Introduction: Aluminium Casting Foundry
Making a foundry for melting aluminium (Aluminum for the US) out of a 13kg propane gas bottle
why am I making an instructable that many people have already done? well I thought it was an amazing Idea but I feel there was some room for better documentation, and a few little changes such as a lifting mechanism for the lid and no fire cement for the refractory.
Step 1: What You Need
SAFETY NOTE: messing about with gas bottles or pressurized containers is very dangerous, do this at your own risk, but if you do decide to do it be safe, use your head, think about everything you do before you attempt to do anything. I have put in some tips as to what I have done in each step.
What you will need for this project
13kg gas bottle (UK), I got mine from freecycle.org from someone who didn't need it any more, in the US they are 12.4kg
Bag of sand
Fire clay
1.5 inch screws
a short length of steel pipe
nuts and bolts
a short length of hose
Charcoal
cotton wool
tools
----------
Angle Grinder with cutting discs and grinding discs
A file
Cordless drill and wire brush attachment
Arc Welder with 6013 rods (we find these rods easier to start and use with less sticking)
an outside tap
gas regulator if you're in the UK or you gas bottle doesn't have a tap
a steel rod if your gas bottle doesn't have a tap or you don't have a regulator
brush
rags for cleaning
marker pen
extension lead for working outside
hammer
------------------------
the bottle I'm using has the following dimensions
Propane: 13kg Patio Gas 580mm 315mm
Step 2: Empty the Tank
using your brush, brush any dirt or cobwebs off the bottle.
You need to make sure the bottle is empty, this bottle had a gauge on it which showed it to be empty but the weight of the bottle felt like it still had gas in it, and if you shook it you could hear the gas slosh around.
so i need to empty it, if you have a regulator or a bottle with a tap on it you can use this to empty it as far as you can, I would suggest you use the gas and not waste it if you can.
I didn't have a regulator and nothing that uses bottled gas so I have to vent it
WARNING: remember this is a pressurized container when you release the pressure it will change the pressure around you which can burst your ear drums, put cotton wool in your ears to protect them. also ensure you are in open space outside without ignition sources around, this could be anything that could make a spark or a flame.
I pushed my steel rod in to the top of the valve and pressed down, this released gas quickly, it slowed down as the gas got colder during the exchange process.
while I was doing this the air became saturated with propane which made me feel very dizzy so I wedged the bar under the handle of my shed.
once the gas slowed down I had a little fun, this you should never do, I ignited the gas, this was a very stupid thing to do, DO NOT DO IT, I videoed it so you don't have to.
the bottle got so cold ice formed on the outside of the bottle so much so that I could write in it.
you need to leave it for a long as possible, even when you can't hear gas escaping it may still be coming out, I would leave it over night with the bar in or the valve open if you have a tap or regulator.
I left my bottle for a few days after I emptied the gas out, when I pushed the bar back in it hissed, this was caused because of temperature changes.
at this point the bottle is NOT EMPTY it still has enough gas to give a fair bang, be careful.
now you need to have the valve open or the bar wedged in, then using your cordless drill or a hand drill, drill two small hole about 4mm in diameter. When I did this I was standing to the side just in case and I had the drill running slowly.
now you need to make the holes bigger, I only had a drill bit that was about 12mm. the two holes are to allow water in one and gas out the other.
using your pipe fill the bottle with water until water comes out of the other hole.
and guess what, it's still not empty there's still a little gas left at the top, I emptied half the water out then using a cooker lighter and keeping well back I ignited the remaining gas, it raged like a jet for a brief second, scared the life out of me.
leave the bottle half full of water this will help to weigh it down while you cut the top off.
Step 3: Chop the Top Off
If you can get a spanner around your valve I would recommend heating the bottle where the valve connects, they seal these valves with a liquid weld which will return to liquid when heated up, this will make it a little easier to get off. I would also recommend using a length of steel pipe on your spanner to give you extra leverage.
ok back to the cutting, you need to allow enough on the top of the bottle for about 2 inches of refractory, I measured up 5 and a half inches from the top of the centre seem and marked them with a mark pen.
cut along the marked line using your angle grinder with a cutting disc, I managed to con my brother in to doing most of the work for me while I cooked him dinner ;-)
once the top has been cut off grind off the sharp edges with a grinding disc
here is by brother grinding the sharp edges off.
Step 4: Handle and Vent
grind off the sharp edges and any excess metal left on the bottle.
mark out the hole for the vent and then cut this out with the angle grinder as well. Circle is 8cm in diameter and will be formed in the refractory later on, now all we need is a easy to cut hole so I put a square around it slightly larger which should help later on so the steel of the bottle doesn't heat up too much when the foundry is running.
place the handle in its position and put a spot weld it to hold it in place, now use your cordless drill with the wire brush to get rid of the paint around where we need to weld this will make it much easier to do, it is possible to do it with the paint in place if you start on a place without any but it's easier and you get a stronger and cleaner weld if you remove the paint first. use a hammer to get rid of the slag from the weld and make sure it's a good weld.
its worth noting at this point that if you won't have a welder you could just drill holes and use a bracket and some screws or bolts to place the handle. I don't have a welder but my brother was here to do some welding on my car so I got him to weld the handle for me.
