Introduction: Space Shuttle Copper Pin
The Space Shuttle Program (officially Space Transportation System or STS for short) was the most iconic program in the history of space exploration, aeronautic and astronautic operations, with a long life period from 1981 to 2011, five units built and a total of 135 missions, the space shuttle was an awesome technical achievement in many ways, enabling multiple experiments and providing cooperation in many important projects such as the launch of the space telescope Hubble, and the support in the construction of the International Space Station.
This instructable shows how to make a copper pin based on a simple model of our favorite hypersonic spaceplane using scrap and reused materials.
Let's get strarted :)
Step 1: Materials and Tools Required.
Materials (See step ''Gathering materials'' below for more info)
3 to 5 Inches of old 1''OD copper pipe.
3 To 5 Inches of copper sheet 0.3mm thick out of a water heater radiator.
2 inches of 3mm flexible copper pipe from an old water heater.
25-30 M8 zinc washers (you can use zinc coins such as the USD pennies if isn't illegal melting coins where you live)
A polystyrene foam food tray.
A piece of 3/4'' scrap wood.
A safety pin (reused is better :D)
Tools
Power Tools
Dremel Tool with multiple accessories (mostly: Cutting disks, wirebrush bit, sandpaper disks, sandpaper drums, carving bit, polishing bits)
Drill, small drill bits and some machine oil to lubricate bits.
Manual Tools
Ballpeen Hammer
Small anvil (I used a sledgehammer head as anvil)
Metal shears
Hacksaw
Pliers
Needlenose pliers
Multitool with needlenose pliers
Round nose pliers
Round and flat fine grit metal files
Sandpaper, fine and rough grits
A section of printer rod to use as a blunt chisel
Propane torch, lead-free solder and soldering flux
Phillips and flathead screwdrivers
Adjustable wrench
A big spoon or a metal crucible
A small spoon
Measuring tools
Vernier caliper
Ruler
Adhesives
Glue stick
Masking Tape
Electrical Tape
Office supplies
X-Acto Knife
Cutter
Permanent Marker
2 binder clips
An old stainless steel ruler
Magnifying glass
Sewing pins
Paint
Nail polish
Spray paint any color
Spray clear laquer
Security gear
Safety glasses (use always, avoid accidents!)
Dust/surgical mask (for dust when cutting, sanding and painting)
Leather gloves
First aid kit (Just in case :))
Others
Printed space shuttle template (see step below)
Sand or a similar powder material such as plaster or concrete
An empty can
Shop towels or old rags
Cellphone charger with alligator clips or any type of DC power source
A pickle jar
Water
Salt
Pepper and your best hot sauce (actually not, I'm just kidding :D)
Step 2: Gathering Materials
In this instructables all the materials were obtained basically from a copper radiator out an old water heater, an old 1'' copper section, some zinc washers and a piece of scrap wood.
First, the old piece of junk that was the water heater was disassembled with the aid of an adjustable wrench and screwdrivers. From this we obtained many cool things to work in this and other future projects, brass nozzles, aluminum parts, and finally copper parts such as the radiator, that is made mostly out of copper with a tin coating to prevent environment corrosion.
From the radiator there was obtained copper sheet (about 0.3mm thick) sections (using a dremel tool with a cutting disk and a pair of metal shears), and 3/8'' copper pipe sections (using a pipe cutter), from the pilot flame mechanism, there was obtained a long section of tiny flexible copper line (about 3mm OD), these materials were used in further steps below.
Also there was used 1''OD copper pipe that formerly was a part of the plumbing of my house, in this project there was used a section of 5'' long, cut with a pair of metal sears and flattened into a flat plate with an anvil and a ballpeen hammer.
As a part of the building process of the pin fuselage, it was used a zinc mold, it was made of melted zinc washers, it were melted about 30 M8 washers that were remains of an attempt to make a 3d printer, if you are not sure if a washer is pure zinc, you can try to melt it with a propane torch, zinc melting temperature is reasonably low (419.53 °C, 787.15 °F), or you can use other things out of zinc such certain types of coins (Not shown in images, actually I used coins instead of washers, but I don't want to break any rule or law regarding melting coins, so it's up to you if you want to use coins).
In order to make the fuselage mold it also was used a polystyrene foam food tray such as the ones used to sell poultry and meat in the supermarkets and a piece of scrap wood.
Easy :)
Step 3: Space Shuttle Pin Design
First it was made a research of images, schematics and illustrations regarding the orbiter vehicle, both NASA's and Buran shuttles to identify the basic shapes and characteristic features of the vehicle's structure.
Then it was made a rough sketch on a CAD program to finally make a template with 1:1 scale ready to print and use as a reference all along the building process.
