Introduction: Electric Vehicle - a Simple Lightweight EV Platform
Driving the Car - With one gear and heaps of torque (300Nm from the twin motors) Driving is simple and effortless and the car rapidly gains speed and without a body the sensation of speed is greatly exaggerated.
Attachments
Step 1: The Chassis
The chassis is one of the few items you need to fabricate. The majority of items are sourced and attached to the chassis. We use a pressed aluminium box from 3mm thick aluminium sheet that doubles as the main structural spine and the battery box. The approach keeps fabrication very simple, maximises rigidity, keeps the weight low down and concentrated in the centre of the car and keeps the battery pack away from damage in impacts.
One of the disadvantages of using a thin walled box section is that large concentrated loads cannot be applied directly to the aluminium walls. This is easily overcome by using tubular steel subframes or bulkheads to spread loads. The tubular steel subframes are relatively small and are not difficult to fabricate.
Aluminium Box
The chassis box requires a large press to bend up. Because it's a simple box, your local metal roofing supplier should be able to supply the material cut and pressed to size.. I sourced a 3m long box, 270mm high x 300mm wide made from a single 1.2m x 3m x 3mm sheet complete with lid for $300.
The width of the box is wide enough for 4 batteries across plus a thin ply lining. The ply lining helps to protect the batteries, stop any drumming noise being transmitted through the chassis, ensures rivet heads don't rub on the sides of batteries. Attach the lining to the aluminium chassis using sikaflex automotive or marine polyurethane flexible sealant/adhesive.
Note that the lip on the aluminium box serves not only as a place to fix the lid, but also strengthens the structure when the lid is not fixed in place.
Inside the chassis box, a series of bulkheads, either aluminium or ply plates are fitted. The bulkheads have a number of functions. They support the chassis box against buckling, support batteries from acceleration and deceleration loads (including an impact) and provide reinforced mounting points for heavy components such as motors and seat frames or floor.
The box also needs a lid that can be opened to access batteries, but it needs to be securely fastened as an integral structural part of the box. While riveting would give a quick and strong attachment, it is not suited to testing and development requirements of a custom vehicle. A suitable alternative to using rivets is using rivnuts and socket screws. 6mm to 8mm rivnuts and screws are suitable. They should be spaced reasonably close and stainless rivnuts and screws are not recommended as the threads tend to bind. I have used 6mm socket screws at a spacing of 50mm. I do not recommend using stainless socket screws and rivnuts, having learned the hard way when several of the socket screw threads binding and needed to be drilled out and replaced.
A drawing showing dimensions for a chassis box is shown above along with an Autodesk Inventor rendering showing the basic chassis layout. The chassis box design is optimised 45 CALB 100Ah lithium cells fitted four wide.
Suspension Subframes
External subframes that slide over the box section are used to mount the suspension. The subframes are welded up from 25mm x 1.6mm steel box section. They are attached to the aluminium box using structural rivets from inside the box. An angle attachment for your drill or a right angle drill is essential for drilling the rivet holes this and a pneumatic riveter is needed to apply sufficient pressure to set a structural rivet as you will not fit a large manual style riveter inside the box.
Structural rivets such as Megalock Rivets should be used for attaching subframes. In Australia they will probably need to be sourced from a specialist supplier such as Profast. At the time of writing there was limited availability of structural rivets on Ebay, but suppliers such as Profast will post out supplies. A pneumatic riveter is available online starting from under $100 and is needed for the higher pressures required to set structural rivets, particularly in confined spaces.
The front and rear subframes mounted to the chassis box are shown above. The suspension mounting points are visible in the photos. The angle of the outer members matches the suspension mounts.
Step 2: Electric Drive
Motors
The car uses two electric motors mounted on a subframe that sits on the chassis, driving the rear wheels via belts. There is one fixed speed and keeping the belts (or chains) inside the chassis box keeps them clean, minimises maintenance and protects fingers.
This platform is easily adaptable to virtually any motor, either face or foot mounted.
I have used AC motors which are 58kg each. They are a good price for their size and have excellent torque over a large rev range. BLDC or permanent magnet AC motors will give a higher power to weight but are more expensive for an equivalent power output at this size due to the cost of large rare earth magnets. My AC induction motors were sourced from EV Power and came with controllers. Brushed motors are an even more economical option and an Etek / Mars style motor such as the Motenergy ME0709 are available from around $600 each.
