the aluminum build plate traps it, but you can lift it somewhat and nudge it out of the way a little so you can access each of four nuts that anchor the corners of the CD drive that is the Y axis. Those nuts are on the four bolts seen on the bottom of the engraver. Once you get the four nuts off (perhaps by turning the bolts from the bottom), the entire CD drive + trapped floor + aluminum bed can be lifted out of the frame of the engraver. There is a little screw on the bottom of the CD drive that anchors the aluminum plate -- unscrew it and the aluminum plate will come off, also freeing the floor plate. Reassembly is trivially easy: use the screw that held the aluminum plate to attach the 3D-printed base, put the CD drive back on the four bolts, tighten the nuts, insert the floor plate, and replace the four side screws. Done!
Both the base and the jigs get trimmed-to-fit sheet magnet glued on them. To mount an object for engraving, simply put it in the appropriate jig and place the jig on the base with the rectangle aligned with the right-side "loop." There is deliberately some play, but you can get consistent alignment by simply pushing the jig from the right side so it is squarely seated against the loop. Positioning is very consistent unless you adjust the laser focus or nudge the laser module out of alignment, either of which can shift image position by a few mm.
Step 4: Protecting Against Eye Injury and Burns
All these cute little engravers come with a pair of laser-protective goggles. Presumably, wearing them provides reasonably good protection... for the wearer. Goggles obviously offer no protection whatsoever to the innocent bystanders who happen to glance at the laser while it is cutting. It also should be obvious that goggles don't prevent you from sticking your hand in the laser light and getting burnt -- remember that at higher powers, it will burn instantaneously.
The obvious difference between these little laser engravers and the bigger, higher-powered, industrial laser cutters is that the laser cutters are all enclosed. There may be a window for you to look through to see what's happening, but the case keeps hands out and that window will be made out of a material designed to block most of the laser light. For the CO2 tube lasers, the window is usually orange/red, and the goggles that came with our semiconductor laser engraver are green. However, don't confuse the apparent color with the ability to effectively block the laser light. To effectively block the laser light, you really need to know what that light is.
All laser products in this power range are supposed to be clearly labeled with their maximum power output (typically in mW, 1/1000ths of a Watt) and their emission frequency (typically in nm, nanometers). Disturbingly, most of these mini engravers, and the laser modules they come with, are completely unmarked. They usually just list the maximum power and describe the laser color as being "blue and purple" -- an imprecise and inaccurate statement. In fact, the reason we bought one of the HTPOW version is because, unlike most ads for these laser engravers, this one explicitly stated that the wavelength of the 1000mW laser supplied is 405nm.
Let's assume 405nm is correct for our HTPOW. That wavelength is just at the visible edge of ultraviolet A (UVA), but 405nm light is visible (invisible lasers are more dangerous) and yet it is close enough to UVA so that most glasses and plastics block quite a lot of it. Green filters tend to block more of this wavelength than red or blue filters, but it depends on the particular filter. Theatrical gel filters (e.g., the Roscolux sampler shown) are very cheap and have published wavelength transmission curves, but theatrical gels are not very durable; unfortunately, most other potential filter materials don't have published response curves. If you momentarily view the low-power (focus) mode diffuse reflection of your laser through an appropriate filter, the color of the light shouldn't be purple -- through the goggles, it's greenish. You need a filter material that blocks the laser frequency fairly well... and it would be nice if it didn't block all the other light so you can still see through it.
One last note about wavelength: some lasers have more than one! Why? Because they are frequency-doubled, such as 532nm "green laser pointers" which might also leak laser light at 1064nm -- a dangerously invisible NIR (near infrared) wavelength that will not be stopped by most filter materials. According to this, 445nm diode lasers are not frequency doubled, while some (but not all) 404/405nm are actually doubled 808nm.
Step 5: An Enclosure
The key to eye safety is making the laser light be well contained. To do that, you just need to enclose the laser within the engraver.
