Introduction: Flux Capacitor - Back to the Future
Since the release of the film back in the 80s I have been obsessed by the film Back To The Future watching the trilogy repeatedly. I watched it at the cinema over and over, I was very lucky that my great uncle was a projectionist so I could just sit in show after show.
So about 10 years back I decided I wanted to build a flux capacitor, but I got stuck back then because I didn't have the correct skills at that time and I was making a mess of it, so I shelved the project.
I decided to come back to it with my now improved skills and technology, and this time I have something awesome!!
The idea was to create a flux capacitor that was as close to the film as I could get, and at some point I want to put it in a Delorean.
Check out the video of it in actionI will be making other Back To The Future props including the Time Circuits so make sure you subscribe to me to get updates by clicking "follow" in the top right of the window.
WARNING: this instructable includes flashing lights and strobe effects especially on the videos.
Step 1: Parts and Tools
some of the parts are very hard to get hold of such as the Torr Vacuum relays (TRV-1 high voltage relay) if you can find them they sell for serious money, often sold by Back To The Future prop geeks for ridiculous prices. In this instance its best to replicate the relay as best as possible.
near enough everything I got on ebay, I love ebay.
Parts
Stahlin J1210HPL enclosure - the one on the film has a window but Stahlin have not made one with a window for years so you have to buy the one without the window and put your own window in.
Clear Acrylic sheet, 250mm x 200mm x 3mm - this is for the window.
3mm thick plastic sheet, grey for the back board.
1 meter of rubber window gasket - I used one with 3mm gap, 5mm gap A and B and 5mm web (see picture)
1 x can of Battleship Grey Spray Paint
1 x can of grey primer
1 x can of lacquer
1 x can of Plasi-kote brass
1 x can of Plasti-kote silver
car body filler
Accel 3009 yellow spark plug leads with orange ends, they have to be the 3009 to have the bend in them.
20mm clear Acrylic balls, I had a hard time finding these you can get them here
http://www.hindleys.com/index.php/materials/plasti...
12mm acrylic tube with 3mm wall
6mm acrylic tube, 1mm wall
6mm acrylic rod, solid
4mm copper tube
3mm copper tube internal Diameter 2mm
2mm thick stainless steel wire, I used a coat hanger, you could use music wire.
12mm thick, clear acrylic block
vero stripboard, prototyping PCB
20cm Jumper Wires, female both ends and some male both ends
1 x Arduino Uno
1 x SD Module
1 x SD card, or a micro SD with adapter
1 x LM386 Audio Amplifier Module
1 x 5w speaker, no thicker than 30 - 35mm so it will fit under the back board.
12 x Warm white LEDs, 5mm, 4.5v
7 x Bright White LEDs, 5mm, 4.5v
68 Ohm resistors
a simple on off switch
9V battery connector
Infra red reciever
Basic universal IR remote control
4 x 3/16 UNF machine screws
a medium project box, no thicker than 30mm
wire red and black.
Tools
A dremmel
Hacksaw
mitre box
screw drivers
soldering iron
solder
large cardboard box or spray booth.
masking tape
3D printer, not really required but it was easier for me to use this, you could make the bases out of clay or something then cast them in resin
Dymo label maker with red tape, 9mm wide.
side cutters
pencil
sharpie marker.
jigsaw
pair of compasses.
ruler.
USB Cable
screw drivers
sd card reader, I picked one up in a pound shop that works well.
various grades of sand paper
T-cut paint restorer.
Software
Google sketch up
Arduino sketch program
Adobe Illustrator (for researching the sizes of things from screen grabs of the film)
Audacity - free sound editing software
Wav sample converter - free wav file converter
Step 2: Research
I did a lot of research 10 years ago on parts of the flux capacitor, BTTF forums and prop making pages, and discovered back then that the enclosure was a Stahlin J1210HPL but one with a window. but they stopped making it with a window but they still make it without a window. they have also stopped making the color that is used in the film. both of these issues will need to be dealt with. I bought my enclosure secondhand on ebay, they are expensive new.
because I knew the enclosure was a J1210HPL, I could download the PDF specs (attached to this page) and get the sizes and use these to scale some screen grabs from the film to the correct size. using these photos I could work out the diameters of the relays and other parts and positions.
I also got from the BTTF forums that the relays that are used are Torr laboratories TRV-1 Vacuum relays. unfortunately they are no longer made, they stopped making them back in the 50s / 60s. if you can find someone with one they will want a lot of money for it, and normally it's a BTTF geek that will have it and will hold it to ransom. and you will need 3 of these.
it's better to replicate the relays, originally when I first was going to do this project I spoke to a guy who used to blow glass for laboratories and he was going to make the glass parts for me for about £25 each. And I was going to cast the bases out of resin, unfortunately my skills at the time were not up to scratch and the bases ended up warped.
