Introduction: Metal Detector - Variable Frequency Using 555
My wife and 9-year old son love to go metal detecting on a weekend. I sometimes go along for a walk but it is a very very slow walk so I decided to build myself a metal detector so that I could join in. I wanted to make a simple robust design that could be easily reproduced by others wanting to build a similar design.
The design is based on the Matchless Metal Detector printed in Silicon Chip in 2002, several other people have taken this design further and now I have taken it a bit further again by making the metal detector variable frequency.
I have made this metal detector out of very cheap and available NE555 Timer IC's as I wanted to see how it performed.
The design is based on the induction balance method which will be described further on in the build.
Supplies
He is a list of the supplies I used:
- Copper dot electronics prototyping board x 1
- 9v battery clips x 2
- 0.3mm diameter Enamelled Copper Wire spool x 1
- 3 pole pcb terminals x 3
- 2 pole pcb terminals x 5
- 100k ohm panel mount potentiometer (frequency adjust) x
- 20k ohm panel mount potentiometer (fine tuning) x 1
- 500k ohm panel mount potentiometer (Course tuning) x 1
- 220 ohm resistor x 2
- Green LED and Holder x 1
- Red LED and Holder x 1
- Power Switch x 1
- Piezo Sounder x 1
- IRF510 MOSFET x 1
- 2N3904 NPN Transistor x 1
- NE 555 Timer IC x 2
- 10k ohm resistor x 1
- 2M ohm resistor x 1
- 500k ohm Trimmer Potentiometer x 1
- 10k ohm Trimmer Potentiometer x 2
- 100uF Electrolytic Capacitor x 2
- 0.01uF Ceramic Capacitor x 1
- XT30 Bullet connectors x 2 pairs
- Heat Shrink Tubing
- 4-core 0.75mm2 cable x 1m
- Various Jumper Wires
- Electronics Enclosure x 1
- 20mm PVC Pipe 2m
- 20mm PVC Equal Tee x 1
- 20mm PVC End Cap x1
- PVC Solvent Cement x 1 Tin
- M6 U-Bolts 21mm Inside Diameter x 2
- 4mm Acrylic Sheet Black x 1
- 4mm Acrylic Sheet Clear x 1
- Nylon M6 x 40 Bolts x 5
- NylonM6 Nuts x 9
Step 1: Mechanical Design
My hobbies usually focus on electronics however a large part of this build was actually mechanical.
The main structure of the metal detector is made from 20mm PVC pipe. It is important that the components of the metal detector are plastic so they do not create any inductive interference with the detector coils.
The detector coils are held in place by being fixed to a laser cut piece of acrylic which forms the detector assembly. Underneath the main black coil holder plate is another clear acrylic plate held in place by nylon bolts which is there to protect the coils from being damaged.
The detector assembly is connected to the metal detector shaft via a clevis joint. It is important that all parts are plastic so the clevis joint was 3D printed from PLA and the connection between the two halves of the clevis joint was made using an M6x40 nylon bolt. The Clevis joint was designed using Fusion 360 then sliced with Cura and printed using an Ender 3 Pro. It is important to add the scaffolding supports when printing the Clevis joint as there are several hollow sections that need support during the print.
Step 2: Sensor Coil Design
This metal detector design uses a method called induction balance. When using the induction balance method two coils are used, the Transmit Coil (Tx) and the Receive Coil (Rx). Both coils are made up of 70 turns of 0.33mm diameter enamelled copper wire wound round a 150mm former. I utilised a ductape roll as the former.
Transmitter coil - The control unit generates an alternating current which is sent to the Tx coil. A 555 Timer IC (Integrated Circuit) is utilised in this design to generate a square wave oscillation at a frequency between 400 Hz and 1000 Hz. Most induction balance metal detectors I have seen online do not have variable frequency so I integrated it into my design to see how it effects the performance.
Receiver coil - This coil acts as an antenna to pick up and amplify frequencies coming from target objects in the ground. The Rx coil is connected to a second 555 Timer IC which is setup as a Schmidt Trigger via a general purpose Transistor. If even a small signal is passed up the Rx coil this gets amplified by the transistor, setting off the 555 IC Schmidt Trigger which then alerts the user via a buzzer and /or LED indicator.
The current moving through the transmitter coil creates an electromagnetic field, the polarity of this magnetic field is perpendicular to the coil of wire. Each time the current changes direction, the polarity of the magnetic field changes. When the coils are held parallel to the ground the magnetic field is constantly pushing down into the ground and then pulling back out of it.
The pairs of coils are set up to overlap twice so that the electromagnetic field from the Tx coil is completely nulled out on the Rx coil when they are in the perfect position. Any deviation on the in this balance causes a signal to be sent back up the Rx coil. This is because if the Tx coil passes over a metallic object a magnetic field is induced in it which the also gets passed to the Rx coil to the receiver part of the controller for further amplification.
When winding the coils it is important to mark the wire at the start and end of the coil, the end wire on both coils is connected to ground. After finishing winding each coil I wound insulation tape round the whole coil. A second bare conductive wire is the soldered to the end wire and wrapped round the insulation tape round about 90% of the coil. Both coils are shielded by using self adhesive aluminium foil tape this foil makes contact with the bare wire wrapped around the coil (insulated by the insulation tape) which is then connected to ground when the coils are connected.
