Introduction: The Model 1882 Wireless Telephone
The most modern of modern gadgets, the wireless telephone,is actually not so modern after all. Within 6 years of the first American patent for a telephonic device (Alexander Graham Bell, 1876), another researcher discovered a method for sending voice through the air without connecting wires. His name was Amos Emerson Dolbear (1837-1910). From 1874 on Dolbear was chairman of the Physics Department at Tufts University. He worked throughout the 1870s on designing a working telephone (as did many other scientists in Europe and America), but was beaten to the patent office by Bell. Undaunted, Dolbear continued to develop his own ideas about electrical communication. One day in 1881 he was working in his lab when he made a startling, accidental discovery:
While at work at the single terminal receiver . . . the cord became detached from the line while I was unaware of it, and I still heard the speech from the transmitter plainly. Upon noticing this I began backing away from the end of the wire from the transmitter, letting the single cord hang free in the air. I could hear the talking in the most remote part of the room.
Wireless telephony was the next big step forward in communication. Telegraph and telephone systems required vast amounts of wire strung overhead on unsightly utility poles. The benefit, in time, money, and esthetics promised by wireless communication would be enormous. Dolbear applied for a patent on his discovery in 1882. Patent 350299 was granted to Dolbear in 1886, but nothing came of it. Wireless telephony did not become widespread till a century later, and not truly ubiquitous until after the turn of the 21st century. Why? Was there a conspiracy by the hard-wired phone company to suppress competing technology? Or was there a weakness, a fatal flaw in the Dolbear system? I decided to try to replicate his 1882 design, with features from later wireless phone designs by Nathan Stubblefield, Archie Collins, and Hugo Gernsback to uncover how well it worked--and how well it didn't.
Step 1: Induction or Conduction?
Professor Dolbear's patent describes the parts of his 1882 wireless phone, but he doesn't really explain how it works. He writes vaguely about varying potentials in the ground connection, but simply put, he uses the earth instead of metal wire for his connections. This method is called earth conduction telephony. (As a side note, Dolbear's use of an isolated capacitor in the air made it impossible for Marconi to patent his early radio apparatus in the U.S. Dolbear's patent covers the use of aerial antennas! Marconi's company had to buy Dolbear's patent in order to market his wireless sets in America.)
Conduction technology goes back at least to Samuel Morse, who invented his telegraph in 1837. Crews stringing telegraph lines hither and yon faced obstacles at natural barriers like mountains, rivers, and ravines. Morse theorized his electrical signals would cross some distance if fed into the ground (or water) at one spot, and picked again on the other side. It worked, but only over short distances.
About 50 years later a Kentucky farmer and inventor named Nathan Stubblefield developed an earth conduction wireless phone. He demonstrated his wireless phone in Washington, D.C. and Philadelphia, trying to attract investors. Stubblefield used conventional phone components connected to long iron rods driven into the earth. Range was still short--effective range was measured in hundreds of yards, though some accounts say Stubblefield's device worked as far as a mile. The secret to Stubblefield's apparatus was power. More batteries meant more voltage and more range. That's why his 1902 model phone (see photo) has such a tall cabinet; it's stuffed with dry cell batteries. Notice too the radial switch operated by his son, Bernard. Moving the switch could add or subtract batteries from the circuit, suiting power to performance.
Stubblefield's dream of earth conduction telephony ended, partly because of the inate weaknesses of the technology, and partly due to the machinations of shady stock promoters. Stubblefield turned to an alternate method of wireless communication, electromagnetic induction.
Induction is the creation of electromotive force across a conductor when it is exposed to a varying magnetic field. In other words, an electric current in one coil of wire will induce a similar current in a nearby coil. Notice the fatal word "nearby." If you use a device to vary the current in one coil--say, telegraph key, or a microphone--the receiving coil will reproduce the variations, which can be converted into sound by using telephone-style headphones.
The strength of an electromagnetic field is inversely proportional to the square of the distance from the charged particle:
F = kQ/r^2
where F is force, k is a constant [9 x 10^9 Nm^2/C^2], Q is the charge of the particle [in coulombs], r is the distance from the charge. Plainly put, the field weakens drastically with distance. That's the reason we don't use wireless induction phones today.
Not that clever men didn't try to make it work! From Professor Dolbear to Archie Frederick Collins, various engineers and inventors tried to make induction phones practical. What follows are my modern attempts to replicate their efforts..