I found a site where someone had already made a flux capacitor and documented it reasonably well, and I really liked the way he made his relays. www.myfluxcapacitor.com is the site if you want to check it out.
Attachments
Step 3: Preparing the Enclosure
I originally cut the hole for the window 10 years ago based on stills of the film I inspected.
radius of the corners is 45mm
200mm wide x 250mm long.
I did a bad job of spraying the inside so I had to rub it back, and use car body filler to finish off the holes I had already started to fill on the previous attempt. I also rubbed the whole surface with sandpaper so the paint would stick easier.
wiped it down with a damp cloth to get rid of the dust.
I used masking tape to tape up the latches, hinges and rivets, then sprayed it with grey primer, gave it a couple of coats and let it cure over night. Make sure you spray in a well ventilated area and use a spray booth or a large cardboard box to protect surfaces and shield it from the wind and any dust.
I then gave it 3 coats of Battleship grey, which was the closest paint I could think of to the original color. Allowed that to cure overnight before giving it 2 coats of clear lacquer to protect it.
Step 4: Base Board
I cut a piece of grey plastic, 3mm thick, and working from the center I worked out where the relays would go and the light spacings and positions, marked them using a sharpie marker on the film coating.
using a 2mm drill bit I drilled pilot holes in case the sharpie got scuffed.
for the LED positions I drilled a 5mm hole through and then using the drill very carefully I drilled a 6mm counter sink on the underside, be careful here its easy to go right through if the drill bit grabs the work piece. the LEDs should fit in tightly enough to hold them selves in.
the points where the yellow leads go through is 7mm, so I drilled those holes.
5mm holes for the corner screw holes.
Step 5: Making the Relay Bases
After looking at the footage and working out the size of the relay bases I designed them on Google SketchUp 2014, complete with the holes for the terminal posts and the large center whole which is 12mm so that the 12mm tube will fit in it.
for those who want to know I made my bases 49mm in diameter and 30mm high.
I printed them on my 3D printer I did a 100% infill so they were solid, each one took 12 hours to print, most people won't do this but I wanted to for this project, i wanted them to be solid. during printing of the last base the feed gears broke in my 3D printer and the last base didn't print 100% correctly but it was solid enough to use and I managed to fill in the gaps with car body filler.
because the 3D printer prints in layers you end up with a slightly corrugated surface so its necessary to sand the surface smooth before painting.
I also drilled out the holes to make sure they were the right size as you cant sand inside the holes.
I gave them 2 coatings of grey primer and 3 coats of Plasti-Kote Brass.
I did think about including the STL files for the base but I figured its just a cylinder and I have given the dimensions, Google SketchUp is free just make sure you increase the surfaces for the cylinder so it doesn't end up all blocky.
Before choosing the brass paint I wanted to test some out before i ruined a part and its a good job I did, some sprays say they are brass but they are just a bad gold, I tested out 4 options and the plasti-kote was the best.
Step 6: Relay Glass Sections
the glass sections of the relays I had to make out of clear acrylic.
I cut 3 pieces of 12mm tube to 70mm long, sanded one end so it was rounded, using lighter and lighter grades of sandpaper alternating the stroke to make them smooth. I then used T-cut to polish the light scratches out and get them coming up clear and scratch free.
I cut 3 Pieces of 6mm tube to 15mm long, sanded one end so it was rounded and polished it the same way as I did with the 12mm. I slide these inside the 12mm tubes so the tips just stuck out, and fixed them with super glue.
I cut 3 pieces of 12mm tube to 16mm, I sanded this so it was tapered to at least half way down, this is so the spark plug boots will slide over. I also polished these with T-cut.
I cut 3 pieces of 6mm solid rod to 25mm, I fixed these inside the tapered 12mm x 16mm tube with super glue. I took the edges off the top of the 6mm rod so the spark plug leads would slip on easily.
I cut 3 pieces of 20mm tube to 20mm, these will be used to hold the fake glass bits in the bases.
I cut 3 pieces of 3mm and 4mm copper tube and super glued them inside each other, this is because the 6mm tube has a 4mm inner diameter but the copper tube has a 3mm diameter, and the steel wire I will used to slide inside has a 2mm diameter. I super glued these inside the 6mm tubes.
for the steel wire I used a stainless steel coat hanger, it has to stick out about 5mm at the bottom and about 1cm at the top end.
I had to sand 3 sides, top bottom and side, of the 20mm acrylic balls flat until the flat area has a diameter of 12mm, I drilled a 2mm hole in the side surface for the steel wire to slide in.
Just a case of gluing each of the tubes on to the sides of the sanded down ball now, the long one needs to go on the side, making sure the steel wire is inside the drilled hole.
