Introduction: Etching on Any Surface Cheaply and Without the Use of Chemicals
This is another of my proprietary processes that, up until now, I've pretty much kept to myself. I've used the Paasche air eraser for many years, and with most people using chemicals, I've turned it into a bit of a small business. I'll add a bit of an overview video at the end of this instructable so you can see the process.
**Due to interest, and folks mentioning that they're having trouble finding these tools, I've created another instructable on how to fabricate one at home. I did try and keep it as simple as possible and resource friendly for those that don't have a well stocked workshop. You can find it here;
https://www.instructables.com/id/Making-A-70-Glass-Etching-Tool-For-Less-Than-10-Co/
One of the biggest advantages to using the air eraser, over chemicals is the variety of materials you can etch on. With chemical etch, you are pretty much limited to glass, and even then, it's difficult, if not impossible to create anything decent on tempered glass. I've successfully etched on glass, plastic, brass, chrome etc. Basically anything with a gloss surface will take an etch. Now, there's also the issue of pollution, waste and many other issues that arise from using chemical etch. Suffice it to say, with the air eraser, there's far less cleanup, and far less impact on the environment.
Secondly, is the cost. Sure, the initial expense of buying the eraser and compressor can be a bit much, however, once you realize that your etching compound can be sifted and recycled over and over again, you're looking at next to zero overhead, other than purchasing masking material (which can be acquired from the dollar store) and the power to run your equipment.
Now this process is far different than sand blasting that uses silica. The air eraser uses a fine aluminum oxide powder that leaves a very shallow, almost untextured etch. Whereas sand blasting can leave a rough porous finish, and can even weaken the glass, the air eraser etch is smooth, very clear and doesn't create small crannies where dirt can build up and ruin your work.
An obligatory caveat: The etching compound is not terribly good for your health, and although it doesn't leave any chemical film behind on your work, it should not be breathed in. It is aluminum after all. I highly recommend you build an etching box, (which I may make an instructable for later on), or at the very least, wear a mask and goggles while you work. A big advantage of having a box is containing the powder for reclamation and sifting later on so it actually works in your favor to play safe.
Step 1: Tools and Equipment
Tools:
Paasche Air Eraser - can be purchased most places that sell airbrush equipment
Silent compressor - If you can't find or afford one, check out my other instructable on how to make one
Etching box - Great way to reclaim your compound, and keep your work area dust free
Ladies Nylons - The powder is very fine and will pass easily through a double layer of nylon material and leave dirt behind when filtered.
Equipment:
Frisket/Masking material - Spend $10 a roll at the art store, or grab clear shelf liner from the dollar store. They're exactly the same.
Aluminum Oxide Compound - There are different grades but fast cutting works fine.
Step 2: Making Your Stencil
Any stencil will work, provided you can fit if over your project. An advantage of using the air eraser is that the stencil doesn't have to fit perfectly because the flow is in one direction, so if it is lifted on one part, you don't have to worry about overspray. And since it's not a liquid, you don't have to worry about it bleeding underneath.
I find that I prefer custom stencils, and for that, you'll need a printer. Ink jet works the best, but you can use a laser like I demo in the vid. You just need to attach a sheet of paper to the plastic side to prevent it melting against the roller. You can make your own stencil from scratch, if you have the photoshop skills, however, a quick search online will usually turn up exactly what you're looking for.
An important thing to remember: You'll be printing on the paper side of the stencil, not the plastic, so you'll need to invert the image before printing, otherwise it'll end up backwards. Another point is to leave small bars connecting 'islands' in the stencil. They can be removed later, when the stencil is attached to it's surface. This will make it easier to keep things nice and lined up.
Step 3: Setting Your Stencil
Having a nice secure place to set your work is crucial. What I'm using is some old packing cardboard to hold my glasses in place, but you can make your own custom jig.
Now, when you're working with curved surfaces, you'll find it easier to set your stencils by hand. You can lift and reset anything that doesn't stick down properly, but you can expect to have bubbles and wrinkles. That's alright. Remember, the powder doesn't bleed, so as long as you don't spray at an angle, it shouldn't get underneath. If you're working on a smooth, flat surfact, you can add a transfer layer to your mask. This is done, simply, by putting a layer of masking tape over the top of the frisket to ensure that it goes down nice and evenly. Once it's in place, you remove the tape leaving the frisket stuck to your surface.
Step 4: Setting Your Air Eraser/Compressor
Compressor:
Having the right pressure on your compressor is crucial. I've found the optimum operating pressure is between 45 and 50 psi. Setting it higher could damage your eraser. I like to double regulate my pressure, setting the first at around 60psi, then setting a second regulator, with moisture collector at 45psi. This gives a nice even flow, while preventing moisture from getting into your tool, and gumming up the lot. There is also a second moisture trap on the line that comes with the air eraser. You should definitely use this line as even the smallest amount of water can cause some serious annoyances.
Air Eraser:
Setting your air eraser can be a bit trickier and is more of a personal thing. The finger trigger is threaded to allow restriction of air flow while there is a second screw on the bowl to limit the flow of compound. For my own use, and because I reclaim over 99% of the powder, I set both to maximum flow. Unless I'm working on finer detail like shading or highlights, there's no need to limit the tool.
Nozzle Clogs:
It doesn't happen often, but it does happen. Usually due to moisture, or pieces of dirt that have mysteriously found their way into your bottle of compound. Keep a needle nearby to help clear out any small clogs. It'll keep you from having to disassemble the tip every time. For bigger clogs, you will have to take it apart, so keep your micro wrench handy.
Step 5: Creating Your Etch
There's really no trick here other than to take your time and make sure you get everything. Now it's a good idea to mask off areas all around the etch. I can't count the number of times I've forgotten to take my finger off the trigger when pulling away from the piece, and almost ruined it with over spray. Suffice it to say, plan ahead.
The etch will only go so deep, so you don't have to worry about overspraying any one area. Keep the nozzle about 3-4 inches away, (unless you're shading where distance is better) and fill in every area. A nice bright daylight bulb, in your box will go a long way to showing areas you may have missed. Just make sure your light source is sealed because the compound is conductive and you don't want to start a fire with it.
Step 6: Cleaning Up
Once you've finished spraying, you can remove your masking and wash up. Simple soap and water will do the trick. There's no special care requirements, other than don't put them in the dishwasher if you don't want them to get ruined or worn.
For the powder you've used, I've found that if you take a pair of ladies nylons and double them up around a mesh strainer, you can clean and reclaim as much as 99%. This means a low overhead cost, but more importantly, less environmental impact than you'd get from the use of chemicals.
Step 7: Finishing Up
I hope you enjoyed the instructable. Thanks for following.
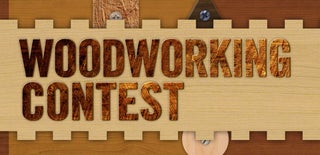
Participated in the
Woodworking Contest
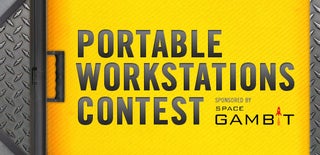
Participated in the
Portable Workstations Contest