Step 2: Winding a Homemade Induction Coil
Professor Dolbear's patent drawing is quite simple. (Note the illustration shows one-way operation; there's no transmitter for the recipient to talk back with. For 2-way communcation you'd have to double the equipment). The patent drawing shows an ordinary telephone transmitter, T, connected to a battery, a condenser, and a small induction coil. ("Condenser" is the old fashioned word for what we call now a capacitor). An induction coil is a form of transformer; in this case it serves to amplify the outgoing impulses from the transmitter. The receiver consists of a telephone ear piece, R, two condensers, and another battery. On the transmission side, the output of one side of the induction coil is grounded in the earth. The other connects to a condenser that seems to be hanging in mid-air. The receiver has one of its leads in the earth while the other connects to a condenser, battery, and another airborne condenser.
First, let's make an induction coil. You will need the following parts:
- 1 empty plastic wire spool, 3 3/4 x 3 1/2 inches, with a hollow core 1 inch in diameter.
- 22 gauge plastic insulated hookup wire, solid copper, 10-12 feet
- 30 gauge magnet wire, maybe 100 feet
- 12-16 iron survey flags, 1 3/4 feet long (these are 16 gauge)
- electrical tape
- 4 8-32 brass bolts, 1 inch long
- 4 brass washers to fit the 8-32 bolts
- 4 8-32 brass nuts
- 4 8-32 knurled nuts
- 4 ring posts
- 2 8 inch nylon zip ties
- As for tools, you'll need a crimper, wire stripper, and a hand-held drill with assorted bits.
Bore a small hole through the spool flange near the core opening. Put about 3 inches of insulated 22 gauge solid copper wire (called hookup wire, bell wire, etc.) through the hole you bored. Wrap the spool with the rest of the wire. Lay the wire on smoothly, tightly together, from one end to the other. Don't overlap the turns. When you reach the end of the spool, reverse direction with the winding. Lay down at least three layers of 22 gauge wire. At the end of the third layer, bore a hole through the spool flange and feed through about 3 inches of wire. Cut off any excess wire. Make sure the second hole is aligned with the first, at the opposite end of the spool. (Study the photos) This is the primary coil of your telephone induction coil. Wrap the wire with two layers of electrical tape, keeping everything as smooth and snug as you can.
For the secondary winding you're going to need finer wire. An old book I consulted recommends 36 gauge magnet wire, but 36 gauge is like hair, and breaks very easily. I used 30 gauge, which is much stronger.
You need to wind on at least 12 layers of fine wire for the secondary. This is tedious, and here's a way to do it without going cross-eyed. Use your hand drill!
Get a metal rod (1/8 of an inch is thick enough) about 8 inches long and two corks or rubber stoppers with 1/8 inch noles bore through them. If you have a drill press, so can make these yourself. Glue one of the corks/stoppers on the rod about 3 inches from the end WITH THE NARROW END FACING INWARD; that is, the wide end of the cork should be facing the short end of the rod, and the narrow end of the cork faces the longer part. Slip the rod through the hollow core of the spool until the cork is tight in the hole. A 1.25 inch wide cork will fit a 1 inch spool core just fine. Slide the second cork onto the rod, narrow end inward, and bring it down tight.
Bore a new hole in the flange 180 degrees from the outer end of the primary winding. Put about 3 inches or so of the 30 gauge enamel-insulated secondary wire through the hole outward, and tape it down to temporarily anchor it. Now chuck the short end of the rod into your variable speed drill, cordless or not. Keep the 30 gauge wire taut with one hand while you lightly speeze the drill's trigger. Make sure you wind on the 30 gauge in the same direction as the 22 gauge primary. As the spool turns, let the 30 ga. wire wind smoothly around the tape covered primary. As with the heavier wire, when you reach the end of the spool reverse direction. Do this 12 times and you've wrapped your secondary. The wire will feed best at modest speed, so don't try to rip through the process too fast. Cut off the 30 ga. wire, leaving enough to feed through a 4th hole drilled in the spool flange 180 degrees opposite the first 30 ga. hole. Study the photos for a clearer idea how this all goes. It's simpler to do than describe!
Wrap the secondary winding with two layers of electrical tape. Anchor the ends of the tape with nylon zip ties so the tape can't come loose.
Trim the 4 wire ends to about 2 inches each. Remove the insulation on the 22 gauge wire, baring about a 1/4 inch of wire. Crimp on a suitably sized connection ring that fits an 8-32 bolt. Follow the same procedure with the two 30 gauge leads. The enamel insulation is best scraped off by using a piece of folded sandpaper. Put the end of the wire inside the fold and pull. Repeat until you have 1/4 inch of clean copper wire exposed.
