Introduction: Carbon Fiber Bike
I AM NOT A PROFESSIONAL FRAME BUILDER , this is my first bike build.
BUILD AND RIDE AT YOUR OWN RISK
I am, however, a student in Polymer and Fiber Engineering at Auburn University with access to a composites lab. We have all sorts of fabrics including carbon fiber, fiber glass, kevlar, and all of those in prepreg as well. I got interested in biking from my dad and have always loved to make things. I found a couple instructables on bamboo bikes and decided i would make something similar. I figured I could make a carbon fiber bike if I replaced the bamboo tubes with carbon ones. After a couple failed attempts I made some decent tubes, it really isn't that hard.
Completing the bike has taken about 4 months, but i could make one in three weeks if i were to spend a lot more time on it. I decided to make a fixed gear because of its simplicity. I don't have to worry about a rear brake bridge, clamping the front derailleur on the seat tube, and all of the cable stops. Plus I already have a geared bike.
I didnt know much about composites or bike building when i started this project, but I know a lot more about both now. Having an experienced frame builder also helped a lot. Having a lot of contacts for tools or advice is a must for this.
I encourage anyone who attempts this project to do a lot of research before hand, I did for about 2 months and asked lots of questions to anyone who knew anything about bikes. I used Sheldon brown's website a bunch for info. They have a bunch of singlespeed and fixedgear stuff as well as basically anything to do with bikes.
Some useful sites:
http://www.bikeforums.net/showthread.php/596392-Bambooo!?daysprune=-1
https://www.instructables.com/id/How-to-Build-a-Bamboo-Bicycle/
https://www.instructables.com/id/How-I-built-a-carbon-bike-frame-at-home-and-a-bam/
https://www.instructables.com/id/Bamboo-Bike-2/
https://www.instructables.com/id/Bamboo-and-Hemp-Road-Bike/
http://www.bikeforums.net/showthread.php/659162-Bamboo-frame-Worklog-MADE-IN-BRASIL?daysprune=-1
https://www.instructables.com/id/The-simplest-bicycle-framebuilding-jig-I-could-com/
There are two things that you will learn aside from dealing with composites and building bikes; patience and the hatred of sanding.
This is not a project for everyone and not a project you can do in a weekend.
Oh yeah, DON'T GET YOUR BOTTOM BRACKET SHELL BACKWARDS LIKE I DID!
Step 1: Making the Jig
You need:
2x4s (scrap will do)
3 "L" brackets (I think 5 inch long)
3 feet of threaded rod (I used M10 x 1.5)
3 cone shapes that fit into the head tube and seat tube
I used a pvc mandrel to hold the bottom bracket shell
6 lock nuts (for rear drop out assembly)
4 regular nuts (for head tube and seat tube assemblies)
6 washers (for rear drop out assembly)
There are 3 vertical 2x4s that hold the head tube, seat tube, bottom bracket, and dropouts. There is a second piece of 2x4 on the back of where the bottom bracket hole goes and where the rear dropout hole goes. I got the measurements from an old bike frame. the cones were made on a lathe out of aluminum stock, I threaded a hole in them so i wouldn't have to use more lock nuts. I drilled a hole for the bottom bracket shell mandrel with a hole saw ( you need a tight fit so it wont move), the pvc was turned down from 1.5 inch so that the bottom bracket just fit. The droputs fit nicely onto the M10 rod. I drilled a hole through the 2x4s for the rod and put a washer and lock nut on both sides. the dropouts are secured with a washer and lock nut on each side. If i continue to make bikes I'll upgrade the jig to extruded aluminum, that way I can make different sizes.
Step 2: Metal Parts
What you need:
Head tube (got mine from here . It is for a 1-1/8 inch steerer, 170 mm long)
Bottom bracket shell ( was also ordered from Henry James, i did not get lugs on mine)
Rear drop outs (from here )
some scrap steel tubing (1/2 inch diameter)
I got a friend (who is a frame builder) to weld some steel tubing onto the dropouts to have extra space to wrap carbon around for a good bond. We took a file and a 3 inch section of pipe and filed a slot down the pipe (about an inch so it has a slot that the dropouts can fit into). I sanded the head tube and bottom bracket shell with really rough sand paper. The extensions on the dropouts were threaded with a die that is too big for them(so not to cut deep) to add a mechanical bond between metal and epoxy/fibers.