Honestly, the enclosing structure doesn't have to be pretty, and a roll of duct tape would probably work fine. Heck, using cardboard to cover the openings in the frame should even work. The catch is that you'd like to be able to get easy access inside... so that's why I made 3D-printed window mounts. There's a small 3D-printed tray that fits into each of the three sides that get fully closed. The tray allows a sheet of appropriately dark acrylic, about 126mm x 143mm (just shy of 5" x a little under 6"), to be inserted in front of each of the side openings. Sticking a magnetic strip at the top of each sheet ensures the filters will not fall out, while leaving easy access.
Suppose you can't find an appropriate transparent filter? No problem. The dark green acrylic side panels I used turned out to be totally opaque for the laser light, so I simply drilled a circular hole in one of them and taped a piece of theatrical gel filter in place over the hole -- that protects the gel filter, but the gel filter has exactly the desired spectral characteristics. However, it is worth noting that if the material being engraved caught fire, the self-sustaining fire should be visible through the acrylic.
Don't like the gel filter solution? Use something completely opaque for the side panels and stick a USB webcam inside to monitor progress!
Step 6: Waiting to Inhale?
Almost everything your engraver marks will end up being burnt and dispersed into the air as smoke. Aside from NEVER engraving nasty materials (e.g., chlorinated plastics like PVC), it would be nice to reduce the smoke a bit.
The little fan in the engraver isn't strong enough to blow air through a very heavy filter, but it is strong enough to exhaust through a layer of activated carbon filter. That doesn't remove everything bad, but it does significantly reduce the smell of the engraver, so it clearly helps. To be precise, the carbon filter does a good job of trapping particles, but not gasses... so it really wouldn't have any impact on the toxic fumes generated by trying to laser unwisely-selected materials. Actually, even engraving harmless materials with a good air filter, you should only use this in a well-ventilated area.
Our filter assembly is very much like the 3 other side panels, but instead of using a sheet of acrylic, we'll use a piece of activated carbon filter pad cut to size. The pad is a little thicker than the acrylic, so the windowbox-like piece it sits in (ventfoot.stl) is slotted for a thicker insert. To hold the filter in place, there is a 3D-printed panel (vent.stl). Simply cut the filter material to fit, push it into the printed holder, and stick a strip magnet at the top of the holder. The filter panel mounts just like the other panels.
Step 7: Taking Control
How is this little laser controlled? The base of the enclosure contains a little microcontroller that does the real work. It even can be used to engrave a pre-loaded pattern without a computer attached by simply pressing the red power button and then the center button twice. However, you do need it connected to a computer to change the pre-loaded pattern and you can more flexibly control engraving directly from a computer connected via USB.
The first thing you might want to do is to replace the USB cable your unit came with. Our first attempts at printing all suffered unpredictable periods where the engraver would just stop, skip several lines of engraving, and then continue as if there never had been a problem. We initially thought it was a software problem. It wasn't. Although the USB cable looked fine, replacing it yielded reliable operation. We actually had the same problem with the USB cable that came with our Wanhao I3 3D-printer... so I think we're seeing a trend: some really nice Chinese tools are shipping with defective USB cables.
Another issue is that the engraver really draws too much to be powered by a typical computer USB port, but will attempt that if it is plugged in and the AC adapter isn't. This doesn't seem to cause any permanent damage, but can result in unfortunate surprises like the laser turning on when the AC adapter is unplugged -- it's presumably a problem induced by the processor rebooting when it gets a power glitch.
The photo shows the controller board in our HTPOW unit. A little research reveals that it's an 8051-compatible microcontroller with truly minimal computing resources, but it's enough. The catch is that it isn't an ideal host for one of the freely-available interpreters for standard G-code and the design is strongly oriented toward engraving images rather than drawing lines, so it speaks it's own protocol. That means it is really tied-into the software support it comes with....
Step 8: Software
You're probably thinking software isn't a safety issue, but it is. You don't want to leave the laser on high power due to a software bug. However, the problem is bigger than that: the software that talks to the SuperCarver controller board only runs under Windows. It does not even seem to work under wine on Linux due to lack of a USB driver. Of course, you can always consult "User manuel" (whoever that guy is). Ok, both the manual and the software itself have a few lapses of proper English... it's not really a big problem. If you can run the software that comes with your machine, it's actually quite usable.
