Introduction: Giant Papercraft Trojan Horse
Step 1: Making the 3D Model
First, I needed a 3D model.
Rather than use someone else's model of a Trojan horse, I decided to design my own from scratch. I knew that I wanted the final model to be quite simple and angular, as this would make it easier to deconstruct into a sensible number of cardboard panels. Fortunately, it's much easier to model a stylized low-resolution horse than a realistic and detailed one.
My initial plan was to have enough room in each pair of legs for someone to stand, with the person in the rear bent forward and the person in the front standing upright, much like with a traditional pantomime horse, only much larger. In fact the horse ended up so large that the person at the back would be able to stand upright quite comfortably.
I modeled the horse in Blender, starting with a simple cube and extruding new faces from it until I had a very rough outline of a horse, as shown in the first image here. I then gradually refined the shape of the horse, subdividing the edges where necessary, until I had something much more distinctive. I modeled the ears, the tail and the mane separately, then joined them to the horse with a Boolean operation.
The whole time I was modeling the horse, I was thinking, "Would this look good 50 feet tall and made of wood?" As design briefs go, I quite enjoyed that one.
Step 2: Deconstructing It in 123D Make
I then imported the model into a preview version of 123D Make. At the time of writing, the publicly available version of 123D Make does not include the "Panel" function that I used for the horse, but it is due to become available at some point in the future.
In theory, this horse model could be made using only 28 folded panels .Many of those panels, however, would have been much larger than the bed of our laser cutter. Once I'd adjusted the size limits within 123D Make, the model had been deconstructed into 119 pieces. That's quite a lot of cardboard.
123D Make lets you choose from a variety of joinery methods for your seams, allowing you to make structures from a wide variety of materials, from sewn fabric to riveted sheet metal. For one glorious day-dreamy half-hour, I contemplated making this Trojan horse from sheets of 1/4" plywood strapped together with industrial metal cable ties. Fortunately, Eric talked me down off that particular ledge of impracticality, so I went for cardboard joined together with plastic zip ties.
Step 3: Labeling and Perforating the Pieces
I opted for the rivet joinery method, as this automatically provides overlapping tabs and holes in the appropriate places on each panel. I spent a while fine-tuning the exact hole diameter and tab width, using scraps of cardboard to roughly test how much stress different arrangements could withstand.
123D does a great job of labeling all of the 2D pieces it generates, with each panel being automatically labeled with its own number and the numbers of the pieces that each edge should be touching. What's more, you can choose to have the precise angle of each fold labeled, letting you know whether the fold is a mountain or a valley and just how far it should be bent.
Step 4: Laser-cutting the Pieces
Once I had all of my horse flesh exported as EPS vector files, then I began the arduous process of laser-cutting each piece using our Epilog laser. Although this is still inestimably faster than cutting by hand, cutting 119 different panels (each of which was also perforated along its folds and labeled with a low-power laser) took a couple of days.
At last, I had a huge pile of precisely cut sheets of cardboard, sorted into numerical order and ready to be turned into a giant horse. I had long since stopped noticing the smell of scorched cardboard that now followed me around like a bad spirit, or the soot that was ingrained into my fingertips. I was approaching oneness with the cardboard and I felt exhilarated to be embarking on the next step.
Step 5: Assembling the Skin!
Step 6: Seam Joinery
We adopted a policy of keeping all the long tails of the plastic zip tie connectors pointing inwards so that the horse would look clean and unblemished from the outside. At first, we trimmed off all of the zip ties' tails, but we soon learned that doing so created dozens of new sharp edges on which to lacerate ourselves. Stowaway passengers be warned!
Here you can see how it was all tied together.
Step 7: Steady Progress
I can't recommend this method of joining sheets of cardboard using plastic zip ties high enough. They're fantastic! My first plan had been to glue everything together with hot glue, but that would have been far weaker, messier and more time-consuming, not to mention permanent.
Zip ties are light, cheap, easy to use and removable. What's not to love?
Step 8: More Progress
By the end of the first day, we had the head and the front legs of the horse assembled. Future plans for a giant chess set were vaguely circling in my mind.
Step 9: Bringing Up the Rear
Here you can see all the tails of the zip ties pointing inwards. Standing inside the hollow horse was a surreal, tree-house-like feeling, with light filtering in through a thousand tiny holes and the soft tendrils of plastic zip ties brushing your arms as you moved.
We constructed the horse in three parts: head, front legs and rump. By the end of the second day we were ready to join all three parts together.
Step 10: Clambering Over Furniture
As we came closer to completion, it became harder and harder to connect the pieces of the horse together. Often, we had to hang precariously from ladders and reach an arm blindly into a tiny gap, trying desparately to feed a zip tie back through a pair of pencil-width holes.
