Introduction: Super Servo With ESC No Soldering.
Power! In the realm of the radio control hobby, there is an unfulfilled dream, to make a powerful, inexpensive and simple servo amplifier. We want to make big projects, like an r/c mower, or really big off road robot. There are electric motors with gearboxes out there, like windshield wiper motors, but how can we use them to steer our project? There are electronic kits you can buy, but in my opinion, they are too expensive. In this house, we build what we want if possible. I'm not building a specific vehicle, just demonstrating how the electronic components go together so you can use this concept on your high power servo application. Here are the highlights:
This project can be done by anyone who has basic r/c skills.
If you have assembled r/c cars, boats or planes, you can make the super servo.
This wiper servo uses an esc (electronic speed control) with equal forward and reverse.
No unattainable or expensive parts needed, the esc has to have forward and reverse.
There is no soldering up a complex transistor bridge, the esc is used instead.
Other wiper motor servos require you to delve into soldering up an transistor "H" board. Not here.
The V-tail mixer and servo tester are super cheap and available at Hobbyking.com.
The market is saturated with these.
Step 1: The Concept
In the above diagram, I have omitted the power battery. Here we are just looking at signal flow.
A servo position pulse is received and the receiver sends it out on signal 1. At the same time, the servo tester is sending out a position pulse too and it is on signal 2. These two pulses are picked up by the v-tail mixer. The v-tail mixer compares the two pulses. If both pulses are the same, the v-tail mixer sends out a neutral position to the esc, on signal mixed line in my drawing. The esc sees this as no throttle, center stick, like a forward and reverse esc should. No movement.
If the positional information changes, as when we move the steering wheel left, the pulse on line 1 is different than line 2. Now the v-tail mixer compares the pulses and finds the difference. It then sends a pulse to the esc that basically says "go forward", the esc sends power to the motor and it turns. The mechanical connection (dotted lines) turn the control knob in the servo tester until it's output pulse matches the receiver's pulse. Once they match, the v-tail mixer tells the esc to stop. This is the feedback loop. It works the same for either way the control wheel turns. Basically, the motor and servo tester "chase" your control inputs.
The servo tester has multiple plug positions, I plugged into it's port #1. The v-tail mixer has 2 outputs, I plugged the esc into the bottom one.
Step 2: The Parts List
1 V-Tail Mixer under $4 V-Tail Mixer
1 Servo Tester under $5 Servo Tester
1 esc with forward and reverse. ESC
I would rather use this one. Another high quality ESC 2
1 Windshield wiper motor or other geared motor
1 Radio control system. Radio
1 12 volt battery 12 volt battery
Step 3: The Mechanics Part 1
I have a love-hate with the Chevy wiper motor. The output shaft is short and has a taper to lock into the output arm. This makes it tough to interface onto. You can use the push rod method of feed back to the servo tester as shown in the second pic in the section. That is how many do it. I wanted something more compact. There is a circuit board under the rear plastic cover that is part of the "park" position when the wiper is turned off, so the wiper blades stops where they are supposed to. I pulled my circuit board out and chunked it. I cleaned off the grease on the rear of the main gear. I needed a place to attach the feedback to the servo exerciser. I took off the nut on the output shaft and removed the arm and the "E" clip. I got the clip off with 2 screwdrivers, not the right tool. The main gear then slid out the back. I cut a block of wood to fit onto the back of the nylon gear with screws to give me something to attach to. I made a foam rubber piece with a hole to grip the knob of the servo tester. It is held in place with a piece of circuit board and screws to grip the control knob on the servo tester. The knob just friction fits.
Step 4: The Mechanics Part 2
I made a small cover for the servo tester to hold it in alignment and cut the rear plastic cover of the wiper to clear the servo tester. The "E" clip is reinserted to hold the gear in. The rear plastic cover is screwed on , then the servo tester's cover is screwed onto that. I felt I needed a stand to demonstrate the power of the servo, so I made one to mount the wiper on. I gave it a coat of spar varnish to stabilize the plywood. I cut a hole on the bottom to access the servo tester if I need to and to make it easier to plug in.
Step 5: Testing for Positive or Negative Feeback.
In this video I am testing the direction of the motor and feed back loop. There were two red wires and one black. Each red wire was for positive, but for different speeds. pick one and insulate the other. At first, i have no mechanical linkage to the servo tester. This was to allow the motor to move freely, if the feedback was positive, it would speed up if I turned the pot in the same direction as rotation. We don't want this. We want the motor to slow and stop when we turn the pot in the same direction as rotation (negative feedback). Then I attached a soft push rod and taped the servo tester down just in case the motor went wild. The push rod system works ok, It really depends on what kind of motor and gearbox you want to use. I am showing another interface option that worked ok, but was bulky. It uses a small piece of fuel tubing as a universal joint to turn the servo exerciser. On a different kind of gearbox, this may be better.
Step 6: The Radio.
The modern radio systems have lots of features. Travel adjusts and rates can be tweaked to get the servo centered and can be reversed to make installation easier. I used a Hobbyking pistol grip 2 channel. Very affordable and totally trouble free. Features and a great price.
Step 7: Safety Issues.
I really just have a few.
The motor case in this application become positive when rotating one way, and negative the other way. So we can't let anything make electrical contact with the gearbox or motor case.
This is a very powerful motor. It can hurt you and snag clothing and fingers, not to mention break any parts entangled in it's arm.
Be sure to fuse your project near the battery. If there is a short circuit, we want to pop a fuse.
Note also the radio is powered through the servo lead from the ESC. The ESC has a battery elimination circuit that pushes 5 volts back through the v=tail mixer and powers the receiver and the servo tester. If you add another esc to say a drive motor, decide which esc will power the radio and disable the red wire on the servo lead from the other. This is a well known situation among r/c hobbyists.
Step 8: Working Together
The above shot is an example of how the super servo would work when used with an r/c project. Seen here is a drive motor, drive motor's ESC, receiver, battery and wire harness. Also notice the automotive fuse near the battery. For those not into circuit diagrams, this is like a ready to mount electronics and electrical parts example. The drive motor is a 100 watt scooter motor. It has a #25 sprocket ready mounted on the shaft. Great motor, got mine for about $30.
Step 9: Conclusion.
The concept of using an esc, servo exerciser and v-tail mixer to create a high power servo amplifier does work. Some refinements could be made. I would love to see the Arduino community make up a tuneable servo exerciser so we could turn up the gain, especially around neutral point, as the center seems a bit soft. I don't think this design as it is now is fast or precise enough for racing buggies or aircraft, but more like for slower vehicles like robots.
Thanks for watching and VOTE!
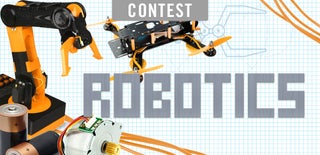
Participated in the
Robotics Contest
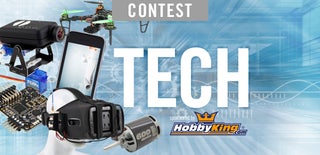
Participated in the
Tech Contest