Step 7: Assembling the Relays and Finishing Off
The wire posts on the relays are just terminal posts, I got these ones on ebay about 10 years ago, I super glued these in to the holes on the bases and put some wire on the posts and put the end in the hole i created for tucking the ends in to.
I made the brackets on the back out of some copper pipe I cut open and hammered flat, I could have used aluminum but that would mean buying something extra and I had enough pipe laying around.
On the bases under the glass tube is a plate with rounded up turned edges thats the glass tube sits in and a wire that goes over the top, I used the copper to make the plate and some garden wire I had laying around to bend and shape over the top and tucked them in to the plates and super glued the fake glass tubes in place.
the copper pieces I coated in primer and then brass paint the same as the bases.
When I first investigated making the relays 10 years ago I spoke to someone on a BTTF forum who had made his own, and he had got some labels printed but and had some spare so I bought some off him. I could have designed and got these printed my self, but why bother when someone else has done the work. Suck these on and I was done.
Step 8: Lighting Circuit
the lighting circuit consists of 4 sets of 3 LEDs for the main chaser lights in the Y for the flux capacitor these are warm white LEDs, 5mm using a 68 ohm resistor
and 4 lights on the outside and 3 in the center. these are bright white LEDs, 5mm using a 68 ohm resistor.
I tested it out using a breadboard and jumper wires, this is the first time I have used an Arduino, I used an Uno as they are cheap and easy to get hold of.
to turn a set of LEDs on you have to set the pin from low to high like so
pinMode(pos1_pin, OUTPUT);
digitalWrite(pos1_pin, HIGH);
for the final circuit I use vero stripboard to hold the LEDs in place, it just made it a little easier to solder together.
in the original Flux Capacitor used in the films they used incandescent bulbs, LEDs are better suited for our needs.
Step 9: Adding Sound
As it was fairly easy to get the LEDs working I thought it would be great to have sound, you can run sound from the internal memory but it wont hold much. I found the following instructable which helped me to use an SD card for the sound.
https://www.instructables.com/id/Playing-Wave-file-...
adjustments I made were to use a 5w speaker which I had to use an amplifier module for, but it meant that I didn't need the transistor or resistor that was used in the original project.
the SD card should be formatted with FAT 16.
the sound files have to be 8bit mono wave files, you can use Wav Sample rate converter, which is free however the free version will only do up to 1 minute of audio, if you want longer tracks you have to pay for the software.
you will need to add the TMR library which you can get here
https://github.com/TMRh20/TMRpcm/wiki
Using the code I got from that instructable I managed to get a bunch of wav files to play very well, I had an issue with the sound not being loud enough even with the amplifier module. Turns out all i needed to do was up the volume on my wav files for this I used a free bit of software called Audacity.
there is an issue that I discovered with the TMR library, when a sound is playing it interferes with the IR library, makes it difficult to use the remote sometimes while a sound is playing which is why I made the background sound optional
Step 10: Adding Remote Control
I explored a few options for remote control of my flux capacitor, the guy on www.myfluxcapacitor.com used the sparkfun nordic fob and a 2.4ghz transceiver. which is great, however sparkfun are no longer making the fob, how ever they do make the eagle files available so you can get the circuit boards printed up and add the components your self if you wanted to. but this seemed to be a over kill for me..... but I still got some boards printed up in case I change my mind, OSH park is good for getting boards made
.
I also looked in to 433mhz transmitters and receivers which are very cheap, and from past experience I knew I could get cloner fobs on the internet which I hoped I could clone the signal from the transmitter. Unfortunately this didn't work either.
finally I decided on Infra red, the down side is that you do have to have line of sight, the plus side is you have more buttons to do more things and you can use near enough any remote so at a later stage I could upgrade it. IR sensors are very cheap and easy to hook up to the arduino but you will need to include the Iremote library which you can get here.
https://github.com/shirriff/Arduino-IRremote
the code to recieve the codes
if (irrecv.decode(&results)) {
Serial.print("IR Number = ");
Serial.println(results.value);
irrecv.resume(); // Receive the next value }
just open the serial monitor and you can see the codes coming in, they can then be put in to variables and used in if /case statements to perform functions like playing sound when a button is pressed.
I was going to put up a schematic of the circuit but its so simple its hardly worth it, one pin goes to 3.3V pin on the Arduino, one pin goes to ground, and one pin goes to an input on the Arduino.
I added the IR sensor in the middle of the base board so that it can read inputs without stuff getting in the way, you can see in the pictures where it is.
Step 11: Light Blocks and Back Board
the blocks ate 12mm thick clear acrylic, I have put up a picture of the dimensions, I actually go the supplier to cut them out on their CNC router to save me a little bit of effort and to ensure I get straight lines, my previous attempt 10 years back they ended up all wonky.