Next, drill a 8-32 sized hole in the spool flange out near the edge 90 degrees from the holes already drilled for the secondary and primary leads. Do the same at the opposite point 180 degrees away. Make identical holes in the other flange. Choose one end of the spool to be 'top' and the other to be 'bottom.' Insert an 8-32 bolt, threads up, through holes in the top flange. Put a brass washer and nut on each bolt and snug in place. Slip the ring connectors over each bolt. Add a knurled nut to each bolt and tighten finger tight.
For the bottom flange, insert the bolt so that the heads are on the outside and the threaded shank is inside the spool. Make sure you put the ring connectors on the bolts. Follow the instructions as above and install the washers, nuts, and knurled nuts. (See photos). Tape the wire to the spool flange to prevent them snagging on other things.
Now we have to make the core of the coil. With a pair of wire cutters, cut 3.5 inch lengths of 16 gauge iron wire made from the marker flags. (Pull off the orange flag and discard). Pack the core of the spool tight. The last few rods will have to be tapped in, but make sure you fill the cavity completely. Both ends of the core should be flush with the spool ends.
Your 1882 style telephone induction coil is finished.
You can check the connections with a multimeter to make sure you have no breaks in the wires. Resistance on the primary and secondary should be very low, though the 30 gauge secondary should be a little higher than the 22 gauge primary.
If you plan to make matching transmitter/receivers, you'll need to make an identical second induction coil.
Step 3: The Transmitter
Because of the relative inefficiency of this type of telephone, you 'll need to use a sensitive microphone. I used a vintage carbon microphone cartridge (made by Shure). This is mounted in a candlestick style handset.
To make this transmitter, you'll need the following materials:
- 1 carbon microphone cartridge about 2 inches in diameter
- 2 lengths of 22 gauge bell wire, 16 inches long each.
- 2 6-32 brass machine screws, 2 inches long
- 2 6-32 brass nuts
- 2 6-32 brass washers
- 2 6-32 knurled nuts
- 4 crimp-on connectors, spade or ring, sized for 22 gauge wire
- 1 8-32 machine screw, 1.5 inches long
- 1 8-32 nut
- 10 inches of 3/4 inch PVC tubing, any color. I used common Schedule 40 plumbing tubing
- 1 3/4 inch PVC tubing cap. This must have a flat end
- 1 3/4 inch PVC elbow, 45 degree bend
- 1 "2 inch" cap, flat ended. These are actually 3 inches outside diameter. I couldn't find one in white PVC, so I used one made of black ABS instead.
- 1 3/4 inch PVC plug
- 1/8 inch thick poplar disk
- 2 1/2 inch stainless steel cup
- 4 3/8 inch long, 4-40 screws
- 2 inches of 1/2 inch basswood square rod
- 1 4-inch round wooden plaque
- 2-wire speaker wire, 4 feet long
- 1/4 inch mono phone jack
On the underside of the wooden plaque, find and mark the center point. 1 inch to the right and left of the center point mark 2 spots. You should have 3 dots total, in a straight line, along the center line. Drill holes all the way through the wooden plaque at each indicated points, then countersink the holes to allow the heads to be flush with the base. The center hole should be large enough to accept an 8-32 bolt, while the 2 flanking holes should be sized to 6-32 bolts. Sand, stain, and seal the plaque. Insert the three bolts from the underside upward.Put a washer and nut on the two 6-32 bolts.
Take the 3/4 inch tubing cap and drill a hole through the center. These caps often have a convenient divot or nub left by the molding process indicating the center of the cap. Attach the inverted cap to the base with an 8-32 bolt. Tighten down the required nut. Insert a 10 inch length of 3/4 tubing into the cap. Drill two small holes in the tube, one on each side near the 6-32 bolts, just above the 3/4 cap. See photos for a clearer image of what to do.
Bare the ends of two pieces of bell wire, each about 16 inches long. Solder the ends of the wires to the two terminals on the microphone cartridge.
You'll need to bore a 3/4 inch hole in the center of the "2 inch" tube cap. Next, bore a pair of small holes in the 3/4 inch pipe plug. Feed the wires from the microphone cartridge through the holes. Press the plug through the "2 inch" cap, and into the open end of the 45 degree PVC elbow. Be sure to feed the wires through the elbow. Temporarily remove the tube from the base and insert the wires. Work each wire through the holes near the bottom of the tube, then firmly press the tube into the base. Crimp ring or spade connector to the ends of the wires, then fit those to the 6-32 bolts. Put on the 6-32 knurled nuts and tighten.
Cut two small blocks of 1/2 squared basswood rod. The exact size depends on the depth of your "2 inch" cap and the width of your mike cartridge. At any rate, the block should hold the cartridge in place and be flush with the cap mouth. Drill the cap and fasten the blocks in place with short 4-40 screws. (See photos).
