Introduction: Saw Blade Custom Knife
Interested in making a custom knife without a forge or expensive, customized tools? It's easier than you think and almost everything you need is probably lying around your workshop! Before we begin, I suppose I should mention that I'm not willing to take responsibility for any way in which someone following this Instructable burns, cuts, abrades, maims, kills or otherwise injures themselves. I managed this without injury, if you can't... just keep it to yourself, okay?
Step 1: Materials:
Old saw blade
Scrap Wood
Brass Rod
Two Part Epoxy
Plastic Wrap (optional but, highly recommended)
Basic Glue (or mix water and flour and make your own!)
Paper
Sandpaper (sharpening stone and/or leather strop)
Step 2: Tools:
Rotary Tool with Cut-Off Wheel (or Hacksaw)
Bench Grinder (and/or Files)
Table-saw (or any tool for cutting the wood for the knife handle)
Clamps
Butane Torch
Kitchen Oven
Awl (or any pointy, metal object for marking and scratching)
Pencil/Pen
Container for water or oil big enough to completely submerge the knife
Step 3: Design Your Knife!
Now, the fun begins! I used Google Images to check out knife designs, looked through knives that I already own, and then tried to decide what I wanted in a knife (also, remember to consider the amount of metal you have to work with). For me, that meant a small knife that would be comfortable in my hand, provide lots of control, and be shaped to work well with a belt sheath (that might be the next Instructable?). Now, it's time to sketch out the blade and cut out the image to create a pattern.
Step 4: Glue, Wait, and Cut
Glue the pattern to the blade (I used regular wood glue but, any white glue or even water and flour will work) and wait a few hours while the glue dries. Once the pattern is glued to the blade, it's time to get out the rotary tool and cut-off wheel (or hacksaw, if you're a masochist) and cut out the pattern. Be sure to leave a bit of metal around the blade; it's better to take a little off with a file or grinder later than to take too much off with the cut-off wheel. Wear eye and respiratory protection, don't try to lick the cut-off wheel or the hot blade, and be kind to small animals.
Step 5: Grind or File Off Excess
This is the part where a grinder will save you a lot of time but, a file will also work. Take your time here to make sure that you get nice smooth edges all around your pattern. Pay special attention to make sure that you're happy with your pattern and hold the blade to see if there are any adjustments that you want to make (I moved my finger indents a little bit once I could feel the knife in my hand).
Step 6: Bevel the Blade
For this step, I chose to work with a basic, manual file because it's easier for me to keep a clean angle by hand than it is with the bench grinder and a smoother angle means a sharper blade. Clamping down the blade makes this process a lot easier. Make sure that the bevel width is even across the entire blade and that the angle isn't too steep (I shoot for around 22 degrees). Fair warning, this is probably the step where you're the most likely to cut yourself on your new blade. Draw the file away from the blade (not toward it) and you should be fine.
Step 7: Smooth and Shape
Next, I took a bit of time to hand file the outer edges (to remove any burs), rounded over the top of the blade, and used a rat-tailed file to add indentations for grip on the top of the handle area. If you can't stand filing and sanding, this project probably isn't for you. If that didn't deter you, it's on to the next step ;)
Step 8: Heat Treating
Make sure that you have a container of water (or oil) nearby that is large enough to completely submerge the blade. I used a glass mason jar full of water. Clamp down your blade by the handle and make sure nothing flammable is nearby (don't blame me if you set yourself on fire!). Hold your torch on the blade until it glows dully red (difficult to see but, you can kind of tell in one of the pictures). I didn't worry about the handle but, made sure the entire cutting blade was glowing. I couldn't take a picture while I did it but, I used a pair of pliers to move the blade from the clamp to the jar, remember, it's HOT!!! As soon as the entire blade is red, immediately dunk it in the water or oil and leave there until the blade cools (this only takes a few seconds for a small knife). Make sure to drink all of the quenching liquid- just kidding, absolutely do not do that (I'm told it tastes bad... and could probably kill you).
Step 9: Prep for Tool Hardening
After the first heat treatment, I took a bit of time (and elbow grease) to polish and sharpen the blade before I moved on to the final heat treatment. Remember when I warned you about sanding and polishing? Well, I did. You're the one who's still reading...