We persevered, though, and soon had an entire headless horse. Notice that the body was completely capable of supporting its own weight just by dint of the cardboard's own rigidity and the complex nature of the folds. At this stage, there was no skeleton of any kind inside the horse. Well, no horse skeleton.
Step 11: Triumphant Head Installation
Connecting the head was a three-person effort. The finished horse stood at 12 feet tall. The ceiling of the Instructables Lab is only 10 feet high. Luckily, I had anticipated this and placed the horse underneath a large recessed skylight.
Step 12: Standing Proud
So, in just under a week, we had a giant cardboard Trojan horse. 3D modeling meets quick fabrication. The possible meets the absurd. Papercraft meets siegecraft.
Success!
Step 13: Building a Frame
I assembled most of a simple frame from beams of wood and sheets of plywood, either screwed or bolted together so as to allow it to be separated easily into two halves for transportation. To support the head, I made a simple mechanism consisting of two PVC pipes under tension, which allowed the head to be nodded up and down by pulling as thick cord at shoulder level within the horse.
The design of the internal structure was determined by the following factors:
- It had to support the head and back of the horse.
- It had to be partially disassemblable so that we could get the darned thing out of the door.
- It had to be mountable on a rolling wooden platform for transport to Christmas parties and sieges.
- I had plans to turn the inside of the horse into a standing desk and workspace afterwards.
- I also had vague plans of using the horse as a kind of portable bar, where punters could stick their heads (one at a time, please) into the belly of the horse and be greeted by friendly bartenders with cocktails inside. This may yet happen.
Step 14: Making It Move
I made a four-wheeled dolly from 2x4s and plywood. The sheets of plywood were reinforced from below and positioned so that each one would support one pair of the horse's legs. I threaded a heavy duty nylon cord through two holes at the front of the dolly, so that the whole horse could be easily towed.
Step 15: Setting It Free
The next stage was to rebuild the whole structure outside. This was not nearly as hard as it might sound; we simple divided the horse's hide into three parts and assembled around the wooden frame out on the pavement. I had visions of lowering the whole thing from our fire escape using climbing rope, but it turned to be unnecessary. Maybe next time.
Notice the dimly glowing plastic orbs in the horse's eye sockets. These grew more and more ominous as night encroached.
Step 16: Charge!
And so began the epic journey from the Instructables Lab to the Autodesk headquarters for the company Christmas party. Pulled by our fearless leader, the Trojan horse made its kilometer journey through the rush hour pedestrian traffic of San Francisco.
Useful tip: Cars will stop for Trojan horses. Trojan horses will not necessarily stop for cars.
I had hoped that the a few of us could stow away inside the horse with cardboard weapons, but this made it prohibitively awkward to tow.
Step 17: Obstacle En Route
On the horse's first outing it encountered low-hanging branches, high-rising curbs and slow-moving pedestrians. It navigated all of them with gusto and aplomb.
Step 18: The Escorts
We kept one person on either side of the horse throughout the journey. Although it never threatened to tip over, we felt reassured that there would be someone ready to break its fall if it did.
Step 19: Turned Away Upon Arrival
Alas, when we arrived at gates of Autodesk's city fortress we found ourselves barred from entry.
"Your horse is too tall," we were told.
"We'll make it bow its head to get through the door," we replied.
"It's wheels will scuff up our polished floor," we were told.
"We'll carry it once we're indoors," we replied.
"It won't fit in the freight elevator," we were told.
"We can just leave it in the lobby. We promise it's not full of armed Greek soldiers," we replied.
That seemed to swing things against our favor. The horse stood and stared balefully through the window into the warm, Christmassy corporate building while we tried in vain to plead our case.
Step 20: Trying to Grease Palms
I'm not going to claim that bringing a 12-foot horse to a verbal disagreement is a good negotiating tactic, but it does lend a certain frisson to the proceedings.
Step 21: You'll Have to Sleep in the Stables...
In the end, we parked the horse on the Embarcadero, under the watchful gaze of some very uncertain police officers. We took turns keeping an eye on the horse while the others went inside for cake, alcohol and socializing.
Those of us who stayed with the horse soon discovered that the internal frame was strong enough to support two people's weights, and we promptly withdrew to eat, drink and listen to music within its spacious belly. Yes, our Trojan horse had been turned away from the party, but sitting cross-legged inside my giant cardboard horse, sipping a beer and munching on some snacks, I had one of the most pleasant winter evenings I can remember.
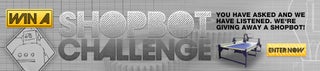
Participated in the
ShopBot Challenge