Introduction: How to Build a Medium Sized Biogas Plant
Long back I have posted an instructable on how to construct prototype of a Biogas plant, using 50 liter capacity tank as digester, which you can see here : https://www.instructables.com/id/Bio-gas-plant-usin...
That was my first instructable and people are still commenting and asking me for guidance on Biogas plants for home use and for demonstration at schools & colleges. I have replied and mailed guidelines to almost all of the queries and I hope that helped them in their quest for building their Biogas plant.
As you can see in the last step of this instructable, I was invited by Hajee Karutha Rowther Howdia College, Uthamapalayam, Theni District in Tamil Nadu, India, to present a keynote address on Biogas and Panchagavya (an organic product made from produce from cow). This event was supported by the Tamil Nadu State Council for Science and Technology, Chennai, attended by local farmers, self-help group members and students. Many of the attendees expressed their interest in Biogas plant using kitchen waste and wanted to see a working plant.
This is my attempt at constructing a medium sized Biogas plant for home use as well for demonstration to students and others using a 750 liter capacity tank as digester and a 500 liter capacity tank as a gas holder, a floating type gas holder method. I have provided easy to understand step-by-step instructions on how to build the plant. Please go through this instructable and feel free to post your comments and queries with respect to biogas.
Step 1: What Is Biogas, What Is Biogas Plant and How It Functions...?
What is Biogas...?
For those who are not familiar with the term Biogas :
Microorganisms who thrive in the absence of air digests the organic material and releases a mixture of gases. The gases thus produced contains mostly methane along with other gases like Carbon dioxide, Nitrogen and Hydrogen Sulphide in small quantities. This process is known as anaerobic digestion.
Methane is a colorless and odorless gas and is highly flammable. (It is Hydrogen Sulphide that smells bad) Methane is not poisonous.
Methane along with other gases occurs naturally in swamps, waste dumps and even in home toilets in the septic tank. Due to its highly flammable quality, it can be used as fuel. But capturing the methane from the atmosphere is very difficult as it is lighter than air. The Biogas Digester or Biogas Plant we see here is a device which helps us in collecting this gas and use it as fuel.
Biogas Plant
You can see the opened-up prototype of a Biogas plant in above photograph.
- The Biogas plant consists of a digester tank, where the organic material is stored and the microorganisms work on them and release gas.
- The gas thus produced is collected in a tank known as gas collector. In a floating type model, this tank is floating in the slurry and moves up-and-down based on the amount of gas stored in it
- A guide pipe helps the gas collector tank to move up-and-down inside the digester tank.
- Waste is fed through feed pipe inside the digester tank.
- The fully digested slurry drains out through the outlet pipe. This can be collected, diluted and used as fertilizer for plants.
- A gas pipe line from the Gas collector tank helps in utilizing the gas for cooking and lighting
Now let's get down to business and construct a medium sized Biogas plant for home use
Step 2: Selection of Tanks
Before selection of tanks, I need to consider how much of digestible kitchen and garden waste I could collect everyday for feeding the tank. In my case I can easily collect between 3.5 to 4 kilogram of waste from kitchen and home garden. This quantity will be sufficient for a biogas plant with 700 to 800 liter capacity digester tank. Since only 750 liter capacity tanks are available in the market, I have selected a 750 liter tank to be used as the digester. A simple thump rule for biogas plant for home use is 5 kilograms of waste needs a 1000 liter capacity digester.
Now for the selection of gas holder tank, I need to consider the following before buying the tank:
The model I am building is with a floating type gas holder tank. That means the gas holder will move up and down based on the amount of gas inside. So, the gas holder tank should fit inside the digester and also should have minimum difference between their width as this will reduce in loss of gas through the sides.
During market search, I found that the 500 liters capacity tank will meet the requirement, having a width difference of about 100 mm, that means 50 mm on each side. So, I have decided to use the 500 liter tank as gas holder, which will have an up-and- down movement inside the digester using guides.
Some designs cater for a water seal between the digester and gas holder, but in my case that will considerably reduce the capacity of the digester. However, the gas loss through the sides will be very marginal with respect to providing a water seal and reducing the capacity of the digester.
In the above photographs, you can see the selection of my tanks. They are of very good quality three layered tanks that can withstand exposure to sunlight and acidic condition of the slurry inside.
