Introduction: Nonagon Cabinet With Gecko Habitat
I wanted to design a habitat for my crested gecko as they like to vertical space and most available habitats aren't very tall, usually square shaped. I scavenged some melamine coated(like a countertop) MDF sign holders that held a plastic sign bent into a circle.(see images). The sign holder was 3 pieces of 9 sided MDF, 2 larger pieces had a 18" diameter ring routed into them and the other piece was a bit smaller, but still 9 sided.
The 2 larger pieces were used as the top and bottom of the habitat, with the routed ring holding clear plastic sheet with a door in it. Three threaded rods support the top. And the smaller piece was duplicated and they were used as the top and bottom of the cabinet. The cabinet is made of 2x2 and 1/4" hard board.
I used a lot of scavenged and re-purposed materials, but something like this could be built from scratch.
Didn't think I would do an Instructable for this at first, but I still had taken some pictures for my own records, so there may be some gaps or some pictures taken out of order.
Step 1: Materials and Tools
Most of the key parts of this were scavenged or re-purposed, so it won't be as easy to recreate, unless you have access to a ShopBot or other CNC rounting machine, but might give some inspiration for other designs.
Parts:
- Nonagon(9 sided) sign holder. See Pic.
- Plastic Strips for trim, 1" x 34" I used black, about 50mil thick, with a textured leather look on it.
- 3x 3ft lengths of 1/4" standard threaded rod to support the top
- ~24" 3/4" aluminum bar
- 12x 1/4" bolts, stainless
- 6x stainless end-cap bolts
- Decorative nails, round top, stainless
- Misc screws, bolts and nuts, all stainless
- Metal Mesh, got it at a craft store, was a bit expensive for what it is though.
- Epoxy, preferably with a mixing spout
- Plastic Sheeting, small piece 20" diameter
- 125mil polystyrene, length is the circumference of the grooves, painted black.
- 20mil clear plastic sheet, for the door frame approx 12" x 12"
- 20mil clear plastic sheet for the enclosure walls, I used 25" x 48", needed 56" but I used some extra to patch the difference.
- Bulb Sockets, I used 2 ceramic ones salvaged from an old light fixture, cut off from a string of 5
- 2x salvaged AC cords, polarized, but depends on setup
- Infra-red heater bulb, such as Exo-Terra Heat Glo
- Daylight spectrum fluorescent bulb
- Wood glue
- Aquarium Sealant
Tools:
- Jigsaw
- Scissors
- Metal Snips, Aviation or otherwise
- Hammer
- Drill and bits
- Table Saw
- Hack Saw
- Utility knife or sharp sturdy razor
- Vise
Step 2: Start With the Enclosure
Test fit plastic sheeting:
- Started by disassembling the sign to get at the 2 matching nonagon panels with a 18" diameter circle milled out of them.
- Scavenged a 27" x 48" 20mil thick, clear plastic PETE sheet.
- To test how it would work I slid the sheeting into the routed ring on one of the nonagon ends, and sandwiched the sheet with the other. Used some tape to hold it, so it formed a cylinder. The sheet was a bit to small, but it was easily patched.
- Measure how big you would like the opening for the door, my door will be 9"x12" so I want a 8"x11" opening. I chose to cut the door over the seam of the cylinder, as there was already a small gap and it makes the most sense.
- Measure and mark with a sharpie, take the sheet out, lay it flat and cut out the door with a razor.
Door:
- The door is made of the same clear plastic, some neodymium magnets and standard nylon window screen. Figured to make the door 9" x 12", enough room to get my hands into the enclosure to clean or what not.
- Out of the 50mil clear plastic, cut 2 matching rectangles, then cut out the inner recteangles leaving a 1" thick borders. These are the door frames.
- Place one of the frames down on a flat surface.
- Cut the window screen to overlap 1/2 way through the frame all the way around, position it on one of the plastic frames.
- The bottom and top of the door is reinforced with metal strapping, cut to length with a bit extra for the hinge.
- On one end of the metal strapping, is bent and hammered to fit around a finishing nail that will be used as a hinge pin later.
- Flat neodymium magnets were positioned strategically around the edge of the plastic frame.
- Position the metal strapping at the top and bottom
- Get a tube of epoxy, with the spiral mixing spout. Its way easier.
- Put a good sized bead right on top of the magnets, screen, metal strapping and plastic frame all around.
- Use the other plastic rectangle and sandwich the magents, screen and metal strapping between them.