In fact, because it is entirely image-driven, it is all the software you need to engrave images. It is less convenient to engrave/cut patterns with precise dimensions, although careful image scaling can enable that. The raster engraving order also can cause more heating marks than if the printer would directly follow arbitrary line segments as G-code would specify, but the engraving quality is honestly much higher than we expected. Apparently, an advantage of the 1000mW laser over most higher-power lasers is that the beam can focus to a finer point. Assuming this is the same 1000mW @ 405nm laser discussed elsewhere, spot size is around 0.1mm; in contrast, a 2000mW @ 445nm laser is quoted as having a spot size of about 0.2mm -- if true, that would mean the 1000mW unit delivers a higher energy density!
At this writing, we've reverse-engineered most of the protocol (by "we" I really mean Paul Eberhart, a fellow maker who happens to be one of my grad students). Our goal is to write a portable G-code interpreter that can run on any Linux, Windows, or Apple host computer and send the appropriate low-level stepping and laser control commands to the engraver. If/when we have that working, we'll post info on it here. By the way, there are a variety of related bits of code around. Arduino-Processing-Laser-CNC is complete code for using an arduino to control CD drive steppers and processing code on the host to convert an image for engraving. Somebody else has reverse-engineered the NEJE protocol... which is similar to, but not the same as, what our HTPOW SuperCarver uses.
Step 9: Engraving Quality
So, is this all worth the effort? Are the engravings good?
The answer is that they are surprisingly good on the right materials with the right settings. The example shown here was burnt too heavy in material that burns too easily (smearing the image a bit), but even it shows fairly good detail. Movement repeatability is also quite good unless you adjust the laser focus or nudge the laser head, either of which can easily shift the image position by a few mm. Depending on material and settings, it can take anywhere from a couple of minutes to about an hour to make one maximum-size 38mm x 38mm engraving.
In truth, the 38mm x 38mm area restriction is a serious limitation and the shape of the frame and having Y motion in the bed means you can't place the laser over a much larger workpiece to make a small marking. Still, for what it costs, it is a useful device.
Step 10: The CamPanel
Ok, I know it's reasonably safe to watch the laser do it's thing through the little filtered window... but I find myself wanting to watch it too much from too close. So, here's how I stuck a little $3 webcam inside to give a 100% eye-safe live view and allow taking stills or making videos like this one (which plays at the actual speed the engraver operated).
It's quite easy: simply replace the rear panel with campanel.stl. Just like your eyes, we don't want to blind the webcam, so glue a little piece of the gel filter over the lens. The webcam simply drops into place and the USB cable goes through either of the angled holes. A strip magnet gets glued to the top of the panel -- just like we did on the acrylic panel it replaces. The camera can rotate in the holder, so mount the panel and manually adjust the angle and focus the camera; put a piece of tape on the camera to temporarily hold that angle. Take the panel off the unit and use a little hot glue (or whatever) to semi-permanently set the angle... and get rid of that tape you stuck on it before. Done.
This webcam apparently has 3 white LEDs for lighting. What it actually has is a clear plastic thing shaped like 3 LEDs that fits over the one LED it actually has (wouldn't want to have to pay for three LEDs, would we?). Anyway, it still provides some useful lighting for both the camera and direct human viewing through the filtered window, so flick the webcam's light switch on.
I had no trouble at all with both the engraver and the webcam being controlled from USB ports on my little old atom-based netbook. Just use whatever webcam software you wish to provide the live view and capture stills or videos. There is lots of free software for this. The image quality isn't great on my $3 webcam, shooting through the green gel filter doesn't help sharpness, and the brightness of the laser spot really confuses auto-exposure (turn brightness up, contrast down), but it's 640x480 and quite usable.
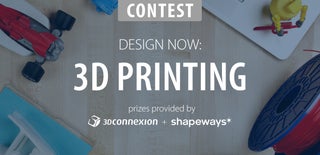
Participated in the
Design Now: 3D Design Contest 2016