Step 3: Other Materials Required
In addition to the tanks, I have utilized the following PVC parts
- PVC Door elbow 120 mm dia one number to be used for feeding waste
- PVC pipe 50 mm dia 300 mm long to be fitted with digester for slurry outlet
- PVC pipes 32 mm dia 250 mm long 4 pieces to be fitted with digester for guide system
- PVC pipes 32 mm dia 1000 mm long 4 pieces for guide system
- PVC pipes 12 mm dia 1000 mm long 4 pieces for guide system and stabilizing gas tank
- PVC pipe 120 mm dia one piece to be used for waste feeding
- PVC cap 120 mm dia for the waste feed pipe
- PVC pipe 50 mm dia about 5 meters for the slurry outlet system
- PVC bend 50 mm dia one piece for the slurry outlet system
- PVC 32 mm dia threaded couplers 4 pieces to be fitted with gas tank for guide system
- PVC 32 mm dia plain couplers 4 pieces to be fitted with digester for guide system
- PVC Elbow reducer 32 mm to 12 mm 4 pieces for the guide system
Items required for the Gas pipe line is given separately in Step 12 below
Step 4: Adhesives Used
For joining the parts of the gas plant, I have used the following adhesives
- Araldite Epoxy Adhesive
- M-Seal Epoxy Compound
- PvC Solvent Cement
Step 5: Tools Required
You can see here that construction of this plant does not require many tools. These are list of tools I have used:
- A hacksaw with frame
- A single sided hacksaw blade
- A sharp knife
- A medium sized hammer
- Set of spanners to tighten the gas pipe connectors
For crimping the connectors with the ends of gas pipes, I got assistance from the shop from where I bought the gas pipes. They helped me with their Hand crimping equipment as per my requirement. (please see Step 12)
Step 6: Preparation of Gas Holder Tank
The 500 liter capacity tank is required to be cut at the top. The visible top ridge will be used as guide line to cut the tank
- Using a sharp knife make a slot along the line
- Now you can insert a hacksaw blade in the slot and cut along the ridge
- The hacksaw blade gets very hot. Wrap the end with a piece of cloth
- Cut through the ridge and remove the top cut portion from the tank
Step 7: Preparation of Digester Tank
The top portion of the digester tank also needs to be cut and removed. However, the width of cutting should be just enough for the free movement of gas tank
- Place the removed top portion of gas holder on top of digester tank
- Leave about 20 mm on all sides and mark the guide line for cutting
- Using a hacksaw, cut slots on top of projected portion of digester tank
- Now use a hacksaw blade to cut along the guide line and remove the top
- Finish the cut edges with sand paper
Step 8: Fixing the Feed Pipe to the Digester Tank
The 120 mm dia door elbow need to be fixed at the bottom of the digester tank
- Place the elbow and mark the cutting line
- make a slot along the line with a sharp knife
- Insert the hacksaw blade in the slot and cut along the guide line
- Insert the Elbow in place
- Seal with M-seal epoxy compound on both outer and inner sides of the tank
Step 9: Fixing Slurry Outlet Pipe With the Digester Tank
The 50 mm dia 300 mm long pipe is to be fitted at the top of digester for the slurry outlet
- Place the pipe on top portion of digester tank opposite to the feed pipe
- Mark the cutting line
- Using a sharp knife cut along the guide line and remove the cut piece
- Insert the slurry outlet pipe and seal with M-seal epoxy compound from both sides of the tank
- You can cut and remove the extra projection inside tank if required. Otherwise leave as it is
Step 10: Fixing the Guides Over Digester for the Movement of Gas Holder Tank
Some sort of guides are to be provided for the easy up-and-down movement of gas holder tank. We will use the 250 mm long 32 mm dia pipes for this.There are six projected portions on top of the digester. The slurry outlet pipe and waste input pipe are in alignment with two them opposite to each other. Leaving these two we will fix 32 mm pipes on other four projections. These pipes will be extended after placing the gas holder tank.
- Place the 32 mm dia pipe on top of projections and make a mark
- Using a hacksaw cut and removea square portion of the marked area.
- Insert 32 mm dia pipes on all these cut portions and fix with M-seal epoxy compound
- After the compound is cured cut and remove excess leaving about 25 mm projection
Step 11: Providing Guide Support on the Gas Holder Tank
As we have seen in the previous step, 4 numbers of 32 mm dia guide pipes have been provided on top of the digester. In order to keep the gas holder tank in alignment, we will provide a sort of guide system on the sides of the gas tanks. Here we can use the 40 mm dia threaded couplers for this. Fix only two numbers opposite to each other. We can fix the other two once we place gas tank inside the digester and observing the movement of gas holder.