Cut a 1 1/2 inch hole in the center of the 3 inch poplar disk. Sand smooth. Paint or color the disk to match the ABS cap (I used Sharpie permanent marker to dye the thin wood black). Drill two holes near the edges to fasten the disk to the poplar blocks--use another pair of 4-40 screws for this.
Drill 4 or 5 holes in the bottom of the stainless steel cup. Use a drill press with a 1/4 inch bit. File the holes smooth. Fit the narrow end of the cup into the hole in the disk as squarely as you can; glue it in place with super glue.
Strip the 4 ends of a 4 foot strand of speaker wire. Separate the wires at one of the speaker wire 4-5 inches. Crimp on ring or spade connectors, then attach to the 6-32 posts on the base of the transmitter. On the other end of the speaker wire attach a mono 1/4 inch plug (follow the directions included with the jack.)
The transmitter is finished.
Step 4: Bare-bones Phone, Mark I
Because you need two phones to talk back and forth, I built two sets. One is a bare-bones device mounted on a board; the other is a fancier, steam-punkish device on tripod legs which I'll describe later. Functionally they are the same and contain the same components.
Parts needed:
- A wooden plank for the base. Mine is made from a piece of pine shelving 16 x 6 x 1 inches.
- 4 rubber appliance "feet," with screws
- 1 single pole, double throw knife switch (In this prototype I used double pole, double throw switches I had on hand, but SPDT are what's needed.)
- A 200 volt (at least) capacitor rated at 1 uF (1 micro-farad)
- 1 induction coil (described earlier) or a small doorbell transformer, 120V to 12V
- 9 crimp on ring or spade connectors (rings preferred)
- 2 2 inch alligator clips
- 4 3/8 inch long, round head wood screws
- 3 8-32 brass machine screws, 2 inches long
- 2 8-32 brass washers
- 3 8-32 brass nuts
- 2 8-32 knurled nuts
- 4 quick detach crimp on connectors
- about 6 feet of 22 gauge hookup wire x 2, preferably with contrasting color insulation (mine's red/white)
- 1 telephone carbon microphone assembly
- 10 inches of 3/4 inch PVC tubing
- 1 3/4 inch PVC end cap, flat-ended
- 1 high impedance earphone or telephone receiver
- 3-4 feet of speaker wire
- Solder, soldering iron, screwdrivers, drill, bits, electrical tape or shrink tubing, etc.
Layout the components however you like. Being right-handed, I put the transmitter on the left so I could hold the earphone with my right hand.
Slap on a coat or two of varnish on the wooden base. Sand smooth. When dry, attach a rubber appliance bumper or "foot" to each corner on the underside of the board.
The transmitter and receiver are salvaged from a modern replica candlestick style phone which I found for sale online. I didn't want the dialer or base, so I disassembled the phone for the microphone and earphone only. You can make another transmitter like I previously described, but cannibalizing an existing phone saved time. You can use a high impedance crystal radio earphone for your receiver.
The imported candlestick replica phone had such flimsy wiring I removed it and re-wired the transmitter and earphone with stronger 22 gauge bell wire. It was an easy job and only requires 2 wires, so I won't go into it in any detail. I mounted the transmitter on a 10 inch stalk of 3/4 inch PVC tubing fixed a 3/4 inch PVC cap to my base board with an 8-32 bolt. The wires from the transmitter are routed out of the tube about 3/4 of the way down through holes drilled for that purpose. The Positive wire will be connected to the induction coil or transformer. The negative lead gets a 2 inch alligator clip, as this will be connected directly to the battery powering the set.
As I said, the Positive wire from the transmitter is connected to the transformer/coil on the Primary side. If using the homemade induction coil, that's the lower end of the 22 gauge winding. If you're using a 120VAC to 12VDC doorbell transformer, you'll need to use the side with three wires (normally attached to house wiring as Hot, Neutral, and Ground). Use either the Hot or Neutral wire, and connect with a crimped on quick disconnector. The Ground wire on the transformer is not used, so tape it off out of the way. The remaining transformer wire gets the other 2 inch alligator clip.
(Don't forget to mount the coil or transformer to the board. Use 2 3/8 inch round head wood screws to do the job.)
The induction coil or transformer has two output connections. One goes to the outside post of the Single Pole, Double Throw knife switch. Mount the switch below the coil/transformer so the switch can swing from left to right. Crimp a spade connector to the transformer/coil lead and attach it to the leftmost post on the switch.
