Introduction: (Another) Scrap Ends Table
If you're like me and love working with reclaimed wood, odds are that you probably have a ton of wood scraps left over from your past projects. After moving to New England, I noticed that pallets seemed to be everywhere up here, so I began using them as a medium to get more experience wood working. Naturally, my garage ended up looking more and more like a scrap pile of pallet wood (some left-over scraps from past projects, some from dismantled pallets that cracked during disassembly). If you're still at the stage of trying to collect reclaimable pallet wood or would like more information about how to find, inspect and dismantle pallets, check out my Pallet Bible Instructable.
I had seen and been inspired by mikeasaurus' Scrap ends table previously, but due to the type of pallet wood that I had lying around, his design and process didn't fit what I wanted or was able to do. So I set out with the intention of building something that was hopefully as handsome as the table that Mike put together. We'll see if that was a success...
Tools Needed:
Saws: a miter saw is key here, and you'll find that a jigsaw and either a table saw or circular saw might come in handy as well
Planer (I'll address this more fully in step 2, but the type of planer you use will save or compound potential headaches)
Sander (I prefer a random orbit sander, but this is up to you)
Clamps (and more clamps... pipe and/or bar clamps come in very handy during the gluing stage - make sure they're long enough to accommodate the width of your table top)
Hammer
Safety Gear (ALWAYS use proper safety gear, including eye protection, a respirator or dust mask, gloves, and ear protection when necessary)
----------------------------------------
Materials Needed:
Scrap Wood!! (I used about 20-25 pallet board pieces, some cracked or damaged, and several other scrap pieces)
Wood Glue
Finishing Nails (I used 2 1/2")
Stains and Oils (depending on how you want the final product to look) and rags to apply them
Step 1: Gather Your Scraps
Since I have become a pallet hoarder over the last 6 months, I have not only dozens of good quality dismantled pallet boards sitting in my garage, but also tons of splintered, cracked, or otherwise damaged boards from dismantled pallets. No matter how good you get at disassembling pallets, you're bound to crack a few here and there, and most of the time these become unusable for the average project. But they're perfect for this one!
I'm going to give the standard disclaimer on pallet wood that I put into all of my pallet-fueled projects, as a lot of it is valuable info that I learned the hard way... Pallet wood is easy to come by (and usually free), has character and is fun to work with. Always ask before taking pallets from a business (even if they're sitting out back by the dumpster), as many companies have pallet suppliers that reimburse them for their used pallets, and taking them without permission is "technically" theft. I'm not saying I haven't done it before, just be safe and courteous. I prefer using a circular or reciprocating saw to cut off the end stringers (the perpendicular posts that hold the pallet boards on the top and bottom), and finally using a prybar to patiently separate the planks from the middle stringer. Key word here is patience - go at the nails from all angles to avoid cracking and ruining your pallet wood.
But this project is by no means limited to pallets. Any piece of scrap wood that you have is in play here. It's good to have a general idea of what you want the dimensions of your table top to be, as that will determine exactly how much wood you need to gather. Based on the sizes of my various scrap pieces, I went with 17"x17". Keep in mind that you can piece together shorter boards to make up the length that you desire for your table.
Since you'll be assembling this table with the boards lying upright as opposed to flat, the only real prerequisite for a piece of scrap wood here is that one of the long thin edges must be fairly level - this will become part of the top of the table. You can always use a table or circular saw to level out the edge of a board, but these are all necessary considerations when choosing your wood.
Step 2: Planing, Cutting, and Sanding
Once your wood is gathered, it's time to transform these mangy scrap boards into useable pieces of wood. When you get to the point of assembling and gluing your table top, you'll want all of your boards to have a flat top and level sides. Any warping or unevenness will make gluing the 20-30 planks of wood together an even tougher task, and it goes without saying that you'll want your table top to be nice and flat as well.
Prior to this table build, I had never used any kind of planer before. Since I'm still getting my woodworking-legs, I did some research and decided that I was going to test my mettle with a jack plane. $40, 60 minutes, a couple dozen four-letter words and two trips to Home Depot later, I was the proud owner of an electric hand planer... I can't say that I gave the manual plane a fair shot, but it became obvious to me that the necessary understanding of setting the blade position in the throat and mouth of the plane, knowing the right cut depth to set on the lever and just having a solid general understanding of the technique needed to plane wood was all beyond me. For about $5 more I was able to get a fairly simple electric hand planer that did the job wonderfully. I have no doubt that someone with the experience and feel for manual planers can do wonderful work with them, but for the admittedly-amateur woodworker the electric plane is a no-brainer. Here's the (fairly cheap) one I got, though I'm sure that in the long run you'd probably have better luck with a more expensive name-brand.