The pin design consist basically in a base that is the shuttle's delta wing made of copper sheet from the 1'' pipe, a preformed long fuselage from the thinner copper sheet, a vertical stabilizer fin from the same sheet as the wing, and an engine bay made of copper sheet with sections of small copper line, all the pieces soldered and fixed to a safety pin at the bottom.
The .pdf file of the template is attached to this step:
Attachments
Step 4: Making the Wing Base, Vertical Fin and Back Engine Plate
Three components were made out the same copper sheet that was made of a 1'' copper pipe as shown in the last step, those tree components are, the delta wing, the vertical fin and the plate located at the end of the shuttle holding the engine nozzles.
First, from the template printed sheet was trimmed each section and glued to the copper sheet using a glue stick.
Then the copper plate was sprayed with paint and when the paint was cured, the paper sections were removed from the plate with tweezers to discover sections were the paint couldn't reach the copper surface holding the shape of each paper section.
Each marked sections were carefully trimmed with a pair of metal shears and then straightened up with the ballpeen hammer and an anvil.
Finally each part was sanded and brushed with the dremel tool to remove all the tooling marks made in the process.
Step 5: Fuselage Mold 1: Foam Casting Mold
Making the fuselage mold to give the final shape to the copper sheet was a long and complicated task, it consists in the 3d form of the fuselage made out of metal, in this case was zinc, and the negative of the same 3d form carved in a piece of scrap wood.
For the casting mold part was used a casting method known as ''Lost-Foam Casting'' consisting in shape molten metal using 3d models of foam buried in fine sand, the process itself is quite interesting and relatively easy to make if it's done right.
The first thing done was making the final 3d form of the mold out of polystyrene foam, using the trimmed longitudinal cross-section of the template transferred to a polystyrene foam tray fixing the paper section with sewing pins. Then the transferred section was trimmed again in foam using an X-acto knife. This part was repeated three times to obtain three equal sections of foam.
Then all the sections were glued together with a glue stick, once the glue was dry, the rough 3d shape was sanded to the original dimensions using the template as a reference. In the back section of the 3d shape was added some small pieces of foam to give more volume to the widest point of the 3d shape.
In the Lost-Foam Casting process it is necessary to add an extra section of foam called ''riser'', that is the part where the casting begins, and it consist of a rectangle of foam glued to a specific location of the 3d shape enabling the molten metal to transfer the foam shape. You can calculate the dimensions of the raiser based on variables such as the size of the desired 3d shape volume, the density of the molten metal and some fluid static considerations. In this case considering that is not a great volume of metal, and we were minded to make the same process many times if it would fail the attempt :D, the riser was made of two rectangular sections of foam of about 1.5 inches long.
Once we had the 3d form ready to cast, the 3d form was buried in concrete content in a used metal can (usually the process involves sand, but didn't found enough fine sand), it was buried in a way that the riser ''rises'' from the sand to the surface, then it was molded a shape of a cone or funnel around the foam riser with the ''sand'', you can use water to modify the sand consistency and make easier the cone molding.
Finally, using a big spoon or a metal crucible, melt the zinc washers/coins with a propane torch. Once the metal is fluid, pour the molten metal to the sand funnel just in top of the foam riser in order to melt alll the foam component and replace the foam form with a zinc form.
Please use common sense regarding high temperature molten metals, wear at least thick leather gloves and safety glasses, please do not burn yourself!!
The poured metal was left a couple of minutes to completely cool down and then was removed from the sand with pliers to reveal the metal casting 3d form. The raiser was removed with the dremel tool and the form was sanded.
The final form was not perfect, sloppy though, but it was a good beginning as metal forming mold, it could be worse :).
Step 6: Fuselage Mold 2: Wood Carved Mold
Similar to the step where explains how to transfer the trimmed shape fixing it with glue and painting with a spray can, the wooden negative mold for the shuttle's fuselage form is transferred in the same way, once the shape is painted, the boundaries were outlined using a craft knife.
Then, using the dremel tool with a carving bit the material was removed using the template dimensions as a reference in order to make the negative part of the mold.
The progress in carving was constantly assessed using a vernier caliper until the negative mold was able to house the metal casting mold.
There were made two molds, the first one was heavily deformed in the first attempt to mold a copper sheet, the second one was used to shape the copper sheet of the final fuselage shape.
Step 7: Making the Fuselage
Once the forming molds were made, the fuselage was formed using a section of thin copper sheet.
First, the tin coating from the copper sheet was removed by sanding, then was located between the wood mold and the metal casting mold. Later using the ballpeen hammer and a blunt chisel the metal mold was pushed and started to form the copper fuselage form. Take it easy because in this part you can shred and heavily deform the copper sheet as shown in the back part of the fuselage form :/.