The motors also require a motor controller. I won't go into detail about motor and controller selection here as there are other good resources available, however most motor suppliers will offer a motors either with a controller, or will recommend suitable controller options. A purpose built motor controller for a vehicle drive system is designed with forward and reverse and often regen programs. They typically also have switch inputs that will be compatible with a 12V ignition switch to switch the controllers on and off. Connecting up a motor controller is about as complex as fitting an aftermarket stereo to a car, although you need to be very particular about not making any errors or there could be smoke and tears.
Gearing
The motors transmit power through a toothed belt to the rear wheels. A 30mm wide Gates GT3 will transmit up to 30kW peak power and run smoothly and silently. Chain drives can be cheaper and lighter and provide a higher torque rating. The use of a belt or chain drive eliminates the need for a gearbox as the electric motors have more than adequate torque for single speed operation, particularly with a light weight vehicle.
I am using two AC motors put out a combined 300Nm of torque and with a 1:3 gear ratio from the motor to the rear wheels and while the acceleration from a standing start is excellent, it is currently geared for a very high top speed, thus even better low range performance could be achieved with lower gearing.
Rear Axle
The rear axle comprises two half shafts bolted to the original mazda drive shafts. A large pulley is mounted directly on each half shaft and is driven from a small pulley mounted directly on the motor. The half shafts are supported by a basic bearing each end, approx 20mm inner and 30mm outer bearing size with a pulley mounted keyed onto the shaft. The diagram above illustrates the rear axel arrangement. The half shafts have an outer flange welded to the shaft and machined to match the rear drive shaft flanges of the MX5 / Miata.
There is no interconnection between the two driveshafts or motors - each drives completely independently of the other. The torque characteristics of the electric motors inherently distribute torque between the driven wheels, thus there is no requirement for any differential. This arrangement will also facilitate simple development of true control systems in the future (torque vectoring)
HOW TO....
Order your selected motors and controllers
Order small pulley or sprocket with hole and keyway to match electric motor
Order drive belts or chains
Order rear pulleys with a ratio between 1:3 and 1:5. Ratios can easily be changed and experimented with and the best ratio needs to consider the motor selection, target vehicle speed and acceleration characteristics. The larger rear pulley will typically require a taperlock bush. This makes it easy to fit the pulley firmly onto the driveshaft and to change pulley ratios in the future.
The only specially machined items in the drivetrain are two half shafts that have a flange at one end to suit the drive shaft flanges from the suspension donor parts. A large rear pulley or sprocket is mounted on each half shaft and the half shaft is supported with a bearing each end attached to the chassis box and rear suspension subframe.
Step 3: Seating
A pressed aluminium floor box is riveted on each side of the chassis box and a 25mm x 1.6mm square hollow steel tube extends across the chassis at the front and rear of the floor box to assist in spreading loads across the chassis so the riveted joints on each side work in unison. Alternatively a frame for the floor boxes hangs over the chassis box and sits on rubber pads making fabrication more suited to interchangeable modular components and providing additional shock absorption for a smoother ride.
It is critical that the passenger cells are well attached to the chassis as considerable loads are encountered in the event of an impact. For the direct riveted floor, loads are shared across a large number of rivets, providing considerable shear strength. Where a floor box subframe is used with a couple of attachment points to the chassis box, reinforcement of the chassis box will reduce the risk of any localised buckling or tearing of the chassis box at the subframe attachment points in the event of higher speed impacts.
The photographs show a ply finish to the top of the floor box. In this example a ply and aluminium composite floor box has been used. The composite panel is constructed by riveting and glueing a ply and alumium sheet over aluminium ribs and a foam core. This increases stiffness, reduces any 'drumming' of the floor and provides a nice finish. It requires more time to fabricate but can reduce the cost of materials as ply is quite cheap and it permits a lighter gauge of the more expensive aluminium to be used.
The seats shown are Jaz Pro blow moulded poly seats. They are light weight, economical and ideal for outdoor use.
.
Step 4: Battery
The motors and controllers that I am using operate at 144 volts so I have used 45 lithium cells in series. The peak current draw is 600 amps for brief periods with a maximum rated current for longer periods of 300 amps so I have used 100Ah cells to limit current draw to between 3C to 5C. This gives a 14kWh battery pack which is a bit more than half of the capacity of Nissan Leaf's 24kWh battery pack.