The other transformer/coil output wire must be fastened to one of two external posts. Drill a hole through the base near the coil/transformer, sized to accept an 2 inch long 8-32 bolt. Insert the bolt from underneath and lock it in place with a washer and nut. Crimp a spade or ring connector to the transformer lead. (If using the homemade induction coil, make a short jumper wire with connectors on each end. Attach one end to the upper secondary post.) Connect the transformer/coil wire to the 8-32 post and hold it in place with an 8-32 knurled nut. From the same post run a 22 gauge wire out to convenient spot near the right edge of the base board. Drill a small pilot hole and insert a 3/8 inch long, round head wood screw. Connect the first external post wire to the screw.
Drill a second hole for the other external post 4-5 inches to the right of the first. Fix the other 8-32 bolt in place. Run a length of 22 gauge wire from the second post to the center post of the knife switch.
The last open post on the knife switch needs a short length of 22 gauge wire ending in a quick detach connector. Next take your 1 microfarad capacitor and fix the other half of the quick detach connector to one of its leads. The cap I used has axial leads and is not polarized. On the opposite end of the capacitor crimp another quick detach connector, and to that add a short length of 22 gauge wire. This wire should end in a ring or spade connector. Drill a second pilot hole near the first wood screw and twist in another round head wood screw. The wire from the capacitor connects to this second screw.
The earphone I also rewired with sturdier 22 gauge leads. If you opt for the simpler crystal radio earphone, use its wiring. Crimp on spade or ring connectors to the end of the earphone leads, and attach these to the wood screws. Tighten all connections firmly.
Study the photos. Hopefully they make things clear!
Step 5: Model 1882 Wireless Phone Mark II
Having made the Bare-bones Phone Mark I, it's time to make the fancier Mark II version. I exhibited this phone at the Maker Faire in Raleigh, NC on June 7, 2014. To meet the deadline I resorted to a few short cuts, such as using small transformers instead of my homemade induction coils, and using DPDT knife switches, which I had on hand.
The components inside are the same as the Bare-bones Phone.
I used:
- 1 chipboard cafe table
- 4 1/2 feet of 1/2 inch quarter round molding
- 4 feet of poplar board, 5 1/2 x 3/8 inches
- 2 feet of poplar board, 2 1/2 x 1/4 inches
- 46 inches of 3/8 x 3/8 square basswood stock
- 3 feet of 1/4 x 1/4 square basswood stock
- 9 inches of 1 1/2 x 1 1/2 inch square poplar stock
- 2 double-ended wood studs, 1/4-20
- 2 1/4-20 threaded knobs
- 2 long shank 1/4 mono phone jack ports
- 1 piece of 3/4 inch pine, 11 7/8 x 11 7/8 inches
- 1 pair radio headphones, high impedance, with a 1/4 size mono jack (I found a pair of ex-Soviet military headphones on Etsy.)
- 1 steel screw-in hook, about 1 inch across
- the Transmitter you made in Step 3
- All the electrical components of the Bare Bones Phone, less the mounting board, transmitter, and earphone
- Tools: miter saw, drill, bits, crimp tool, soldering iron, solder, stain, varnish, chip brush, carpenter's glue, sanding block (medium/fine).
To start with I happened to have a tripod cafe table I found at a local freecycle shed, so it cost me nothing. The top, which is 20 inches in diameter and about 3/4 of an inch thick, is made of chipboard. The legs are pine, round, and 24 inches long. They screw into steel leg mounts on the underside of the table. I eventually stained the table with Minwax Golden Oak stain and liberally applied Minwax water-based polyurethane varnish. I also put black vinyl caps on the ends of the legs to cushion them.
The Mark II's case is a simple wooden box. I marked off a square on the table top in pencil with sides 13 inches long. The size is a bit arbitrary; I intended the box to hold not only the electrical components of the phone but a fair number of batteries as well. I cut four lengths of 1/2 inch quarter round molding to be the base of the box. I mitered all four corners 45 degrees and glued them to the table before it was stained or varnished, of course. I used a good grade of outdoor carpenter's glue and clamped the molding down until it was dry.
I next cut the 5 1/2 inch wide poplar board to fit inside the molding. This resulted in two pieces (the front and back) being 11 3/4 inches long while the side pieces came out 11 3/16 inches. I did not miter the corners of the box, though you can if you want. I simply butted them together with glue along the corners and along the bottom where the boards met the table top and molding. Clean off any excess glue and let dry.
Cut 4 pieces of 3/8 square basswood stock 5 inches long each. Glue one of these into each inside corner of the box.