Once the copper sheet was formed, the sides were trimmed and there was left a small tab in each side of the fuselage to fix this part to the delta wing part. Then the delta wing part was drilled to receive the fuselage fixing tabs, also at this point there were drilled the holes to insert the safety pin, each hole was started with a drill bit, and then enlarged using a file or dremel cutting bit.
Step 8: Etching Parts
Some details of the pin were made using the electrolytic etching method on copper, basically is a chemical circuit in winch there is a power source (the cellphone charger) with two electrodes, in the the positive side, it is connected the part to etch (the copper part), at the negative side is connected a piece of stainless steel (an old metal ruler), between both electrodes there is a 10% salt brine. The circuit and the electrolytic fluid make an eletrochemical reaction that dissolves the copper of the plate and transfer the copper particles to the negative electrode, so if you isolate some areas of the copper side, the etching would be stronger in some uncovered spots and none in isolated zones.
In order to isolate areas to etch, there was used nail polish an electrical tape, first using masking tape stripes in the copper surface outlining the design comparing the one of the template, then when all the etching intended details are marked with masking tape, a coat of nail polish was applied to all the remain surfaces. Once the nail polish is fully cured,all the masking tape sections were removed with tweezers and an X-acto knife. Then using electrical tape a piece of scrap copper was fixed to the etching part to connect the alligator clip of the positive electrode.
The etching depth, depends on how much time the circuit is on, for both wing and vertical fin, the etching time was about 2 hours and was too much fine, for the fuselage, the etching time was about 3.5 hours and some spots of the part were totally dissolved making tiny holes in the surface, those defects were corrected later on soldering a small section of copper sheet below the damaged surface.
Once all the pieces were etched, they were cleaned and brushed with the dremel tool.
Step 9: Making the Engine's Back Nozzles
The shuttle's back has five nozzles distributed in a pattern that was drilled in the previously trimmed copper back piece, then there were soldered five sections of small (about 3mm OD) copper pipe about 0.5'' long all of them. Each section of copper pipe was tapered using a nail, a pair of roundnose pliers and a ballpeen hammer to give a look of a divergent nozzle.
Step 10: Soldering 101: Putting Everything Together
The first thing soldered was the wing base to the safety pin, it were used a pair of binder clips to hold in position the piece when soldering. Later the fuselage was assembled to the wing base bending the trimmed tabs, then soldering them. At this point I realized that soldering the safety pin wasn't the best idea, because with the heat of the propane torch, the safety pin steel annealed and became too fragile to use, so the pin was removed.
Then, the vertical fin and the back nozzles were soldered in an awkward position, it was hard this part because the vertical fin moved and it wasn't squared with the base wing most times.
Just use a lot of soldering flux, fix the pieces to solder, be calm and be safe. (don't burn yourself for short :))
Finally, when all the pieces were soldered all the soldering residues were cleaned with the dremel wirebrush.
Step 11: Final Details
All the soldering residues were removed with the wirebrush, all the surfaces were polished using the dremel tool. Then a clear lacquer coat was applied to all the surfaces.
Finally, a new safety pin was located using needlenose pliers and roundnose pliers, bending the end of the pin. The holes were modified with a round file to fit the new size of the safety pin.
Now you can call it ''pin'' to that piece of metal. :D
Step 12: Final Thoughts
Although it was a little bit sloppy, I'm happy with the final result of the pin, it was a fun project to work with and is a great reminder of a great invention of the mankind.
I'm considering to paint the pin in black and white to resemble the original colors of the real model, Ill will update any changes if there are any.
The making of the fuselage mold was difficult, but from the beginning I was considering to make more than one pins in the future, so the fuselage mold was the best idea that I come up, and at the end I think it will still work in the future.
If you have any question or comment please leave a message.
Thanks for reading and see ya later space cowboys!!
Andyfuentes22 2016
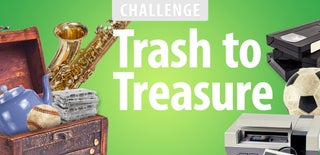
Participated in the
Trash to Treasure Challenge
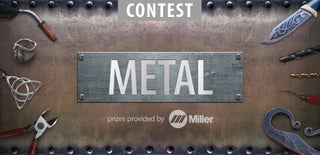
Participated in the
Metal Contest 2016
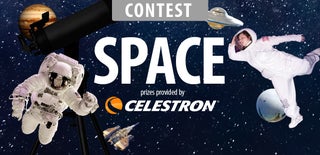
Participated in the
Space Contest 2016