Step 3: Electronics Design
This is relatively simple however it is more of an intermediate project than a beginners project. If you are a beginner I would recommend that you learn the basic 555 timer circuits first such as the monostable and astable and have a go at building them.
The heart of the electronics design is two 555 Timer IC's. IC1 is used to generate a square wave used in the Tx coil and IC2 is used to detect any signals picked up by the receive coil.
The Tx (transmit) section of the circuit generates a square wave that is fed to the Tx coil via a MOSFET. A MOSFET is utilised to allow more current to be driven through the Tx coil. The equation for calculating the magnetic force on a wire is Force (N) = magnetic flux density (T) × current (A) × length (m) therefore allowing more current through the coil increases the magnetic force. The maximum output current from the 555 is about 200mA however if we use this to drive the IRF510 MOSFET it is then possible to drive a current up to about 5A through the coil, which is then limited by the impedance generated in the coil.
The Frequency at which the Tx coil operates is calculated using the equations shown below:
Minimum Frequency = 1 / (((R1 + 2 x (R2max + R3)) x C4) / 1.44)
Minimum Frequency = 1/ (((1000 + 2 x (100000 + 75000)) x 10x10^-9) / 1.44) = 410 Hz
Maximum Frequency = = 1 / (((R1 + 2 x (R2min + R3)) x C4) / 1.44)
Maximum Frequency = 1/ (((1000 + 2 x (0 + 75000)) x 10x10^-9) / 1.44) = 953 Hz
The Rx (receive) section of the circuit acts as the detector. In this circuit the 555 Timer IC is setup as a Schmitt Trigger. If an imbalance occurs between the RX and Tx coils it is fed initially to the transistor Q1 via capacitor C2 which amplifies the signal. The base of the transistor is biased using R5 and R6 and is tuned using R5. The signal is basically a weaker version of the square wave generated by the Tx coil. A Schmitt Trigger works by setting the output high if the upper threshold of the input is reached and then setting the output value low if the lower threshold of the input is reached. The nature of a 555 Timer means that the lower and upper threshold limits are set at 1/3 and 2/3 of the supply voltage accordingly. This means with a 9v supply the lower threshold is 3v and the upper threshold is 6v. The threshold and trigger pins of the 555 timer are connected together and the voltage at this point is set by a voltage divider by the three potentiometers, R7, R11 (Fine Adjust), and R10 (Course Adjust). By setting up these three potentiometers we are aiming to set the midpoint of the input to somewhere between 3v and 6v (around 4.5v). The output of the Schmitt trigger is from pin 3 which can drive 200mA therefore is capable of directly driving the piezo buzzer and indicator LED.
The electronics was built using the schematic diagram above and soldering everything to a copper dot prototyping board (perf board).
Step 4: Setting Up
Setting up the detector coils is an important part of setting up of an induction balance metal detector design. The process I followed is as followed:
- Set R7, the 100k ohm trimmer potentiometer, to about 90%.
- Set R5, the 0.5m ohm trimmer potentiometer, to about 50%.
- Set R10, the 0.5m ohm panel mount rotary potentiometer, to about 50% (course adjustment)
- Set R11, the 20k ohm panel mount rotary potentiometer, to about 50% (fine adjustment)
- Set R11, the 100k ohm panel mount rotary potentiometer, to about 50% (frequency adjustment).
- Hot glue the Tx Coil in position on the mounting plate so that it is secure.
- Turn on the system.
- Place the Rx Coil over the Tx coil and the buzzer will buzz loudly at the set frequency.
- Move the Rx coil horizontally away from the Tx coil until the buzzer falls silent.
- Keep moving the Rx coil until the buzzer starts to buzz again.
- Move the Rx coil very gently back until the buzzer just clicks (it sound a bit like a Geiger counter).
- Fix the Rx Coil in place.
When the metal detector is used in the field you will need to adjust the settings again with the Course and fine adjustment dials. I also found I needed to adjust the fine and course settings when I changed frequencies.
With some time and patience you can get this metal detector setup to detect up to about 500mm with good sensitivity.
Step 5: Testing
I tested the metal detector on my bench and then in the field. I found I got very good sensitivity on the bench once set up however the results vary depending on the size and type of metal.
The videos above show the results more clearly.
Step 6: Conclusion and Improvements
In conclusion the metal detector actually works very well for a simple low budget build.
Some improvements I would make are:
1. Try a different 555 Timer. I used an NE555 timer as I had loads in my parts box. I am going to try the LM555 Timer IC as I expect it will give me better results.
2. Improve the signal being generated on the Tx coil. I would like to try a higher quality sine wave.
3. Try different coil configurations. This would include a large cable diameter, more coils and try out both smaller and larger coil diameters.
4. Consider a band pass filter on the signal on the Rx Coil. This means I could achieve a better signal to noise ratio.
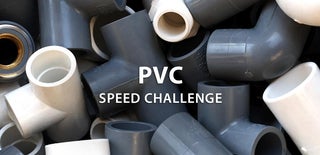
Second Prize in the
PVC Speed Challenge