Step 3: Making the Tubes
You need:
carbon fiber fabric (I used a light twill fabric and some unidirectional fabric as well)
peel ply (resin wont stick to it)
epoxy resin
fiberglass fabric for metal tubes.
3 ft of pvc tube ( here the inside diameter will determine how big your tubes are)
2 pvc end caps
10 or so pipe clamps
bike innertube
long bar clamp
acetone (for clean up, it dissolves any uncured resin so you can clean it off of scissors or something)
I used two different sizes of pvc; a 1-1/2 inch ID tube for the top tube and down tube and a 1-1/4 inch tube for the seat tube. Cut the pvc tube to about 3 feet long. Now cut the tube down the middle(from end to end, a band saw works best because it has a thin blade) mark and end to ensure proper alignment when making a carbon fiber tube.
Cut the bike innertube to 4 feet making sure the valve is close to one end( about 8 inches from one end). Put contact cement on the inside of the tube on both ends and press them together when tacky, now tie a knot where the contact cement is. This creates a good seal for the tube when it is inflated.
DO A DRY RUN BY INFLATING THE INNERTUBE IN THE PVC PIPE WITHOUT ANY FABRIC
Wrap the innertube in two layers of peel ply. cut holes for valve.cut some fabric to make the tube (I went with 26 inches wide by however many layers you want in the tube) I used the light twill fabric on the top tube and down tube, about 5 layers on each( circumference of a circle is pi x diameter). For the seat tube I used a unidirectional fabric for the 2 inner layer and the twill for the outer(you may have to make a couple tubes because you need the inside diameter to be within the range of available seat tubes(25.2mm to 27.2mm, I took my seat tube to a local bike shop and they had one that fit nicely)
Lay the carbon fabric on a surface (we have a disposable waxed paper covering on the tables) to wet it out. Make sure you wet it out thoroughly (the inflation process will squeeze some excess resin out). Then wrap the fabric around the inner tube. Make sure it is tight because you have to place it in the pvc tube and clamp it shut without the pvc pinching the fabric. Wrap another layer of peel ply on the outside of the wet fabric (so it wont stick to the pvc).
Make sure the innertube is inside the pipe, then place the end caps on the tube and clamp the tube together. Then tighten the pipe clamps spaced evenly along the pvc pipe. Inflate the innertube to about 30 psi. Much higher will pop the inner tube in my experience.
For the stays i wrapped the unidirectional fabric around a wooden dowel.first wet out the fabric and let it sit for about an hour(or until the resin is tacky) then wrap it around the dowel, this makes sure the fabric is tight and wont slip on itself, then I braided( with a braiding machine) around the dowel and fabric to compress it ( it makes a nice pattern). you can do this by hand( not braiding but compressing with a yarn)
for the metal tubes i first wrapped them in fiberglass fabric to prevent galvanic corrosion. I did some reading on this and found that everyone has a different opinion of how fast it occurs. to be safe I insulated the metal parts with fiberglass. make sure to remember the dropouts later). I put the tubes in a vacuum bag to ensure compression( you could do this with the electrical tape trick on some other bike instructions)
Step 4: Notching the Tubes and Setting Up the Bike
Now you have to line up all the pieces to ensure a straight frame. The farthest hole on the L bracket turned out to be 115mm out from the jig so I set up everything else from those. the spacing on the rear drop outs is 120 mm(for a singlespeed bike). so the inside of the drop outs should be 115mm minus 60mm and 115mm plus 60mm from the jig.
I used a drill press with a hole saw (use a hole saw close to the same size that the tube will notch into) to make a rough cut on the tubes then used another tube with sand paper wrapped on it to do final notching. Carbon fiber dust is harmful if a lot is inhaled. Wear safety clothing (respirator, goggles, longsleeves). If you get the dust on your skin it will start itching really bad, scratching makes it worse. it goes away eventually but if your clothing touches the affected area it will drive you crazy.
Notch the tubes after you have finished the head tube and bottom bracket shell.
Put grease on the threads for the bottom bracket so no resin will get into the threads. Any thick grease will work.
I used some resin to glue the tubes together. We had some milled fiberglass that I added to thicken the resin so it stays on the joints better.
Step 5: Wrapping the Joints
Now the fun part, wrapping the joints in carbon fiber yarn. If the resin were to get on the threads it would be really difficult to remove the bike from the jig later (I need to redesign the jig). I used teflon tape ( maybe you can use electrical tape) on the cones and some on the dropouts and all of the threads. I covered everything in masking tape as well.
Sand all joints prior to wrapping.
