Introduction: Toy Story 2 the Cleaner's Tool Chest
One of my favorite scenes in Toy Story 2 is the Woody's cleaning process, in which is depicted an awesome toolchest, with endless drawers and hidden compartments, I love the way that Woody is repaired and cleaned. This instructable (my very first one indeed) shows all the challenging steps of making my own versión of the famous Geri's (AKA "The cleaner") toolchest.
Al McWiggin:"So, uh, how long is this gonna take?"
Geri the Cleaner: "You can't rush art."
Lets get done :)
Recent Updates:
04/18/16 Grammar corrections
10/13/16 Minor text edition changes and grammar corrections
Step 1: Materials and Tools Required
Bill of materials
Wood
1/4'' Plywood 1 sheet 8'×4'
1--- Sheet of 3/8'' thick plywood 8'×4' (in this project was used red plywood)
2--- Strips of wood square moulding 8' long
Scrap wood (I used several woodsticks, some wood blocks of 1/2''x3/8''x2'', and a couple of wood strips to use as cutting guides/drilling jigs and to make sanding blocks)
Fasteners
120---M3x20mm screws (I cut some of them to length in order to fit in specific cases)
120---M3 nuts
120---M3 washers
50---3/16''x1 1/2'' flat head screws (I cut some of them to length in order to fit in specific cases)
50---3/16'' nuts
1---10-32 unc x 3.5' screw
2---10-32 unc nuts
20---10-32 unc washers
40---10 mm long binding post screws (found them in office supply stores)
4---3'' long M8 threaded rod and enough M8 nuts and washers. (Used in drawer construction jig, see Step 5)
6---3/8'' long wood screws.
Hardware
1---3' Long 1" OD copper pipe
2---Strap hinge leaf wide 3'', height 1.5'' (used only 1, the other was used as a jig to drill holes into the drawers)
2---Small hinges 1'' long wide 2''
2---Semi concealed cabinet hinges
7---Small drawer knobs with proper screws
2---Small draw latches
Adhesive
Wood glue
Painters tape or masking tape
Epoxy glue
CA glue (krazy glue, super glue, etc... used to lock nuts and screws)
Paint
Half liter of cherry wood stain
1 can of clear lacquer spray paint
A small brush
A fabric rag
Tools
Handtools
Ball peen hammer
Rubber mallet
Hacksaw
Metal shears
Fine grit file
Pliers
Needlenose pliers
Multitool
Small anvil ( I used a sledgehammer head as anvil)
2---C-clamps 2''
Craft knife
Tweezers
Sandpaper sheets (both wood and metal, multiple grits, rough, medium, fine)
Manual stapler (and staples duh..)
Workbench/worktable
Machine oil (used to cool down drillbits when cutting metal)
Powertools
Jigsaw with fine cut blade
Cordless drill and multiple drillbits (1/4'' maximum) and a 20mm forstner bit or a flat drill bit of same diameter
Dremel tool with cutting guide, a cutting bit, a wirebrush bit and a cuting disk (all accesories included in dremel 4000 bundle)
Circular saw with fine cut blade
Vacuum cleaner (To clean the constant mess of sawdust)
A flashlight (for tight spaces)
Measure instruments
12'' Ruler
Square ruler
T-shape ruler
Measuring tape
Vernier caliper
Office supplies
Pencil
Eraser
Sharpener
Permanent marker
Millimetric paper
Safety Gear
Safety glasses (use always, safety first)
Dust/surgical mask (for sawdust when cutting, sanding and painting)
Earplugs ( when using powertools)
Disposable gloves ( for the painting part)
First Aid Kit (Just in case, please be safe)
For the copper etching part
Power supply ( I used an old cellphone charger with aligator clips on each terminal)
A pickle jar
Clothes iron
Rubbing alcohol
Steel wire
1 cup of water
Salt
Magazine paper sheets
Electrical tape
Nail polish
Craft knife
Laser printer
Text editor
Step 2: Toolchest Design
First of all I started watching the movie and stop at the scene to analyze the posible dimensions of the whole thing, then make a list of the possible and (painfully :( ) the impossible features to aply in the box's design such as the side compartments, specially the one with the aerograph compresor ( I sincerely don't have idea how there's enough space due the front drawer .-.) and the chair compartment that flips the whole worktable that is so cool that you don´t stop to think the complicated mechanism behind the table unless you dare to build the same box.
