Introduction: Creating a Two Tone Engagement Ring
Here's how I made a two tone Gold and Platinum engagement ring start to finish. In this particular ring the center stone is a Diamond, the bezel is Platinum and the ring shank is 18k rose Gold. The ring shank is carved in wax and is cast using the lost wax process and the bezel is formed from flat stock.
Every job begins at the jeweler's bench. Jewelers use a LOT of tools! The bench has multiple files, sanding sticks, pliers, hammers, brazing torch, flex shaft and wax carving tools. In addition to these tools there are things like a polishing motor, ultrasonic cleaner, rolling mill and a casting machine.
The first step is carving a wax pattern for the ring shank. This is carved from a green wax using a wax saw blade, files and burrs with a flex shaft. The real trick is keeping the design symmetrical.
The wax is then cast in 18k rose Gold. This is done using the lost wax process. The wax pattern is sprued, placed into a steel flask and then put into the burnout furnace overnight. The next morning the ring shank is cast using a centrifugal casting machine and the shank is cleaned up using files and sandpaper. The inside of the ring is also reamed out/finished to the proper ring size and the shank is polished to make sure it is free of defects.
The next step is making the Platinum bezel. Platinum stock is rolled out to the correct size using a rolling mill and a bezel is formed to the proper shape in order to hold the stone. The bezel is welded using a gas torch and the shape is refined using a mandrel and then filed and sanded to the final shape. The finished bezel is then polished using Platinum polishing compounds and is soldered to the ring shank using Gold solder. The stone is then set by cutting a seat in the bezel, inserting the stone and using a burnishing tool to tighten the stone.
The bezel then receives a final polish, the ring shank is given a brushed finish and after a cleaning in the ultrasonic cleaner the ring is done! If anyone has any questions about materials or processes just ask!
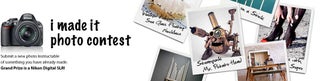
Participated in the
I Made It Photo Contest