I had some concerns that the handle might heat up so I cut it at an angle to try and keep as much steel out of the way of the vent as I could.
I marked a rough angle by hand and started cutting, then ground the cut using the angle grinder to remove the sharp edges.
here is a really short video of my brother welding.
Step 5: Preparing for the Refactory
we need to prepare the gas bottle for the refractory, we will need to put screws in to hold the refractory in place once it has dried.
turn the body of the gas bottle on its side and drill 3 holes in a line up the gas bottle, the first one near the bottom should be higher than the level the refractory will be, which is 2 inches thick so you want your first hole to be a bit higher up than that. also make sure your centre hole should be above the weld line.
do this all the way around the gas bottle, I have lined mine up with where the base connects to the body.
then you need to counter sink those holes to reduce the amount of screw head that sticks out.
then screw all the screws
you will need to repeat this with the lid, make sure you don't put them too close to the edge as they will end up sticking up above the refractory. you will also have to put some in the lid pointing down.
now we have the problem of holding in the refractory within the lid so it doesn't fall out, we will do this with some wire, making a web by wrapping wire around the screws, making sure we leave a void in the middle which will become our vent later on.
I wrapped the wire from the outer screws and down to the lower screws to create triangles, then all around the top screws in a circle, and then across from one top screw to the opposite one, all of this will reinforce the lid and hold it in place.
Step 6: Lifting Pedel
I thought about adding a hinge to the back but I thought it might not be wise as this may encourage me to reach over the hot furnace so I decided on a method where I could swing the lid off to the side.
I also didn't want to have to lift the lid by hand as this would be clumsy so I thought I would make a foot pedal to lift the lid and then I could use the handle to pull it aside keeping my hands and arms well away from the fire avoiding accidents.
So the first thing I needed to is create a frame for the pedal and lifting plate, I managed to salvage some metal that used to be racking that my next door neighbour had thrown out which is ideal for what I need.
I cut 2 lengths the width of the gas bottle plus the width x 2 of the metal I am using, and another 2 which are slightly longer to allow for movement.
I bolted these together to form a square frame, the rear of the frame i mounted upside down so there is a lip to hold the pole I am going to use to lift the lid.
I then drilled holes in the base of the gas bottle and bolted the frame to it so I had more of the frame towards the front.
Step 7: Air Inlet (the Tuyere)
I needed to cut a hole for the air inlet pipe (the tuyere), this should be slightly higher than the level where the refractory will go.
I first started using a hole cutter drill bit to cut the hole, without reading the packet, I blunted the bit as it was only for light metal use so I switched to the angle grinder. the hole was cut off centre so it was towards the back of the gas bottle, the purpose is so that when air is pushed in it will circulate around the inside.
I had some pipe in the pile of junk which I cut at an angle so it would be flusher to the refractory lining, and cut it to length.
I brushed both the pipe and the gas bottle ready to weld
Step 8: Lifting Pole and Brackets
I would be using the same pole that I used for the air inlet to make the lifter and the brackets.
using the angle grinder I cut a slit down the length of the pipe and then cut 3 pieces to about 3 inches long, 2 for the main body of the gas bottle and one for the lid.
using a file I make sure there wasn't any sharp bits, then pulled them open slightly to allow a piece of the same pipe to fit inside them.
Step 9: Finishing the Lid and Welding the Air Inlet
Welding the brackets was tricky as the pipe I was using was thin walled but I managed to pool the weld between the pipe and the gas bottle.
The original plan was to weld a cap on the top of the bracket that was attached to the lid so the pipe at the back would be loose inside but would lift the lid, this didn't work as expected and only lifted the back of the lid, I then inserted a larger pole and welded that to the bracket and lid, this worked much better. I also cut the rear pipe to the height of the handle, this will help later with the refractory mix when we ram it in the lid.
this is the first time I have used an arc welder so my welds are not too pretty but they hold up, I will get better with more practice.
Here is a video of the lift mechanism working.
Step 10: Testing the Refactory
The mix I will be using is the same as what David Gingery specified in his book about making a home foundry.
2 Parts Sand
1 Part Fire Clay
Measured by volume not weight.
here is a video of the test I did, I made up the mix and rammed it in to a large tin (originally for baby milk, in the US it's about the same size as a coffee tin) so I basically made a mini furnace. Using my girlfriends hair dryer for blowing air in the inlet.
so by the colour of the glow on the tin I can assume that I was getting between 800 - 900 degrees C aluminium melts at around 660 degrees C so it looks like the charcoal furnace will be Ideal.
