Introduction: Mini Wood Lathe
I needed to make round things, if you need to make round things this is the instructable for you! I don't have the space for a large lathe in my workshop full a full-sized lathe and figured I could probably make a simple wood lathe while I save up for the sweet mini metal lathe I've got my eye on.
Also for giggles, I decided to go ultra cheap and build most of this project from scrap I had lying around. Afterall I am meant to be saving up.
Supplies
Parts
- Scrap plywood (12mm thick)
- Wood glue
- Threaded bar (10mm)
- Nuts (10mm)
- Washers
- A metal pipe or bar
- Two ball bearing races (10mm internal diameter)
- A piece of metal bar or a bolt (approx 10mm diameter)
- Screws
- A bolt for handle
- A small length of tubing for the handle
- Threaded insert (M6)
- Threaded inserts (M10)
- Pullies (see this instructable to make your own)
- Thumb screws (see this instructable to make your own)
- PVC sheet (see one of the above Instructables on how to make this)
- Lathe Live Centre
- Lathe Drive Centre
- Drill chuck that fits the threaded bar (A chuck designed for an Angle Grinder is M10)
- Speed Controller (Optional)
Tools
- A Wood vice or clamps
- Engineering Vice
- A drill (drill press recommended)
- A drill bit of the same diameter as the pipe or bar
- A drill bit of the same diameter as the outside of the bearings
- A drill bit slightly smaller than the outside of the bearings
- A square
- Marking knife (or a knife)
- Marking gauge (I'll get around to making an instructable for one at some stage)
- Saw
- Sandpaper
- A wood plane
- Tape measure or ruler
- Screwdriver
- Spanners or adjustable crescents
- Taps (M10 & M6)
Step 1: Dimensioning the Plywood
This is probably the more time-consuming part as I'm only using hand tools and offcuts. It would go a lot faster with a table saw, but I don't have one.
Cut the pieces of plywood to size and length, use a marking knife to strike a line, and then go over it with a pencil. Then glue two boards together so that you end up with plywood twice as thick (24mm). Either clamp or use a wood vice to hold the plywood while the glue sets.
Once the glue is set use a wood plane to make sure the sides are straight and all the timber is the same width.
Step 2: Make the Supports
Use a marking gauge to lay out the support, you need to make four of the same size. Once you have the lines marked out, use a saw to carefully cut them out. Lastly, use a plane to finish the surfaces.
Step 3: Drill the Holes in the Supports
Mark the centres for the bottom pipe and the head/tail stocks. I recommend drilling a pilot hole before drilling to the final size. The bottom hole should be drilled to the same diameter as the bottom pipe.
Two supports need to be drilled out to the outer diameter of the bearings, but only drill these as deep as the bearings are wide.
The last two supports only need to be drilled out to the correct size for the 10mm threaded inserts, but we'll install them later.
Lastly, drill the holes for screwing the supports together.
Step 4: Optional (not Recommended)
It's very important to accidentally forget that only two of the supports need bearings and drill the wrong size holes in all four. No worries, all is not lost! Just glue in a dowl plug, cut to size, and plane or sand flush once the glue drys. Remark the centre and drill a pilot hole again.
Step 5: Assemble the Headstock & Tailstock
Cut four lengths of the ply out and then glue and screw the supports onto these to complete the Headstock and Tailstock.
Once completed you can test fit these on the pipe to ensure everything sits flat. At this stage, you may need to lightly sand the pipe to make sure it's smooth and the tailstock can move freely, it's good for the headstock to be a little tight.
When assembling the headstock make sure the ballbearing race holes are on the outsides.
Now drill a hole through the plywood so you can install a threaded insert and use a thumbscrew to lock the head and tailstocks into place on the pipe.
Step 6: Tool Rest & Tool Base
Glue a couple of your plywood boards together to make a double-thick board. While this is gluing up cut out the tool rest and drill a hole for the metal bar (10mm) or bolt. This hole should be one size smaller (9.5mm) than the bar to make it a tight fit. You should need to carefully hammer the bar into the hole.