- Place on a flat surface with something heavy ontop leave for hour or so.
Enclosure Supports:
- Take the 2 nonagon ends with the circle groove
- Align them and screw or clamp together. Mark the sides so they can be matched up, a piece of tape is good.
- In 3 evenly spaced corners, drill a 9/16" hole for 1/4" threaded rod. 9 sided works out well, as 3 points can be evenly spaced.
Step 3: Bottom Cabinet
Cabinet Frame:
- The nonagon sign I used had 2 larger nonagons and 1 smaller one. The smaller one is going to be used for the cabinet, except I need one for the top and one for the bottom of it. I placed the smaller nonagon on some 5/8" MDF, traced it, cut it out with a jigsaw.
- I then attached them together and sanded the edges till both were exactly the same. Take them apart.
- Cut 7 2x2s, I cut mine to 34", so the bottom of the habitat was about 37" high.
- Position and mark where the 2x2s will go, fit them in to the corners, see digram.
*Note if I would have had a router I would have tried to angle the corners of all the 2x2 so they fit better into the corners of the nonagons.
- Drill and countersink the holes, screw the 2x2s into the top and bottom MDF parts from the outside.
- Flip it over so the bottom is up and attach some 2x2's cut with 45 degree cuts on each end.
*Note: I had tried to get away with 4 supports instead of 7, but ended up adding 3 more later after I added horizontal supports. So the vertical and horizontal supports are sort of woven in with each other, but that is not necessary.
Cabinet Outer Walls:
- Carefully measure the sides of the nonagon, mine were approx 6.25"
- On a table saw ripped 6 pieces of 1/4" hardboard into 6.25" by 37" parts, these are for the sides
- Then cut 3 pieces of 1/4" hardboard into 6.25" x 34" parts, these are for the door.
- Ripped one of the 34" long pieces in half, so there are 2 3.125" x 34" pieces. These will be for where the door meets.
- Stacked the 7 matching pieces up and drilled 2 holes in the top and bottom, evenly spaced and 3/8" in from the ends.
- Paint all 10 of the pieces with a color of your choosing, I chose matte black. The smallest piece( 3.125" width) make sure to paint the edges as well, rest will have their edges hidden.
- Create a mask, I laid out a vector design in Adobe Illustrator and used it to cut mask using a vinyl cutter.
- I applied the mask to the all the hardboard pieces, did some edges with frog tape.
- The 2 smallest pieces were butted together and the mask applied, so half of the image is on each piece.
- Painted them with green gloss spray paint.
- Wait till dry and remove the mask.
- Attach to the frame, make sure to align them flush to the top.
Attachments
Step 4: Door and Molding
Cabinet Door:
- The cabinet door is hung using some piano hinges that I got surplus, they happened to be the exact size.
- The hinge is attached with nuts and bolts to one of the 6.25" x 37" hard boards and to one of the 6.25" x 34" hard boards.
- I used the top to trace the corner profile onto some MDF sheet and cut out top and bottom corners, see image.
- Positioned the corners and marked and drilled the holes for mounting the door pieces to the corners and the hinge.
- Finally added some 2x2 supports to the door so it was more rigid.
Molding:
The bottom needs some molding to cover up the bottom edges of the hardboard.
- First the sides where the door is need some hardboard strips nailed to the bottom of the sides because all the other sides have hardboard that hang down.
- Found some 3" wide molding at the hardware store, did some trial and error to find the exact right length.
- Carefully set the mitre box for 20 degrees, which is hard since it most snap in to 22.5 degree which is for octagons.
- Cut the molding.
- Align the trim flush with the floor and Nail in with finishing nails, sink them
- Apply latex wood filler to the nail holes and I also filled in some gaps between the molding as they were not perfect.
- Sand smooth and painted it matte black, like the sides.
Step 5: Trim and Hardware
Trim:
- Cut 9 pieces of 1" x 34" plastic, 50mil black with a textured look.
- Stacked them all up and drilled 1/16" holes with 4" spacing, alternating on each side.
- Used an make-shift acrylic bender and heated them up and bent them over the side of some plywood. The shape didn't hold completely but well enough.
- Positioned the now bent strips over a seam and used the holes I already drilled as guides for pilot holes into the hard board.
- Using round top decorative nails, I nailed them all in, 20 nails per strip
- Do all 9 corners
Hardware:
- The door handle, I found some cool aluminum ones at Home Depot, centered them to the painted pattern and screwed them in as per directions.
- And some magnetic door holders were installed.
