Introduction: Bicycle Wheel Truing Stand
This is a simple truing stand for bicycle wheels. It's no-frills so it might not appeal to professional bike mechanics but it's perfect for recreational bikers who might only build a few wheels a year. It's made from just a few pieces of steel so it's cheap, and it breaks down nicely for storage.
I made it at TechShop.
www.techshop.ws
To create this wheel truing stand you’ll need the following raw materials:
- 36 in. x 2 in. x 1/8 in. steel angle
- 36 in. x 1 in. x 1/8 in. steel angle
Steel angle (aka angle iron) is just a length of steel that is bent at a 90 degree angle along its long axis, forming an L in cross-section. It’s pretty cheap and you can get the two pieces you need from your big-box hardware depot for about $20.
You will also need the following tools (all of which are available at TechShop):
- Angle iron bender/notcher
- Vertical bandsaw
- Disk grinder or hand file (to clean up rough edges)
- MIG welder
- C-clamps, welding magnets
These are tools that I had available to me at TechShop so that’s what I used. This wheel truing stand is pretty simple so other metalworking tools and techniques can be used to build this project.
Step 1: Make the Parts
The first few operations are done on the Iron Worker, a machine that can punch, shear and notch metal. Here’s an Instructable with more info: https://www.instructables.com/id/How-to-use-the-metal-worker-at-Techshop/
Using the Iron Worker’s shear function, cut 2 x 14.5 in. lengths of the 1 in. steel angle. These will become the uprights to hold the wheel.
Using the shear function, cut 2 x 14 in. lengths of the 2 in. steel angle. These will become the base for the truing stand. Next, using the notching function, cut out 6 inches in the middle of each base piece. This notch is where the uprights will go and the 6 inches is enough so you can handle wheels with up to 135 mm spacing. If you want to build wheels with a larger spacing (e.g. tandems), you’ll need to adjust accordingly.
The notcher will leave a bit of a raised edge so you’ll want to even it out a bit, especially near the ends where the uprights will go. I used a hand file to do this.
Use a disk sander, grinder and/or hand file to clean up any rough edges.
Step 2: Notch the Uprights
Using the vertical bandsaw, cut a notch into each end of the upright. Each leg of the notch is roughly half an inch, it doesn’t have to be too exact, just big enough for the wheel axle to rest in. Since the two uprights need to be identical to each other (not mirror-images), cut the notch in the same side for each upright.
Line up the notches back to back, clamp the uprights together and use a hand file to make sure both notches are the same size and depth.
Step 3: Assembly
All the parts are now done, time to do some assembly.
The idea is to weld one upright to one base piece, then repeat so you end up with two identical units. You could do these individually but I wanted to make sure the uprights were even and the notches lined up so I clamped everything together and tack welded the parts first.
Clamp the two uprights together, making sure the notches lined up. Position the base plates in the fully-closed position and insert the uprights. Because we want the notches to align, the faces of the uprights and base pieces do not overlap anywhere. The two pieces only have about 3 inches where edges butt up against faces. It’s a bit difficult to describe, just take a look at the pictures.
Fiddle around with clamps, welding magnets and shims until everything is plumb and level, then tack weld. With all the pieces clamped together it can get confusing, make sure you understand how it’s all supposed to go together so you tack the right pieces together.
Now unclamp everything and complete your welds.
Step 4: All Done
And there you have it, your complete wheel truing stand. Just flip one base/upright unit around and position the base pieces back-to-back, slide them side-to-side to get the desired spacing between the uprights and clamp the base pieces together. The stand is pretty stable all by itself but you can clamp it to a workbench if you want.
This is a no-frills wheel truing stand and lacks any calipers or guides to show wheel trueness or roundness. I currently use the extension nozzle from a can of lubricant to serve as a guide. Works well enough for the two or three times a year when I build a wheel. If I get ambitious I may create a set of calipers that attach magnetically to the base.
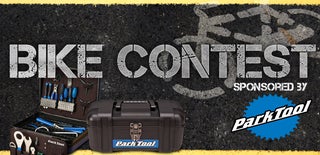
Runner Up in the
Bike Contest