Each cell is 3.3kg giving a total battery weight of 150kg.
A battery pack of this voltage is enough to do some serious damage if you drop a tool across the terminals and can give a dangerous electric shock. A qualified electrician with experience in DC power circuits should complete work on the battery pack.
An essential part of the battery pack is the battery management system. The battery management system is required to ensure individual cells are not over or under charged. A good battery management system will also provide information about the battery state of charge and the current draw in or out of the battery. The cells sourced for this project were CALB 100Ah cells from EV-Power, ordered and supplied complete with EV-Power's own battery management system and a compatible single phase battery charger. The individual cell and battery pack installed in the car is shown in the photos above.
Some background on lithium cells for electric vehicle use from the battery supplier...
LFP batteries have many advantages over Lead Acid, half the weight, higher voltage under load, double the usable capacity and ten times the cycle life! The total cost of ownership is less for LFP batteries than for lead acid.
- Voltage: 3.2-3.4V nominal, 2.5V min, 3.9V max
- Cycle life: 2000+ to 80% DOD, 3000+ to 70% DOD, measured, not just claimed.
- high discharge rate
- Consistently low internal resistance. (=longer life)p
- Safe LFP chemistry, proven performance in EVs.
Step 5: Suspension and Steering
A vehicle platform with double wishbone suspension on each wheel and rear drive has been developed. Wishbone suspension provides maximum flexibility both with body design and ride height as wishbones give easy height adjustment and typically require lower height above the wheels than strut type suspensions. Wishbones also provide optimum handling performance while driving the rear wheels is a little simpler, avoids the need for CV joints on the steered wheels and provides more entertaining handling. Rear wheel drive is also suited to more central placement of the electric motors for optimum placement of the heaviest components closest to the vehicles centre of mass.
The cheapest and easiest way to obtain suspension components is to source from a wrecking vehicle, however there is a limited number of vehicles with front and rear wishbones and rear wheel drive. Two fairly light weight vehicles are the Mazda MX5 / Miata and Honda S2000. I have used a wrecked Mazda MX5 as they are more commonly available in Australia. The suspension from a MX5 is conveniently attached to subframes that can be detached from the car by removing a few bolts. The subframes include all of the suspension mounting brackets so they could be reused, but the chassis box would need some work to cut and fit around the original subframes, so a simpler (and lighter) approach is to fabricate your own front and rear subframes and attached the suspension, wheels, hubs, brakes, springs etc. complete onto the new subframe.
Photographs: The front and rear wheel and suspension after removal from an MX5 is shown in the above photos along with the original front subframe and a rear subframe. Note the front suspension subframe is reasonably heavy as it also incorporates the front engine mounts. The new fabricated subframe can be easily seen on the car in the last photo.
Even though the MX5 is a light weight vehicle, there is still significant unsprung weight, with the four wheel, brake and suspension assemblies weighing a total of approx 140kg, which is nearly 1/3 the weight of the car. For lighter weight (but more expensive and more fragile) aluminium racing wheel uprights and hubs with fabricated wishbones and rod ends can be sourced eg from Formula Ford parts suppliers.
HOW TO.....
Firstly if you need to disassemble the host car to get the components out, refer to a useful guide such as how to remove an MX5 body from the makers of the exocet kit car, although suspension components can easily be removed just by removing wishbone pivot bolts and driveshaft flange bolts at the rear and wishbone pivot bolts at the front.
Secondly press up brackets for the suspension pivots from 50mm wide x 3mm thick steel plate. The bracket widths need to match the width of the suspension bushes on the inner ends of the wishbones. They may need to be slotted to cater for camber angle adjustment. The Mazda uses a simple offset washer to position the suspension mounting point in the slotted hole for camber adjustment.
Thirdly attach the brackets to the suspension arms in the middle of their adjustment range. With the suspension and wheel still assembled, clamp the brackets onto the suspension mounting subframes and check the position and alignment of the wheels. Clamp long lengths of tubing to the wheels to assist in aligning them. Once the wheels are in position and aligned, tack the mounting brackets onto the suspension subframes with a welder, then remove the suspension arms and weld into place.
