Introduction: Garage Door Table
A couple years ago we replaced our old heavy wooden garage door with a lightweight aluminum door. I hung onto the panels since they were made with high quality pine wood and marine grade plywood. I turned one of the panels into a workbench in my garage, and 2 others were reserved for a new dining room table. Thanks to the furniture contest, I finally took the time to make the table.
I tossed around several ideas on how to fill the recessed pockets of the door sections. The first thought was to fill them with concrete and grind and polish the surface much like a concrete countertop. However, if I did that, it would cover up most of the beautiful wood grain. So I decided on a clear epoxy. Because of this decision, I found out HOW MUCH epoxy is required to fill the recesses and cover an entire 48" x 83" table top, and also just how expensive it is! Sometimes, finding the right solution to upcycle materials will cost you more money than just buying new ones, but where is the fun in that!? I don't think you could ever buy a table made from a garage door at the mega furniture stores.
Step 1: Getting Started and Planning
LET'S GET STARTED
Because this is such a specialized project and I highly doubt many people have old wooden garage door sections lying around, please look at this instructable more as an inspiration for other possibilities of making custom furniture. My approach to this project was to try to plan as much as possible, but the majority of the work was trial and error. I want to share lessons learned and ideas to make your own furniture as painlessly as possible.
CAD OVERKILL
I laid out the general idea of the table in CATIA - yes I know a little bit of overkill on the CAD software, but hey, it's what I do for a living so why not!? I actually used the CAD model to calculate the exact amount of Epoxy I would need. I had the option of just leaving both sections at their length (8') and using them side by side, OR I could cut the sections in half and butt them up against one another. Leaving them long and side by side made for a really long skinny table whereas cutting them and stacking them end to end made for a semi-really-long and wide table. Stacking them also allowed for more symmetry due to how these garage doors were made. - see pictures for explanation.
DISCLAIMER
I started by attempting to scrape the peeling paint off the doors. This proved to be very difficult as there were approximately 60 years worth of paint stuck to the door. Since I wasn't using the painted side of the door for the top, I didn't spend a lot of time trying to remove paint. I basically wanted to make sure I didn't have loose paint chips coming off the bottom of the table. (Note* - I want to point out that I have no idea if the paint on these doors was lead based. I made sure that any paint that could be peeled, picked, or knocked off was removed and sanded smooth. Any unsealed painted surface would not be exposed to food and would be out of reach of prying hands. Please keep this in mind when working with older painted materials.)
Step 2: Sanding, Cutting, Scuffing, Beveling, and Brushing
KICKING UP SOME DUST
The doors had either been stained on the inside or had just absorbed many years worth of dust and dirt as they were definitely dark and dirty. I sanded the upper surfaces of the ribs with an orbital sander and finished them by hand. The surfaces of the pockets I also attempted to sand with the orbital sander, but it was pretty tricky and I ended up eating up my sanding pads pretty quickly due to the disc bumping against the edges and tearing the pads. The thing I found that worked best was my metal grill brush. It would easily take the loose materials off and would do a sort of sanding action as well. I wasn't too worried about getting the surfaces of the pockets smooth since they were going to be filled with 1/2" of epoxy in the end. Please note when sanding, it is highly advisable to use a respirator or at the very least, a dust mask.
ROUNDING THINGS OUT
After the cutting and sanding, I tried to round off the sharp edges created by the cuts. I wasn't very particular with this either since it was a worn, rustic, industrial look I was going for. Rounding over the edges also helped prevent splinters - which I was unfortunately blessed with MANY from this project!
CLEAN UP THE ROT
The bottom section had some areas that were starting to rot, so I cut about an inch and a half off the bottom section. Then I cut each section in half. Once I cut the sections in half, I had to cut about an inch off what used to be each edge of the sections so the width of the edges would be the same. - Again, Please look at the pictures for clearer explanations.
Step 3: Nice Legs!
Figuring out which style of legs to make was the next step. I thought about regular post legs, angled legs, pedestal legs, even tensegrity legs. Finally my wife showed me a wonderful how-to on making a farmhouse table. The legs were perfect! (and very easy to make!) Thanks Ana White! For the most part I copied what she had done, but I did make a few modifications to mine. The dimensions will vary based on the application, but I have included mine for reference.
TORCH IT!
NOTE: The following instructions are dangerous if proper caution is not exercised! I will not be held responsible for improper use of a blow torch!
The 2x4's I bought were red pine so they would match the aged red pine of the garage door. I made all the cuts, and glued and screwed them together. Once they were set, I torched them! A few years ago, I had came up with a way (I'm probably not the only one who has done this) to texture and age dimensional soft wood.
- CAREFULLY sweep a torch over the wood allowing the flame to scorch the wood. You don't want to burn the wood to ashes, just char the outer grains to a nice dark brown/black. I varied the amount of charring over the wood to give it some variety.
- Once you have a level of blackening you are happy with, take a wire brush and scour off the charred wood. The more you burn it the more material you will remove. The flame burns the softer part of the grain and hardly touches the harder parts.
- After you have removed most of the blackened grains, go over it with fine grit sandpaper to smooth out the top grains. You should end up with a very textured wood with beautiful darker color variations.