I drilled 4 x 5mm holes for the leds, first one is 6mm from the back of the block then every 16mm.
the blue you see on the blocks is a film to protect the block from scratches, we need to masking tape the edges so we don't get paint on them later, and remove the film. then with light sandpaper rough up the exposed side, wipe with a damp cloth and then you can spray them with primer and when thats dry spray them with silver. repeat for the other side.
When they have fully dried out they can be slotted over the LEDs and a spot of super glue to hold them on the back board.
place the relays and screw them in place from the back of the board.
the Accel 3009 yellow spark plug leads, 7mm, with orange boots. it has to be the 3009, I got some 3008s by mistake and they are not suitable. only the 3009s will do. we need to cut the cable to length, they will be going from the top of the relays through the holes on the board. the boots should slide in to place with a firm push on to the relay.
Step 12: Adding the Window
to make the window I had to make a template first, so I taped together some paper so I had a piece big enough, then layed the piece I cut out from the main enclosure on the paper and traced a line around it.
I measured 5mm inside that line to make the shape for the window, laid the plastic on the paper and made sure I still had the film on it to protect it. Using a sharpie I traced around the template.
I cut out the plastic with a jigsaw, now my first attempt was free hand, this was a mistake and cost me a piece of plastic, because it wasn't secured the saw snagged and cracked the sheet taking a chunk out of it. I had to order another piece and wait 4 days for it to turn up and then try it again.
the second attempt I put a piece of wood across the plastic and clamped it to the bench to stop it jumping around and I also make sure the jigsaw was flat on the work piece and took it very slowly.
the rubber gasket / window seal you can to put on the box first and cut to size then you can work the clear plastic in, once you have taken the protective film off. It takes a bit of effort to get it in, but be careful not to crack it.
I also cut the supports out as well, 30mm of 12mm tubing, and a 40mm 3/16 UNF machine screw, later on i super glued the 12mm tubes to the back board to make it easier to install later on.
Step 13: Access Alcove / Box
It dawned on me that If I wanted to make changes later on I would have to remove the panel to get to everything, or if I wanted to replace the battery.
I didn't want to cut holes in the bottom edge of the box, as its standing up, and ruin the look of it as it would then not match whats on screen.
I had a brain wave, if i got a project box from the local electronics store, take the lid off and cut a hole in the back of the enclosure I could screw the project box to the enclosure creating a recess. I then cut holes for the USB socket, and 9v power socket on the Arduino, also for the SD card , power switch and 9V battery connection.
I also put in a instructables sticker ;-)
and put on the labels on the front using a Dymo junior label maker with red 9mm tape.
Step 14: Install the Electronics and Finishing Off
I used a hot glue gun to secure the electronics inside, it works really well and it wont cause a short circuit and if need be you can remove it with a little effort.
I was going to print some bases on the 3D for everything to screw into but I would have ended up just hot gluing them in to the case and it seemed pointless as the cost of the electronics is not very much and I have enough spare stuff kicking around to replace any of the parts.
lastly I screwed the back board in place and it was complete.
Step 15: Conclusion and Showing Off
I am extremely please with the result its not far off the film in looks of things. on the film you can see there are 2 right angle pipes attached to the flux capacitor, I didn't do these for several reasons, I didn't to snap them off trying to store it or move it about, also in the UK our pipe bends are different so I would need to source some from the US to get the right look and I have decided to do this when I go to install it in the Delorean which one day I will buy. ... ok stop laughing, I will own one.... one day ;-)
Features
Plays all 3 main themes
plays several quotes from each film
has the power on sound when you turn it on
has the option of having the electrical circuit sounds when its running.
has 3 modes, standard, reverse and disco
plays time travel sound when temporal shift is initiated.
has IR remote control.
light speed can be increase and decreased.
sounds can be updated by removing the SD card at the back and uploading new files
Arduino can be updated by plugging a USB lead in the back.
can run on a 9V battery, 9V power adapter, USB power or 12V car battery for when I put it in the Delorean.
can be interfaced with future Back to the future props such as the coming time circuits.
VIDEO!!
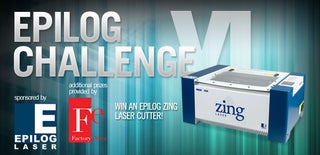
Runner Up in the
Epilog Challenge VI
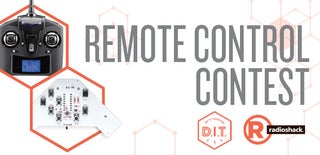
Participated in the
Remote Control Contest
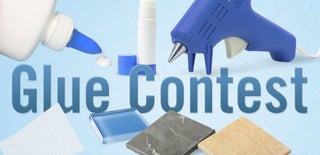
Participated in the
Glue Contest