Cut 2 pieces of 2 1/2 inch wide poplar board 11 3/16 inches long. Place a pair common 6 volt lantern batteries inside the box against either side wall. Apply glue to the bottom edge and ends of one piece of 2 1/2 inch poplar and fit into place inside the box up close to the batteries. This small board should run front to back, that is, parallel to the side of the box. (See photos). Repeat this process on the opposite side of the box. You're making bays, or trays for the phone's batteries. Cut four pieces of 1/4 inch square basswood stock and glue these to the inside corner of the battery walls to strengthen them. Don't put them inside the tray area or you'll compromise the space for the batteries.
Drill a 1/2 inch hole in the exact center of the table (now the bottom of the box, too). Then drill two smaller holes to accept 8-32 machine screws for the phone's antenna connections. I put mine 2 inches from the center hole, offset one to the rear and the other offset toward the front of the box.
Bore a 1/2 inch hole in the very center of the front of the box. Drill a 1/2 inch hole in the center of the back of the box. Install in each the long shank 1/4 mono phone mount.
Cut a 3/4 inch thick piece of pine planking into a square 11 7/8 per side. To make it look nicer, round the top edges with a router. Sand smooth. This is the box lid. Cut 4 pieces of 1/4 inch basswood 6 1/2 inches long. Glue these to the underside of the lid 1/2 an inch in from the edge and staggered around the underside (see picture.) These help center the lid on the box.
Cut 2 pieces of 1 1/2 inch square poplar stock 4 1/2 inches long. Glue these vertically inside the box tight against the inner wall of the battery boxes. I offset mine left and right, but they can be symmetrical. Drill 1/4 pilot holes in the center of the block tops and install 1/4-20 double ended studs. Be sure about 2 1/4 or 2 1/2 inches of stud protrudes from the block. Carefully drill 1/4 holes in the lid to match the location of the studs. With 1/4-20 knobs in place, the lid will be secured to the box.
Now is the time to stain and seal the table, box legs, and lid.
Install the electrical components as in the Bare-bones Phone, except that the external (antenna) connections are made with 8-32 bolts put through the underside of the table. Solder the required wires to the transmitter and headphone jacks. I found the shanks of the 1/4 mono jacks were actually a bit too long. Inserting them fully actually unmade the connection. This was fixed by fitting small plastic or rubber spacers to the jacks.
Dead center on the lid of the box mount a single pole, double throw knife switch. (Once again in the photos I am using a double pole, double throw switch, which is what I had on hand. SPDT is all that's needed.) Bore appropriate holes alongside the switch for the three wires from the phone and connect them as on the Bare-bones phone. When the switch is pushed toward the transmitter, you can talk; moved to the other side to the headphones, you can hear any replies.
To give the headphones a place to hang when not in use, install an appropriate size hook in the edge of the table.
Step 6: The Induction Coil Antenna
The induction coils make wireless telephony over short distances possible. I made two coils 4 feet in diameter, with 60 turns of wire each. You'll need 2, exactly alike.
Materials to make the antennas and stands:
- 5 pounds of 20 gauge solid copper magnet wire (this makes 2 antennas of 2 1/2 pounds of wire each)
- 5 1x2 pieces of white pine, each 6 feet long
- a couple dozen short (2 inch) deck screws
- 2 1x4 pieces of white pine, each 6 feet long
- at least 24 feet of 1/2 inch PVC tubing
- 4 1/2 inch PVC X joints
- 4 1/2 inch PVC 45 degree elbows
- 12 1/2 inch PVC T joints
- 2 1/4-20 bolts, 4 inches long
- 2 1/4-20 flat washers
- 2 1/4-20 wing nuts
- a whole lot of small nylon zip ties
- 12 8 inch nylon zip ties
- chop saw, screwdriver, carpenter's rule, square, pencil, sandpaper
Making the wire coils will require a frame, or jig that you can dismantle after you're done. Some old manuals suggest drawing a 4 foot circle on your shop floor or wall and hammering nails around the circumference. This was not possible for me, so I made a star-shaped frame out of scraps of 1x2 white pine lumber (see picture). The end result was a 16 point "star." Using a 2 foot length of old metal tape measure, I tacked the tape to the center of the star, then used it to mark each 1x2 exactly 2 feet out from the center. At those points I drove a 3 inch nail into each branch of the star.
I then took my 5 pound reel of 20 gauge magnet wire and started wrapping it around the star. I left about 12 inches of lead to start, wrapped twice around the lowest nail, and commenced wrapping in a clockwise direction. It doesn't matter which way you wrap, just make sure you wrap both coils in the same direction! When I had done 60 turns, I anchored the wire and cut it loose from the reel. All around the coil I used small (3 inch) nylon zip ties to bind the wire together. I spaced the ties every 2 inches. Don't spare 'em; the last thing you want is 60 turns of 20 gauge wire coming loose! If you don't have zip ties, you can wrap the coil at close intervals with electrical tape.