Now you can cut the double thick board to shape and size, this is now your tool rest support. Drill one large hole for the bottom pipe to go through. Now drill a series of holes (10mm) along the top for the tool rest to slot into at different positions. For each of these positions, you need to drill a hole perpendicular for a threaded insert. The last hole required is on the back perpendicular to the bottom pipe hole.
At this stage you can insert the tool rest and mark the required length. Now cut the bar to length.
The final step is to screw in the threaded inserts (M6) to each of the locking holes
Step 7: Tailstock Handwheel
The handwheel can be cut out of whatever material you have lying around. Another piece of plywood is fine, but for mine, I used some PVC. You can make the PVC handwheel using the same method I used to make the thumbscrews & pulleys.
Drill and tap the handwheel, I used an M10 for the centre and an M6 for the handle. Cut a length of small tubing or pipe the length of how long you want you handle. Now bolt the handle onto the wheel with a lock nut on each side and tighten it down.
You can now screw the handwheel onto a length of threaded bar and once again use a lock nut on each side to really tighten everything down.
Now drill out the holes to the correct size for the M10 threaded inserts and use a hex key to insert them. Now screw in the threaded bar through the left side. The threaded inserts on each side are likely out of alignment and you will need to use the hex key to rotate the second inserts until you can screw the handle assembly through smoothly.
Step 8: Tailstock Lock
Cut a piece of the PVC sheet, heat it in a mini oven, and then form it around some 10mm bar. When you clamp it into shape in a vice use some thin wood to leave a gap.
Now test fit this into the tailstock and drill a hole through the plywood and the PVC. Dissemble the tailstock again and using a small piece of scrap metal make a solid surface to drill and tap for an M6. I also drilled two small holes and screwed this onto the PVC.
Reassemble the tailstock and screw in one of the thumbscrews, you will need to put a washer between the thumbscrew and tailstock. If everything worked correctly you should be able to lock the threaded bar in position now.
Step 9: Spindle
Now install the ballbearing race into the headstock. They should be a snug fit, but if they are a little loose you can use a small amount of 5 minute epoxy to glue them in place. Just don't use to much glue or you'll gum up the bearings.
Insert some threaded bar through the bearings and use two lock nuts on each end to make sure they don't come undone. Don't forget to use a washer before putting the nuts on, the washer should only be big enough to contact the inner race of the bearing and not touch the outer race.
Now screw another two lock nuts onto the threaded bar. At this stage select a pulley and tap that with to an M10 as well, screw it on tightly and follow up with another two lock nuts.
Step 10: Assemble the Parts
You can now assemble all the parts, it should almost look like a lathe at this stage. Screw on an M10 chuck onto each of the threaded bars. On the tailstock use the chuck to hold the live centre, and on the headstock use the chuck to hold the drive centre.
Step 11: Mount the Lathe
Now to mount the lathe on a board or workbench. To do this I just screwed the headstock to the board from underneath. For the other end I quickly made up a block to hold the pipe down, it's a good idea to make the centre of this hole a couple of mm higher than the hole in the tailstock. This allows the tailstock to move freely without sticking to the base.
You can use whatever motor you choose, I've seen a lot that use a drill. I however wanted to use an angle grinder for a couple of reasons, it's a lot easier to mount and I can get much faster speeds. A couple of simple 'L' bracket are enough to bolt onto the grinder's handle mounts and then screw into place.
The small pulley was also taped out to M10 thread so screwed straight on, and I used an old o-ring for the belt.
I do recommend you get a grinder speed controller to slow the grinder down a bit, you really want it going slow while you first round out the wood. Once it's round and balanced you can speed it up again.
Step 12: Use Your New Lathe!
Now for the fun part, using it! Have some fun, be careful. Run it slow at the start, where ear and eye protection.
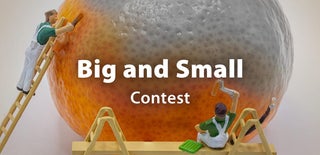
Second Prize in the
Big and Small Contest