Introduction: Sound Reactive LED Halo Hat
Want to light up the night in style? Why not build a Sound-Reactive LED Halo Hat?
Total cost if you have no parts, is around $140 and 3-4 hours of labor with basic tools, very worth it!
At its core, it is a LED ribbon, attached to a wire ring with zip-ties, attached to a hat/baseball-cap. LED sound-control is by a SP107E (on Amazon) LED Controller which has an embedded microphone. Then just connect power to a 5v supply (USB Battery Pack), it fits in your pocket and is good to go!
Please see the photos on each step of the guide, they are very helpful in understanding how to complete each step.
Portable, wearable, practical, fun, and looks very cool! Enjoy!
Supplies
Tools
- Needlenose Pliers
- Regular Pliers
- Diagonal Cutters (Dikes)
- Wire-Strippers (or a knife/snap-off utility knife)
- Table Vic
- Hammer
- Soldering Iron
- Solder (preferably rosin-core)
- Lighter
Materials
- Baseball Hat/Cap - $15-20 - I'm using this one: https://www.amazon.com/dp/B00USMQ66W
- Stainless Steel Wire Coat Hangers - $10 for 15x - https://www.ebay.com/itm/184539660202
- 10" Gold Hoop Rings - $12x for 6x Variety Pack - https://www.amazon.com/dp/B081Q8G3CC/
- WS2812B 5 volt IP65 LED Ribbon, 144pixels/meter - $23 - https://www.amazon.com/gp/product/B01CDTEHRC
- 19 AWG Stainless Steel Wire - $8 - https://www.amazon.com/dp/B0039V6V8W
- SP107E LED Controller/Mic - $20 - https://www.amazon.com/dp/B07H28SWJX
- USB to Power/Barrel adapter - $8 - https://www.amazon.com/dp/B01MZ0FWSK
- JST SM (3 wire) Quick Connectors - $10 - https://www.amazon.com/dp/B00NBSH4CA
- Heat Shrink Tubing - $6-10 - https://www.amazon.com/dp/B072PCQ2LW
- 3-pin Wire - $7 - https://www.amazon.com/dp/B08JPLRXRK
- 4 inch cable ties - $4-8 - https://www.amazon.com/dp/B087MHY15J/
- Large-Eye Needles - $6 - https://www.amazon.com/dp/B07VXTSZZG/
- 6lb Fishing Line (Thread) - $7 - https://www.amazon.com/dp//B094FMR1NS
- 2-Part Epoxy Adhesive - $4 - https://www.amazon.com/dp/B0044F9KFI
Step 1: Coat Hanger Into Halo Holder
Cutting the Coat Hanger
The core structure of the hat is a steel clothes hanger that is cut and bent to wrap around the head, just above the ears, and the stem unbent into a straight line (compared to the "hanger" at the top) as a "halo-holder".
Measure the distance from the back of your head, to just past your ears. You can just roll a ruler from the center of the back of your head. For me, it was 7 inches.
Then mark with a sharpie, and cut the steel hanger with some pliers. It will take some force, a few tries, and most-likely rolling the pliers around the hanger back and forth to cut it, it is steel after all.
Forming the Frame
Once you've got the hanger cut, unbend the top so it is straight, and bend the sides so they wrap around your head with some slight clamping pressure.
Once complete, you'll want to use a table-vice to clamp the stem, and bend it forwards around a 90 degree angle. I found this easiest to have the stem going vertical through the vice, starting the bend with some big needle-nose pliers, then hitting it gently with a hammer repeatedly to make it flat.
Forming the "Hook"
Once it's fully 90-degrees, the hardest past of the build -- bending it backwards over itself, to be a "hook" for the halo. The only way I was able to do this was needle nose pliers and a lot of muscle. Thank goodness it's steel to take a beating and retain its shape.
Holding the Halo
Once you've got the hook formed, carefully insert your aluminum (gold painted) halo ring into the hook, and *GENTLY* smash the hook around the halo. Don't keep pounding with a ton of force, you can damage the halo or break through it. Just enough to get it reasonably gripped by the steel hook.
Step 2: Steel Wire and Two-Part Epoxy
The halo by itself, is loosely secured by the hook. We need to make this connection impossible to separate.
Enter: Steel Wire and Epoxy.
Steel Wire
Snip off about a 6 inch piece of 19AWG steel wire.
The steel wire is threaded with needle-nose pliers through the gap between the halo and the hook, then wraps around both. Meet up the wire ends, and twist them with medium force. Tightening/twisting this steel wire will make the connection between the halo and hook much stronger. Once you cut the tails, you'll only have used about 1.5 inches of steel wire.
Two-Party Epoxy
If you've never worked with two-part epoxy before, know two things:
1. It is very strong when cured.
2. It is mixed in equal parts then stirred together in a container you will throw away.
3. It is very messy.
I personally use the plastic packaging the epoxy comes in, to pour in a small (about a large spoonful) amount of epoxy, stir it with a wooden stick thoroughly. Mix it well, but it will begin drying within 2-3 minutes of mixing.
Once it's mixed, quickly and carefully drip the epoxy onto the joint where the steel wire, halo, and hook all meet. Try to cover every surface at the joint in epoxy, but keep it small and clean, like a little ball of epoxy with the core of the ball at the joint.
