Introduction: Wood LED Desk Lamp
Summer is almost over and unfortunately it's time to get to work again, so I've decided to make a new desk lamp to help me study, I also added a dimmer to control the light, since staying up until late in the morning with a light that can't be dimmed really hurts my eyes.
In this instructable I'll show how I built it. Also, the dimmer I built can be used with any kind of LED light below 20 watts, so even if you're not interested in this kind lamp, feel free to use it to control any LED lamp you wish.
Step 1: Materials and Tools:
Materials:
- About 2 meters of wood strip (1,8x0,9cm / 0,7x0,35in)
- Thin aluminum plate (5,5cm x 25cm / 2,2x9.8in )
- Led strips (5 strips of 25 cm each)*
- Assorted wood screws
- Wood glue
- Threaded rod and 4xbutterfly or security nuts (3 to 5 mm in diameter)
- Switch (rated 3 amps at least)
Tools:
- Drill
- Miter box
- Wood saw
- File
- 100 grit sandpaper
- 400 grit sandpaper
- Router (optional)
This lamp also includes a dimmer, which is optional since not all people are versed into electronics, the materials have been separated for the sake of simplicity.
The total cost of this project in parts is around 15$.
- LEDs: ~2$ for the length used (bought at: http://goo.gl/g3ihrU )
- Aluminum piece: ~1$
- Wood: ~3-4$
- Screws, nuts and washers: ~2$
- Electronics: ~3-4$
- Other: 1$
*You can also use high power LED's, which are probably more efficient than LED strips.
Step 2: LED Holding Plate
I begin by cutting a 5.5 by 25cm (or 2,2x9.8in ) piece of aluminum, this will serve as the heatsink for the LED strips, which will be adhered to it.
Step 3: Making the LED Frame
With the help of a router, I cut a groove at the side of the wood strip, the total length of this strip is around 70 centimeters. If you don't have a router you can glue a thin wood strip to achieve the same effect.The groove is 4mm in depth and goes almost halfway through the strip.
Then, with a miter box, I cut 45 degree angles to create a rectangular frame for the aluminum strip. Place the plate on the groove and mark where it should be cut, this ensures a perfect fit.
Step 4: Making the LED Frame, 2
Before gluing the frame I sand the surfaces where the strips will meet with 100 grit sandpaper to make the union stronger, I don't want to sand too much because it's easy to ruin the perfectly angled cut.
I found quite difficult to clamp the pieces together, so I used some tape to glue it, it worked surprisingly well. I just laid out the pieces over the tape, making sure they stick properly, with the extremes touching. Then, I applied glue and folded the pieces into shape. Sanding is important before doing this, as wood fibers can get in between and weaken the joint. I used four small and round head wood screws at each side to secure the joints.
Step 5: Making the Arm
To make the arm of the lamp I used two 70cm strips, which I cut in half, making a total of four wood strips with 35cm each, I then used an appropriately sized washer to draw with a pencil the area to be cut away and the hole to be drilled.
I use my homemade router table to round the tips of the strips, some coarse sandpaper has the same result. It's preferable to clamp all the pieces and sand them together so they all have the same rounded edge. The same applies when making the holes, this reduces the chance of misalignment. A drill press is preferred, but I don't have one, so I used a hand drill as perpendicular as possible to the surface of the strips.
Step 6: Making the Arm, 2
A pair of strips are used to support the LED frame, forming the upper part of the arm, to do this, I drill a hole through the frame 1/4 of the way and use wood screws to attach the strips to the frame. The hole of the strips has to be big enough to allow them to pivot freely, with enough friction between the strips and the frame to allow it to be adjusted easily.
The lower part of the arm has to be structurally reinforced, so I add two pieces between the strips, the total width of the arm has to be the same as the LED support frame, as seen in the 4th picture. The reinforcements are placed at 5 centimeters in one side and as close to the holes as possible in the other, this is because for the arm to be adjusted, pressure must be exerted from the outside, creating enough friction for the structure to be still.
The reinforcements are glued using some lengths of threaded rod to push the outer strips against them. Four holes are drilled through the strips into the reinforcements and two screws are added to each side.
Step 7: Making the Base
To make the base cut a 15x15cm square, with the exception of a small protrusion, which has the same width as the internal section of the lower arm. This protrusion is cut with some margin of error, and sanded down to ensure a tight fit with the arm.
Two holes are carved with the router, this holes will be used to hide the the circuitry, later, a channel is routed between the two holes to pass the wires from the circuitry to the controls. Two 45º holes are also drilled to allow the cables to pass trough the wood into the carved holes where the circuitry will be placed.
A hole is drilled through the protrusion using the lower section of the arm as a guide, I make sure the arm is perfectly perpendicular before making the hole, as seen in the 4th picture.