When the coil is secure, pull the nails out of the frame and release the coil. Put the nails back in and make another coil exactly like the first. Store them flat somewhere while you make the stands.
Since the 1x2 lumber comes in 6 foot lengths, it was an easy choice to make the stands 6 feet tall. Take two straight pieces of 1x2 and sandwich short blocks (6-8 inches) between them, starting at what will be the top of the stand. Use short deck screws to bind things together. Stagger the screws (it improves strength) and use them from both sides. Leave a 4 inch gap at the bottom end of the stand for the base.
To make the base, cut a 6 foot length of 1x4 into 2 equal 3 foot lengths. Mark the center of each 3 foot piece and cut halfway through the lumber, making a slot just wide enough to fit the other piece. You're making an "X" out of the 1x4s. Fit them together and drive a long deck screw vertically through the joint. Next, fit the bottom of your upright stand over the "X" frame, tight against the joint. Put a few screws through the upright into the base. If need be, use leftover pieces of 1x2 to make 45 degree braces between the base and the upright. Make 2 stands, of course.
A PVC tube frame will hold the coils. To make one frame, cut a short piece of tubing (about 2 inches long) and join two of the "X" joints together. Cut lengths of 1/2 tubing to fit the side joints of the lower "X" out to a length of 4 feet total. (Make sure to allow for the portion of the tubing that fits into the joints). Add a third piece of 1/2 inch tubing to the bottom joint of the bottom "X" and a another piece to the top joint of the top "X". This should total 4 feet in length also (see picture).
Cut two short joining tubes 2-2 1/2 inches long and fit them to the side joints of the upper "X". Push on the 45 degree elbows here. Measure and cut lengths of 1/2 tubing from the elbows to the outer rim of the frame so that the total distance from the rim to the center is 2 feet. Jam the joints together as tightly as possible, or glue together. Be sure the frame is flat and that none of the joints are canted.
Lastly, take 6 1/2 inch PVC "T" joints and cut open the long axis. To do this, fit the short end of the "T" to a handy length of tubing and hold the joint in place under your chop saw. Bring the blade down and shave off about 1/4 inch of the long axis of the joint, making an open channel. Fix all six "T" joints this way and fit them to the PVC frame.
Carefully fit the wire hoop into the open "T" joints, all the way around. Make sure the wire leads from the coil are at the bottom of the frame! Around each "T" wrap an 8 inch zip tie so that it forms an X across the open side of the PVC joint. Tighten the zip tie to hold the wire coil inside the joint. Do this to each joint.
Bore a 1/4 inch hole all the way through the center of the lower "X" joint. Also bore a 1/4 size hole through the wooden stand, about two inches below the top. Put a 4 inch long 1/4-20 bolt through the hole, and fit the antenna assembly to the stand. Put a washer over the PVC frame, add a wing nut, and finger tighten it until the coil and frame are secure.
Strip the enamel insulation from the coil leads with sandpaper. The induction coil antenna leads attach to the antenna posts on the two phones.
Step 7: Earth Conduction Vs. Electromagnetic Induction
If making induction coils with 5 pounds of copper wire does not appeal to you, you can use the 1882 phones Mark I and II as earth conduction phones. All you need for this are 4 long, conductive rods and wire to connect them to the phones. Nathan Stubblefield used steel rods for his device; Hugo Gernsback added flat copper and zinc plates to the rods he buried for his experimental phone.
The trick to this method of wireless communication is geometry. With the induction coil phone, successful transmission and reception is dependent on coil size and battery power. With earth conduction, range is achieved by widely separating the ground rods used. Archie Collins, in his 1905 book "Wireless Telegraphy," states that the ground rods should be twice as far apart as the desired operating distance. In other words, to talk wirelessly through the earth for 100 yards, the ground rods of the sender and receiver should be 200 yards apart!
Publisher and inventor Hugo Gernsback (after whom the annual science fiction awards the Hugos are named), creator of the magazines MODERN ELECTRICS, ELECTRICAL EXPERIMENTER, and many others, issued a book in 1910 outlining methods of wireless telephony used up to that time. He describes experiments of his own made in 1903, when interest in Nathan Stubblefield's work was still high. Gernback recommends burying ground rods with zinc and copper plates attached 4 feet deep in the earth and 25 yards apart. He then saturated the ground over the rods with zinc chloride to enhance the galvanic effect. Gernsback claimed this system worked up to 3 1/2 miles.