Wait For Curing
Through epoxy will dry 5-10 minutes, and be touchable in about 30 minutes to 4 hours. We need it fully cured before we can move forward. As long as its over 60F, just leave it in a stable position, and don't touch it for 16-24 hours.
You'll know its cured, when if you touch the dried epoxy with your fingernail, it is rock-hard.
Step 3: Wiring and Testing LEDs
The wiring is pretty simple. Everything should be running on 5 volts, as that is what a USB Battery Pack puts out.
If you use say, a 12v power supply on a 5v strip, you will instantly burn it out. 5v, all the way. The SP107E controller will take a large range of voltages, and pass on whatever it gets, 5v or 12v.
Connection Path
USB Battery Pack > USB to Red (+) / Black (-) Wires > SP107E Controller > 3-pin extension cable > LED Ribbon Connector > LED Ribbon.
Though that looks like a lot of steps, it's really not that back once you get into it.
USB Power Cable
Take the USB to Power Cable, and just cut off the end. Inside will be four wires, Green, White, Red, and Black. We only want the red and black (power and ground respectively). Strip the wires short, maybe 1/2 inch, and drop a blob of solder onto the end if you want a stronger connection (something bigger for the "springs" to grip onto).
The SP107E has two input wires, red and black, just match em up, and tighten down the springs via the small flat-head screws underneath.
Outputs
From the SP107E Controller, there are four outputs. Power (Red), Data (Green), Clock (Blue), and Ground (Black). For our case, using a WS2812B strip, we only need three: Power, Data, and Ground. Our goal is to make an extended 3-pin wire, solder some quick connectors on the end, secure with heat-shrink tubing, then just connect the pieces together.
3-Pin Extension Cable
This is the cable that will go from the SP107 Controller in my pocket, up my back (in-between undershirt and outer layer), out my collar, up the stem, and connect to the LEDs.
Your 3-pin cable may not match in colors to the quick disconnects or the LED ribbon. Usually the color that differs is the ground, which may be white, black, or blue. Recommend just matching up Red to Red, Green to Green, and the third is whatever is available.
Strip the ends of the wires, "tin" them with a blob of solder, slide on a piece of heat-shrink tubing before you solder your joint, solder the join, slide the tubing over the joint, wave a flame back and forth underneath the tubing to shrink/secure it. Rotate as needed.
Use the Male or Female Quick Disconnects as needed to get power to your LED strip.
Testing the LEDs
You will need a smartphone. Download the app, "LED Chord", by scanning the QR code on the SP107E Controller. Enable Bluetooth, connect power, and open the app. You'll be prompted to select your device.
For WS2812B strips, use: WS2811 format, GRB Color arrangement, 4 segments of 36 pixels.
For testing, I just use static pattern #1 (Rainbow Repeating). In-concert can use sound-reactive later.
Step 4: Mounting the LED Ribbon to the Halo
This is a pretty easy step.
Put the LED Ribbon around the halo ring, and cut along the line of the three copper terminals of the LED ribbon with some scissors, you're just trying to get the right length of LED ribbon. One end will come pre-soldered, it's a very strong, heat-shrinked connection, so try to use the pre-soldered connection if you can.
There is an adhesive backing on the LED ribbon. I found it helpful to use a tiny cable tie, to attach the lead wire from the LED strip to the stem, pull the adhesive tape/cover, and stick the LED ribbon to the halo. Then, just apply 6-8 cable ties to hold it in place (see photos).
You should be able to test your connections at this point, hopefully it will light up!
Step 5: Mounting the Frame to the Hat
There are ways to make the frame mount by itself, e.g. wrapping over your ears, combined with an additional neck support brace under the back, and using "clamping force". Personally... I wanted something easy, comfortable, and practical, so I decided to take the simple route and attach the frame to a hat for stability.
If desired, you can put heat-shrink tubing over the ends for grip/friction, to keep the frame a little more stable. Not sure if it's necessary, but can't hurt.
I purchased a Pokemon hat, any hat will do though. We are going to "sew" the frame to the hat using a needle and fishing line. It doesn't have to be perfect, it doesn't even have to be pretty, it just has to be excessive enough that the frame won't go anywhere.
Please see the photos for reference. I just loop over on the outside, under on the inside, and make knots randomly tightening the line on both sides. Takes some force, needle-nose pliers help.
You can get an idea of where the frame will go, inside a little "pocket" between the outer hat and inner rim. I used some diagonal cutters/dikes to cut a slit in the fabric to allow the frame to go through.
Step 6: You're Done! Woohoo!
At this point, use the Smartphone App LED Chord to configure your LEDs as desired via Bluetooth.
For reference again, the settings for a WS2812B strip are:
WS2811, GRB, and enough pixels as there are LEDs.
If you liked this Instructable, have any constructive input, questions, ideas, or want to share your work, feel free to leave a message, photos are very welcome.
Go have some grand adventures and light up the night!
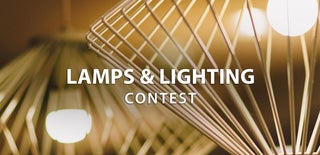
Participated in the
Lamps and Lighting Contest