Step 10: Final Heat Treatment
Make sure no one will need the oven for around two hours (lunch and dinner times are not ideal for this step), set it to 400 degrees, and set the knife in there. Let the knife "cook" for an hour and then turn off the oven and let the knife cool (with the oven closed) for about another hour. At that point, the knife should be cool enough to touch (this is another one of those "not-my-fault-if-you-burn-yourself-steps). Congrats, you now have a tool hardened knife! Time for more polishing to remove discoloration from the heat, yay!!!
Step 11: Make Knife Scales (Handle)
Find some scrap wood that's larger than you want the handle to be and big enough to make two pieces (about 1/4" thick). Cut that sucker down (CAREFULLY, I don't even want to know if you manage to lose a finger). TIP: if you're using a table saw; a zero clearance plate is EXTREMELY helpful for this type of small work. You can see the one I made in the picture above and I can't recommend doing that enough.
Step 12: Scratch EVERYTHING and Prep the Clamps!
To give the epoxy enough grip to make sure you don't have a loose handle, rough up the metal and the wood anywhere that they will come into contact. I use a small awl and a cross hatch pattern. You'd probably be fine using a nail and drawing landscapes but, it's totally up to you, just give the epoxy plenty of surface area to adhere to. With that done, prep your clamp(s) by covering them in plastic wrap; the plastic won't stick to the epoxy and keeps your clamps clean (those suckers can be expensive and don't work as well if they're glued together!).
Step 13: Epoxy- Sticking It All Together
Two part epoxy is wonderful stuff and we could debate the merits of different setting times but, use what you want, I'll stick to (ha!) 5-minute clear because it's what I like and that gives me enough time to coat everything and set up. If you need more time, take more but, use longer setting epoxy. Gloves are recommended; at the very least avoid touching parts of your body together that you wouldn't want permanently connected and wash off any excess glue as soon as you can. Now, clamp the handle pieces to the blade and walk away until the epoxy has cured. Now, assuming you aren't stuck together in ways that require emergency medical treatment, it's time to remove excess handle material!
Step 14: Cut-Off Excess Handle Material
I like to use the band-saw for this part but, you could use any type of saw or even whittle or file the excess away (if you'd like to finish this project some time next week). Being careful, I can feel the difference between cutting the wood and rubbing up against the metal of the blade so, this is what works for me. Go slowly and, when in doubt, leave more material (it's a lot easier to remove than to add!) and see how it feels in your hand before moving on. Still have all your fingers and toes? Good! It's time for more sanding!!!
Step 15: Sand and Shape
This part is pretty self-explanatory, sand the handle so that it feels good in your hand. As with all sanding, start with a smaller (rougher) grit and work your way down. The more you sand, the smoother the handle will be. Stop from time to time to see how it feels in your hand and adjust as you see fit. If you need more explanation on sanding... there's probably an Instructable on that; I think I've done my part and I'm ready to add the pins.
Step 16: Drill Holes and Make Pins
Yes, you COULD use a hand crank drill; go for it. I used my drill press. Either way, make sure your drill bit is the same size as your brass rod and go SLOWLY. You'll feel really stupid if you try to go too fast, break your handle, and have to start all over again. Don't do that; go slowly. Cut the brass rod into two pieces just a little bit longer than they need to be to clear the handle, twist them into place, and then hammer them to flatten out the ends. Don't worry if they still stick out a bit, that's what sanding is for and it'll make the pins feel like part of the handle. Either way, sand the whole thing some more and then decide how to finish the handle. I stained it and then used polyurethane but, you do you.
Step 17: Finished Product!
After some finish sanding and sharpening (I used a stone and a leather strop) you have your finished knife! I hope you've enjoyed this little journey, finished yours unscathed, and ended up with a knife you can be proud of. This was my second attempt at this so, if you have any suggestions, found something ridiculous that I overlooked, or just want to share what you ended up with, I'd love to hear about it. If you'd like to complain that you followed my instructions and injured yourself; type up a formal email, print it out, read it out loud, and consider your work done; the same goes for complaints about sanding, polishing, and sharpening (You were WARNED!!!). Thanks!
Step 18: Bonus: the First Attempt!
Just for fun, and since I mentioned that this Instructable was my second attempt; I thought I'd share the results of my first attempt at making a saw blade knife. This one was a bit more ergonomic but, I'm not sure how I'll make a sheath for it and I didn't spend as much time making the blade look nice. Anyway, there it is.
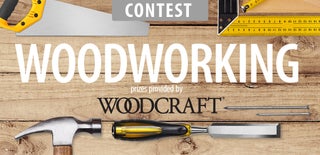
Participated in the
Woodworking Contest 2017