Then I made a rough draft of my final design with all the features intended to make to decide which materials use in the final build, I based my "sizing analysis" based in objects shown all arround the scene, the hands of Geri, the size of the tools, etc so, the dimensions in this project can be scaled up for conveinence if my proposed dimensions doesn't convince you.
The final design consists in a 7 drawer cabinet base (6 small drawers, 1 large drawer), 8 folding cantilever-style drawers (4 both left and right sides) and a mini working table that can be removed to access a large compartment in the cabinet base over the lower drawers.
Step 3: Cutting 101: Drawer Cabinet Panels.
I started my long and not-too-straight-as-I-would-wish journey of cutting the basic panels for the cabinet with the jigsaw, first measuring and drawing the section shapes on the plywood sheet, then I used painters tape to outline the cut and prevent chip out.
For the side panels a 20mm flat bit it was used to make the extraction half hole for the worktable, then it was used a Dremel tool with a cutting guide and a cutting bit to make dados to fit the drawers bases, it was done with a guide (a ruler clamped to the wood sheet, "guide? yeah, right ¬¬" you may say ) to make the cuts as straight as possible.
The dremel tool in that configuration is very loud when cutting wood, I highly recomend wearing earplugs specially at this point of the build. Also you can use a router to do the same thing and possibly with straighter and cleaner results.
For the front panel was outlined with pencil the drawers locations, then I made holes for each corner of the drawer space to allow the jigsaw blade start a cut through the wood, once all the drawers holes were made, all edges were smoothed with a file and a sanding block using a straight surface as a guide.
Since my jigsaw is not quite accurate (is as accurate as a carnival rifle :( ) the sanding process is key to ensure the proper further assembly.
Step 4: Drawer Cabinet Construction
The drawer cabinet structure is based in the wood panels secured on each corner with 1'' wood square moulding strips that were bonded with wood glue, M3 screws (with a separation of about 2 1/2'') and wood screws for the front panel.
Due the drawers hole location in the front panel, the corner strip was modified drilling and cutting the excess material to ensure the drawer clearance. Those custom strips were fixed with 3/8'' wood screws.
Both side panels were bonded to the front panel and then the drawer bases were installed each in every dado slot and secured with wood glue.
Each drawer base was trimmed in each corner to fit correctly due the square moulding corner location, then wood sticks were bonded to each base to act as a drawer sliding constraint to avoid drawer mislocations.
Finally the back panel was installed and secured with M3 screws nuts and washers, this was difficult because there was not enough room to put a nut by hand in such a reduced space, I installed it holding the nut with a pair of tweezers by many, many trials and errors. :/
Step 5: Lower Drawer Construction
In this project all drawers are made of 1/4'' plywood, and all begins drawing every piece directly on the plywood sheet (many, many pieces so you better have your pencil sharpened), then I cut every single section with my deviated friend, the friendly and noisy ''jiggy'' jigsaw :), later I clamped all the same sections and sanded to make them sorta of straight ':(, then when all was straight and nice, every section was trimmed to make the ''jigsaw'' style box (like a straight dovetail box, but ) construction.
Once every section was trimmed the next step is build the drawers, to make this possible, I made a press/jig with some sections of scrap wood (a pair of coffee table legs from an old project) and M8 threaded rods that were recycled from an attempt of building a 3d printer :(, it consisted in two wood strips with two 8mm holes on each end at the same level, I fixed one of the scrap wood strips to the table with screws and the other one run freely as each nut travels trough the threaded rod so it was used as a large clamp to ensure the drawers were straight.
All the drawers were bonded with glue and reinforced in the corners with square moulding corner sections.
Once the glue fully cured, each drawer was sanded and fit tested in the drawer cabinet, and when every drawer successfully fit in the drawer hole, the drawer front plate was installed (Every drawer front plate was sanded at an angle to make an elegant chamfer :) ), every knob hole was drilled to finally fix the front plate with glue and the knob with a screw.
Step 6: Cantilever Drawer Construction
This step is pretty much the same as the lower drawer construction, with the difference that now the sections were cut with a circular saw that I recently get used from a pawn shop, it was faster to cut every section of wood :) but due the higher velocity of the cutting disk, the saw burned a little the section edges and at the end of the day all my clothes smell like smoked ham. :(
Once all the pieces were cut, I used again the custom press/jig to help the construction, every drawer base was secured with glue and staples using a manual stapler and each corner was secured with corner moulding sections and later reinforced with M3 screws, nuts and washers.
