Introduction: Wooden Finger Engine
Put your idle digits to work with an amazing Finger Engine !
This incredible device :
- converts pointless finger tapping into continuous rotary motion !
- eases tensions and induces relaxation !
- provides healthy and wholesome diversion !
- and much much more !
Above all, a Finger Engine is just plain fun to have around. Young and old cannot seem to resist working its lever and getting it spinning - the faster the better ! The finger engine featured here is made of wood odds and ends with common home shop tools.
Step 1: Construction Details
The drawing shows the basic Finger Engine exactly to scale. The dimensions can be taken from this if you wish to make more or less the same version. However, nothing is particularly critical in these gadgets, so there is wide scope for variations. Available materials and tools also influence the final outcome of any project.
On this Finger Engine, the crankthrow offset is 1/2" and the two arms of the lever are approximately equal. This gives about 1" travel at the finger end, which seems to be an all around comfortable excursion for operating. After making the engine, the finger end of the lever can be easily cut a bit shorter for less travel if desired.
The height of the fulcrum pivot was taken to be 1-1/4" above the base. This gives a comfortable height for working the lever with my hand resting on the table as in the video. But this height also gives just adequate clearance between the lever and the base to prevent a finger from being pinched.
The 6" diameter flywheel is fitted with a 1/4" diameter shaft that is simply a good push fit into its central hole. Likewise, the crankthrow was drilled with a 1/4" bit and pushes tight onto the shaft with no additional means of securing required.
With1/4" I D ball bearings for the main shaft, the engine gets going easily, and will free-wheel for nearly a couple minutes if spun up good and fast. My friend Gary, who received one of these engines as a birthday present, added lead weight to the flywheel and now his free-wheels for almost four minutes !
The weighted flywheel also revealed two other advantages. First, Gary was able to add the weights to bring the wheel into virtually perfect balance. Wood is not homogeneous; its density varies with location. So even a perfectly cut wooden wheel will turn out unbalanced. This is not really a problem for a finger engine like this, but a balanced wheel does run a little sweeter. On the other hand, an unbalanced wheel adds character, and can be positioned relative to the crank so that when the engine coasts to a stop, the crankthrow rests more or less horizontally; the engine will be then ready to start turning as soon as the lever is touched.
The second advantage of the weighted flywheel is its increased moment of inertia. This is not only what gives it a longer free-wheeling time, but adds some resistance when driving the lever. This makes it easier to keep your finger in sync with the up and down timing. A lighter flywheel tends to "get ahead" of your finger timing so that you end up pressing down at the wrong time, or too long, actually slowing down the engine. So the lesson is to make the flywheel as massive as is reasonable. Pine wheels work just fine as the video shows, but a denser hardwood would present some advantage.
The finger lever was made from a piece of walnut, 3/4" wide and just over 1/4" thick. The end was slotted and drilled to accept the connecting rod which was mode up from a scrap of 1/8" thick oak. Each end was drilled a little over 3/32" to work freely over the crankpin and lever pin.
Step 2: Construction Sequence
The photographs show the placement of the various components on the base board which measures a little over 4 X 7". The upright pillar that carries the flywheel bearings was first glued in place with a good strong wood glue. After it had set, gussets were glued down. This seemed plenty strong enough, but one day during handling, the base slipped out of my hand and the fall knocked the bearing pillar clean off with ease. So it was carefully re-glued in place, and after setting, a 3/8" hole was drilled in from the underside and a dowel set in. In the several more Finger Engines I have since made, the dowel was put in right away!
The fulcrum pedestals for the finger lever were then glued to the base with the finger lever and pivot shaft in place to make sure they were aligned and the lever located in proper relation to the flywheel bearing pillar. The lever pivot shaft is 1/8" diameter steel rod. Gas welding rod is good inexpensive stock to have on hand for such uses, but the shank of a suitably sized nail would also serve the purpose.
The flywheel was rough cut from 5/8" thick pine, drilled 1/4" diameter for the shaft, and then finished to circularity on the disc sander. Then six equally spaced 1" holes were bored through for visual effect. The crankthrow was fashioned from 1/2" square softwood.
The ball bearings for the main shaft fit into counterbores in the bearing pillar as shown in the closeup photo; they need not be a tight fit because they are captured in place between the flywheel and crank throw . O-rings were used as spacers to prevent rubbing against the outer race of the bearing or the bearing pillar. Ball bearings are not essential for a successful finger engine. I have tried plain brass bearings myself and they work just fine, but free-wheeling is not nearly as long. A length of brass tubing fixed into a hole drilled through the bearing pillar serves as an effective plain bearing; cut the tubing a little longer than the 1" width of the pillar to provide clearance for the flywheel and crankthrow.
Step 3: L-lever Version
Another version of this Finger Engine is shown in the photos here and in the scale drawing. It features an articulated L-shaped driving lever. As can be seen in the closeup photograph, both arms of the lever are free to rotate about the fulcrum pivot shaft. The upright arm however incorporates stop blocks which bear against the end of the lower arm. This constrains the upper arm to make not more than a 90 degree angle to the lower arm. Hence a finger pushing down on the lower arm moves the upper arm with it to pull the connecting link and turn the flywheel crank. However, flywheel momentum cannot push the lower arm down. It actually is an automatic safety against wacking a finger that happens to wander below the lower arm. Because of this, the fulcrum shaft can be positioned closer to the base as shown, providing an even more comfortable height for the driving finger. All the other details are the same as for the basic Finger Engine. The wooden parts of both engines are finished with "Danish Oil". This wipes on and soaks in and is dry enough for handling in an hour or two.
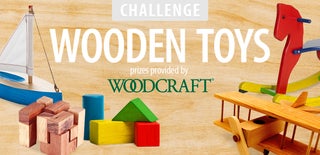
Participated in the
Wooden Toys Challenge 2016