Step 8: Staining and Final Assembly
This wood is too clear for my taste, so I've decided to stain it with some homemade copper based stain.
Before staining the pieces I sanded them all, making sure to get rid of all the ridges and imperfections with 100 grit sandpaper and then leaving a smooth surface finish with 400 grit sandpaper.
Once all the pieces of the lamp are smooth and stained, the threaded rods can be cut to length and placed on each sides of the lower arm section so the lamp can finally be assembled.
To tighten the sections of the arm I used security nuts and security washers. The security nuts won't roll off when changing the position of the arms, and the security washers ensure the nuts aren't too tight, and maintain a constant pressure over time. In conjunction, this makes the arm assembly really reliable and easy to adjust, and the arms can be moved into any position and stay locked in place thanks to friction. The lightness of the wood makes it quite better than any other metal lamp I've used before, which ended up breaking after adjusting it too many times.
I've added a simplified drawing of how it all should be assembled together so you can visualize it better.
Step 9: Wiring the LEDs
LED strips are cut into 25cm sections and then glued to the aluminum plate, the sections are 1cm wide, so 5 of them are enough to cover the entire plate. Make sure to clean the plate with alcohol before sticking the strips. A bit of tape is added at the extreme to avoid possible shorts with the plate.
All the negative terminals and all the positive terminals are then soldered by separate, when it comes to wire the lamp, a hole will be made though the frame to pass the wire, and the wires will be soldered to the LEDs.
Step 10: Gluing the LEDs to the Frame
After the LED plate has been made, it is assembled on the frame using some glue, the excess is removed with a napkin. It is recommendable to leave some weight on top while the glue solidifies.
Step 11: The Dimmer
If you wish, you can add a dimmer to your lamp with this circuit, it's a very simple and effective circuit anyone with a soldering iron can build, it's based on the popular 555 IC.
This circuit uses pulse width modulation to vary the time the LED stays on during a determined period of time, this makes the LED lights appear dim, but they're actually turning on and off thousands of times per second. In this case the dimmer is set to operate at around 2 kilohertz, so there won't be any annoying flickering.
I've designed and tested the circuit so you don't have to, all the components run stone cold even at full load.
You can download the Eagle files if you wish to print your circuit board.
Materials:
- 555 IC
- 47kOhm potentiometer
- 1kOhm resistor
- 10 Ohm resistor
- 220uF capacitor
- 100nF capacitor
- 10nF capacitor
- 2x 4148 diodes
- IRF540 MOSFET
You will also need a switch, to turn the power on and off.
Step 12: Wiring It Up
If you have decided not to use a dimmer, you'll just have to solder the positive wire coming from the power supply to the switch, another wire from the switch to the LED's positive and the power supply's negative to the negative of the LED's.
If you have decided to use the dimmer circuit provided in this instructable, the positive wire will also be soldered to the switch, but a wire must be soldered from the switch to the circuit's VCC, as indicated in the schematic (Step 10). The LED's positive wire will be connected to LED+, and its negative to LED-, which is the drain of the MOSFET transistor. The negative or GND will be connected to the negative wire coming from the power supply.
The 47k potentiometer middle lead must be connected to pin 7 on the 555, the lateral leads are connected to the diodes, it doesn't matters which way around, connecting them one way or the other will just change the direction in which you have to turn the potentiometer in order to increase or decrease the brightness.
To wire the lamp I used some wires I had laying around, I cut one meter of them and with the help of a drill I twisted them to make them look neater, I coiled the already coiled wires around a rod and installed them on the lamp, connecting the LEDs to the circuit. The double coil allows the wire to extend when the arms are extended too. A couple of screws are all what's needed to keep the wire attached to the arm of the lamp.
The holes for the switch and the potentiometer are drilled, and the wires are passed through a small recess at the bottom, the circuit board is secured in place with some glue. The switch and potentiometer are installed and soldered in place. For the switch, I used a file to carve the rectangular shape to make it fit.
For the PSU I'll use a 12 volt, 2 amp wall wart. Always check the amperage of the wall wart is higher than the amperage you'll be needing.
Step 13: Testing
The lamp is already finished, now it's time to do some testing and take some nice pictures :)
As you can see, the lamp is very bright, with 75 LED's the total power is around 14 watts, that is why I used a dimmer. That amount of light could damage my eyes in no time, with a dimmer I can use just the right amount of light for each case, saving energy and my vision.
Thank you very much for watching, have a nice day.
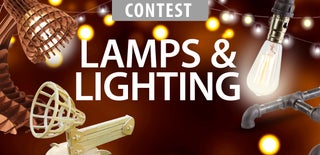
Participated in the
Lamps and Lighting Contest 2016