The holes for the M3 screws were made with the help of a drilling jig that consist in a piece of wood that was measured and drilled by convenience to locate quickly the hole location in the drawer side.
Step 7: Paint
All the wood pieces of this project were painted, applying first the wood stain with a brush and rubbing the excess dye with a rag. At first when the wood was stained it was very dark and dull, then I was preoccupied because it was not looking good, but once the first coating of lacque was applied, the color came up and turn into a bright and elegant rosewood vintage tone.
In this step I highly recommend to use a dustmask, disposable gloves and expendable clothing.
Step 8: Custom Hardware: Custom Hinge
The cantilever pivoting drawer mechanism design involves a hinge that is fixed to the main frame. The hinge that I made consist in a strap hinge that was broke down apart removing the central pin with a file and pushing out the pin with a ballpeen hammer.
Then, I measured the original pin diameter and search for a long screw that fits the hinge. After hours in the hardware store looking for the right diameter, I found some brass 10-32 unc screws that may fit in the hinge with some wacks of the ballpeen hammer.
To fit the screw into the hinge, I sacrificed one of the screws making a bigger hole to fit a new same diameter screw, once the new screw/pin is located between the hinge sides, I secured the end with a 10-32 nut and several washers.
In the custom hinge installation more washers were added to raise the level of the pivoting drawers, you can see that in Step 11.
Step 9: Custom Hardware: Copper Cantilever Links and Box Corners
Some of the custom hardware of this project is made of copper pipe, it was cut a section of copper, then cut in half longitudinally with a pair of metal shears and then flattened in an anvil with a ballpeen hammer, is a fun process because the result is awesome with unique pieces of hardware.
For the cantilever links were used 3 sections of copper pipe of 7'' long from which we get 6 flat plates, from each plate we can get 2 long links, or 4 small links, from the design we need 8 long links and 8 small links.
Once we get the 6 flat plates, the basic shape of the link design was drawn on the copper and then each section was cut with the metal shears, then the necessary holes were drilled to finally round edges with a file and polished with a wirebrush dremel bit.
For the box corners it takes 4 sections of copper pipe of 3'' long with the difference that this time the copper is not splited in half, besides there is just one longitudinal cut to get a single copper flat plate which from you can get 2 corners per plate.
Draw the rough design pattern in the copper plate that is a basic triangle form, then cut it with the metal shears, once you have the flat shape, bend it using a flat hard surface, for example I used a file clamped to the shape and a ballpeen hammer to achieve the bend.
Bend both side and round any sharp edge with a file and a wirebrush.
Step 10: Custom Hardware: Copper Name Plate
This is a brief explanation of how electrolytic etching works, if you want to try it, there are several instructables that explains better than me how to secure and successfully do it.
For more info about electrolytic etching: https://en.wikipedia.org/wiki/Electroetching
As a personal touch, the toolchest design includes a name plate with my nickname etched on it, it was made with a leftover copper sheet and started using a PC text editor and making a design in negative and mirror text, then the design was printed in magazine paper (it must be a toner printer), next the design was trimmed and transfered with heat (using a clothes iron) for about half an hour, after cooling the copper plate, the paper is removed washing the plate revealing the transfered toner.
If the design after the washing is not perfect, you can ''correct'' the missing toner spots with a permanent marker, nail polish and pieces of electrical tape, the idea is that the spots that are not protected whether with toner or any means will be corroded with the etching agent.
Once you have you corrected design, cover all the discovered copper areas (except the ones that you want to etch) with electrical tape leaving a copper section or a cable connected to the plate.
Fill a pickle jar with water at 90% of the jar capacity then add about 10% of salt and mix the solution, submerge you copper sheet in the brine (only the insulated and design areas, it must be out of the water the copper section that acts as a terminal) and submerge a steel wire in the other side of the jar.
Then use a direct voltage source and plug the negative terminal first to the steel wire, and the positive wire to the copper side, I used a 5 volts cellphone charger to do it.
Leave the electrolytic cell plugged for a couple of hours (5 hours in my case) and when you consider the etching is deep enough open the circuit and get the copper plate.
Wash and sand any toner or nail polish leftovers and polish with a wirebrush.