Step 12: Preparation of Gas Pipes
I spent one full afternoon in shopping and preparing the Gas pipes. There will be three sets of gas pipes as below
- From Gas Holder tank to the Link Pipe mounted on wall
- Link pipe between gas holder tank pipe and kitchen
- From the link pipe to Biogas stove
Parts required
- Three pieces of gas pipes, all about 2.5 meters long
- Ball valve 2 numbers one with gas outlet on gas tank and another with the end of link pipe
- Bend 1 number over the gas tank
- Nipple 1 number over gas tank
- Adapter 1 number inside gas tank connecting nipple with the bend
- Three numbers of barbs with male threaded ends crimped with clips at one end of pipes
- Two numbers of barbs with female ends crimped with clips at other end of pipes (One end of the pipe is left free as this will connect with the stove)
- Inner and outer washers
- One roll of teflon tape
- Few 12 mm size U-clamps for fixing the link pipe on the wall
At the shop itself I have measured all the pipes and used their hand-crimping tool to crimp all the ends of pipes. The pipes are tested for leakage by fixing the closed ball valve at each end separately, immersed in water and blowing air from the other end.
Step 13: Fixing Gas Outlet From the Gas Holder Tank
- Assemble all parts required for the gas outlet.
- Using a sharp knife, make a small hole at the center of the Gas holder tank. You can make a neat round hole by just twisting the knife all around. This hole should not be larger than the threaded portion of the accessories
- Use suitable inner and outer washers at all joints. All threads must be covered with teflon tape.
- Connect the gas pipe with the bend
- Connect the bend with the nipple
- Connect the nipple with the adapter inside the tank. Make sure all joints are tightened properly
- Provide a leak proof joint by applying epoxy resin over the joint from outside and inside the tank
Step 14: Placing Tank and Fixing Slurry Outlet Pipe
Now we can move our digester tank to the desired location. Select a site where,
- The unit gets more sunlight
- Easier access for feeding waste
- Easy to remove the slurry and use it properly
- Minimum distance from the Biogas unit to the place of utilization
Here, I have place the unit on the terrace which gets maximum sunlight throughout the day. I have also provided a pipeline from the biogas plant for easy collection of slurry down. The kitchen is very adjacent to the plant and the gas line can be taken through the ventilator opening on the wall.
The couplers required for fixing guide pipes for the gas holders also added at this point. Place the couplers over the already fixed 32 mm dia pipes and lightly tap them down in place using a hammer
Step 15: Fixing the Waste Feed Pipe
- Clean the inner surface of door elbow and bottom outer surface 120 mm dia waste feed pipe
- Apply PVC solvent cement over both the cleaned surfaces
- Join them together immediately before the solvent cement dries out
- Place the cap on top of the feed pipe
Step 16: Place the Gas Holder Tank and Finish
Gently lift the gas holder tank and place it over the digester tank so that the 40 mm dia guide couplers fixed on the sides of the gas tank sits over the 32 mm dia couplers on the digester
Place one set of guide pipes through the 40 mm dia coupler as seen in the photograph
Now our Biogas plant is ready...
Step 17: Feeding the Biogas Plant for the First Time
Initially you need to feed fresh cow dung to start the process. On the same day this plant was made ready, I collected about 10 kilograms of cow dung from nearby farm and another 20 kilogram the next day. Visited a cattle farm again and collected 50 kilograms of more cow dung. Now I have a total of 80 kilograms of cow dung for initial feed.
I have diluted these 80 kilograms of cow dung with about 300 liters of water. I have also added about 250 grams of country-made jaggery (it is a concentrated solid product made from sugarcane, palm sap and coconut sap). The addition of jaggery will help the multiplication of microorganisms at a faster rate.
This mixture was fed into the digester through the feed pipe.
After feeding, wash the feed pipe and replace cap.
We use bore well water. Most of the water supplied through municipalities, corporations are treated with chlorine. Do not use chlorinated water as this will kill all microorganisms. If you have access to only chlorinated water, then keep the required amount of water open to atmosphere overnight and stir well, so that the chlorine evaporates.
Step 18: Gas Formation
Gas formation will start after about two days of feeding the digester with cow dung slurry. You can see here in these photographs that the gas holder tank started raising along the guide pipes.
But, this gas contains lot of impurities and will not burn. Moreover, there was air present in the gas tank when we placed it over the digester.
Once the gas tank is full, this gas will be released to the atmosphere.