Mix up some resin ( not too much about 80 grams). Apply a thin coat of resin to the joint prior to wrapping with a paint brush( maybe a 1 or 1-1/2 inch brush). Wrapping each joint takes a while so the resin might kick off while you're wrapping if you have too much. Start wrapping! i wrapped the yarn over itself to secure it in place. Wrap the whole joint in one layer then apply more resin. Use a stabbing technique (hold brush perpendicular to surface and stab bristle ends into the carbon yarn) to ensure you have saturated every fiber. Pull the yarn tight with each revolution around the tube. When you have wrapped two or three layers cut the yarn, unwrap one revolution and slide the end of the yarn under the previous layer then pull tight. This will lock the yarn in place. Now you can apply a layer of electrical tape to compact the yarn to save time on sanding later. Make sure to pull the tape off before the resin has cured.
Sand all of the joints after at least 24 hours for the resin to cure. You dont have sand until there isn't any untouched place, just most of it. repeat the wrapping process. The second time i added some fabric to reinforce the joints with "zero" direction yarns. this means the yarn runs parallel to the tube and not perpendicular like the wrapping. Parallel fibers are very strong in a bend only in one direction, if you bend perpendicular to the fibers it wont take much to break the structure.
Step 6: Finishing the Frame
Once you have wrapped the joints with a bunch of carbon, its time to finish the frame. After I wrapped my final layer of carbon on the joints, I wet out the entire frame with epoxy. I then sanded the entire frame with 80 grit to take down the high spots, then with 180 to get rid of those deep scratches. I was able to get rid of most of the deep spots on the tubes after this step. It is not necessary to sand out every spot, it will blend into the next layer of epoxy. Make sure you don't sand into the fibers as this will ruin the carbon fiber look. When the sanding dust turns gray or black you know you have sanded to just the right depth.
If you wet out the whole frame while it is upright in the jig, the resin will flow to the bottom bracket area. So suspend your frame above the table as I have done and flip it over about every 5 minutes, or if the resin is about to drip off the frame turn it over. You will have to do this for about 2 hours but it is well worth it. If you notice a dry spot within the first hour you can use a brush to lightly add resin. After an hour though the resin gets too tacky to brush anymore but it will still run. I tried to use a heat lamp to cure the resin faster but it just made it run more, bad idea.
Let the resin cure overnight.
Step 7: Piecing Together the Bike
At long last, it is time to put the bike together. If you have made it this far I congratulate you, I know it wasn't easy. There are some things you must do now.
You must face the head tube! There is a special tool for this that thankfully my friend, the frame builder, had. This tool scrapes a little off both ends of the head tube to ensure that the surface the headset seats on is perpendicular to the axis of the head tube. Then you can use another tool to press the headset into both ends of the head tube. Next I had to seat the lower headset race onto the front fork. We used a spare head tube and a mallet to push it all the way down the steerer tube. Next you need to cut the steerer tube to length. put the fork in the head tube with as many spacers as you need and the stem in place, make a mark at the top of the stem and cut about 4 mm below the mark. Next you have to get the star nut in the steerer tube. This took a star nut tool and some persuasion with a hammer. Install the front fork now.
So I got the bottom bracket shell backwards when I made the bike, such a rookia mistake! That is why in the picture below i have the chain on the left side. Left side drive? That's insane! I didn't have a lock ring at the time so I couldn't push forward on the pedals but i could resist them to tighten the rear cog. Also the thread on the pedals is backwards this way, your pedals will unscrew while you are riding if you have it like this! I put the cranks on the correct sides after a little while of this. On the bottom bracket itself there are two cups, a press fit one and a dinky plastic one. I have the dinky plastic on the drive side now. eventually this will break because of the torque applied to it. For now I have to live with it. Eventually I may cut the shell out or build another frame.
Go to a local bike shop to get a seat tube clamp, stem, wheels, cranks, a seat, rear cog with lockring, chain, and anything else you need to start rolling.
On the first rides I didn't hear any complaint from the frame, like popping or cracking, which would mean some fibers are breaking, not good. Riding a fixed gear for the first time is a weird experience, you can't stop pedaling! It not so bad after a while, you realize coasting is not necessary.
I will get a front brake for the bike soon. Safety is number one in my book!

Runner Up in the
Spring Bike Contest
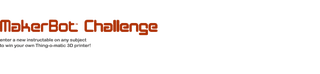
Participated in the
MakerBot Challenge