With 15-30 planed, straight boards (depending on the size of table you want to build), it's time to cut all of your pieces to size. Once again, I decided on making a 17" x 17" table, mostly due to the fact that I had enough scrap boards to accommodate this size. This step is greatly aided with the use of a power miter saw, and if you have a big enough one you can even cut multiple boards at the same time. One thing to note is that you're going to want these boards to be as close as possible to the same length, so precision is key here.
Once they're all cut to length, it's time to tackle my least favorite task in woodworking... sanding. Sanding pallet wood can be a potentially hazardous task. Pallets are used in transport all over the world, and you can never know exactly where your pallet has been and what it may have carried. You should always use a respirator or mask when sanding wood of any kind, but this is especially important here. Again, check out my Pallet Bible instructable for a ton of useful information about how to find safe pallets and how to prepare them for use. You're going to need 5 of the 6 sides of your boards to be totally smooth to the touch and completely level for the table to fit together properly, but as you can tell from some of the pictures in the other steps, I wanted the bottom side of my table top to be unfinished and uneven. Keep this in mind during the oh-so-enjoyable task of sanding.
Step 3: Organization and Staining
Ok, now the tedious part is over... You've planed, cut, and sanded all of your boards and now have a bunch of clean, ready-to-use pallet boards for your table top. Depending on the look you want to achieve here, the sky is the limit to your design. Whether you want to leave your table with a natural all-wood look, add in a few stained accent pieces, or go with a more multi-colored approach, you'll need to first figure out the order in which to set your boards. Keep in mind that although 5 of the 6 sides of each of your boards are finished and clean, the bottom of each is still raw. This should influence how you determine to assemble your table. Do you want a seemingly random assortment of tall and short pieces, or do you want a sort of gradient from short to tall? Also, as you'll see in the assembly phase, you'll need two end pieces that will sit on the very outside of your leg frames. Choose a couple of interesting pieces specifically for this role. Once you've lined up your boards in the order you'd like, it's time to get to staining.
With as many pieces of scrap wood as I have lying around, I have almost as many cans of wood stain from past projects. So I thought that I would add some color and tone to the table top, and mix and match different stains for each board. For this process, I used a combination of water-based and oil-based Minwax stains as well as a few different colors of Danish Oil. I love working with the Danish Oil, as the application process is easy and not nearly as messy as traditional stains, and it really seems to bring out the shades of the wood grain in the piece you're working with. I tend to prefer using lint-free rags when applying stain, rather than a brush or sponge. Rags will allow you to get a more even finish than other methods, and you have a lot more control of how you apply your stains. Also, be sure to do this task in a well-ventilated area, and preferably with some sort of respirator just to be safe.
Step 4: Build Leg Frames
Frames:
I struggled with how I wanted to attach legs to this table top, and went through a number of different design concepts. I considered building sides out of sheets of plywood and routing a design into them. I thought about attaching simple leg posts to the sides for a cleaner look. But ultimately I decided that - since this is a table meant to be built from scrap materials - I would build sides with scrap wood as well.
I had a few different lengths of furring board laying around - some 1x2" and 1x3". With these I decided to make two frames for the sides, and would inlay even more scrap wood pieces in the sides (I know, I may be overdoing it here...). The beauty of this design, however, is that from the perspective of the table top, these sides would look like just another scrap wood board. So I knew that the top pieces of these frames would need to be 17" long (to correspond to the rest of the table top), and decided upon a table height of 26". My 1x3" board pieces (which were really more like 1x2.5") would serve as the top pieces and my 1x2"s would be the sides.
Compensating for the width of the top pieces, I cut four lengths of 1x2"s to 21". In order to ensure that the two table sides would be identical in height, I lined up all four of my 1x2"s after cutting them to size and shaved off a few millimeters to square them all up precisely. With all of the pieces cut, I got out my pocket hole jig to help attach these pieces together. Though not necessary, this jig is a huge help when assembling furniture and picture frames to get a stronger, less-noticeable joint. With my holes pre-drilled, I applied a light stain to these pieces and assembled them with screws and wood glue.
