Introduction: DIY Spot Welder From Microwave - Now With OLED Display!
This project is an outline of how to build a resistance spot welder using salvaged parts from an old microwave. Im using it to weld nickel tabs onto 18650 battery cells but depending on how you position the arms it can be used to weld sheet metal and other metals objects. Lets get welding!
Step 1: Salvage the Microwave
Quick note of caution!
The inside of the microwave is quite dangerous. The large capacitor maybe charged and can deliver a nasty or even fatal shock so ensure you discharge as soon as possible by touching a metal rod such as a screwdriver across the terminals to discharge it.
Okay so open up the microwave casing to reveal the electronic bits. Discharge that capacitor and get to work on removing the parts. You should find the transformer which should look very similar to the one in the photos. Remove the nuts and it should slide out pretty easily. I salvaged a few limit switches that we will use later and some of the cables are handy for power connections.
Step 2: Remove the Secondary Coil
We are going to rewind the secondary coil of the transformer as we want more amps and less volts. The primary is where the mains power is attached and the secondary has finer wire windings with the red wires attached.
The fewer turns of wire increase the amps but lowers the voltage, and more turns increase volts while reducing the amps. We don't need the secondary coil so it can be removed either by cutting off or by grinding the weld on the transformer body and sliding it out. Be careful not to damage the primary coil as we will be keeping this.
Step 3: Add the New Winding
The new winding will provide the current needed to weld stuff. By using really thick cable we can reduce the thousands of windings to a couple which will provide loads of amps. The thick cable is needed as the resistance will cause it to heat up and melt the insulation if its too thin. Not good!
The primary coil is put in first followed by the 2 shunts either side and finally the low gauge wire (blue cable) is wrapped a couple of turns. Remember to leave a decent length of cable that will attach to the welding electrodes.
Step 4: Finish the Transformer
Our super high powered transformer is nearly complete. We just need to weld the top back on to seal it up. You could alternatively use 2 part epoxy to stick it on. Options are good, pick whichever one is easiest for you. :)
Step 5: Electrode Terminals
We now need to attach our cable ends to the copper pins which we will use to weld. I machined some copper terminals but you could use some copper clamps from the hardware store. I've also attached the CAD file for the electrode clamp that I made. Here's the Fusion360 link too. http://a360.co/1Loyh1j
Attachments
Step 6: Welding Arm
I'm using this to weld nickel tabbing to battery cells so I've positioned the two welding electrodes side by side although you can easily mount them opposing like a traditional machine. I designed and laser cut a simple MDF case for the arm which houses the switch for operation and holds the electrode terminals.
Step 7: Package It Up
There is 230v of dangerous electricity coming into the transformer so its important that its covered. This laser cut case should do the job pretty well. Just make sure everything is contained as it will also look much better as well as being safe. Bonus!
As for wiring its pretty simple. Just connect the live and neutral to the transformer primary using the existing spade terminals, I would recommend adding a switch in between one of the power cables to make it easy to turn on and off. I salvaged this one from the microwave.
Thats it we're done! Have fun with your new spot welder!
Step 8: Add an OLED Display & Pulse Control
Add this circuit for precise control of the duration of the weld pulse. Very handy for welding 18650 cells and other thin metals.
The duration is varied using a potentiometer and the duration is displayed on the OLED display in milliseconds the coil of the transformer is connected inline with the SSR.
Build up the circuit on a breadboard and then transfer it to some perfboard when you've got it working. The big red button can be replaced with a simple foot switch if preferred.
I installed my board and SSR on top of the transformer, remember to add some insulation between the metal transformer body and the circuit board to prevent shorts.
You may need to add a 5v source for the Arduino as the SSR can draw a modest amount of power, I just cracked open an old 5v phone charger and connected the 5v output to VIN and GND on the Arduino.
Attachments
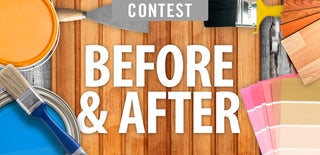
Participated in the
Before and After Contest 2016
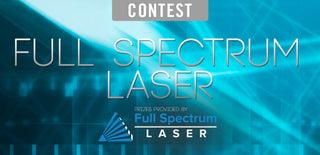
Participated in the
Full Spectrum Laser Contest 2016