The steering rack sits at the front of the chassis and two tube or angle arms are welded to the front suspension subframe to mount the rack. The angle of the steering shaft and column needs to be determined to suit the seating position in the car. Placement of a pivoting joint on the steering column mount caters for a height adjustable steering wheel.
USEFUL INFO
3d CAD drawings of Mazda MX5 / Miata suspension assemblies are available online from grabcad and can be used with free 3d CAD programs such as Autodesk Inventor Fusion for development of the suspension design.
The mazda steering rack with power steering has a higher (faster) ratio than unassisted racks. With the lighter weight of this vehicle design, hydraulic assistance is not required and the assisted rack can easily be depowered. Instructions for depowering an MX5 steering rack are available online on MX5 / Miata community forums.
Step 6: Driving Experience
The experience of driving and fine tuning a light weight EV designed around a central battery box has been a lot simpler than a petrol powered car. Basically it was plug everything in and check that the motors are running in the right direction, fine tune the two throttle pots, tighten the drive belts and very little else to do.
The concept of twin motors independently driving the two rear wheels has worked perfectly and the motor torque and speed characteristics automatically distributes power to the two rear wheels without the need for an "electronic differential". There has been some drifting in the adjustment of two separate throttle pots that send signals to their respective motor controller. This doesn't cause problems in normal driving and in the future will be addressed by going back to one throttle pot with an electronic splitter.
The EV is being used around a farm with a small tray and is proving convenient, smooth and quiet and with the short range trips typical around the farm, the battery pack does not get discharged below about 85%.
The large section size of the chassis box provides excellent stiffness and there is no discernible scuttle shake and the design will continue to be tested over rough farm roads to prove the strength and reliability of the concept and to expose any weaknesses.
The level of performance of the motors far exceeds that which can be explored on gravel farm roads and some track time will need to be booked in the future for further performance testing. The gravel farm tracks do provide an excellent testing ground for testing torque vectoring systems to get the best performance on slippery gravel roads and a future project to develop an Arduino based torque control system is planned, although not in time for the current Arduino challenge.
Range, Speed and Recharge Time
Update May 2014 typical energy consumption 0.74Ah/km (106wH/km), normal driving, gravel roads.
It uses around 1% of the battery's charge per kilometre on unsealed farm roads and off road, so that equates to 100 km or 60 miles per charge.
For my application and testing, the range is a lot more than required around the farm and the pack was sized more to ensure safe peak current draw than range. The advantage is the extra pack capacity gives a mobile power source around the farm.
Speed is excessive for farm tracks and haven't explored the upper end of the speed range, this will have to wait for track time. On the tree lined farm tracks I wouldn't go more than 100km/h or 60mph. Estimated top speed is around 160km/h or 100mph but dependent on the aerodynamics of the body as the car good low end torque geared for a top speed of 200km/h (1:3 motor to drive ratio, 6000 rpm motor speed) although it will not be able to reach speeds this high without a low drag, streamlined body. A lower gear ratio is planned and will increase acceleration to 100km/h which is faster than needed.
The recharge time is about 5 minutes per 1% of charge or 8 hours for recharge from fully discharged using a 10amp 240 volt single phase battery charger. The charge rate is not linear and as the battery approaches fully charged, the charge rate drops off.
Step 7: Resources
Plans
BotEV Chassis Platform November 2013 2D CAD file (dwg)
Chassis Box cross section CAD file (dwg)
3D CAD model information
https://grabcad.com/library/mazda-mx5-miata-rear-u...
https://grabcad.com/library/mazda-mx5-miata-front-...
https://grabcad.com/library/mazda-miata-steering-r...
Suppliers & Parts
Motors, Controllers, Batteries and Battery Management - EV Power (Australia)
Smaller motors for light weight EV projects also check out Cyclone Motor, Golden Motor and Kelly Controls
Drive pullies and belts - Gates GT3, Busselton Bearings
Aluminium Pressings - Combined Metal Industries
Seats Jaz Pro - Ebay, Sydney supplier
Acknowledgements
I would like to thank Rod Dilkes from EV Power for his encouragement, support knowledge and assistance. Rod is the brains behind the electrical setup for this project.
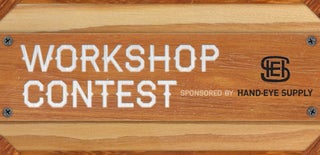
Third Prize in the
Workshop Contest