- Another thing you can do is spray the wood with black spray paint and let it sit for a few seconds, then wipe it off with a rag and sand. This gives the grains even more texture, but it would have been too dark for my preference here.
I applied stain to the wood per the manufacturers instructions, then applied 3 coats of polyurethane. This gave a wonderfu
l look that complimented the table top. I wasn't going for an exact match, but a complimentary look to make a pleasing flow of colors and textures.
Step 4: Substructure and Support
Since my background is in engineering and design with structural steel, it was only fitting that I over-engineer the bottom support of the table. I didn't want the slightest bit of sag, which is a problem with many tables over time. I built the frame of dimensional lumber first and then added it to the panels. I assembled the frame to the panels on our flat and level living room floor. Our basement floor is not level and would have made a very uneven table top had I assembled it down there.
- I placed 2x4's over each seam where the panels joined together.
- I added notched 1x4's perpendicular to those 2x4's. These ran along the ribs of the door.
- I then added a box of 1x4's around the whole outside of the substructure.
Finally after the frame was attached and adhesives dried, I took the whole thing outside for a final leveling sand. Where the panels met, it wasn't always smooth due to varying thicknesses of the panels and differing layers of paint . Since the door was outside I could see more areas that needed to be touched up than I could in the basement.
Step 5: Attach Those Nice Legs....stain the Frame and Seal the Top.
DRILL, COUNTERBORE, AND SCREW
Plain and simple: Pre-drill and counterbore the holes to get a nice tight connection and screw directly into the 2x4. Use lag bolts or other strong type of fastener with a wide head or shoulder. You could also add regular washers and lock washers to prevent any loosening of the screws.
I wanted the legs to be removable so the table can be disassembled for easier moving, therefore I did not use any adhesive.
SEAL THE DEAL
The next thing I did was to apply 3 layers of Satin Polyurethane to the ribs. I also applied - what I thought was sufficient - one layer inside the pockets. The instructions on the epoxy explicitly tell you to apply a skim coat of the epoxy before pouring your flood coats. I assumed one layer of polyurethane was just as good. It ALMOST was. I ended up with thousands of teeny tiny air bubbles on the base layer - just like the instructions said I would if I didn't listen. You can't actually see them unless you nearly put your face on the table and really look for them, but never-the-less they are there. (I am also my own worst critic so I am prone to look at all the mistakes I made.) More on the epoxy pouring in the next step.
Step 6: Now Comes the Hard Part!
So my decision to pour epoxy into the pockets had my anxiety levels elevated! I had poured epoxy before, but it was in much smaller areas and it was usually tinted with sign paint, so air bubbles were not always a problem due to opaqueness. This on the other hand, had to be nearly perfect and I know from experience that I am no where near perfect in my projects. My goal was to only fill the pockets and leave the sealed wood exposed to create a nice contrast of finishes.
WHERE DO I BEGIN?
I won't go into explicit detail on pouring the epoxy as that could be a whole instructable in itself. I will just pass on a few lessons I learned from such an undertaking.
- In order to pour the epoxy to 1/2" thickness, I had to do 4 pours in each pocket. Each pocket pour required 3/4 of a gallon each of the resin and hardener! Doing the math equals 6 gallons total of resin and hardener.
- I researched online to find US Composites and they were the least expensive that I found. (Note when buying epoxy - if you are buying a 4 gallon kit, it means you get 2 gallons of resin and 2 gallons of hardener.)
- Follow the directions - there's a reason they include them with their products, and they are found on several pages on their website.
- Don't rush it.
- Use a blow torch to remove air bubbles and when you think you have them all removed, use your blow torch again. I wouldn't recommend a heat gun or hair dryer since those are using forced air and can stir up a lot of dust - which you do not want in your epoxy.
- Did I mention following the directions?
NOW WHAT!?
Once all pockets had been completely filled, I noticed that when I had sanded the ribs, I had dipped the belt sander a little on some of the sides and the epoxy was flowing into those low edges, thus erasing any crisp clean edges from epoxy to rib. My solution!? Pour more epoxy over the whole table top making it all one level. It worked, but it was a L O N G day and I was bordering on insanity trying to ensure all bubbles were removed and all surfaces were level. I was also chasing drips off the sides of the table since I didn't bother to hassle with barriers to contain the epoxy at the edges. Adding the top coat of epoxy required almost another gallon total, so I used 7 gallons of epoxy when the whole project was finished! In the end, it was worth it since the finish made the wood grains *pop* more.
Step 7: Wrapping It Up
FINALLY
Overall it turned out beautifully in my opinion even though it didn't have the look I was going for initially. I hope it inspired you to go out and use, reuse and upcycle items to make beautiful furniture yourself! The less we throw away the better it is for everyone! Thanks for sticking with me all the way through this I'ble and PLEASE VOTE FOR ME!
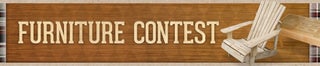
Grand Prize in the
Furniture Contest
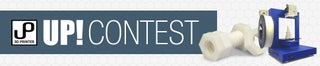
Participated in the
UP! Contest