Inlay:
For the scrap inlay that I wanted to do with my leg frames, I dug into the bucket of small scrap wood that I knew I had always been saving for a reason... Most of these pieces are too small to have much more than a decorative use, but they work perfectly here. I played around with these trying to find a combination of pieces that would fit snugly into the wood frames that I just finished, and had to take a jigsaw to a couple of them to shave off a centimeter here or there to make them fit. Once I was happy with the arrangement, I sanded them down, stained a few of them with a little color to match the table top, and set off to glue them. After letting them sit the proper amount of time, you can scrape off any excess glue and set these aside. Be conscious of the surface that you're letting these dry on after gluing, as some of the wood glue will naturally seep through and potentially attach your leg frame to your workbench.
Step 5: Assemble Table Top
Here's the step we've been waiting for. With all of your pieces, cut, sanded, stained and arranged, it's time to see it all come together. For this step you're going to want a ton of wood glue and some finishing nails. Though the wood glue will produce a strong enough bond to hold this table top in one solid piece, the nature of this design makes it difficult to glue all of the pieces at once. Since you're going to want to do your best to ensure that all of your boards are completely even on the sides and top, it is going to save you a lot of frustration by doing this table top in sections.
I decided the best way to go about this was to start at one end of the table top, and work my way to the other. My overall process was to glue four or five of the boards together one at a time, clamp them down, remove any excess glue, insert two or three nails along the length of the boards, and give the glue a minute to dry. Most wood glues require very little time to harden, and inserting your finishing nails here will allow you to continue working your way down the table top without worrying about previously glued sections shifting or coming apart.
TIP:I suggest keeping a small container of water and a few paper towels handy during the gluing process. As you assemble and clamp your glued boards together, excess glue will be squeezed through the cracks, and if you don't remove this the process will become unnecessarily messy and may effect the final look. Most wood glue hardens clear, but I still prefer to remove this whenever possible. Wet paper towels will streamline this process significantly. Also, keeping a small screwdriver or file handy will allow you to scrape excess glue out of any cracks
In order to keep your boards in line with one another, having a 90º L-ruler will allow you to line them up precisely as you glue. So, starting at one end, take two boards and apply a very generous amount of glue. Line them up, press them together, and continue until you have about five boards in all. At this point you can take a few clamps (three spaced out along the boards is ideal), and tighten them down. For this next step, I used 2 1/2" finishing nails (these are best as they have no nail head and you can pound them all the way in) but any size will do. Nail in a couple of these while the boards are clamped together. At this point you can wipe off some of the excess glue while the boards harden. The nails will allow you to remove the clamps and continue down your table top without waiting as long for your glue to dry.
TIP:I nailed a couple of scrap 2x4 pieces to my workbench to serve as a place to set my boards while they were clamped together (see picture). With three clamps attached to your in-progress table top, and since the bottom of your table top is not even, you don't have a flat side to lay your table top on while it hardens. To make things harder, nailing in finishing nails is near impossible without having an even surface to set your table top on. A couple of properly-spaced 2x4's allow you to sit your boards down while they glue and insert your nails safely.
TIP:Keep some light tape (like packaging tape) handy while inserting nails into your boards. You can use some thin strips to indicate where nails are in your table top as you progress further along. This will help prevent you from hitting a hidden nail in a previous section of your table top, and keep some distance between your nails to avoid splitting any boards.
Continue working your way through the table top in sections of four or five pieces at a time until you've come to the end. Remember that you want to keep your two end boards set aside until the last step. Once the table top is all glued and nailed together, you're ready to attach the leg pieces.
Step 6: Final Assembly
With your table top and leg frames all done, it's time to put everything together. As with any table, you want to confirm that your legs are evenly aligned when attaching to ensure that your table doesn't have any wobble. Similar to your table top, we're going to use wood glue and nails to attach your legs frames to the sides. Ensure that you have the right sides of your leg frames facing outward, and attach them to your table top. Finally, you can take your end pieces and glue them on to the ends of your leg frames, concealing the nails that you just hammered in. After clamping these down and allowing them to dry for a few minutes, you should be all done!
I decided not to put any clear coat on my table as I enjoy the flat appearance, and the finishes that I put on to my table top boards should help a bit to keep the wood sealed. That's it! I hope yours turned out as you intended, and please post any pictures of finished examples that you make!
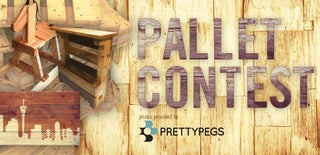
Participated in the
Pallet Contest