Step 19: Type of Material Whicn Can Be Used for Feeding the Biogas Plant
Once the gas formation starts, you can feed waste material to the digester. The following are some of the wastes commonly available in a household
- Rotten vegetables
- Vegetable peels
- Fruit skins
- Left-over spoiled food which are unfit for consumption
- Very sour curd unfit for consumption
- Over-fermented Dosa batter
- Left-over vegetable oil used for frying
- Grass and weed clippings
- Dried flowers
- Tender banana stems
- Cattle waste like cow dung, goat's dung and poultry waste
- Leftovers coffee grounds and leftover tea leaves
- Water used for rinsing rice and pulses. You can use this water for diluting the feed material
This list is endless... there are so many organic waste material you can use in the anaerobic digester. Make sure you chop them into pieces as small as possible. However, avoid certain items given in the next step which are unfit for feeding the biogas plant.
Remember, food is precious. Do not waste food. Use only spoiled food which is unfit for consumption
Step 20: Materials Unfit for Biogas Digester
Avoid following type of materials in a Biogas plant
- Dry skins of Onion and Garlic
- Egg shells
- Fibrous materials like coconut husk
- Bones, raw or cooked
Step 21: How Much to Feed...?
Once gas formation starts, you can start feeding the digester regularly with wastes from kitchen and home garden. But the big question is How much waste we can feed ?
Here, the capacity of my digester is 750 liters. So I will feed about 3500 to 4000 grams of waste in this plant daily.
Why this much quantity only ?
All solid wastes we feed into the digester will take between 30 to 50 days to get fully digested based on the type of waste. For example, cow dung will take about 30 days for full digestion and solid vegetable wastes may take 50 days. This is known as Retention Time.
By adding the wastes in small quantities everyday, I will have a regular supply of about 750 grams of gas after about 30 days. This will assist the wastes to get fully digested and release optimum gas and get discharged through the slurry outlet pipe. Overfeeding the digester will drain out the partially digested wastes, which will increase acidity of the slurry in the digester as well decrease the colony of microorganisms working on the wastes.
As a thump rule, for 1000 liter capacity digester, feed approximately about 5000 grams of waste.
Also, the solid wastes should be made into chunks as small as possible. Here, you can see in the photographs above that I have used an old mixer grinder to pulverize the larger chunks of vegetable waste.
Step 22: A Vented Ram for Pushing Down Larger Chunks and Agitating the Slurry
After feeding kitchen waste through the feed pipe, you may find some larger chunks floating inside the feed pipe. I have made a small vented ram using some scrap material and a one meter long 32 mm pipe. This ram can be used inside the feeding pipe to push down the chunks down. The vents in the ram will allow the water to seep through, thus making it easier to operate inside the feed pipe.
Repeated up and down movements of the ram inside the feed pipe not only help in pushing down the larger chunks, it will also help in agitating the slurry inside the digester and help in releasing trapped gas. This will also break down the scum formed on the surface of the slurry and accelerate the digestion process.
Wash the ram with clean water after every use.
Step 23: A Word of Caution : Never Try This
Real Story... One student who got guidance from me over telephone, constructed a mini biogas plant for school exhibition and was overenthusiastic... She opened the gas valve from the gas holder and tested whether the gas burns or not by holding a burning match stick in front of the gas pipe. The entire gas tank exploded. Fortunately, nobody was injured but they had to spent lot of time to clean up the mess.
Never do this... only use a Biogas stove or a Bunsen burner or a suitable nozzle arrangement to test the gas.
Step 24: Biogas Stove
To use the biogas for cooking, you need a stove specially made for biogas. I got a new twin-burner biogas stove from the market after an exhaustive search. Normally, LPG is used at home, so there is no demand for biogas stoves and shops do not stock them.
If you look at the picture of the biogas burner, you can see that the holes are larger than that used in LPG stoves. The nozzle of the burner also has a larger orifice. The biogas stove is designed in such a way that methane is mixed with double the quantity of air before being burned.
The specifications on the sticker says the pressure required is 747 N/m2, that is 747 Newtons per Square meter, converted to 7.62 gf/cm2 (gram-force per square centimeter). Each burner consumes about 450 liters of gas per hour if fully opened. That means with a 500 liter gas holder tank filled with gas, I can use it for about an hour in one burner.