Step 6: Top and Light
Top Prep:
- Started by cutting a 12" diameter hole out from the top. Used a plastic thing as a compass.
- Drilled a pilot hole and used a jigsaw to cut out the hole.
- Finish it up with some files and sandpaper.
- Rubbed 2 coats of wood glue into the exposed edge of MDF to make it stronger
Light Grating:
This grating will keep any critters from crawling out the top where the lights will shine in.
- Used the same plastic I used for the trim and cut out partial circles with a scissors.
- It took there pieces to make a whole circle. Need 2 identical rings.
- Carefully sized and trimmed them so they would butt together without any gaps.
- Cut the metal grating down so it overlaps half way through the rings.
- Place one ring down flat, center the grating on top of it
- With a tube of epoxy lay a good sized bead
- Use the other ring and sandwhich the grating between them, place under something flat and heavy to dry.
- Once its dry, it was tack nailed onto the top, centered over the hole that was cut in it.
Lights:
- Used a length of coat hanger to practice bending a support to hold the light bulbs.
- Once it was good, I bent a some 3/4" aluminum bar to the same shape.
- Salvaged some ceramic light bulb sockets and attached them with nuts and bolts to the aluminum bar.
- Attached some salvaged AC cords to the bulb sockets, each socket gets its own cord. Zip tied them to the aluminum bar.
- Centered it and screwed it in over the hole in the top. Made it parallel with the front of the cabinet.
- Not shown, but I wrapped the bulbs with tinfoil in a cone shape. to reflect the light down and not shine it out into the room.
With each on its own cord, it will be easy to control the day/night with a timer and the heater with a controller.
Step 7: Assembly and Inside
Now everything is built its just a matter of putting it all together
- While everything was in pieces, all the parts of the habitat were cleaned off with warm soapy water and rinsed.
- I put the habitat cylinder together, and measured how long the threaded rods needed to be, leave enough to put the end-cap bolts on.
- I measured and patched the small gap in the cylinder with some scrap plastic and some Methylene Chloride that fused it together.
- Cut the threaded rod down with a hacksaw lubricated with some WD-40, makes it a lot easier.
- Each end threaded rods has 4 bolts, 2 on the top and 2 on the bottom, they are tightend in on each other so they don't slip.
- Then on the outside there is the end-cap bolt, the top has washers.
- Last I used a piece of 3" wide x 55.5"(that's the circumference of the cylinder) of 125mil polystyrene, painted it black and fit it into the round groove with the clear plastic cylinder on the bottom, as the groove was wide for just the clear plastic and it covered up the bottom few inches of the habitat which will be filled with mulch.
- I had left the habitat not attached to the cabinet till now, I placed it on top, positioned it and screwed it in from inside the cabinet.
- I then attached the door, I bent some more metal strapping into small loops and hammered them to shape around the same size nail I used on the door.
- Marked, drilled and attached to the habitat cylinder with pop rivets, with the smooth side(top) inside the habitat.
- Attached the door using nails as hinge pins, they will be cut down at some point.
Inside:
- Before everything was together I used some aquarium sealant, sold at Home Depot, to fill in all the unused over screw holes in the top and bottom of the habitat.
- Cut a piece of plastic sheeting 20" in diameter, and washed it in a bucket of hot water and dish soap to get any oils or chemicals off it from manufacturing. Placed it in the bottom, it goes a 1" or so up the side.
- Placed river smoothed(large so they can't be swallowed) rocks on the bottom to hold the plastic down and covered with cypress mulch from the pet store, it said it was best for crested geckos.
- I landscaped it somewhat, definitely something that is going to get rearranged and alot more and added to it before I am satisfied.
So far there is a pachira aquatica, or Money Tree, in there as it was the cheapest tree looking plant there was, if it doesn't die and the habitat works out I plan on getting a different tree. Along with some more plants.
It gets misted a few times a day, but I hope to install a cool mist humidifier, maybe a small fountain with no standing water.
Placed a few rocks, but it needs more yet. Going to place some good sticks when they are easier to collect in the spring. And after watching the gecko, it seems he would like many more places to hide as it tries to get under the plastic sheeting during the day time.
Thanks for reading, please visit My Profile to see my other Instructables.
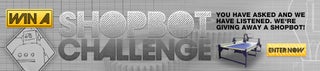
Participated in the
ShopBot Challenge
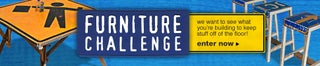
Participated in the
Furniture Challenge