In the video I say the top is crumbly, it turns out it was just a little sand dust, and it was solid enough.
Step 11: Making the Inner Mould
we need to work out what the diameter of the inner mould should be to do this I take the diameter of the gas bottle and minus off twice the width I want the refractory to be which is 5cm twice that is 10cm the width of the gas bottle is 31.5cm so our inner mould needs to be a 21.5 cm in diameter.
On a scrap of wood or board draw a circle with a diameter of 21.5cm and draw 2 D shapes on the inside of the circle which will form a handle in the middle of the circle.
drill holes in the points of the D's, use the holes to start the jig saw and cut out the 2 D's then cut out the circle.
You need to make 2 of these so just trace round the original and cut it out in the same way, I cut out 3 with the intention of using one in the centre section, I was originally trying not to use a sheet of metal but my attempts at using hard board failed so I reverted back to having to use the metal to form the outside of the mould.
Now it's important when working with sheet metal to wear gloves, I got over excited and forgot this and took a chunk out of my finger which bled through the plaster I put on it. :-( see the picture as a reminder to wear gloves.
what you need to do is wrap the metal around the 2 wooden forms, using duct tape to hold it while you roll it, this requires a fair bit of strength depending on the thickness of the metal your using.
The idea of this mould is It's suppose to be collapsible so it can be removed without damaging the refractory, according to David Gingery's book on making a home foundry, we shall see.
Step 12: Mixing and Ramming the Refactory
the refractory is mixed in a ratio of 2 parts sand 1 part fire clay by volume.
Using a small bucket measure out your ingredients in to a mixing container and mix them together, your aiming for the sand and clay to clump together when squeezed but not be wet or sticky, it shouldn't stick to your hand and it should break cleanly.
shovel some of the mix in to the bottom of the gas bottle and ram it down using a piece of wood, you need to make sure you ram this very hard and get all the air out you can. You need to do this until the bottom is to the level of the bottom of the air inlet pipe, and fairly level.
I started this with the screws still in place but they seemed to be getting in the way so I took them out and as the refractory got over there level I put them back in.
Place the inner mould in the gas bottle and try and get it as centred as possible.
using a garden trowel put some mix in around the mould and ram it down, you may want to use a hammer to tap the wooden ram to make sure it's packed in tight. you want to build up the outer wall in layers don't just fill it up then ram it do it in parts until you reach to top.
if at any point you wish to stop, I stopped because it was late in the evening, cover your work with foil to keep the moisture in you don't want it to dry out until you're ready to fire your mix.
the flash on the camera has made my sand look yellow, it's not yellow it's actually a red / orange colour.
for the lid I put duct tape over the hole and popped a brick under the hole, using a postal tube as a hole mould I then rammed as much as I could in to the lid. to remove the postal tube just slowly twist it and pull gently upwards as you do.
Step 13: Removing the Inner Mould and Firing
to remove the inner mould cut the duct tape off the top and remove the wooden spacer do the same at the bottom, cut the duct tape on the side.
You will have to squeeze the metal cylinder to part it from the side and carefully lift it out, this might be a little tricky and will need a little strength.
ok now comes the final bit, this will take some time, you need to start a fire in it, you can do this with charcoal and lighting fluid like a BBQ, I just put some newspaper and the scraps of wood from cutting out the wooden spacers I also broken up and put the spacers in.
you just want to have a fire in it for now, do not start the hair dryer through the air inlet, you want the refractory to dry out gradually if you heat it too fast the steam will blow out bits of the refractory and you will get large cracks. You might get a few cracks in your refractory but that's ok they shouldn't be too big.
Run it for a couple of hours without extra air and without the lid on, we need to harden the lining of the bottom section first. then put the lid upside down on top, this will stop the refractory just falling out and the heat from the fire will help harden the lid.
now you can put your hair dryer on through the air inlet on low power, once the lid has dried out enough, put it on the furnace properly and leave it for about half an hour with low power on the hair dryer then turn it up for a few hours, the lining should glow.
here is a video safety tip for when your firing your refractory.
here is a video I did while firing the refractory.
Step 14: Test Melt
I had a couple of scrap pieces for the test, some off cuts of rod and rails, a coke can, an ornament and some other little bits.
once all the bits had melted I left it a little while to get hotter so it wouldn't just cool in the crucible, unfortunately I hadn't considered the ground being cold so some of the metal started to set in the bottom which made me put down the camera.
I managed to cast 2 ingots from what I had, it would have been 3 had the metal not started to cool in the bottom of the can, but the point is that it works.
from these tests I have concluded that best fuel would if you're using charcoal like I am then the briquettes are the best to use, the lump wood charcoal produced a lot of sparks. You could of course use propane if you made a burner.
here is a video of the melt and the pour.
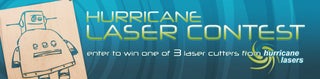
Finalist in the
Hurricane Lasers Contest