Step 25: Attach Gas Pipe to Stove
In an earlier step, we prepared three sets of gas pipes to be used with the biogas plant. The first set of pipe is being fixed with the outlet from the gas holder tank. The second set will be used to link the gas line from the gas holder to gas pipe fixed with the stove. Here we use the third set of gas pipe to be fixed with the stove.
Attach the free end of gas pipe to the stove. I have also used a layer of insulation tap to seal the joint from any leakage.
The other end with the crimped attachment will connect to the gas link pipe.
Now our biogas stove is ready for testing.
Step 26: Add Ballast on Top of Gas Holder Tank
Before testing the biogas in the stove, you need to check that the collected gas in the tank has enough pressure to flow through the gas pipe to the stove.
Methane is lighter than air. When you connect the gas pipe line and open the gas outlet valve, there are chances of negative pressure at the pipe end which may suck in the out side air into the tank. This is known as Flow back. This can be avoided by placing ballast on top of the gas holder tank.
Here I have added an old car tyre with a semi-inflated tube inside on top of the gas holder tank. The semi-inflated tube will prevent any rain water getting collected in the tyre and becoming a breeding ground for mosquitoes.
After placing the ballast, open the valve and check the gas flow. You can hear a hissing noise when the gas is flowing out. you can also feel the gas flow by placing your fingers in front of the valve opening.
Step 27: Test the Biogas
The gas initially produced may contains lots of impurities and will not burn. I have emptied the gas holder tank three times before testing the gas.
Connect the gas inlet pipe and open the knob slightly. Now you can hear the hissing noise of gas escaping through the burner. Hold a lighted match stick over the burner and voila, you have a flame...!!!
The gas still has lots of impurities, but it started burning. You can see the blue flame of methane burning here.
Step 28: Watch the Video of Impure Biogas Burning
Watch the video and see how the impure methane burns...
Step 29: The Digested Slurry
Initially, I have added diluted cow dung slurry which covered slightly more than half of the digester tank. Periodical addition of about 3 to 4 kilograms kitchen waste and weeds from the garden everyday, gradually increased the slurry level inside the digester tank. Once your digester is full, you will find the digested slurry oozing out of the outlet pipe, whenever you feed the plant.
Place a bucket beneath the outlet and collect the slurry. This slurry does not have any odor and will not attract any flies. it is also an excellent organic fertilizer.
Dilute the slurry with water and feed your garden plants with the diluted slurry.
Step 30: My Presentation on Biogas and Panchagavya
A Science awareness Program was organised at Hajee Karutha Rowther Howdia College, Uthamapalayam, Theni District in Tamil Nadu, India, during 15th and 16th July 2014. The event was supported by the Tamil Nadu State Council for Science and Technology, Chennai. I was invited to present a Key Note Address on Biogas and Panchagavya. Many local farmers, ladies from Self-Help groups and Staff & Students of Biology Department attended the presentation.
My presentation covered all aspects of Biogas plant including construction, feeding and functioning. As you can see in the photographs above, the local farmers were very much interested in the simple technology which can convert organic waste from the kitchen in to useful biogas and the composted slurry as fertilizer for the plants. They were also very much eager to visit a working unit of a plant which uses only wastes to make fuel. My attempt in constructing this model is for home use as well for demonstration to students, farmers, Self-help groups and all those who are interested in this technology
Step 31: Bottom Line
It is nearing a month after we installed the Biogas plant. The quality of gas has considerably increased compared to the initial output. Now the plant produces gas which burns for about half an hour. The solids we introduced in the digester will take more time to get fully digested. The gas production will gradually increase and we may be able to get a regular supply of gas for about an hour's cooking in the following months. This will considerably reduce the consumption of LPG.
The total cost of the Project worked out to 12000 Indian Rupees, that is about 200 US Dollars. Now we do not throw away any organic waste from our home. What is more, we are getting free gas as well as free organic manure for our home garden
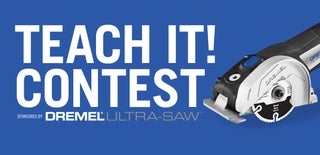
Second Prize in the
Teach It! Contest Sponsored by Dremel
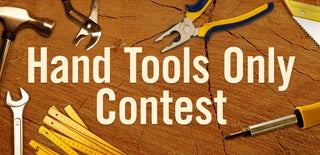
Participated in the
Hand Tools Only Contest
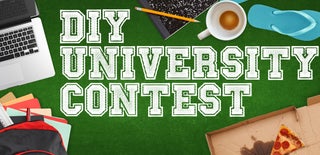
Participated in the
DIY University Contest