To try earth conduction yourself, get 4 lengths of steel rebar. Clean off any rust or paint. Using either the Bare-bones phone or the Mark II connect the antenna posts to the rebar using long, single strands of copper wire. Try Gernsback's gap of 25 yards to start with. (I don't recommend pouring zinc chloride on the ground!) Position the 2 phone devices 25 yards apart and try them. If you can't hear anything, move one set closer until you do. You can also try increasing the battery power, but beware of overheating your circuit components.
I had more success with earth conduction than aerial induction with the wire hoops.
Step 8: Batteries, Batteries, Batteries
The real secret to making 19th century wireless phones work is power, and that means batteries. Lots of batteries. Prof. Dolbear, in his patent, casually mentions using 100 volts to power his 1882 type phone. Nathan Stubblefield experienced problems in his 1902 Washington D.C. demonstration, which he solved by adding more batteries to his equipment. By the time of his Philadelphia demonstration, he had built a much larger cabinet for his device, which was crammed with dry cell batteries. In his 1903 experiments, publisher Hugo Gernsback mentions using 6-10 6 volt batteries--36 to 60 volts. Archie Frederick Collins worked for years to perfect a wireless phone using the output of Ruhmkorff spark coils, which could operate at 15,000 to 20,000 volts.
My earliest attempts at natural conduction telephony used 6 to 12 volts per phone. All I heard was the 60 Hz "dialtone." This is because modern household electrical systems are grounded in the earth, so I was picking up the hum of 60 cycle household electricity. Not till I upped the voltage to 48 volts was I able to hear voices through the apparatus. With my kids helping, we drove iron stakes into the ground and set up the telephones. Our best distance that day was about 10 yards.
To add batteries to the circuit, use double ended jumper wires (alligator clips on both ends). Connect the batteries in Series; that is, connect the Positive post of one battery to the Negative of the next, so that you end up with a sequence like P-N-P-N-P-N. The first open post you connect to the phone circuit must always be the opposite of the last open post. Hooking up batteries in series adds the voltage of the batteries together. Hooking them up in Parallel does not increase the voltage, but does increase the amperage. In a parallel connection, all the Positive posts are connected together and all the negatives together: P-P-P / N-N-N. For the 1882 wireless phone, you'll want series connections.
Using the 4 foot induction coil hoops, I was able to use the wireless apparatus at the Raleigh, NC Maker Faire on June 7, 2014. It was a crowded, noisy exhibition hall, so I could only separate the hoops about 10 feet--but they worked. Many people stopped by for a demonstration.
I used common 6 volt alkaline lantern batteries (6 volts apiece) or 12 volt gel cell batteries. Attempts to use DC power supplies highlighted another peculiar problem associated with this technology--too much power and the carbon microphone cartridges get hot. Really hot. This makes sense, since the carbon mike is basically a variable resistor, and pumping too much power through a resistor will make them hot. That's why the knife switches were so important. After speaking, the transmitter needed to be turned off ASAP. The headphones, operated electromagnetically, did not get hot. There is no volume control on these devices though, and at short range the POP when the switch was closed to "listen" was kind of painful.
It's easy to see why this technology did not endure. True radio had far greater range, and wired telephony did not require high voltage. (Landline phone systems in the USA operate at 48 volts DC, battery powered, which is why landline phones continue to work when there's a blackout. They're not on the same circuit as standard household power.). Induction technology is currently making a comeback in the form of charging devices--for cell phones.
Step 9: Books on the Subject
If you'd like to read more about early wireless telephony, I can recommend these books:
The Wireless Telephone, by Hugo Gernsback, 1910. Facsimile edition, 2012.
Wireless Telegraphy, by A. Frederick Collins, 1905. Facsimile edition, 2012.
The Book of Wireless Telegraph and Telephone, by A. Frederick Collins, 1922. Facsimile edition, 2014.
Kentucky Farmer Invents Wireless Telephone--But Was It Radio? by Bob Lochte. Murray, Kentucky: All About Wireless, 2001.
The Boy Electrician, by Alfred P. Morgan, 1940. Reprinted by Lindsay Books, 1995.
Electrical Things Boys Like to Make, by Sherman R. Cook, 1954. Reprinted by Lindsay Books, 2005.
The Telephone: An Historical Anthology, edited by George Shiers. New York: Arno Press, 1977.
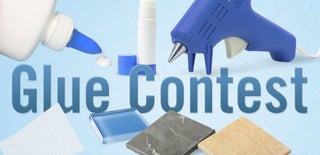
Participated in the
Glue Contest
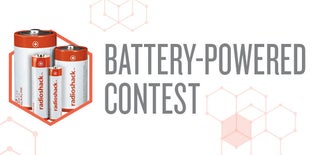
Participated in the
Battery Powered Contest