Step 11: Cantilever Drawers Installation
First there was drilled the holes in order to install the binding post screws, it was used a drilling hole locating jig to make the job much easier.
Next, the custom hinge was installed, in order to fix the hinge to the main box frame it was made a mounting block made of scrap drilled wood blocks secured with 3/16''x1 1/2'' screws and nuts, there were added washers to the custom hinge bolt to raise the level and avoid collisions with the frame and the pivoting drawers.
Once the custom hinge was installed, there were drilled the hinge holes to fix the strap hinge to the cantilever drawers. Then, the cantilever links were installed (by levels, first the links of the lower drawers, next the second ones, so on and so forth... ) using binding screws that act all along as a rivets and pins to allow the mechanism run free, all screws were secured with CA glue in order to avoid loose links.
Finally there were installed a couple of double-nut screws to lock the cantilever mechanism travel in order to make a more comfortable access to the contents of the drawers.
Step 12: Folding Cover Installation
The folding cover consist mainly in two parts: the back panel that is fixed with cabinet hinges to the main back frame and the top panel where the lock latches are, both are linked by two 1'' hinges.
The back panel was installed first fixing the two cabinet hinges to the panel with shorted wood screws since the plywood panel was not very thick for the original screw length, and then assembling the panel to the main frame fixing each hinge with 3/16'' screws an nuts, each hinge is 3'' far from the end of the panel.
This was a good moment to install the removable workable panel, since we don't need to install anything in the double bottom compartment, the worktable was modified to fit in the slightly reduced space due the installation of the custom hinge so there was trimmed at the center with a hacksaw, some drilling holes, a knife and a file to remove and smooth the excess wood.
Next the link hinges between the back and top panel were installed, those hinges are not symmetrical, one latch is larger than the other one to make easier the type of hinge configuration, those hinges were installed with M3 screws, nuts and washers. Then the lock latches were installed with M3 screws at the bottom part and wood screws at the top part.
Finally there were installed the supports for the folding cover that is a couple of 3/16'' screws with three nuts at the end to ensure that the folding top panel correctly rest over those supports. Those supports are at the large drawer height so, the nuts to fix them were reached through the large drawer hole using a pair of needlenose pliers. The purpose of the folding cover is to give extra support to the cantilever drawers to minimize the risk of fatigue of the custom hinge support.
Step 13: Handle Installation
A handle was made to make the toolchest a little more portable (I said "a little" because this thing is heavy, it weights empty 5 or 6 kilograms, about 10 kg when loaded with tools, anyway that's why the cabinet structure was reinforced with nuts and bolts), it was made out of an old leather belt and a leftover piece of copper.
First it was measured on the old belt the size of the handle (8'') plus the slack of the strap (10'' overall, 2'' slack) then it was marked and shaped with circular ends, next it was cut with scissors and then transferred the both ends shape to the copper piece.
The copper piece was cut with metal shears with some offset of the original transfer from the leather strap, then were drilled two holes in each end for 3/16''screws both leather strap and piece of copper. With a hard straight surface and a ballpeen hammer bend the copper's piece offset to make a pair of nice copper handle guards. :)
Finally the holes were centered and drilled on the top panel and screwed the leather strap with the pair of handle guards on each end.
Step 14: Final Touches
As a final part of the build there were glued the box corners on each end of the cabinet, it was used clear epoxy glue to avoid undesirable stains in the box paint job. The corners that are located over worktable face were modified to allow the worktable to be removed, it was just cut a little corner with the metal shears.
And finally, the name plate was drilled and installed at the front of the base cabinet with a pair of M3 screws, nuts and washers.
Step 15: Final Thoughts
I really like the final result of this project, now I can repair vintage toys with the proper gear just as seen in the movie, it is a great box to store electronics, craft and model making supplies. It may be nesesary to do some little adjustments such as the cantilever mechanism that is a little loose, or the custom hinge support that is not very sturdy, but, anyway, I am very happy with the final build, it really resembles to the basic shape shown in the movie.
Here is a little video of the tool chest:
If you have any idea, comment or doubt, just let me know.
Thanks for reading and so long... partners!
Andyfuentes22 2016
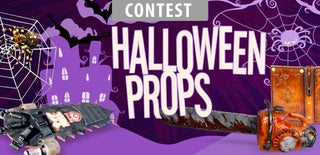
Participated in the
Halloween Props Contest 2016